Welcome to the comprehensive guide on carbide insert shims! Whether you’re a seasoned engineer, a manufacturing enthusiast, or just curious about this essential component in machining, you’re in the right place. Let’s dive into everything you need to know about carbide insert shims, from their functions and types to selecting the right ones for your needs.
Overview of Carbide Insert Shims
Carbide insert shims are critical components used in machining to support and secure carbide inserts in cutting tools. These shims provide the necessary stability and precision required for effective machining operations. Without them, achieving high accuracy and surface finish in metal cutting would be challenging.
Carbide insert shims are made from a variety of materials, including metal powders, which are sintered to form a dense, durable product. They come in various shapes and sizes to match different insert and tool holder configurations.
Why Are Carbide Insert Shims Important?
Carbide insert shims play a crucial role in:
- Maintaining Stability: They ensure the insert remains securely in place during machining.
- Precision and Accuracy: They help achieve high levels of precision by providing a stable platform for the insert.
- Prolonging Tool Life: By absorbing some of the forces during cutting, they reduce wear and tear on the inserts.
- Versatility: They allow for the use of different inserts in a single tool holder, enhancing versatility and cost-effectiveness.
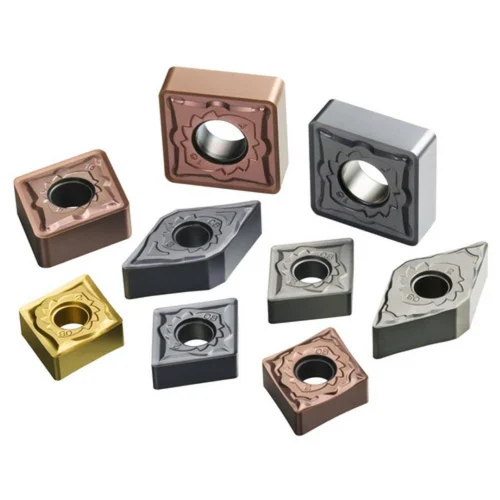
Types of Carbide Insert Shims
To cater to the diverse needs of machining operations, carbide insert shims come in various types. Here’s a detailed table presenting the different types of carbide insert shims:
Type of Carbide Insert Shim | Description | Common Applications |
---|---|---|
Flat Shims | Simple, flat shims for basic support | General machining |
Angular Shims | Provide angular support for inserts | Specialized cutting tasks |
Curved Shims | Designed for inserts with curved edges | Complex geometries |
Thicker Shims | Offer additional support and stability | Heavy-duty machining |
Thin Shims | Used for fine adjustments and precision | High-precision tasks |
Custom Shims | Tailored to specific tool and insert combinations | Specialized applications |
Applications of Carbide Insert Shims
Carbide insert shims find applications in various machining operations. Here’s a table showcasing their applications:
Application | Description | Benefits |
---|---|---|
Turning | Used in turning operations to support inserts | Improved accuracy and finish |
Milling | Supports inserts in milling cutters | Enhanced stability and tool life |
Drilling | Used in drill bits for better performance | Increased precision |
Grooving | Supports grooving inserts for precise cuts | Better groove quality |
Boring | Essential in boring operations for stability | Consistent bore size and finish |
Material Properties of Carbide Insert Shims
The material properties of carbide insert shims are crucial for their performance. Here’s a table detailing the key properties:
Property | Description | Impact on Performance |
---|---|---|
Hardness | Measure of material’s resistance to deformation | Higher hardness means better wear resistance |
Toughness | Ability to absorb energy and resist fracture | Essential for durability under high-stress conditions |
Density | Mass per unit volume of the material | Affects weight and stability of the shim |
Thermal Conductivity | Ability to conduct heat | Higher conductivity helps in dissipating heat during cutting |
Corrosion Resistance | Resistance to chemical degradation | Important for longevity in harsh environments |
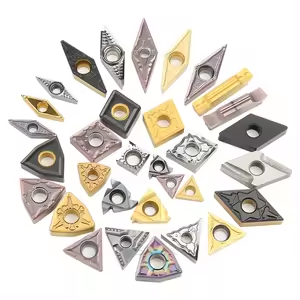
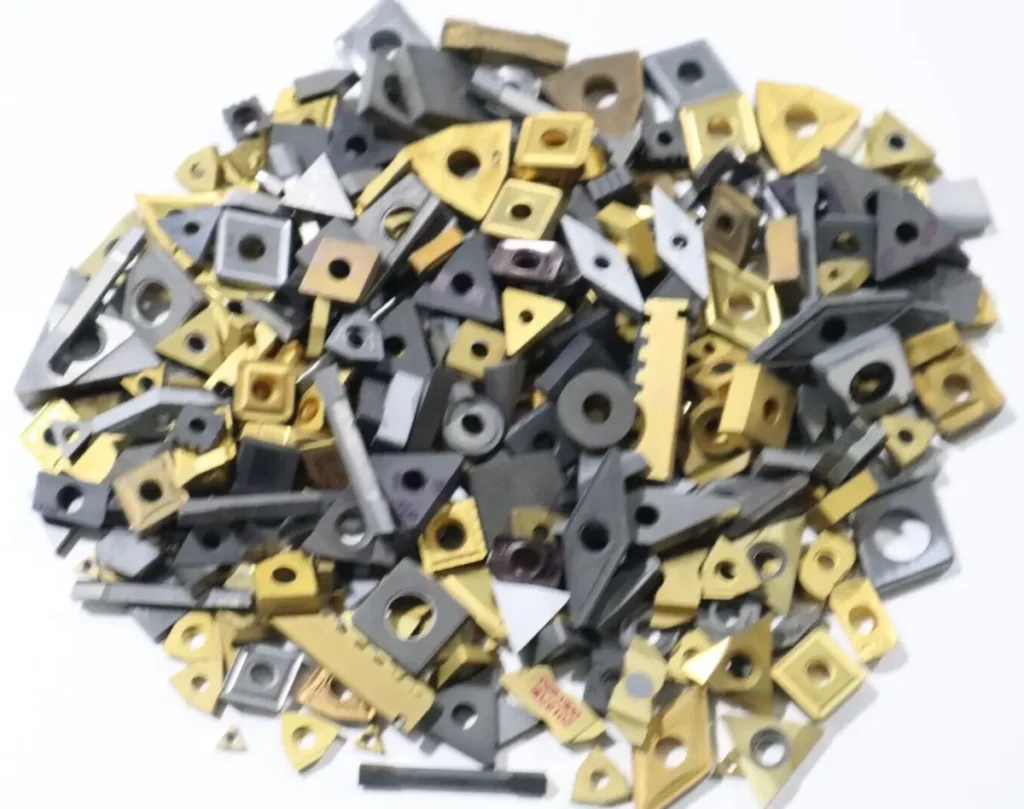
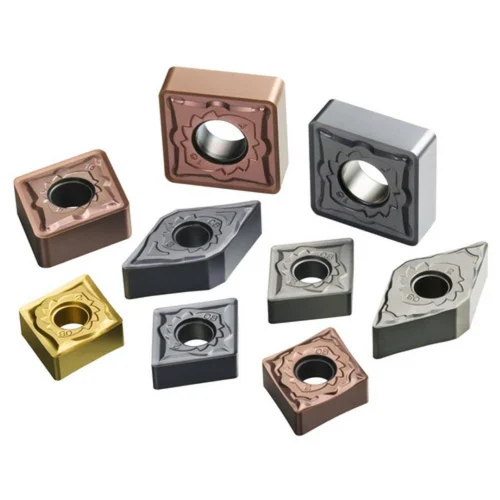
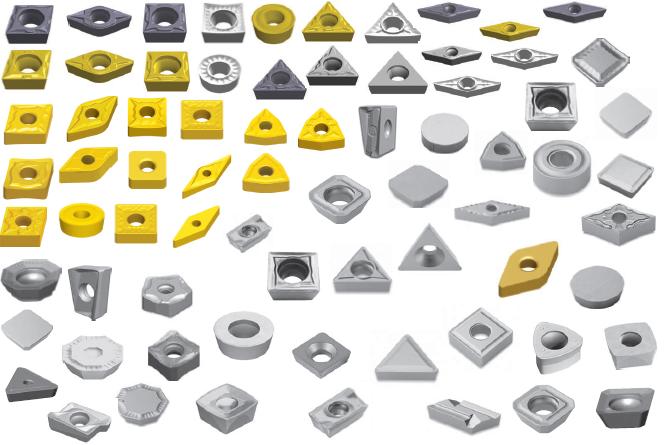
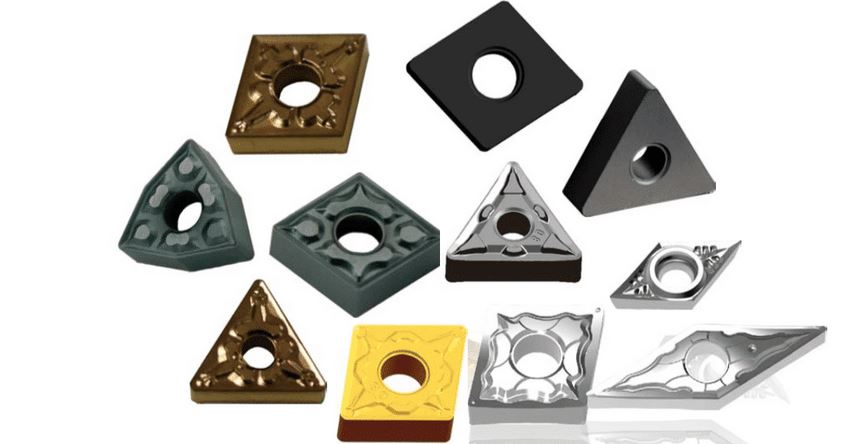
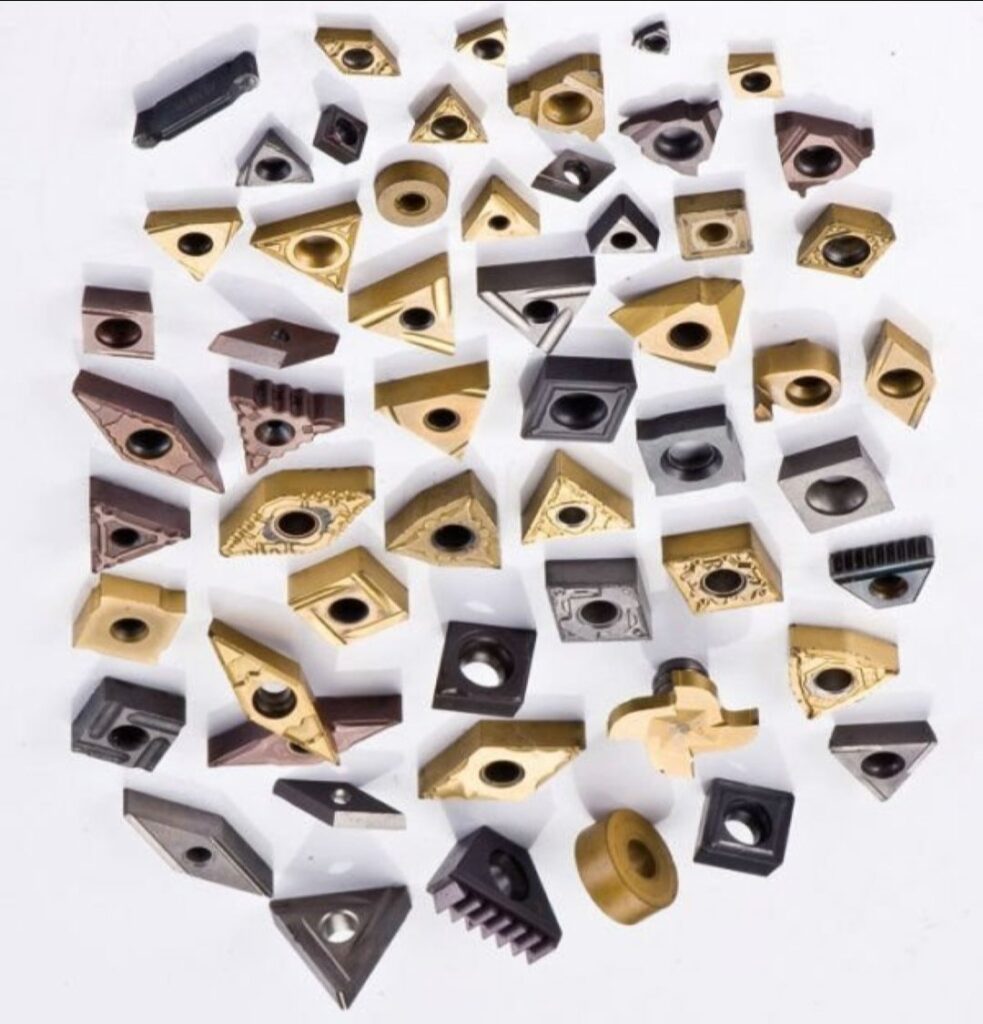
Composition and Characteristics
Understanding the composition and characteristics of carbide insert shims helps in selecting the right one for your application. Here’s a detailed table:
Material Composition | Properties | Characteristics |
---|---|---|
Tungsten Carbide | High hardness and wear resistance | Ideal for high-speed machining |
Cobalt | Provides toughness and binding | Enhances overall strength |
Titanium Carbide | High thermal stability | Suitable for high-temperature applications |
Tantalum Carbide | Improved toughness | Reduces brittleness |
Niobium Carbide | Corrosion resistance | Good for corrosive environments |
Hardness, Strength, and Wear Resistance
These three parameters are critical for evaluating the performance of carbide insert shims. Here’s a comparison table:
Parameter | Description | Impact |
---|---|---|
Hardness | Resistance to surface indentation | Higher hardness means better wear resistance |
Strength | Ability to withstand applied forces | Higher strength improves durability |
Wear Resistance | Ability to resist material loss due to friction | Essential for longer tool life |
Specifications, Sizes, and Shapes
Carbide insert shims come in various specifications to suit different needs. Here’s a detailed table:
Specification | Size Range | Shape | Standards |
---|---|---|---|
Thickness | 0.5mm to 5mm | Flat, angular, curved | ISO, ANSI, DIN |
Width | 10mm to 50mm | Rectangular, circular | ISO, ANSI, DIN |
Length | 20mm to 100mm | Various | ISO, ANSI, DIN |
Suppliers and Pricing Details
Knowing where to buy and how much to expect to pay is crucial. Here’s a table listing suppliers and pricing details:
Supplier | Price Range | Comments |
---|---|---|
Supplier A | $5 – $15 per piece | Wide range of standard sizes |
Supplier B | $10 – $20 per piece | Custom shims available |
Supplier C | $8 – $18 per piece | Bulk discounts offered |
Supplier D | $7 – $17 per piece | High-quality materials |
Supplier E | $9 – $19 per piece | Fast delivery options |
How to Select the Right Carbide Insert Shims
Choosing the right carbide insert shims can be daunting. Here’s a table to guide your selection process:
Criteria | Considerations | Recommendation |
---|---|---|
Material | Type of material being machined | Harder shims for harder materials |
Application | Specific machining operation | Specialized shims for complex tasks |
Size and Shape | Dimensions of the tool holder and insert | Custom shims for non-standard sizes |
Budget | Cost constraints | Balance between quality and cost |
Supplier | Reliability and availability | Reputable suppliers with good reviews |
Comparing Advantages and Limitations
Understanding the pros and cons of different carbide insert shims helps in making an informed decision. Here’s a comparison table:
Type | Advantages | Limitations |
---|---|---|
Flat Shims | Simple and easy to use | Limited support for complex shapes |
Angular Shims | Better support for angled inserts | More complex to manufacture |
Curved Shims | Ideal for inserts with curved edges | Higher cost |
Thicker Shims | Enhanced stability | Increased weight |
Thin Shims | High precision | Less durable |
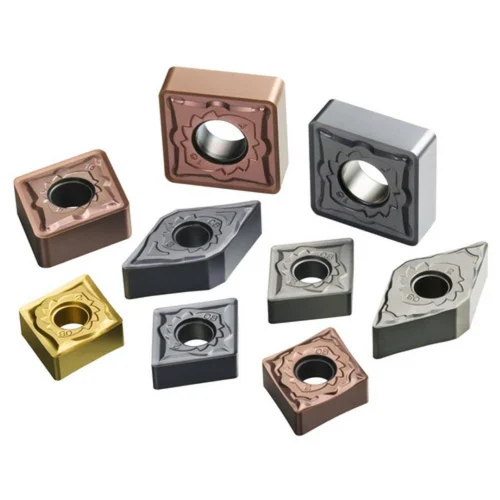
FAQ
Here are some common questions about carbide insert shims, answered in a tabular format for clarity:
Question | Answer |
---|---|
What are carbide insert shims? | They are components used to support and secure carbide inserts in cutting tools. |
Why are they important? | They provide stability, precision, and prolong tool life. |
What materials are they made from? | Typically, tungsten carbide, cobalt, titanium carbide, tantalum carbide, and niobium carbide. |
How do I choose the right shim? | Consider the material, application, size, shape, budget, and supplier. |
Can I get custom shims? | Yes, many suppliers offer custom shims for specific needs. |
What are the common types of shims? | Flat, angular, curved, thicker, thinner, and custom shims. |
Where can I buy carbide insert shims? | Various suppliers offer them, including Supplier A, B, C, D, and E. |
How much do they cost? | Prices range from $5 to $20 per piece, depending on the type and supplier. |
What are the key properties to look for? | Hardness, toughness, density, thermal conductivity, and corrosion resistance. |
What applications use carbide insert shims? | Turning, milling, drilling, grooving, and boring operations. |
Conclusion
Carbide insert shims are indispensable in the machining world, providing the necessary support and stability for carbide inserts. Understanding their types, applications, material properties, and how to select the right ones can significantly enhance your machining operations. Whether you’re looking for standard shims or custom solutions, this guide offers all the information you need to make an informed decision.