Introduction
Carbide saw tips are essential components in various cutting tools, known for their unmatched hardness and wear resistance. However, not all carbide grades are created equal. Different grades of carbide are engineered to meet specific cutting requirements, each offering unique properties tailored for distinct applications. In this comprehensive guide, we will explore the various types of carbide grades used for saw tips and delve into their distinctive properties to help you make informed decisions for your cutting needs.
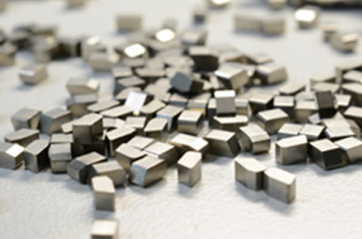
Understanding Carbide Compositions
Carbide is a composite material composed of carbide particles (typically tungsten carbide) and a binder metal (usually cobalt). The proportion of these components can vary, resulting in different carbide grades with unique physical and mechanical properties.
Key Components
- Tungsten Carbide (WC): Provides hardness and wear resistance.
- Cobalt (Co): Acts as a binder, offering toughness and impact resistance.
Types of Carbide Grades
Carbide grades are typically categorized based on their composition and intended applications. Here are some of the most common types:
1. Micrograin Carbide
Micrograin carbide features extremely fine carbide particles, usually less than 1 micron in size. This grade offers a combination of high hardness and toughness, making it suitable for precise cutting applications.
- Properties: High hardness, excellent edge retention, moderate toughness.
- Applications: Precision cutting, woodworking, and machining non-ferrous metals.
2. Sub-Micrograin Carbide
Sub-micrograin carbide has even finer carbide particles than micrograin, typically less than 0.5 microns. This grade provides exceptional hardness and wear resistance, ideal for high-precision and high-speed cutting.
- Properties: Superior hardness, excellent wear resistance, high edge stability.
- Applications: High-speed cutting, precision machining, and finishing operations.
3. Medium Grain Carbide
Medium grain carbide has larger carbide particles, usually between 1 to 5 microns. This grade balances hardness and toughness, suitable for a wide range of cutting tasks.
- Properties: Good hardness, balanced toughness, versatile performance.
- Applications: General-purpose cutting, woodworking, and metalworking.
4. Coarse Grain Carbide
Coarse grain carbide consists of larger carbide particles, typically greater than 5 microns. This grade emphasizes toughness over hardness, making it suitable for heavy-duty cutting applications where impact resistance is crucial.
- Properties: High toughness, good impact resistance, moderate hardness.
- Applications: Heavy-duty cutting, rough machining, and applications involving high impact forces.
5. Ultra-Fine Grain Carbide
Ultra-fine grain carbide features extremely small carbide particles, less than 0.2 microns. This premium grade offers unparalleled hardness and sharpness, ideal for the most demanding cutting tasks.
- Properties: Maximum hardness, superior edge sharpness, excellent wear resistance.
- Applications: Ultra-precision cutting, micro-machining, and high-performance applications.
Comparing Carbide Grades
To better understand the differences between these carbide grades, let’s compare their properties and typical applications in a table.
Carbide Grade | Particle Size | Hardness | Toughness | Wear Resistance | Typical Applications |
---|---|---|---|---|---|
Micrograin | < 1 micron | High | Moderate | High | Precision cutting, woodworking, non-ferrous metals |
Sub-Micrograin | < 0.5 microns | Superior | Moderate | Excellent | High-speed cutting, precision machining, finishing |
Medium Grain | 1 – 5 microns | Good | Good | Good | General-purpose cutting, woodworking, metalworking |
Coarse Grain | > 5 microns | Moderate | High | Moderate | Heavy-duty cutting, rough machining, high impact forces |
Ultra-Fine Grain | < 0.2 microns | Maximum | Moderate | Superior | Ultra-precision cutting, micro-machining, high-performance applications |
Description: This table highlights the key properties of different carbide grades, providing a clear comparison to help you select the appropriate grade for your specific cutting needs.
The Role of Binder Content
The binder content in carbide grades significantly affects their properties. Higher cobalt content increases toughness and impact resistance, while lower cobalt content enhances hardness and wear resistance.
High Binder Content
- Properties: Increased toughness, higher impact resistance, lower hardness.
- Applications: Heavy-duty cutting, rough machining, applications involving high impact forces.
Low Binder Content
- Properties: Increased hardness, superior wear resistance, lower toughness.
- Applications: Precision cutting, high-speed machining, finishing operations.
Innovations in Carbide Grades
Recent advancements in carbide technology have led to the development of innovative grades with enhanced properties. Here are some notable innovations:
1. Nanostructured Carbide
Nanostructured carbide features carbide particles on the nanometer scale. This advanced grade offers exceptional hardness, toughness, and wear resistance, making it suitable for high-performance cutting applications.
- Properties: Exceptional hardness, superior toughness, excellent wear resistance.
- Applications: High-performance cutting, precision machining, aerospace, and automotive industries.
2. Gradient Carbide
Gradient carbide consists of a graded structure, where the composition changes gradually from the surface to the core. This design enhances both surface hardness and core toughness, providing a balance of wear resistance and impact strength.
- Properties: High surface hardness, tough core, excellent wear resistance.
- Applications: Cutting tools for demanding applications, such as metalworking and mining.
3. Coated Carbide
Coated carbide involves applying advanced coatings to the carbide substrate, further enhancing its properties. Common coatings include titanium nitride (TiN), titanium carbonitride (TiCN), and diamond-like carbon (DLC).
- Properties: Enhanced hardness, reduced friction, improved wear resistance.
- Applications: High-speed cutting, precision machining, cutting abrasive materials.
Practical Applications of Carbide Grades
Different carbide grades are optimized for various cutting applications. Here are some practical examples:
1. Woodworking
- Micrograin Carbide: Ideal for precision cutting and woodworking, providing sharp edges and excellent wear resistance.
- Medium Grain Carbide: Suitable for general-purpose woodworking, balancing hardness and toughness.
2. Metalworking
- Sub-Micrograin Carbide: Perfect for high-speed machining and finishing operations, offering high hardness and wear resistance.
- Coarse Grain Carbide: Suitable for heavy-duty cutting and rough machining, providing high toughness and impact resistance.
3. Plastic Cutting
- Ultra-Fine Grain Carbide: Ideal for ultra-precision cutting and micro-machining of plastics, offering maximum hardness and sharpness.
- Micrograin Carbide: Suitable for general plastic cutting, providing good edge retention and wear resistance.
4. Construction
- Coarse Grain Carbide: Suitable for heavy-duty cutting and rough machining in construction, providing high toughness and impact resistance.
- Gradient Carbide: Ideal for demanding cutting applications, offering a balance of surface hardness and core toughness.
Related Content
Material Science in Carbide Manufacturing
Understanding the role of material science in carbide manufacturing can help optimize the performance and properties of carbide grades. Explore the impact of different additives and binders on carbide properties.
Industry-Specific Design Considerations
Different industries have unique requirements for carbide saw tips. Learn how to optimize carbide grades for specific applications in woodworking, metalworking, plastic cutting, and construction.
FAQ
Q1: What is the difference between micrograin and sub-micrograin carbide?
A1: Micrograin carbide features carbide particles less than 1 micron in size, offering high hardness and moderate toughness. Sub-micrograin carbide has even finer particles, typically less than 0.5 microns, providing superior hardness and wear resistance, ideal for high-speed and precision cutting.
Q2: How does the binder content affect the properties of carbide grades?
A2: Higher binder content increases toughness and impact resistance but reduces hardness and wear resistance. Lower binder content enhances hardness and wear resistance but decreases toughness. Selecting the appropriate binder content depends on the specific cutting application.
Q3: What are the advantages of using coated carbide grades?
A3: Coated carbide grades offer enhanced hardness, reduced friction, and improved wear resistance. Common coatings like titanium nitride (TiN), titanium carbonitride (TiCN), and diamond-like carbon (DLC) extend the tool’s lifespan and improve cutting performance, especially in high-speed and abrasive applications.
Q4: What cutting applications are best suited for coarse grain carbide?
A4: Coarse grain carbide, with larger carbide particles, provides high toughness and impact resistance, making it suitable for heavy-duty cutting, rough machining, and applications involving high impact forces. It is ideal for construction and metalworking tasks requiring robust cutting action.
Q5: How do nanostructured carbide grades enhance cutting performance?
A5: Nanostructured carbide grades feature carbide particles on the nanometer scale, offering exceptional hardness, toughness, and wear resistance. These advanced grades are suitable for high-performance cutting applications, including precision machining in aerospace and automotive industries.
Want to buy Carbide Tipped Saw Tips at a good price? Please click here.