Introduction
What are carbide disc blanks?
Carbide disc blanks are a type of cutting tool that are widely used in various industries. These blanks are made from a durable and hard material called carbide, which allows them to withstand high temperatures and resist wear and tear. They are commonly used in applications that require precision cutting, such as in the manufacturing of metal products, automotive parts, and woodworking. The use of carbide disc blanks ensures clean and accurate cuts, resulting in improved productivity and quality of the final product. With their exceptional durability and performance, carbide disc blanks have become an indispensable tool in many industries.
Applications of carbide disc blanks
Carbide disc blanks have a wide range of applications in various industries. One of the key applications of carbide disc blanks is in the manufacturing of cutting tools. Due to their exceptional hardness and wear resistance, carbide disc blanks are ideal for producing high-performance cutting tools that can withstand the demands of heavy-duty machining operations. Additionally, carbide disc blanks are also used in the production of wear parts for industrial machinery, such as bearings, bushings, and seals. The superior strength and durability of carbide disc blanks make them highly suitable for these applications, ensuring reliable and long-lasting performance. Furthermore, carbide disc blanks find applications in the automotive industry, where they are utilized in the production of brake discs and clutch plates. The excellent heat resistance and frictional properties of carbide disc blanks make them an excellent choice for these critical components. Overall, the versatile applications of carbide disc blanks make them a valuable material in various industries, contributing to enhanced productivity and performance.
Benefits of using carbide disc blanks
Carbide disc blanks offer numerous benefits when it comes to various applications. One of the key advantages is their exceptional hardness and durability, which allows them to withstand high temperatures and heavy loads. This makes them ideal for use in industries such as automotive, aerospace, and manufacturing, where precision and reliability are crucial. Additionally, carbide disc blanks provide superior cutting performance, ensuring smooth and precise cuts with minimal friction. Furthermore, they have excellent wear resistance, reducing the need for frequent replacements and resulting in cost savings in the long run. Overall, the use of carbide disc blanks greatly enhances productivity and efficiency in cutting and machining processes, making them a preferred choice for professionals in various industries.
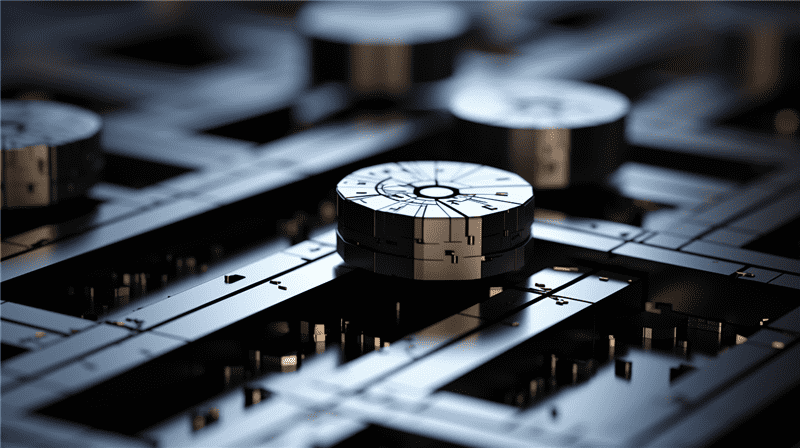
Types of Carbide Disc Blanks
Solid carbide disc blanks
Solid carbide disc blanks are high-quality cutting tools used in various industries. These disc blanks are made from carbide, a durable and wear-resistant material that ensures long-lasting performance. With their precise dimensions and excellent hardness, solid carbide disc blanks are ideal for applications that require high precision and accuracy. Whether it’s for metalworking, woodworking, or other machining processes, these disc blanks provide exceptional cutting performance and help improve productivity. Additionally, their resistance to heat and corrosion makes them suitable for use in demanding environments. Overall, solid carbide disc blanks are essential tools for professionals who seek reliable and efficient cutting solutions.
Tungsten carbide disc blanks
Tungsten carbide disc blanks are essential components used in various industries, such as manufacturing, construction, and engineering. These discs are made from high-quality tungsten carbide, a strong and durable material known for its exceptional hardness and resistance to wear and corrosion. With their precise dimensions and excellent cutting performance, tungsten carbide disc blanks are widely used in cutting tools, grinding machines, and other applications that require precision and reliability. Whether it’s for cutting, shaping, or grinding, these disc blanks provide the necessary strength and durability to ensure efficient and accurate operations. Furthermore, their long lifespan and low maintenance requirements make them a cost-effective choice for businesses looking to enhance productivity and reduce downtime. Overall, tungsten carbide disc blanks play a crucial role in various industries, enabling efficient and precise machining processes.
Ceramic carbide disc blanks
Ceramic carbide disc blanks are a type of cutting tool used in various industrial applications. These disc blanks are made from a combination of ceramic and carbide materials, which provides them with exceptional hardness and durability. They are commonly used in the manufacturing and machining industries for cutting, shaping, and grinding a wide range of materials, including metal, wood, and plastic. The ceramic carbide disc blanks offer superior performance, precision, and longevity, making them an essential tool for professionals in the metalworking and fabrication fields. With their high heat resistance and ability to maintain sharpness even under heavy use, ceramic carbide disc blanks are the go-to choice for demanding cutting tasks. Whether it’s for precision cutting or heavy-duty grinding, these disc blanks deliver consistent and reliable results, ensuring efficient and accurate operations in various industrial settings.
Properties of Carbide Disc Blanks
Hardness
Carbide disc blanks are known for their exceptional hardness. This hardness is a result of their composition, which includes tungsten carbide, a material renowned for its high hardness and wear resistance. The hardness of carbide disc blanks makes them ideal for applications that require cutting, grinding, or machining of tough materials. With their superior hardness, carbide disc blanks can withstand high temperatures and heavy loads, ensuring long-lasting performance and durability. Whether used in manufacturing or in various industrial applications, carbide disc blanks provide the hardness needed to tackle even the most demanding tasks.
Wear resistance
Carbide disc blanks are known for their exceptional wear resistance. They are specifically designed to withstand high levels of friction, heat, and abrasion, making them ideal for applications where durability is crucial. The unique composition of carbide materials, such as tungsten carbide, ensures that these disc blanks can maintain their shape and performance even under heavy usage. Whether used in cutting tools, grinding wheels, or other industrial applications, carbide disc blanks offer unmatched wear resistance, providing long-lasting and reliable performance.
Heat resistance
Carbide disc blanks are known for their exceptional heat resistance. This makes them ideal for applications where high temperatures are involved, such as cutting and shaping metal. The heat resistance of carbide disc blanks allows them to maintain their hardness and durability even under extreme heat conditions. This ensures that they can withstand the demands of heavy-duty machining operations without compromising their performance. Moreover, the heat resistance of carbide disc blanks also contributes to their long lifespan, making them a cost-effective choice for industries that require reliable and long-lasting cutting tools.
Manufacturing Process
Powder metallurgy
Powder metallurgy is a manufacturing process that involves the production of metal parts by compacting and sintering metal powders. It offers several advantages, such as the ability to create complex shapes, improved material properties, and cost-effectiveness. Carbide disc blanks are an important component in the powder metallurgy process. These blanks are made from tungsten carbide, a hard and durable material that is ideal for cutting and grinding applications. The use of carbide disc blanks in powder metallurgy allows for precise and efficient shaping of metal powders, resulting in high-quality finished products. With the advancements in powder metallurgy technology, carbide disc blanks continue to play a crucial role in the manufacturing industry.
Sintering
Sintering is a crucial process in the production of carbide disc blanks. It involves heating the compacted powder mixture of tungsten carbide and cobalt to a high temperature in a controlled atmosphere. During sintering, the powder particles bond together, resulting in a dense and solid carbide material. This process not only enhances the mechanical properties of the carbide disc blanks but also improves their wear resistance and overall performance. Sintering plays a vital role in achieving the desired hardness and toughness of the carbide discs, making them suitable for various industrial applications such as cutting, grinding, and drilling.
Finishing operations
Finishing operations are an essential part of the manufacturing process for carbide disc blanks. Once the blanks have been shaped and hardened, they undergo a series of finishing operations to achieve the desired surface quality and dimensional accuracy. These operations include grinding, polishing, and coating. Grinding is performed to remove any excess material and to ensure a smooth and uniform surface. Polishing further enhances the surface finish, making it more resistant to wear and corrosion. Finally, a protective coating is applied to improve the disc blanks’ durability and performance. These finishing operations play a crucial role in ensuring that the carbide disc blanks meet the highest quality standards and perform optimally in various applications.
Applications of Carbide Disc Blanks
Cutting tools
Carbide disc blanks are an essential component in the manufacturing of cutting tools. These blanks are made from high-quality carbide material, known for its exceptional hardness and durability. The use of carbide disc blanks ensures that cutting tools can withstand the rigors of demanding applications, such as metalworking and woodworking. With their superior strength and resistance to wear, carbide disc blanks allow cutting tools to maintain sharpness and precision for extended periods, resulting in efficient and accurate cutting. Whether it’s for industrial or DIY purposes, the incorporation of carbide disc blanks in cutting tools is crucial for achieving optimal performance and achieving quality results.
Rotary cutting discs
Rotary cutting discs, also known as carbide disc blanks, are essential tools used in various industries for cutting and shaping different materials. These discs are made from carbide, a durable and high-performance material that ensures precision and efficiency in cutting operations. Whether it’s cutting through metal, wood, or plastic, rotary cutting discs provide clean and accurate cuts, making them a popular choice among professionals and DIY enthusiasts alike. With their versatility and durability, carbide disc blanks have become a go-to tool for tasks that require precision and reliability.
Grinding wheels
Grinding wheels are essential tools used in various industries for shaping and finishing materials. One popular type of grinding wheel is the carbide disc blank. These disc blanks are made from high-quality carbide material, which provides exceptional durability and cutting performance. Carbide disc blanks are commonly used for precision grinding applications, such as sharpening tools, shaping metal parts, and removing excess material. With their superior hardness and resistance to wear, carbide disc blanks ensure precise and efficient grinding operations. Whether in manufacturing or maintenance, the use of carbide disc blanks in grinding wheels is crucial for achieving excellent results.
Maintenance and Care
Proper storage
Proper storage of carbide disc blanks is crucial to maintain their quality and performance. These disc blanks are made of high-quality carbide material, which is known for its hardness and durability. To ensure their longevity, it is important to store them in a dry and clean environment. Moisture and dirt can degrade the carbide material and affect the cutting performance of the disc blanks. Additionally, it is recommended to store them in a protective case or container to prevent any physical damage. By following these storage guidelines, you can maximize the lifespan of your carbide disc blanks and ensure optimal performance when using them for various cutting applications.
Cleaning and maintenance
Cleaning and maintenance of carbide disc blanks is essential to ensure their longevity and optimal performance. Regular cleaning helps remove dirt, debris, and residue that can accumulate on the discs during use. It is recommended to use a soft cloth or brush to gently wipe the surface of the disc, avoiding harsh chemicals or abrasive materials that may cause damage. Additionally, periodic maintenance such as lubrication and inspection for any signs of wear or damage is crucial to prevent potential issues and extend the lifespan of the carbide disc blanks. By following proper cleaning and maintenance practices, users can maximize the efficiency and durability of their carbide disc blanks, ensuring reliable performance for various applications.
Sharpening and reconditioning
When it comes to sharpening and reconditioning carbide disc blanks, it is essential to follow proper techniques and guidelines. Carbide disc blanks are known for their durability and long lifespan, but over time, they may become dull or damaged. To restore their cutting performance, a sharpening process is required. This process involves removing the old edge and regrinding the disc blank to create a new, sharp cutting edge. It is important to use the correct grinding wheel and apply the appropriate amount of pressure to achieve the desired results. Additionally, reconditioning carbide disc blanks may involve cleaning, inspecting for any defects, and applying a protective coating to prevent corrosion. By properly sharpening and reconditioning carbide disc blanks, you can prolong their lifespan and ensure optimal cutting performance.