Overview of Carbide for Mining Tools
Carbide is the unsung hero of the mining industry, playing a crucial role in the efficiency, durability, and performance of mining tools. This unique material, known for its extreme hardness and resistance to wear, is indispensable for tasks like drilling, cutting, and boring. But what makes carbide so special? And why is it a game-changer for mining operations?
Mining involves intense wear and tear on equipment due to constant exposure to abrasive materials like rock and ore. Carbide, specifically tungsten carbide, steps in as the optimal solution, offering unmatched toughness and longevity. It’s not just a material—it’s the backbone of many heavy-duty tools.
Let’s dive into the nitty-gritty of carbide’s applications, its advantages, how it’s used, and everything in between.
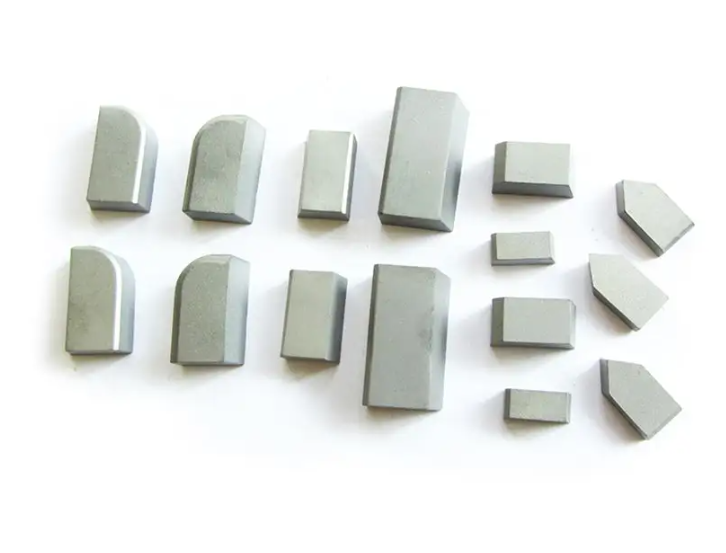
What is Carbide?
Carbide, especially tungsten carbide, is a compound of tungsten and carbon. Known for its extreme hardness and high resistance to temperature, it’s often combined with cobalt to create alloys for industrial uses. Its molecular structure gives it an edge over other materials, making it a prime choice for mining tools.
Fun Fact: Carbide ranks just below diamond on the Mohs scale of hardness, making it a top contender in industrial applications.
Why does this matter for mining? Because every drill bit or cutting tool needs to withstand the abrasive nature of rocks and minerals. Carbide delivers on this front with aplomb.
Advantages of Carbide for Mining Tools
- Durability and Longevity: Carbide tools last significantly longer than those made from traditional materials like steel. This reduces replacement costs and operational downtime.
- Heat Resistance: Carbide retains its hardness at high temperatures, crucial for high-speed drilling or cutting operations.
- Wear Resistance: Its superior wear resistance makes it ideal for repetitive and high-pressure tasks in mining.
- Precision: Carbide tools maintain their sharpness longer, ensuring consistent performance and efficiency.
Comparison: Steel vs. Carbide
Feature | Steel Tools | Carbide Tools |
---|---|---|
Hardness | Moderate | Extremely High |
Wear Resistance | Low | High |
Heat Tolerance | Limited | Excellent |
Lifespan | Shorter | Much Longer |
Applications of Carbide in Mining
Carbide is a workhorse material in the mining industry. Its most common applications include:
- Drill Bits: Used in boring through hard rock or mineral deposits.
- Cutting Tools: For shaping, breaking, and cutting raw materials.
- Boring Bars: Essential for creating precise tunnels or holes.
- Wear Parts: Used in equipment subjected to intense friction.
Whether it’s a rotary drill bit or a shearer blade, carbide plays a pivotal role in mining productivity.
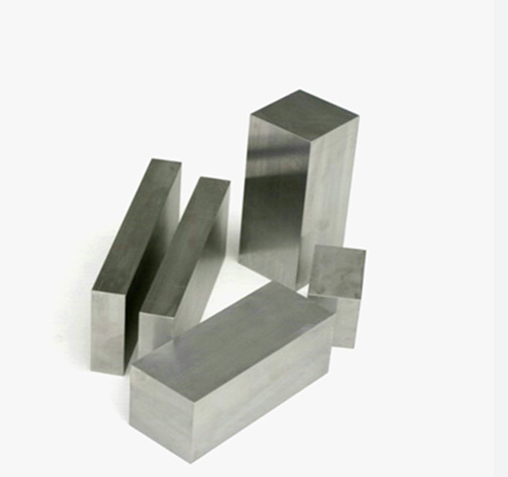
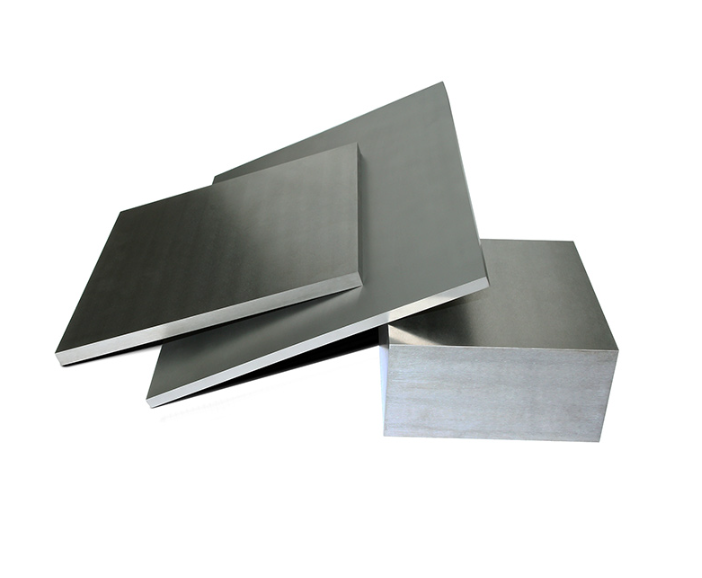
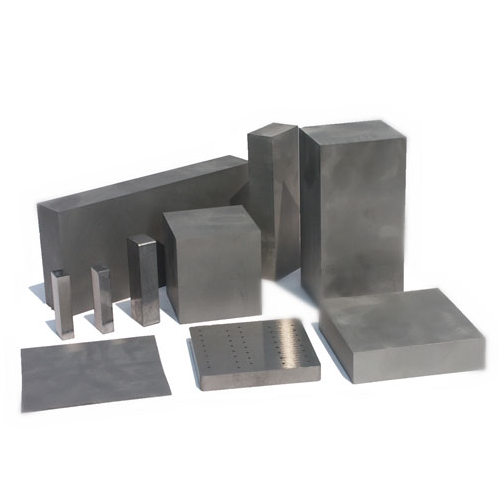
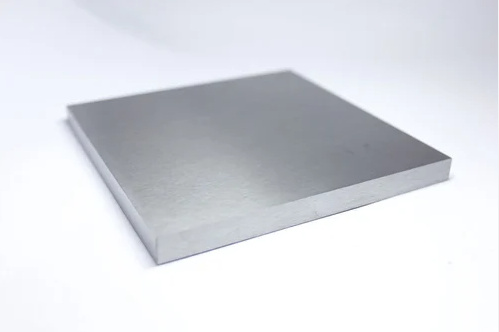
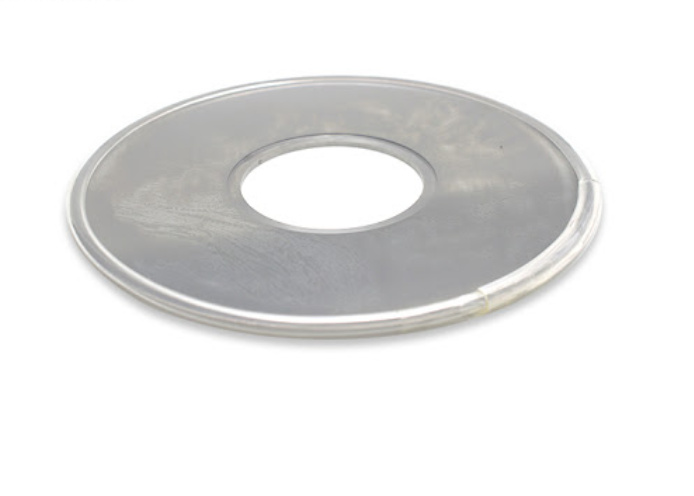
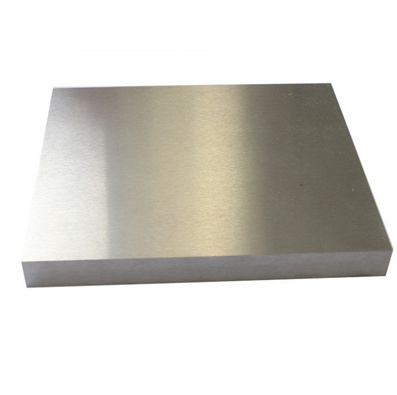
How to Operate Carbide for Mining Tools
Using carbide-based tools isn’t rocket science, but it does demand some best practices for optimal performance:
- Choose the Right Tool: Match the carbide tool to the task. For instance, use specific drill bits for different rock hardness levels.
- Proper Cooling: Always use a cooling fluid to prevent overheating and maintain tool integrity.
- Regular Maintenance: Inspect carbide tools for wear and replace them promptly to avoid inefficiencies.
When operated correctly, carbide tools can take your mining operations to the next level.
Maintaining Carbide Tools: Tips and Tricks
Maintenance is the secret sauce to extending the life of carbide tools. Here are the essentials:
- Clean Regularly: Remove debris and residue after every use.
- Avoid Excessive Heat: High temperatures can degrade the binder material, even in carbide.
- Sharpen Periodically: Dull tools not only underperform but also stress equipment.
Use ultrasonic cleaners for intricate tools and proper storage solutions to prevent chipping or damage.
Choosing the Right Carbide Tools
When picking carbide tools, focus on these parameters:
Parameter | Details |
---|---|
Grade | Tungsten carbide grades vary by application. Look for high cobalt content for tough tasks. |
Size and Shape | Ensure the tool fits your specific machinery. |
Price Range | Higher grades may cost more but offer better longevity. |
Suppliers and Price Range for Carbide Tools
When sourcing carbide tools, consider reputable suppliers and their offerings.
Supplier | Price Range ($) | Features |
---|---|---|
Supplier A | 50–1000 | High-grade tungsten carbide options |
Supplier B | 70–1500 | Customizable tools |
Supplier C | 100–2000 | Specialty mining tools |
Installation, Operation, and Maintenance of Carbide Tools
Process | Key Points |
---|---|
Installation | Securely attach to machinery, ensuring no misalignment. |
Operation | Operate at recommended speeds and use cooling systems. |
Maintenance | Regular cleaning and inspections are a must. |
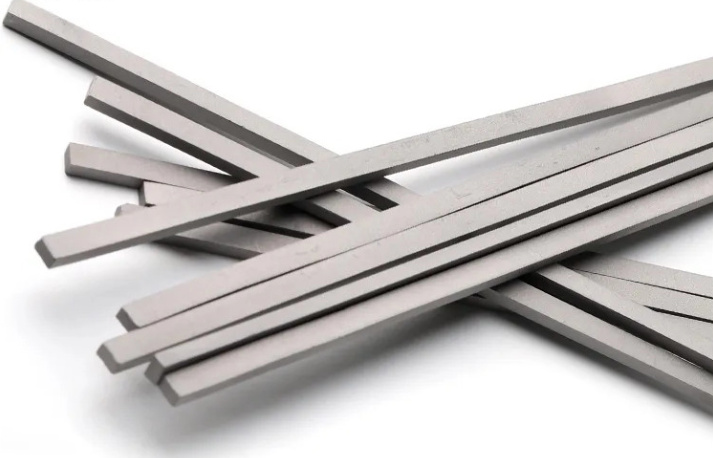
Pros and Cons of Carbide Tools
Feature | Advantages | Limitations |
---|---|---|
Durability | Long-lasting, reducing costs | Higher upfront cost |
Performance | Exceptional at high speeds | Requires expertise to maintain |
FAQ
Question | Answer |
---|---|
What makes carbide so durable? | Its unique molecular structure and high density. |
Can carbide tools be recycled? | Yes, many suppliers offer recycling programs. |
Are carbide tools worth the cost? | Absolutely, due to their long lifespan and efficiency. |