Carbide insert end mills are crucial tools in modern machining, known for their durability and precision. Whether you’re a seasoned machinist or just starting, understanding these tools can significantly impact your projects’ efficiency and outcome. This guide will delve into everything you need to know about carbide insert end mills, from their types and applications to material properties and how to select the right one for your needs.
Overview of Carbide Insert End Mills
Carbide insert end mills are cutting tools used in milling operations. They feature replaceable carbide inserts that provide a cost-effective and efficient solution for high-performance milling. These inserts are made from a combination of tungsten carbide and other metallic powders, offering exceptional hardness and wear resistance.
Carbide inserts are known for their ability to maintain a sharp cutting edge for extended periods, which is crucial for achieving high-quality finishes and precision in machining operations. Let’s dive deeper into the various aspects of carbide insert end mills.
Types of Carbide Insert End Mills
Different types of carbide insert end mills cater to various machining needs. Below is a detailed table summarizing the types:
Type | Description | Applications |
---|---|---|
Square End Mill | Features a square end for sharp corners and flat bottom cuts. | Slotting, profiling, and plunge cutting. |
Ball Nose End Mill | Has a rounded end, ideal for 3D contouring and milling complex shapes. | 3D milling, contouring, and complex surface cutting. |
Corner Radius End Mill | Combines the features of square and ball nose end mills with a radius at the corner. | Reduces chipping and extends tool life in corner cutting. |
Roughing End Mill | Designed with serrations for high material removal rates. | Heavy roughing operations and bulk material removal. |
Finishing End Mill | Provides a smooth finish, often used after roughing end mills. | Finishing cuts and achieving high surface quality. |
Tapered End Mill | Has a tapered profile for milling angled surfaces. | Mold making and machining of complex angles. |
High-Feed End Mill | Optimized for high feed rates and efficiency. | High-speed milling operations. |
Thread Mill | Used for thread milling operations. | Creating internal and external threads. |
Chamfer Mill | Designed for creating chamfers on edges. | Chamfering and deburring operations. |
Face Mill | Used for large surface area cuts. | Facing operations and large area material removal. |
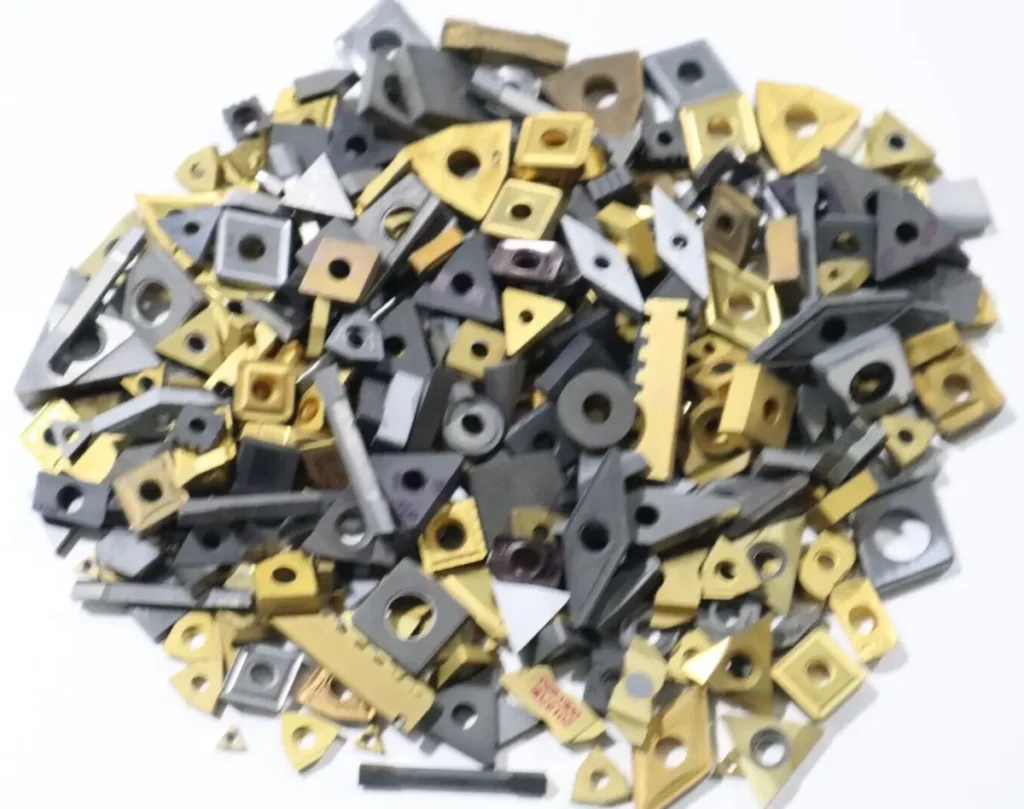
Applications of Carbide Insert End Mills
Carbide insert end mills find applications across various industries due to their versatility and robustness. Here’s a table outlining their primary applications:
Industry | Applications |
---|---|
Aerospace | Machining aircraft components, turbine blades, and structural parts. |
Automotive | Manufacturing engine parts, transmission components, and molds. |
Medical | Creating precision surgical instruments and implants. |
Mold and Die | Mold making, die sinking, and machining intricate cavities. |
Oil and Gas | Machining parts for drilling equipment and pipelines. |
Electronics | Fabricating components for electronic devices and circuits. |
Tool and Cutter Grinding | Sharpening and grinding cutting tools and inserts. |
General Engineering | Versatile applications in various machining tasks. |
Material Properties of Carbide Inserts
Understanding the material properties of carbide inserts is essential for selecting the right end mill for your specific application. The following table summarizes key material properties:
Property | Description |
---|---|
Hardness | Measures the resistance to deformation and wear. Typically ranges from 85 to 94 HRA. |
Toughness | Ability to absorb energy and resist fracture. Essential for impact resistance. |
Wear Resistance | Resistance to abrasion and material loss during machining. |
Thermal Conductivity | Ability to conduct heat away from the cutting edge. |
Chemical Stability | Resistance to chemical reactions and oxidation. |
Composition and Characteristics of Carbide Inserts
Carbide inserts are made from a mixture of tungsten carbide (WC) and metallic binders like cobalt (Co). The composition significantly affects their performance. Here’s a detailed table:
Composition | Percentage | Characteristics |
---|---|---|
Tungsten Carbide (WC) | 70-90% | Provides hardness and wear resistance. |
Cobalt (Co) | 5-20% | Enhances toughness and binding properties. |
Titanium Carbide (TiC) | 1-5% | Increases resistance to cratering and oxidation. |
Tantalum Carbide (TaC) | 1-5% | Improves high-temperature strength and hardness. |
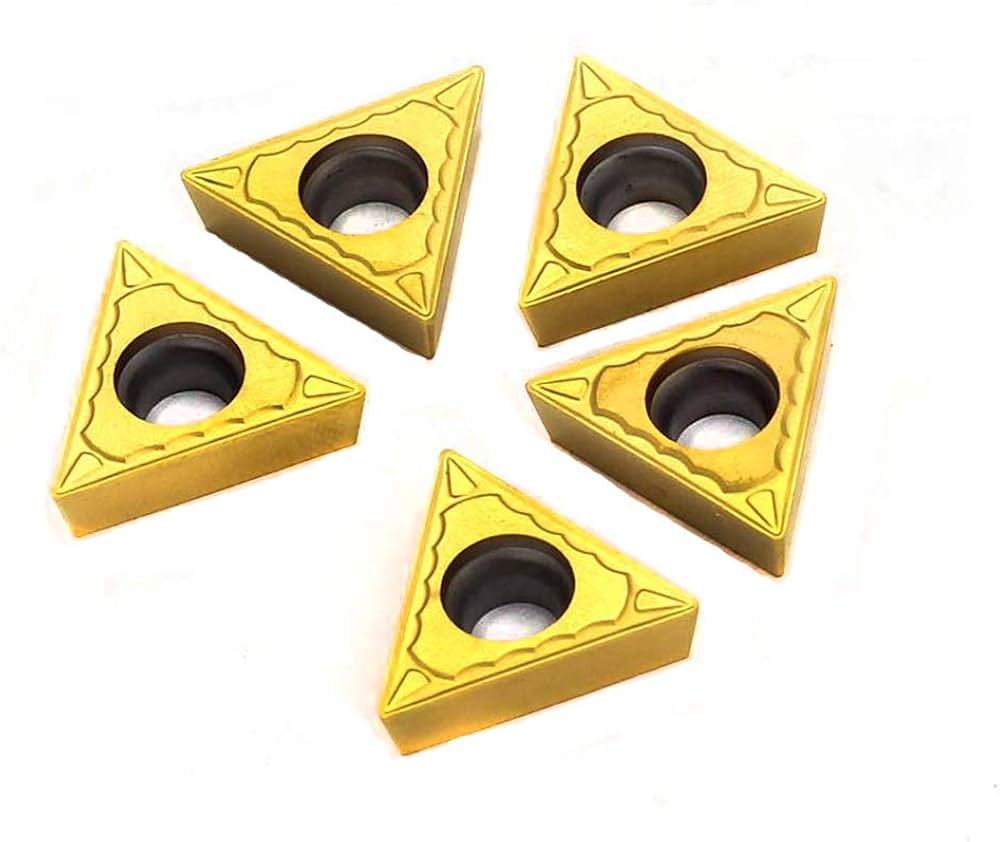
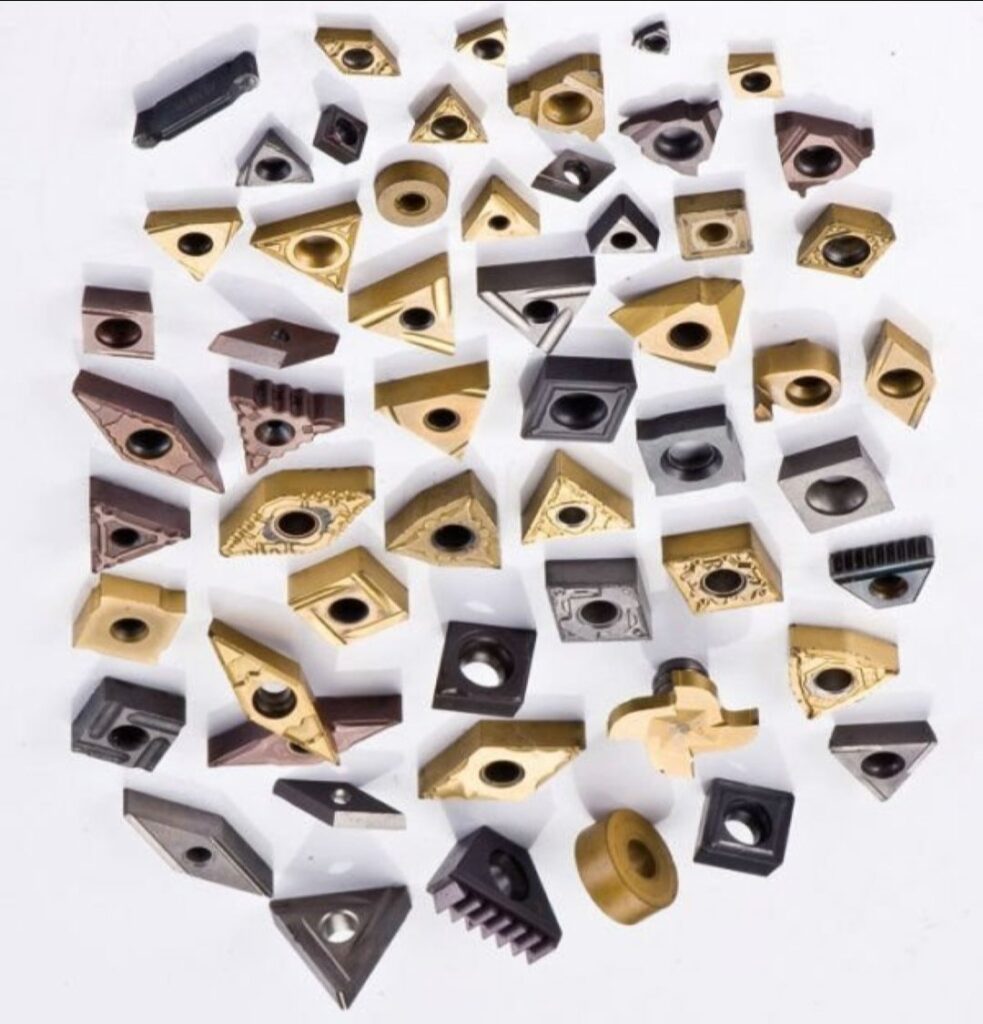
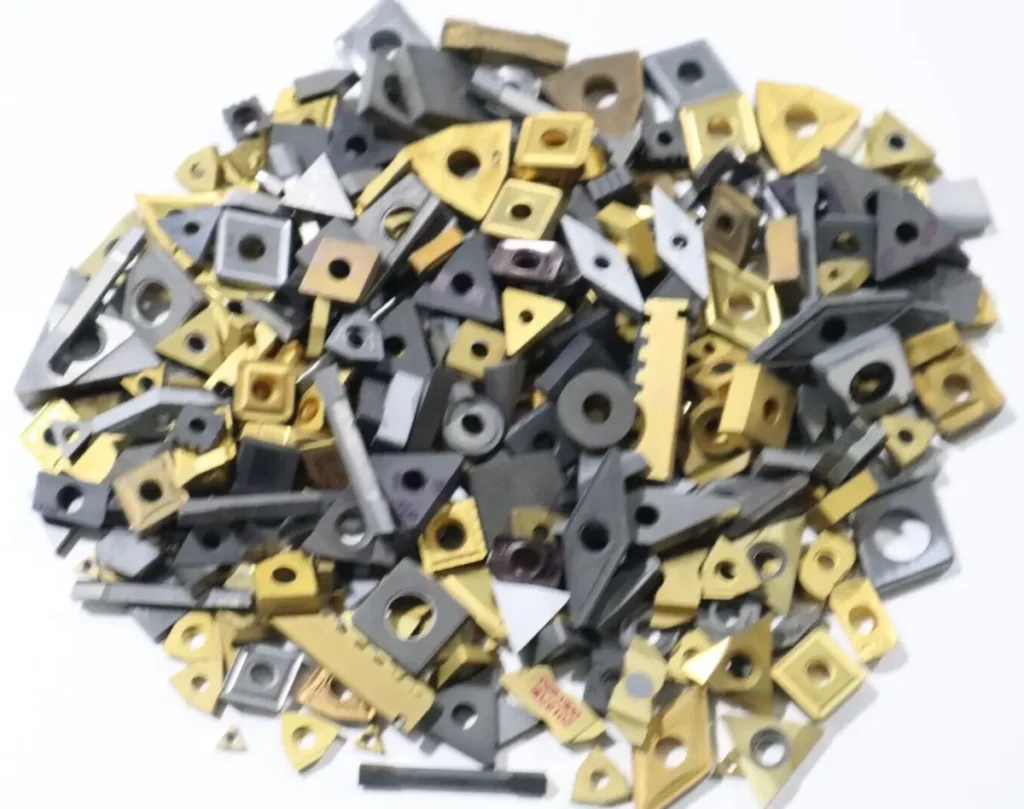
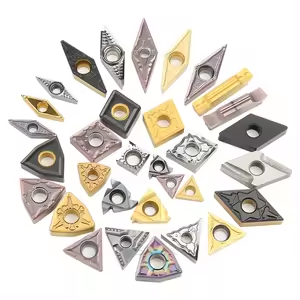
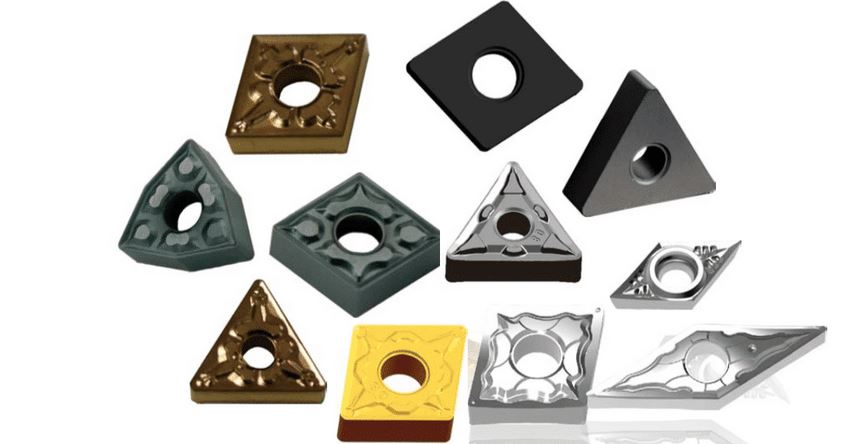
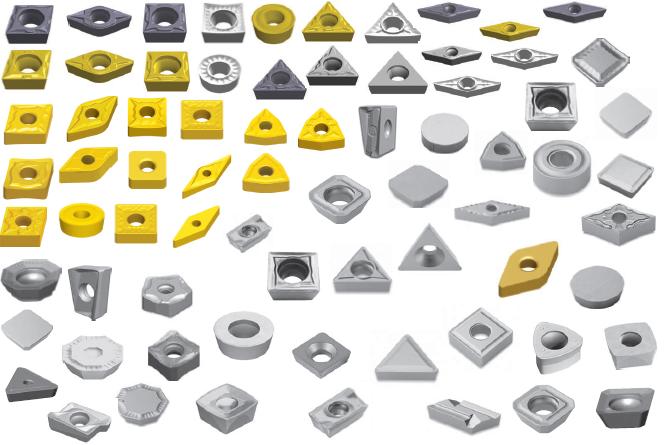
Hardness, Strength, and Wear Resistance
The following table highlights the hardness, strength, and wear resistance of carbide inserts:
Property | Measurement |
---|---|
Hardness | 85-94 HRA |
Compressive Strength | 4000-6500 MPa |
Transverse Rupture Strength | 1500-2500 MPa |
Wear Resistance | High |
Specifications, Sizes, Shapes, and Standards
Carbide insert end mills come in various specifications, sizes, and shapes. Below is a summary table:
Specification | Details |
---|---|
Sizes | Diameters ranging from 1mm to 50mm. |
Shapes | Square, round, hexagonal, octagonal, and custom shapes. |
Standards | ISO, ANSI, DIN, and other industry standards. |
Suppliers and Pricing Details
Knowing where to source carbide insert end mills and their pricing is essential. Here’s a table summarizing key suppliers and their pricing:
Supplier | Price Range (USD) | Contact Information |
---|---|---|
Kennametal | $20 – $200 | www.kennametal.com |
Sandvik Coromant | $25 – $250 | www.sandvik.coromant.com |
Seco Tools | $30 – $220 | www.secotools.com |
Walter Tools | $35 – $240 | www.walter-tools.com |
ISCAR | $28 – $210 | www.iscar.com |
Kyocera | $22 – $190 | www.kyocera-unimerco.com |
Mitsubishi Materials | $24 – $230 | www.mmc.co.jp |
Sumitomo Electric | $26 – $210 | www.sumitomotool.com |
YG-1 | $18 – $180 | www.yg1.kr |
Tungaloy | $29 – $220 | www.tungaloy.com |
Selecting the Right Carbide Insert End Mill
Choosing the right carbide insert end mill involves considering various factors. Here’s a detailed guide:
Factor | Considerations |
---|---|
Material to be Machined | Different materials require specific insert properties and geometries. |
Machining Operation | Select based on roughing, finishing, threading, or chamfering needs. |
Cutting Speed and Feed | Higher speeds and feeds require inserts with high thermal stability. |
Tool Holder Compatibility | Ensure the insert fits the tool holder system. |
Cost and Budget | Balance between performance needs and budget constraints. |
Supplier Support | Availability of technical support and after-sales service. |
Advantages and Limitations of Carbide Insert End Mills
Understanding the pros and cons of carbide insert end mills can help in making an informed decision. Here’s a comparison:
Advantages | Limitations |
---|---|
High Hardness and Wear Resistance | Higher Initial Cost |
Precision and High-Quality Finishes | Requires Correct Setup and Maintenance |
Replaceable Inserts Reduce Downtime | Potential for Chipping if Misused |
Versatility Across Different Materials | May Require Specialized Holders |
Extended Tool Life | Complexity in Selection for Specific Applications |
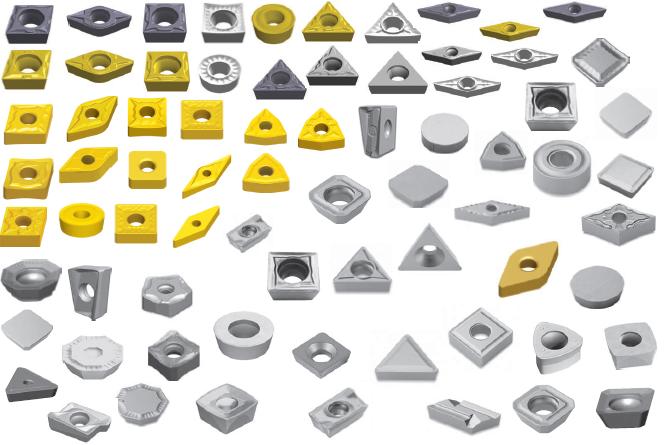
FAQs
Question | Answer |
---|---|
What are carbide inserts made of? | Primarily tungsten carbide, cobalt, and other metallic powders. |
Why choose carbide over other materials? | Superior hardness, wear resistance, and longevity. |
How to select the right insert geometry? | Based on the material and type of machining operation |
Can carbide inserts be resharpened? | Typically, no. They are designed to be replaced. |
What is the typical lifespan of a carbide insert? | Depends on use, but generally lasts longer than HSS or cobalt tools. |
How to maximize the life of carbide inserts? | Proper setup, appropriate cutting parameters, and regular maintenance. |
Are carbide inserts suitable for all materials? | Yes, but specific grades and geometries are better for certain materials. |
What are the common sizes available? | Sizes range from 1mm to 50mm in diameter. |
How do I know when to replace an insert? | Signs include poor surface finish, increased cutting forces, and visible wear. |
What are the cost considerations for carbide inserts? | Higher upfront cost but lower overall cost due to longevity and performance. |
Conclusion
Carbide insert end mills are essential tools in modern machining, offering precision, durability, and versatility. By understanding their types, applications, material properties, and how to select the right one, you can significantly enhance your machining operations’ efficiency and quality. Whether you’re working in aerospace, automotive, medical, or general engineering, investing in the right carbide insert end mills can make a substantial difference in your projects’ success.