Carbide inserts are a critical component in the machining industry, known for their durability and precision in cutting, shaping, and finishing materials. They are made from carbide, a compound consisting of carbon and a less electronegative element. These inserts are essential for tasks requiring high precision and wear resistance, making them indispensable in modern manufacturing.
Types of Carbide Inserts
Carbide inserts come in various shapes and sizes, each designed for specific applications. Here’s a detailed table highlighting some common types and their applications:
Type of Carbide Insert | Shape | Application |
---|---|---|
C-Style | Diamond | General turning and boring operations |
D-Style | 55° Diamond | Finishing and semi-finishing applications |
S-Style | Square | Rough turning, facing, and interrupted cuts |
T-Style | Triangle | General purpose turning, good for a wide range of tasks |
R-Style | Round | Heavy roughing and high-feed turning |
V-Style | 35° Diamond | Precision finishing and contouring |
W-Style | Trigon | Versatile, for both roughing and finishing |
A-Style | Parallelogram | Profiling and cutting intricate shapes |
P-Style | Pentagon | Specialized tasks requiring multiple cutting edges |
M-Style | Hexagon | Machining in hard-to-reach areas |
Applications of Carbide Inserts
Different carbide inserts are suited for various machining processes. Here’s a table showing the primary applications:
Application | Carbide Insert Type |
---|---|
General Turning | C-Style, T-Style |
Finishing | D-Style, V-Style |
Rough Turning | S-Style, R-Style |
High-Feed Turning | R-Style |
Interrupted Cuts | S-Style |
Profiling and Contouring | A-Style, V-Style |
Machining Hard-to-Reach Areas | M-Style |
Heavy Roughing | R-Style |
Precision Finishing | V-Style, D-Style |
Specialized Tasks | P-Style, M-Style |
Material Properties of Carbide Inserts
Carbide inserts are renowned for their exceptional material properties, making them suitable for demanding machining tasks. The following table highlights these properties:
Property | Description |
---|---|
Hardness | Extremely hard, often measuring over 90 HRA |
Wear Resistance | High wear resistance, extending tool life |
Thermal Conductivity | Excellent, which aids in heat dissipation during machining |
Toughness | Sufficient toughness to withstand high-stress environments |
Chemical Stability | Resistant to oxidation and corrosion |
Compression Strength | Very high, ideal for maintaining shape under pressure |
Composition and Characteristics
Carbide inserts are made from various materials, each with unique characteristics. Here’s a breakdown of their composition:
Composition | Characteristics |
---|---|
Tungsten Carbide (WC) | High hardness and wear resistance |
Cobalt (Co) Binder | Adds toughness and binding properties to the carbide |
Titanium Carbide (TiC) | Increases hardness and chemical stability |
Tantalum Carbide (TaC) | Enhances hardness and resistance to high temperatures |
Niobium Carbide (NbC) | Improves toughness and resistance to thermal shock |
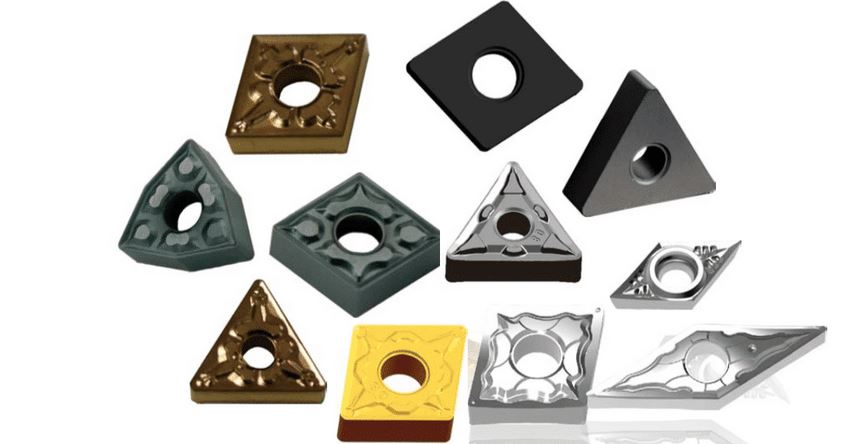
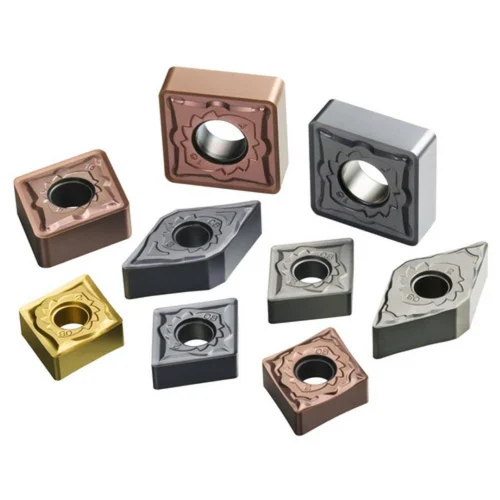
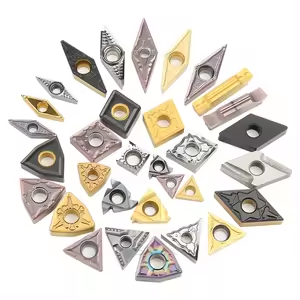
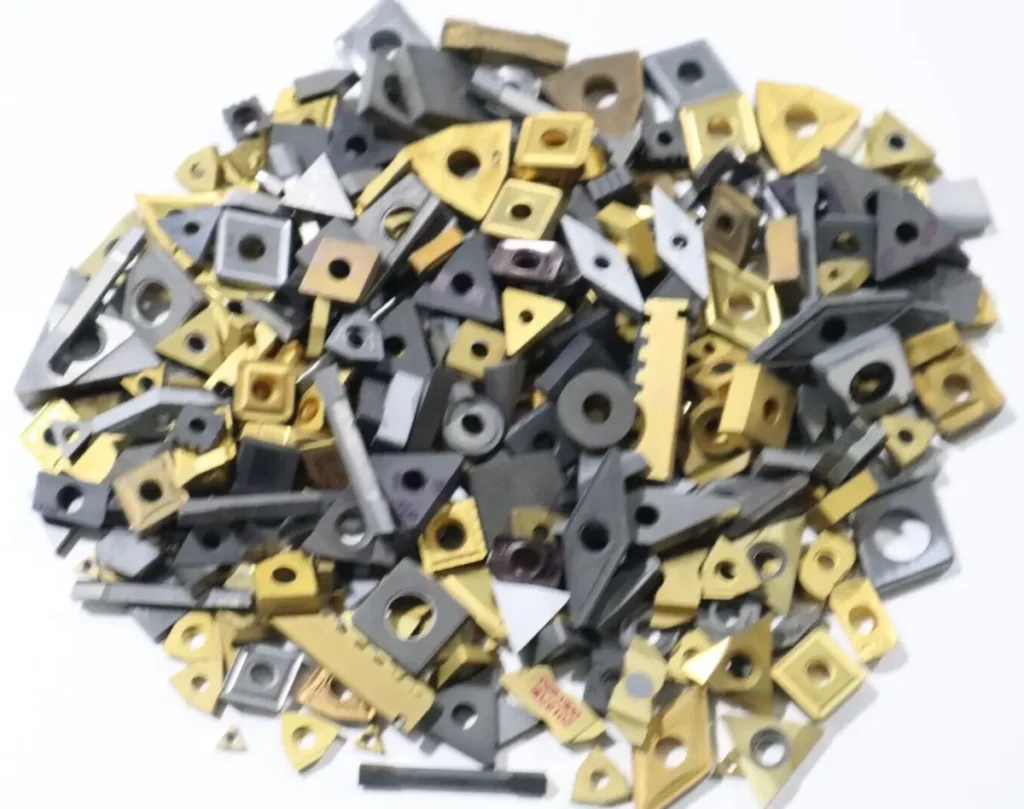
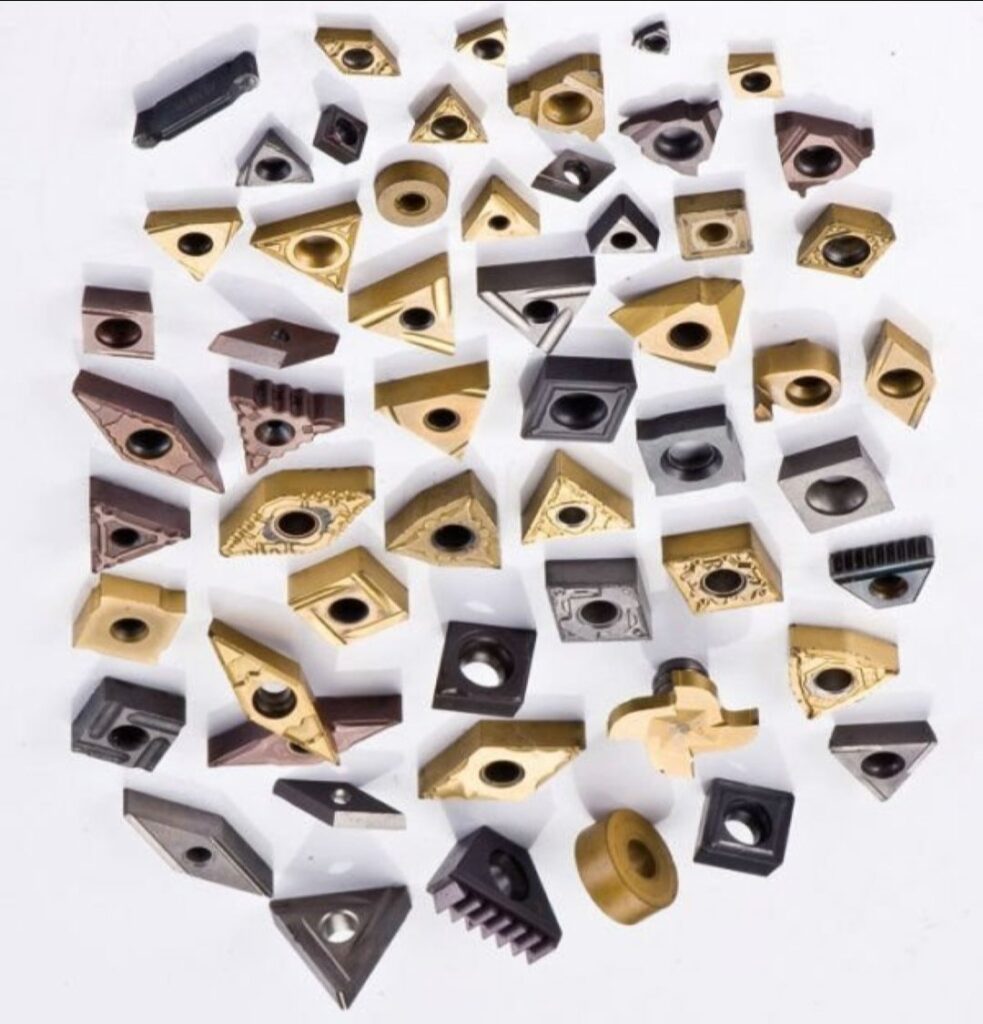
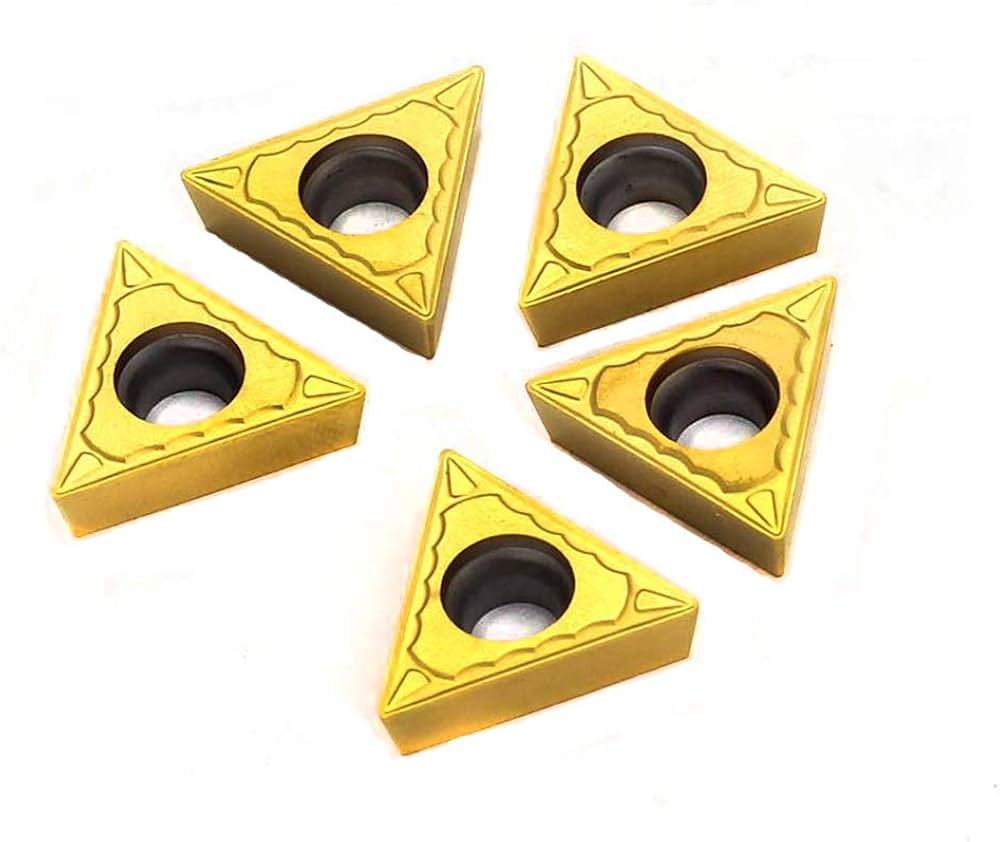
Hardness, Strength, and Wear Resistance
Carbide inserts excel in hardness, strength, and wear resistance. The following table compares these properties across different grades:
Grade | Hardness (HRA) | Strength (MPa) | Wear Resistance |
---|---|---|---|
WC/Co | 90-94 | 2000-2500 | Excellent |
WC/TiC/Co | 92-95 | 2200-2700 | Very High |
WC/TaC/Co | 91-93 | 2100-2600 | High |
WC/NbC/Co | 92-94 | 2300-2800 | Excellent |
Specifications, Sizes, and Standards
Carbide inserts come in various specifications and sizes, adhering to industry standards. Here’s a table detailing common specifications:
Specification | Size (mm) | Shape | Standard |
---|---|---|---|
ISO P35 | 6-25 | Triangle | ISO 1832 |
ISO K10 | 5-20 | Square | ISO 1832 |
ANSI C2 | 4-30 | Diamond | ANSI B212.4 |
ISO M20 | 8-22 | Round | ISO 1832 |
ANSI C5 | 3-28 | Trigon | ANSI B212.4 |
Suppliers and Pricing Details
Several suppliers offer carbide inserts, each with varying pricing. Here’s a table listing some notable suppliers and their pricing details:
Supplier | Price Range (USD) | Notes |
---|---|---|
Sandvik Coromant | 10-50 | High-quality, reliable |
Kennametal | 8-45 | Extensive range of products |
Seco Tools | 12-55 | Known for innovative solutions |
Mitsubishi Materials | 9-48 | Durable and efficient |
Sumitomo Electric | 11-52 | Precision-focused |
Selecting the Right Carbide Inserts
Choosing the right carbide insert depends on several factors, including the material being machined, the type of machining operation, and the desired surface finish. Here’s a guide to help with the selection process:
Criteria | Recommended Carbide Insert |
---|---|
Material Hardness | WC/TiC/Co for hard materials |
Surface Finish | V-Style or D-Style for fine finishes |
Machining Operation | R-Style for heavy roughing, C-Style for general turning |
Machine Stability | S-Style for interrupted cuts, A-Style for profiling |
Cost Consideration | Evaluate suppliers like Kennametal and Seco Tools for cost-effective options |
Advantages and Limitations
Carbide inserts offer numerous benefits but also come with some limitations. Here’s a comparative analysis:
Aspect | Advantages | Limitations |
---|---|---|
Durability | High wear resistance and long tool life | Higher initial cost compared to HSS |
Precision | Excellent for achieving fine tolerances | Requires precise handling and setup |
Versatility | Suitable for a wide range of materials | Limited in extremely high-temperature applications |
Performance | Maintains cutting efficiency at high speeds | Can be brittle if improperly used |
FAQ
Question | Answer |
---|---|
What are carbide inserts used for? | Carbide inserts are used for cutting, shaping, and finishing materials in various machining operations. |
How do I choose the right carbide insert? | Consider factors like material hardness, desired surface finish, and type of machining operation. |
Are carbide inserts cost-effective? | Yes, despite their higher initial cost, their durability and precision make them cost-effective in the long run. |
Can carbide inserts be used on all materials? | They are suitable for a wide range of materials but may not be ideal for extremely high-temperature applications. |
How are carbide inserts made? | They are made by combining carbide powders with binders, followed by pressing and sintering. |