Carbide flat plates are an important material used across various industries for their extreme hardness and wear resistance properties. This article provides a comprehensive overview of carbide flat plates, their composition, properties, applications, specifications, pricing, comparisons, and more.
Overview
Carbide flat plates are plates made from cemented carbides with exceptional hardness usually well over 2000 HV. Carbide plates offer superior wear resistance, strength, and durability compared to common steel plates in applications involving high contact stresses, abrasion, corrosion, and dynamic impacts.
Some key details about carbide flat plates:
- Made from cemented carbides usually containing tungsten carbide along with cobalt, titanium, tantalum carbides etc.
- Hardness ranging from ~85 HRA to even 95 HRA depending on grade
- Tensile strength up to 3500 MPa, can withstand very high compressive stresses
- Stiffness and resistance to bending stresses also very high
- Chemically inert, highly resistant to corrosion and oxidation
- Withstand temperature fluctuations ranging from cryogenic to ~1000°C
- Dimensional stability better than steel with lower thermal expansion
- Electrically conductive, thermal shock resistant, non-magnetic
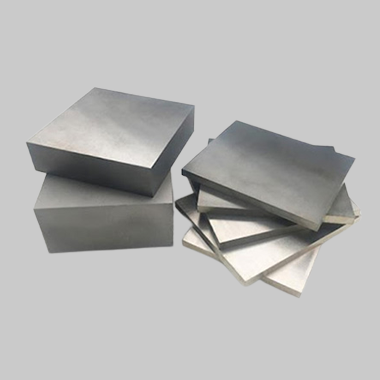
Carbide Flat Plate Composition
Carbide plates contain the following major elements in their metallurgical composition:
Element | Composition Range |
---|---|
Tungsten Carbide | 85-97% |
Cobalt | 3-12% |
Titanium Carbide | 0-8% |
Tantalum Carbide | 0-8% |
Tungsten carbide is the primary constituent which gives cemented carbides their extreme hardness, strength, stiffness and wear resistance. Cobalt acts as the matrix binder which holds the carbide particles together. Titanium, tantalum carbides enhance properties further when added.
The relative proportions of these metal carbides and binder can be varied to obtain different grades of cemented carbides optimised for specific applications. The powder metallurgy manufacturing process allows very homogeneous mixing and distribution of the carbide compounds in the binder matrix.
Mechanical Properties
The outstanding mechanical properties of tungsten carbide flat plates are highlighted below:
Property | Values |
---|---|
Hardness | Up to 95 HRA |
Compressive Strength | Up to 8 GPa |
Flexural Strength | Up to 3.5 GPa |
Fracture Toughness | Up to 45 MPa√m |
Young’s Modulus | 500-700 GPa |
The high hardness of over 90 HRA makes them extremely wear resistant and well suited for working against abrasive surfaces or slurries. The strength and stiffness values are much higher than alternative materials, enabling use in heavy-duty structural parts. They also exhibit excellent dimensional stability across a wide temperature range and have high thermal conductivity for heat dissipation.
Corrosion & Wear Resistance
Carbide plates provide exceptional resistance to:
- Abrasive & Adhesive Wear
- Solid Particle Erosion
- Fretting Wear
- Cavitation & Slurry Erosion
- Corrosion in Acids, Alkalis, Organic Chemicals
- Oxidation Resistance up to ~1000°C
The primary wear and corrosion resistance mechanism is the high chemical inertness and hardness of the tungsten and other carbides. The cobalt binder also contributes by filling any pores.
Proper choice of carbide grade ensures longevity even in extremely demanding erosion-corrosion conditions with particle laden fluids or submerged highly acidic chemical exposure over long terms.
Applications of Carbide Flat Plates
Some typical applications which benefit from using carbide flat plates are:
Industry | Components | Benefits |
---|---|---|
Mining | Chute liners, Hopper plates | Wear & erosion resistance |
Dredging | Impellers, Slurry pipes | Hard particles handling |
Oil & Gas | Valve parts, Nozzles | Resist abrasion & corrosion |
Steel | Rollers, Die blocks | Strength & thermal stability |
Cement | Grinding drums, Separator cones | Withstand abrasion |
Paper & Pulp | Refiner plates, Screw conveyors | Resist erosion & chemicals |
Agriculture | Plough blades, Feed cutters | Wear resistance in soil |
Food Processing | Cutting blades, Nozzles | Corrosion & bacteria resistance |
The consistent material properties and composition of carbide allow reliable, predictable long-term performance in the harshest operating conditions.
Carbide Grades For Different Applications
Application | Recommended Grades |
---|---|
Wear Resistance | Micrograin grades with fine ~1 micron carbides |
Corrosion Resistance | Grades with >10% cobalt binder |
High Hardness | Ultrafine or nanograin <0.5 micron carbides |
Impact Resistance | Grades with some TiC and TaC content |
High Strength | Medium ~2-6 micron carbide particles |
Specifications
Carbide plates are available in standard or custom geometries and sizes as per application requirements:
Standard Size Range:
- Thickness: 2mm to 300mm
- Width & Length: Up to 2000mm x 5000mm respectivel
Surface Finish:
- Precision ground to under 1 micron Ra finish
- Polished finish also possible
Flatness Tolerance:
- Up to 0.02mm per linear foot
- Can be machined & ground to precise tolerances
Custom Shapes:
- Cutting, profile operations can shape complex geometries
- Formed plates for lining cylindrical vessels
- Threaded holes, inserts, contours as per drawings
Grades & Standards:
Standard | Grades | Hardness Range |
---|---|---|
ISO 513 | C1, C2, C3 etc. | Up to 95 HRA |
ASTM B274 | A, B, C, D etc. | 88-93 HRA |
DIN/EN | K01, K05, K10 etc. | 85-90 HRA |
The grade is selected based on application, properties needed, international standards followed etc. Custom proprietary grades also offered.
Pricing of carbide flat plate
Price Range:
- $20 to $300 per Kg
- $50 to $1000 per plate
Bulk discounts available on large orders.
Price Drivers:
- Carbide grade and purity
- Tolerances and finish
- Order quantity
- Level of customization
- Regional tariffs & taxes
Cost Saving Tips:
- Select standard sizes & common grades in production
- Combine multiple small orders for bulk pricing benefits
- Allow for longer, predictable lead times
- Enter annual rate contracts for high volume usage
- Qualify local manufacturers to save on logistics
Price Comparison With Alternatives:
Material | Price Per Kg |
---|---|
Tungsten Carbide | $100-300 |
Stainless Steel | $5-15 |
Hardened Steel | $10-25 |
Cast Iron | $2-6 |
Chrome Carbide Overlay | $30-60 |
Carbide plates offer much better wear properties and life cycle cost benefits compared to cheaper alternatives which may need very frequent replacement. The productivity and maintenance savings outweigh the higher initial price.
Manufacturers & Suppliers
Some leading global suppliers of carbide plates include:
Company | Locations | Grades | Capabilities |
---|---|---|---|
Kennametal | USA, Germany | K01-K40, Custom | Casting, Machining |
Sandvik | Sweden, India | GC20, Custom | Full Range Manufacturing |
Mitsubishi Materials | Japan | Custom | Casting, Surface Treatments |
Iscar | Israel, Asia | C1-C5 | Cutting, Profiling |
Kyocera | Japan | Custom Ultrafine | Advanced Powder Processing |
Besides these branded manufacturers, numerous regional producers and machine shops also offer fabrication and finishing services for standard or custom carbide plates.
Choosing suppliers capable of jointly designing and manufacturing integrated carbide components for specific applications results in the best performance. Local distributors stocking standard inventory can meet general purpose needs.
Comparison With Alternatives
Vs. Stainless Steel
Carbide | Stainless Steel | |
---|---|---|
Hardness | Much higher ~90 HRA | Lower ~200 BHN |
Strength | Higher 2-4X | Moderate |
Wear Resistance | Extremely high due to hardness | Low especially against abrasion |
Corrosion Resistance | High in most chemicals | Higher is most acids, alkalis |
Temperature Withstand | Better beyond 550°C | Lower softening point |
Relative Price | 5-10X costlier | Lower |
Ease of Machining | Challenging | Easy to machine and fabricate |
Vs. Hardened Tool Steel
Carbide | Hardened Steel | |
---|---|---|
Hardness Retention | Excellent at high temperatures | Rapid lowering beyond 500°C |
Thermal Properties | More dimensional stability | Higher expansion coefficient |
Fracture Resistance | Lower | Less brittle in thin sections |
Fabrication | Limited forming capability | Easier to machine and grind |
Reactive Metals | No limitations | Cannot handle titanium alloys etc. |
Part Integration | Difficult material transitions | Easier design flexibility |
Vs. Cast Iron & White Iron
Carbide | Cast/White Iron | |
---|---|---|
Hardness | Much more consistent | Variability in properties |
Range of Grades | Wider flexibility | Limited alloys |
Corrosion Resistance | Significantly better | Prone to chemical attack |
Component Size | Small plates & parts | Bulkier sections possible |
Fabrication | Controlled powder metallurgy process | Casting defects possible |
Among all competing materials, cemented carbides offer exceptional combinations of hardness, strength, chemical and temperature resistance required in extremely demanding applications. The advanced powder manufacturing and ability to engineer a range of possible carbide compositions and microstructures makes them indispensible despite higher price.
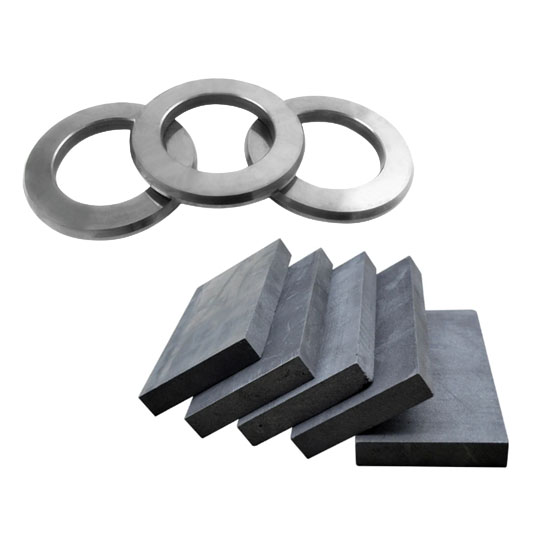
Pros & Cons
Advantages
- Extreme hardness for wear resistance
- Maintains strength at high temperature
- Chemically highly inert
- Customisable composition and microstructure
- Consistent homogenous properties
- Enables lightweight, compact component design
Limitations
- Brittle with lower fracture toughness
- Challenging to produce complex shapes
- Higher cost than steel alternatives
- Not easily repaired or modified after fabrication
- Requires cobalt binder limiting high temperature use
- Difficult to machine using conventional tools
Careful grading selection, design choices, and manufacturing process optimizations can mitigate the cons while fully benefiting from the numerous pros.
FAQs
Q: Are carbide plates suitable for food/pharma contact applications?
A: Yes, grades without cobalt and conforming to standards like ISO 23529 can be safely used. Corrosion resistance and non-porous nature also minimise bacterial adhesion.
Q: What thickness range is available for small worn liner parts?
A: Miniature plates up to 2mm thickness with very fine ~1 micron carbide grain size can be made via pressing and grinding. Brazed backing possible for thicker sections.
Q: Can carbide liners be installed in the field for faster repairs?
A: Yes, precise prefabricated replaceable carbide plate modules can be designed for quick installation using suitable screws, clamps and seals.
Q: How to clean oil, grease, carbon deposits from carbide surfaces?
A: Most chemical/solvent cleaning procedures for metals are applicable for carbides as well. Ensure to select compatible non-hazardous degreasers.
Q: What standards should suppliers comply with?
A: Reputable carbide manufacturers should follow quality systems per ISO 9001 along with metallurgical standards like ISO 513, ASTM B274, and environment norms.
Conclusion
Carbide flat plates offer unmatched wear life benefitting numerous industries, making them a strategically important engineering material. This guide covers the fundamentals of composition, properties, applications for our readers to make optimal data-driven choices. Reach out with additional questions!