Carbide end mills. These small but mighty tools are the unsung heroes of modern manufacturing, quietly shaping the world around us with incredible precision and power. But what exactly are carbide end mills, and what makes them so special?
In short, carbide end mills are cutting tools used in milling machines to remove material and create precise shapes and features. What sets them apart is their cutting edge: it’s made of tungsten carbide, an incredibly hard and wear-resistant material. This means carbide end mills can handle tougher materials, operate at higher speeds, and last significantly longer than their counterparts made from high-speed steel (HSS).
But their versatility doesn’t stop there. Carbide end mills come in a dizzying array of shapes, sizes, and configurations, each designed for specific tasks. This makes them indispensable across a wide range of industries and applications. Let’s dive into 10 of the most essential:
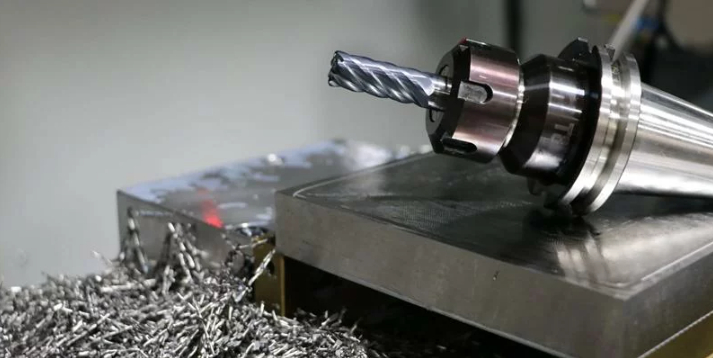
1. Aerospace: Taking Flight with Precision
The aerospace industry demands the highest levels of precision and reliability, and that’s where carbide end mills truly shine. They are essential for:
- Machining engine components: Creating intricate turbine blades, engine casings, and other critical parts from high-temperature alloys.
- Manufacturing structural components: Shaping and finishing lightweight yet strong components like airframes, wings, and fuselage sections.
- Producing interior components: Creating precise cutouts and features in aircraft interiors for seating, galleys, and other fixtures.
2. Automotive: Driving Innovation in Manufacturing
From engine blocks to intricate dashboard components, carbide end mills play a crucial role in shaping the automotive industry:
- Engine manufacturing: Creating precise features in cylinder heads, engine blocks, and transmission housings.
- Body and chassis components: Machining complex shapes and contours in body panels, door frames, and chassis parts.
- Mold and die making: Producing the high-precision molds used to form plastic and metal components for vehicle interiors and exteriors.
3. Medical: Engineering Life-Saving Devices
The medical industry relies on carbide end mills for their ability to machine intricate, often miniature, components with exceptional accuracy:
- Surgical instruments: Creating delicate instruments for minimally invasive surgery, such as forceps, scalpels, and drills.
- Implants and prosthetics: Machining custom-fit implants, such as hip replacements, knee joints, and dental implants.
- Medical devices: Producing components for a wide range of medical devices, including pacemakers, defibrillators, and imaging equipment.
4. Mold Making: Shaping the Future of Manufacturing
Carbide end mills are the go-to tools for creating the highly accurate molds used to mass-produce a wide range of products:
- Plastic injection molds: Creating the intricate cavities and features in molds used to produce plastic parts for consumer goods, electronics, and more.
- Die casting molds: Machining the high-temperature molds used to create metal parts with complex shapes and thin walls.
- Blow molding molds: Producing the molds used to form hollow plastic items like bottles, containers, and automotive parts.
5. Energy: Powering the World with Precision
The energy sector relies on carbide end mills for their ability to handle the tough materials and demanding conditions found in power generation and extraction:
- Oil and gas exploration: Machining components for drilling equipment, downhole tools, and pipelines.
- Power generation: Creating turbine blades, valve components, and other critical parts for power plants.
- Renewable energy: Manufacturing components for wind turbines, solar panels, and other renewable energy systems.
6. Tool and Die: The Backbone of Manufacturing
Carbide end mills are essential for creating the very tools and dies that shape countless other industries:
- Cutting tools: Manufacturing punches, dies, and other cutting tools used in stamping, forming, and shearing operations.
- Forming tools: Creating the molds and dies used to shape metal and plastic parts through bending, pressing, and drawing processes.
- Fixtures and jigs: Machining precise components for workholding fixtures and assembly jigs used in manufacturing processes.
7. Electronics: Enabling the Digital Age
From smartphones to circuit boards, carbide end mills play a vital role in the electronics industry:
- Semiconductor manufacturing: Creating the highly precise features on silicon wafers used to produce microchips and other electronic components.
- Printed circuit board (PCB) production: Drilling holes, routing traces, and creating other features on PCBs.
- Electronic component manufacturing: Machining connectors, housings, and other components for electronic devices.
8. General Machining: Versatility for Diverse Needs
Beyond specialized industries, carbide end mills are workhorses in general machining applications across various sectors:
- Prototyping: Creating prototypes and one-off parts for product development and testing.
- Repair and maintenance: Machining replacement parts, repairing damaged components, and performing general maintenance tasks.
- Custom fabrication: Creating custom parts and components for a wide range of applications.
9. Robotics: Building the Future of Automation
As robotics and automation continue to advance, carbide end mills are essential for creating the precise components that bring these systems to life:
- Robot arms and end effectors: Machining lightweight yet strong components for robotic arms, grippers, and other end-of-arm tooling.
- Actuators and sensors: Producing precise housings and mounting features for actuators, sensors, and other robotic components.
- Automation equipment: Manufacturing components for automated machinery used in various industries, including manufacturing, logistics, and healthcare.
10. Education and Research: Shaping the Future of Innovation
Carbide end mills are invaluable tools in educational institutions and research facilities:
- Technical training: Providing students with hands-on experience in machining, manufacturing processes, and material science.
- Research and development: Enabling researchers to create custom experimental setups, test fixtures, and prototype components.
- Materials science: Studying the properties and behavior of materials under various machining conditions.
Choosing the Right Tool for the Job
With so many types of carbide end mills available, selecting the right one can feel overwhelming. Here’s a simplified guide:
Feature | Consideration |
---|---|
Number of Flutes | Fewer flutes for roughing (faster material removal), more flutes for finishing (smoother surface) |
Flute Geometry | Straight flutes for slotting, helical flutes for general purpose, variable helix for reduced vibration |
End Mill Diameter | Match to the desired slot width or hole size |
Coating | TiN for general purpose, TiCN for increased hardness, AlTiN for high-temperature applications |
No matter the industry or application, carbide end mills have earned their place as essential tools for precision machining. Their ability to handle tough materials, deliver exceptional accuracy, and provide extended tool life makes them indispensable for shaping the world around us.
Want to know more? Please click.