The Importance of Carbides in the Automotive Industry
Carbides have emerged as a game-changer in modern vehicle manufacturing. With growing demand for lightweight, durable, and wear-resistant materials, automakers are increasingly turning to carbide-based components. Whether it’s improving the longevity of cutting tools used in machining or enhancing the performance of vehicle parts, carbide plays a crucial role in making cars more efficient and robust.
Modern vehicles need materials that withstand high temperatures, extreme friction, and heavy loads. Carbides—especially tungsten, titanium, and silicon-based compositions—are tailored to meet these rigorous conditions, ensuring minimal wear and extended service life for critical components.
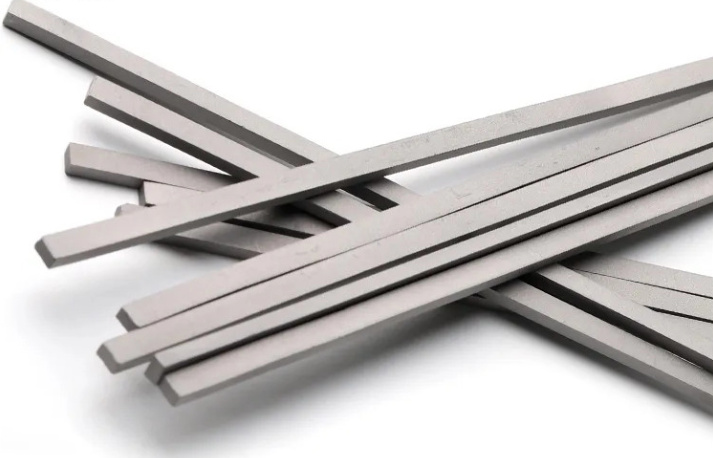
Why Are Car Manufacturers Increasingly Using Carbides?
The shift toward carbide materials in the automotive sector isn’t just a trend—it’s a necessity. With advancements in electric vehicles (EVs), hybrid technologies, and fuel efficiency regulations, manufacturers require stronger and more heat-resistant materials. Carbides offer:
- Superior Hardness – They are much harder than steel, improving the longevity of automotive tools and components.
- High Wear Resistance – Ideal for components that undergo friction, reducing replacement frequency.
- Heat Tolerance – Perfect for high-temperature applications, especially in internal combustion engines and EV powertrains.
- Efficiency Boost – Carbides enhance machining precision, reducing material waste and production costs.
By adopting carbide-based components, carmakers can develop high-performance vehicles that last longer, perform better, and require less maintenance.
What Are Carbides? Definition and Main Components
Carbides are compounds composed of carbon and a metal element, typically tungsten (WC), titanium (TiC), or silicon (SiC). These materials are known for their exceptional hardness, strength, and resistance to wear. Some of the most commonly used carbides in the automotive sector include:
- Tungsten Carbide (WC) – Extremely hard and used for cutting tools, wear parts, and high-performance coatings.
- Titanium Carbide (TiC) – Known for its strength and heat resistance, often used in aerospace and automotive components.
- Silicon Carbide (SiC) – Excellent thermal conductivity, making it ideal for EV inverters and semiconductors.
The combination of these materials with binders like cobalt or nickel ensures that carbide-based products offer unmatched durability in extreme conditions.
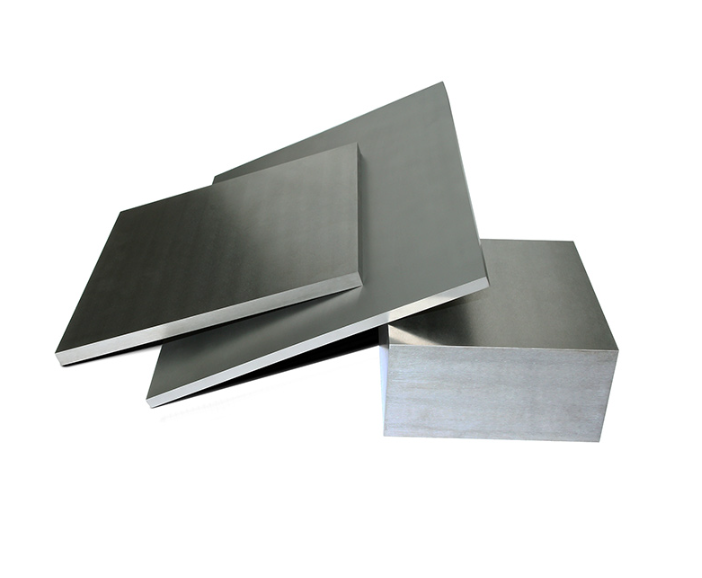
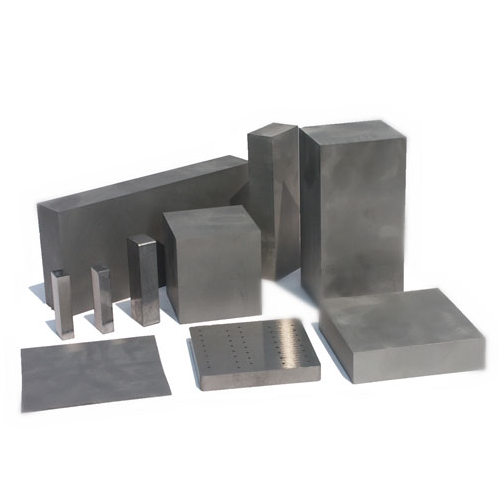
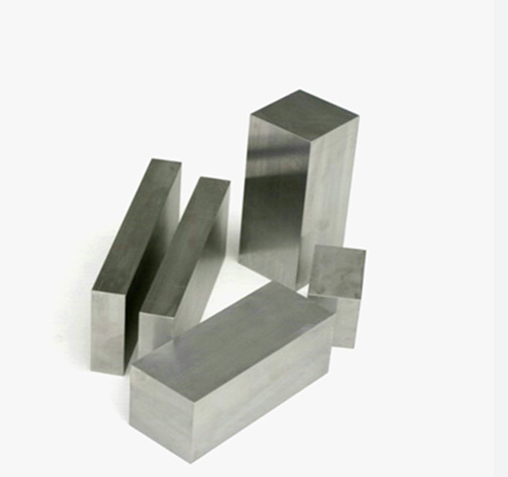
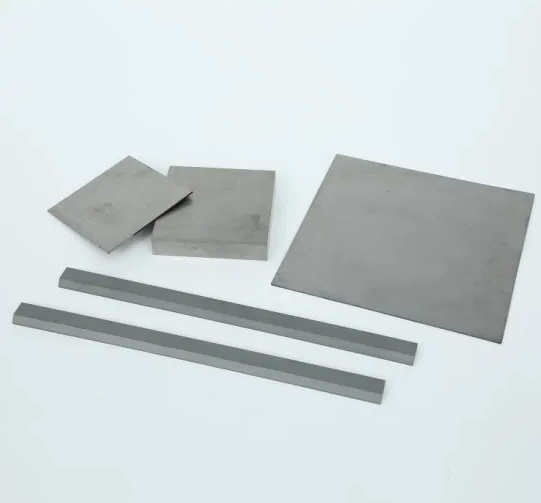

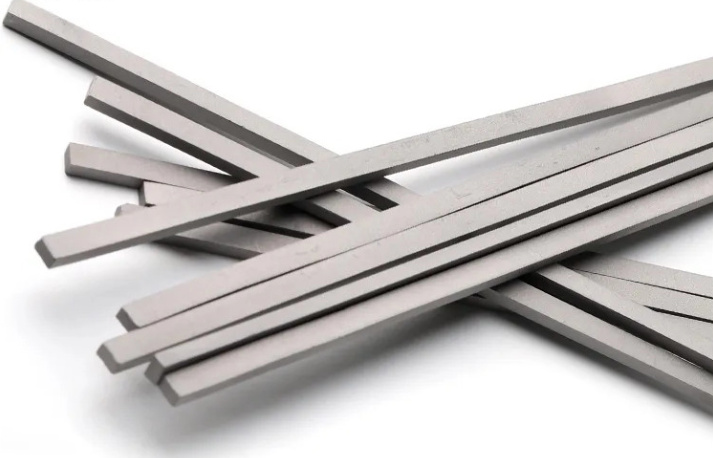
Key Applications of Carbide in the Automotive Industry
Application | Description |
---|---|
Cutting Tools & Machining | Carbide-tipped tools are used in milling, drilling, and cutting automotive components with precision. |
Dies & Molds | Carbide dies enhance the durability of stamping and forming processes in vehicle manufacturing. |
Engine Components | Silicon carbide parts improve heat resistance in combustion chambers and exhaust systems. |
Brake Systems | Tungsten carbide coatings increase wear resistance in high-performance braking systems. |
Suspension Systems | Carbide-reinforced components extend the life of shock absorbers and suspension arms. |
Bearings & Seals | Carbide-based bearings reduce friction and improve efficiency in rotating components. |
Power Electronics | Silicon carbide is crucial for EV inverters, enhancing power efficiency and thermal management. |
Advantages of Using Carbide in Automotive Manufacturing
Advantage | Benefit to Automotive Industry |
---|---|
Extreme Hardness | Ensures longevity and durability of tools and components. |
Wear Resistance | Reduces the need for frequent part replacements. |
Heat Resistance | Ideal for high-temperature applications such as engines and EV power systems. |
Precision & Accuracy | Enhances machining processes, improving vehicle part quality. |
Lightweight Performance | Helps reduce vehicle weight, improving fuel efficiency. |
Corrosion Resistance | Extends the life of parts exposed to harsh environments. |
Future Trends of Carbide in the Automotive Industry
The automotive industry is undergoing a transformation with the increasing adoption of carbide materials. Here are some trends shaping the future:
- Expansion in Electric Vehicles (EVs) – Silicon carbide is revolutionizing power electronics, improving battery efficiency and charging speed.
- Advanced Coatings – New carbide coatings are reducing wear and increasing component lifespans.
- 3D Printing & Additive Manufacturing – Carbide-based powders are being used in cutting-edge manufacturing techniques for custom automotive parts.
- Sustainability & Recycling – Efforts are being made to recycle tungsten and other carbide materials to reduce environmental impact.
These innovations are making carbide an indispensable material for the next generation of vehicles.
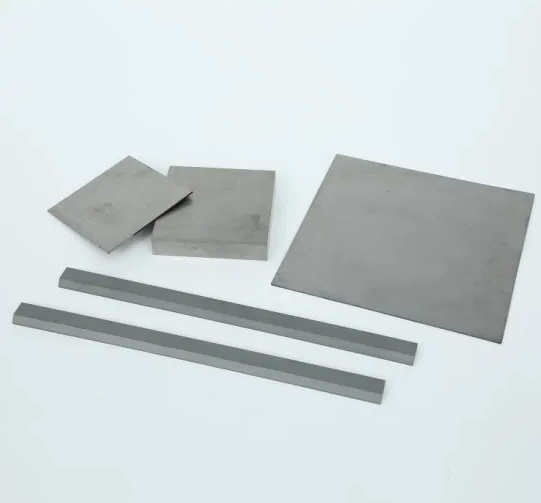
FAQ
Question | Answer |
---|---|
What are carbide rods used for in the automotive industry? | Carbide rods are used in high-precision drilling, milling, and cutting operations, ensuring superior wear resistance. |
Why choose tungsten carbide over regular steel for drilling? | Tungsten carbide offers extreme hardness, heat resistance, and durability, making it ideal for automotive machining. |
How does carbide improve drilling efficiency? | Carbide tools maintain sharpness longer, reducing tool wear and increasing precision in metalworking. |
Can carbide rods be used for both manual and CNC machining? | Yes, carbide rods are suitable for both manual and automated CNC machining, offering consistent performance. |
Are carbide rods environmentally friendly? | Many carbide rods are made from recycled materials, reducing their environmental impact. |