Introduction
Definition of Carbide Flat Blanks
Carbide flat blanks are solid pieces of carbide material that have a flat and rectangular shape. They are commonly used in various industries, including manufacturing, machining, and tooling. These flat blanks are known for their high hardness, wear resistance, and excellent thermal conductivity. They are often used as a starting point for creating cutting tools, such as drills, end mills, and inserts. Carbide flat blanks provide the necessary foundation for precision machining and are essential in achieving accurate and efficient results. With their exceptional durability and performance, carbide flat blanks are a crucial component in many industrial applications.
Applications of Carbide Flat Blanks
Carbide flat blanks have a wide range of applications in various industries. One of the main applications of carbide flat blanks is in the manufacturing of cutting tools. These blanks are used as the base material for producing high-performance cutting tools such as drills, end mills, and inserts. The exceptional hardness and wear resistance of carbide make it an ideal choice for applications that require precision machining and long tool life. Additionally, carbide flat blanks are also used in the production of wear parts for industries such as mining, construction, and oil and gas. The high strength and durability of carbide allow these parts to withstand harsh operating conditions and provide extended service life. Overall, the applications of carbide flat blanks are crucial in enhancing productivity and efficiency in various industrial sectors.
Importance of Carbide Flat Blanks
Carbide flat blanks play a crucial role in various industries due to their exceptional hardness, durability, and resistance to wear. These specialized materials are commonly used in the manufacturing of cutting tools, such as drills, end mills, and inserts. The importance of carbide flat blanks lies in their ability to withstand high temperatures and maintain their cutting edge, resulting in improved productivity and longer tool life. Additionally, carbide flat blanks offer superior performance in machining applications, providing precision and accuracy. With their remarkable properties, carbide flat blanks have become an indispensable component in the production of high-quality tools and parts across industries including automotive, aerospace, and medical. The use of carbide flat blanks not only enhances the efficiency of machining processes but also contributes to overall cost savings and improved product quality.
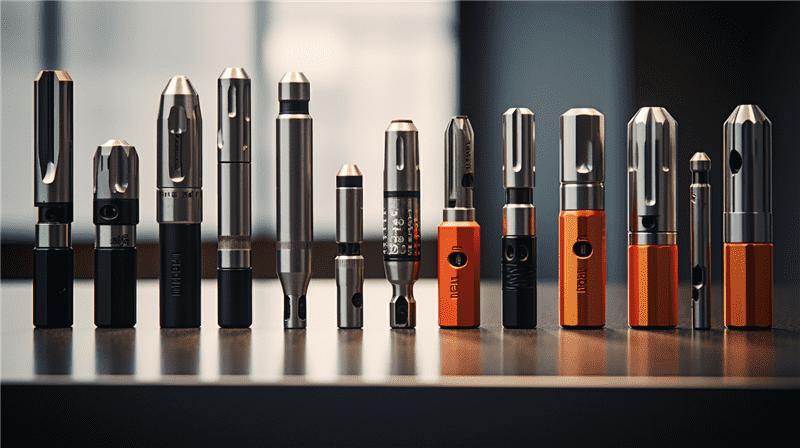
Properties of Carbide Flat Blanks
Hardness
Carbide flat blanks are known for their exceptional hardness. With a high level of carbon content, these flat blanks are able to withstand extreme pressure and wear, making them ideal for various industrial applications. The hardness of carbide flat blanks ensures their longevity and durability, allowing them to be used in demanding environments where other materials would fail. Whether it’s in the automotive, aerospace, or manufacturing industry, carbide flat blanks provide the necessary hardness to meet the rigorous demands of modern-day applications.
Wear Resistance
Carbide flat blanks are known for their exceptional wear resistance. This quality makes them highly suitable for applications that involve constant friction and abrasion. The unique composition of carbide materials, such as tungsten carbide, provides a high level of hardness and toughness, ensuring that the flat blanks can withstand even the most demanding conditions. Whether it is in the manufacturing industry, automotive sector, or any other field that requires durable components, carbide flat blanks are the go-to choice for achieving long-lasting wear resistance.
Heat Resistance
Carbide flat blanks exhibit exceptional heat resistance, making them ideal for a wide range of applications. These blanks are able to withstand high temperatures without losing their structural integrity or performance. The heat resistance of carbide flat blanks allows them to be used in demanding environments such as metalworking, aerospace, and automotive industries where extreme heat is present. With their ability to handle intense heat, carbide flat blanks provide reliable and long-lasting performance, ensuring efficient and effective operations in various industries.
Manufacturing Process
Powder Metallurgy
Powder metallurgy is a manufacturing process that involves the production of metal parts using powdered metal as the raw material. This technique offers several advantages over traditional metalworking methods, such as the ability to produce complex shapes, improved material properties, and cost-effectiveness. In the case of carbide flat blanks, powder metallurgy is a crucial step in their production. The powdered carbide material is carefully mixed, compacted, and then sintered to form solid carbide blanks with precise dimensions and high strength. This process ensures that the carbide flat blanks have excellent wear resistance, hardness, and toughness, making them ideal for various industrial applications. Powder metallurgy has revolutionized the manufacturing of carbide flat blanks, enabling the production of high-quality and high-performance components.
Compaction
Compaction is an essential process in the production of carbide flat blanks. It involves compressing a mixture of tungsten carbide powder and a binder material into a desired shape and size. This compaction process is typically performed using specialized machinery, such as hydraulic presses, which apply high pressure to the powder mixture. The goal of compaction is to achieve a dense and uniform structure, ensuring the mechanical properties and performance of the carbide flat blanks. Additionally, the compaction process also plays a crucial role in controlling the porosity and density of the final product, which directly affects its strength, hardness, and wear resistance. Overall, compaction is a critical step in the manufacturing of carbide flat blanks, ensuring their quality and reliability.
Sintering
Sintering is a crucial process in the production of carbide flat blanks. It involves heating the raw materials, typically tungsten carbide and cobalt, to a high temperature in a controlled atmosphere. The purpose of sintering is to bond the particles together, creating a solid and durable material. During the sintering process, the particles undergo diffusion, allowing for the formation of a dense structure with excellent mechanical properties. The temperature and duration of the sintering process are carefully controlled to achieve the desired material characteristics. Sintering plays a vital role in determining the final quality and performance of carbide flat blanks.
Types of Carbide Flat Blanks
Solid Carbide Flat Blanks
Solid Carbide Flat Blanks are high-quality, durable materials used in various industries. These flat blanks are made from carbide, a strong and tough material that provides excellent performance and longevity. The carbide flat blanks are carefully engineered to have precise dimensions and a smooth surface finish, making them ideal for applications that require tight tolerances and precision. Whether it’s for cutting tools, wear parts, or tooling components, solid carbide flat blanks are the go-to choice for professionals who demand superior quality and reliability. With their exceptional hardness and resistance to wear and corrosion, these flat blanks ensure optimal performance and extended tool life. Invest in solid carbide flat blanks and experience the difference they can make in your applications.
Tungsten Carbide Flat Blanks
Tungsten carbide flat blanks are a versatile and highly durable material used in a variety of industries. These flat blanks are made from a combination of tungsten and carbon, resulting in a material that is incredibly hard and resistant to wear and tear. They are commonly used in the manufacturing of cutting tools, such as drills, end mills, and inserts, as well as in the production of wear parts for machinery and equipment. The exceptional hardness and toughness of tungsten carbide flat blanks make them ideal for applications where high precision and long-lasting performance are required. With their superior strength and resistance to heat and corrosion, tungsten carbide flat blanks are the go-to choice for many industrial applications.
Cemented Carbide Flat Blanks
Cemented carbide flat blanks are essential components in various industrial applications. These high-performance materials are widely used in the manufacturing of cutting tools, wear-resistant parts, and precision instruments. The unique properties of cemented carbide, such as high hardness, excellent wear resistance, and superior toughness, make it an ideal choice for demanding applications. With their exceptional strength and durability, carbide flat blanks ensure long-lasting performance and reliable functionality. Whether it’s for machining, drilling, or milling operations, cemented carbide flat blanks provide the necessary stability and precision to achieve optimal results. Furthermore, their resistance to heat and corrosion makes them suitable for use in harsh environments. In summary, cemented carbide flat blanks play a crucial role in enhancing productivity and efficiency across a wide range of industries.
Advantages of Carbide Flat Blanks
High Strength
Carbide flat blanks are known for their exceptional strength and durability. When it comes to high strength applications, these flat blanks are the perfect choice. They are specifically designed to withstand heavy loads and extreme conditions, making them ideal for use in industries such as automotive, aerospace, and manufacturing. The high strength of carbide flat blanks ensures that they can handle the toughest tasks with ease, providing reliable performance and long-lasting durability. Whether it’s for cutting, drilling, or shaping, these flat blanks deliver superior strength and precision, making them a top choice for professionals and enthusiasts alike.
Long Tool Life
Carbide flat blanks offer exceptional tool life, especially when it comes to long tool life. The hardness and durability of carbide make it resistant to wear and tear, allowing it to maintain its cutting edge for extended periods of time. This means that users can rely on carbide flat blanks to deliver consistent performance and precision, even in demanding applications. Whether it’s milling, drilling, or turning, carbide flat blanks provide the longevity needed for a wide range of machining operations. With their superior tool life, carbide flat blanks are a reliable choice for professionals looking to optimize productivity and minimize downtime.
Excellent Machinability
Carbide flat blanks offer excellent machinability, making them a preferred choice in various industrial applications. With their high hardness and wear resistance, these flat blanks can be easily machined into precise shapes and dimensions. This exceptional machinability ensures efficient and accurate manufacturing processes, resulting in high-quality end products. Whether it’s for cutting tools, wear parts, or precision components, carbide flat blanks deliver exceptional performance and reliability. Their machinability also allows for cost-effective production, as they can be efficiently shaped and finished to meet specific requirements. Overall, the excellent machinability of carbide flat blanks makes them an indispensable material for industries that demand precision and durability.
Applications of Carbide Flat Blanks
Cutting Tools
Carbide flat blanks are an essential component in the manufacturing of cutting tools. These blanks are made from high-quality carbide material, known for its exceptional hardness and wear resistance. The flat shape of the blanks allows for precise cutting and shaping, making them ideal for applications in industries such as automotive, aerospace, and metalworking. With their superior strength and durability, carbide flat blanks ensure the production of reliable and long-lasting cutting tools that can withstand the toughest materials and operating conditions. Whether it’s for milling, drilling, or turning, carbide flat blanks play a crucial role in enhancing the performance and efficiency of cutting tools.
Wear Parts
Carbide flat blanks are essential components used in the manufacturing of wear parts. These blanks are made from carbide, a durable and high-performance material known for its resistance to wear and corrosion. The use of carbide flat blanks in wear parts ensures longevity and reliability, making them ideal for applications that require heavy-duty performance. With their exceptional hardness and strength, carbide flat blanks contribute to the overall performance and efficiency of wear parts, providing durability and precision in demanding environments. Whether it’s for mining, construction, or industrial applications, carbide flat blanks play a crucial role in enhancing the performance and lifespan of wear parts.
Milling Inserts
Milling Inserts are essential tools used in the machining industry to shape and cut various materials. These inserts are typically made from carbide flat blanks, which are known for their exceptional hardness and wear resistance. Carbide flat blanks provide the necessary strength and durability required for high-speed milling operations. With their precise cutting edges and excellent heat resistance, milling inserts made from carbide flat blanks ensure efficient and accurate machining processes. Whether it’s for roughing, finishing, or precision milling, carbide flat blanks are the preferred choice for achieving superior results. Their ability to withstand heavy loads and maintain sharpness for extended periods makes them indispensable in the manufacturing and metalworking sectors. When it comes to achieving precision and productivity in milling applications, carbide flat blanks for milling inserts are the go-to solution.