Overview
Carbide die blanks are precision pre-machined blocks used as starting workpieces for manufacturing dies, molds, and tooling inserts. The extremely high hardness, compressive strength, and wear resistance of carbides make them ideal materials for producing long-lasting tooling components.
Carbide blanks enable machining complex die cavity geometries to tight dimensional tolerances using electrical discharge machining (EDM), milling, grinding, and other techniques. This guide covers the properties, manufacturing, grades, applications, and global suppliers of carbide die blanks. It includes helpful comparison tables summarizing technical specifications for various blank configurations.
Selecting the optimal carbide die blank requires matching the carbide type, binder, size, shape, tolerance, and finish requirements to the tooling application and machining capabilities. This guide provides product engineers, tool designers, mold makers, and procurement managers an in-depth understanding of carbide blank options to facilitate optimal material selection.
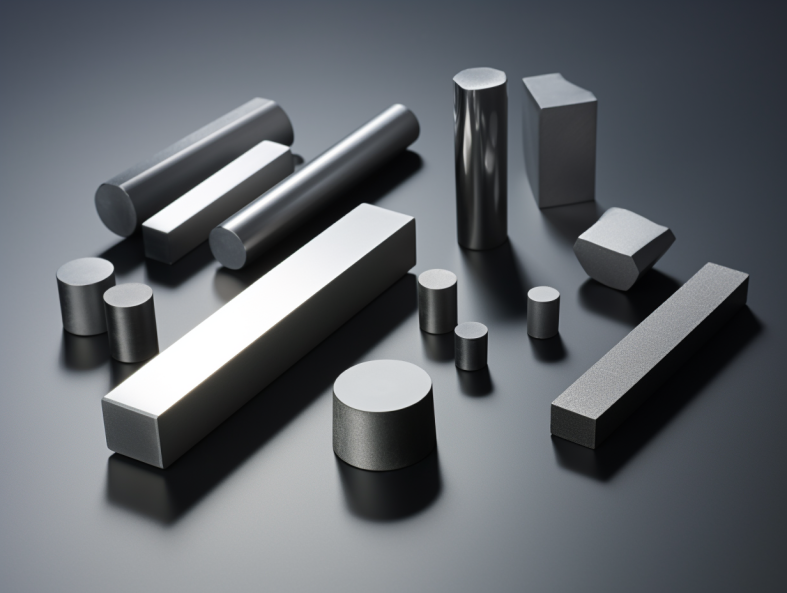
Types of Carbide Die Blanks
There are two primary categories of carbide used in die blank materials:
Carbide Types Used in Die Blanks
Carbide | Description | Key Properties |
---|---|---|
Tungsten carbide | WC formed with cobalt binder | Highest hardness and wear resistance |
Titanium carbide | TiC as primary carbide component | Excellent corrosion resistance |
Tungsten carbide is most prevalent, providing extreme hardness levels along with good fracture toughness. Cobalt content varies from 3-25% to balance hardness against impact strength.
Titanium carbide offers the highest heat resistance and chemical inertness. It is blended with other carbides in engineered compositions optimized for specific applications.
Grain size and carbon control during carbide powder sintering further tune hardness, strength and toughness. Smaller carbides resist fracture better under stress.
Manufacturing Process for Carbide Blanks
Carbide die blanks start as powder metallurgy compositions containing microscopic carbide grains consolidated under heat and pressure into a solid carbide mass.
Key Production Steps:
- Carbide powder milling – Forms carbide particles with uniform size distribution
- Powder mixing – Carbide powder combined with metal binder elements
- Compaction – Powder consolidated into a solid green body by pressing
- Sintering – Binder liquefaction bonds carbide particles into a dense structure
- Hot isostatic pressing – Further densifies the microstructure
- Annealing – Heat treatment to optimize mechanical properties
- Rough machining – Blanks saw cut and ground to shape from sintered blocks
- Finish machining – Required blank dimensions and tolerances achieved
Blank quality hinges on precise control of powder characteristics, composition, and achieving full sintered density free of voids.
Grades of Carbide Die Blanks
There are many standard blank compositions formulated by powder metallurgy to offer a balance of hardness, fracture resistance, and manufacturability.
Common Grades of Carbide Blanks
Grade | Description | Hardness Range | Key Properties |
---|---|---|---|
C2/C3 | Straight tungsten carbide + cobalt | 89.5-91.5 HRA | Universal, low-cost grade |
C5 | Enhanced toughness and EDM speed | 88.5-90.5 HRA | Good wear resistance |
C6-C8 | Improved resistance to brittle fracture | 90-92 HRA | High impact strength |
C10-C20 | High hardness compositions | 92-94.5 HRA | Maximum wear performance |
TiC0.3 | Titanium carbide-nickel cermet | 85-88 HRA | Corrosion resistance, stability |
Higher cobalt content improves fracture resistance but reduces hardness in tungsten carbide grades. Nanograin compositions provide both hardness and toughness.
TiC0.3 contains an engineered nickel alloy matrix supporting titanium carbide for optimal chemical inertness.
Uses of Carbide Die Blanks
The combination of extreme hardness, compressive strength, and dimensional stability makes carbide blanks ideally suited for manufacturing:
- Plastic injection molds
- Metal die casting dies
- Extrusion and drawing dies
- Blow molds
- Compression and stamping dies
- Trimming/punching dies
Carbide withstands aggressive stamping and drawing processes when shaping tough alloys like stainless steel or titanium without excessive wear. The corrosion resistance provided by titanium carbide blanks resists acidic materials and environments.
Precision EDM machining of carbide enables fine details, smooth surface finishes, and complex internal coolant circuits within the die cavity not possible with other tooling materials.
Carbide Die Blank Specifications
International standards from ASTM and ISO help define:
- Allowable compositions
- Mechanical property ranges
- Acceptable microstructure
- Permissible flaws
- Sampling methods
- Test procedures
for tungsten carbide and titanium carbide die blank materials to ensure reliability and performance consistency.
Carbide Die Blank Specifications
Standard | Scope | Hardness Range | Density | Microstructure | Defect Limits |
---|---|---|---|---|---|
ISO 513 | WC-Co grades | 89-95 HRA | >14.5 g/cc | Coating uniformity | Porosity, carbide agglomerations |
ASTM B776 | TiC-based cermet grades | 85-92 HRA | 4.9-5.2 g/cc | TiC distribution | Cracks, pits, voids |
JIS R1601 | Testing methods | — | — | — | Flaw characterization |
ASTM B312 | Standard EDM test block | 90 HRA | — | Fine grained WC-Co | Machinability indicator |
These specifications promote quality, consistency, and reliability when designing tooling with carbide die blanks across their demanding production lifetimes.
Carbide Die Blank Manufacturers
Carbide die blanks are supplied globally by many major manufacturers as well as smaller regional producers near customer hubs.
Leading Carbide Die Blank Suppliers
Supplier | Capabilities | Materials | Pricing |
---|---|---|---|
Kennametal | Widest grade selection, custom sizes | WC-Co, TiC, cermets | $$$/lb |
Sandvik | High accuracy, maximum dimensions | WC-Co, TiCN | $$$/lb |
Carborundum Universal | Grades for high temperature stability | WC-Co, HfC, cermets | $$/lb |
Erasteel | Specialists in large and multi-ton blocks | WC-Co | $$/lb |
Hyperion Materials | Custom blank engineering | WC-Co, TiCN, Cr3C2-NiCr | $$$/lb |
Cost varies from around $20/lb for standard C2/C3 tungsten carbide up to $100/lb or more for special geometries, grades, and finishing operations.
Larger sizes, higher material performance, and precision machining increase pricing. Smaller regional suppliers can offer competitive pricing.
Selecting the Best Carbide Die Blank
Choosing the optimal carbide blank requires matching:
- Hardness level to required die life and abrasion resistance
- Grade uniformity for consistent machinability and performance
- Toughness to withstand stamping loads without chipping
- Corrosion resistance if needed for chemistry compatibility
- Accuracy and surface finish to ease EDM machining
- Maximum die size capability for complexity and number of cavities
- Service and technical assistance from the supplier
Get input from machining subcontractors on specific grade recommendations and seek technical advice from vendors early when designing a major tooling program. Prototype smaller areas first before committing to large tools.
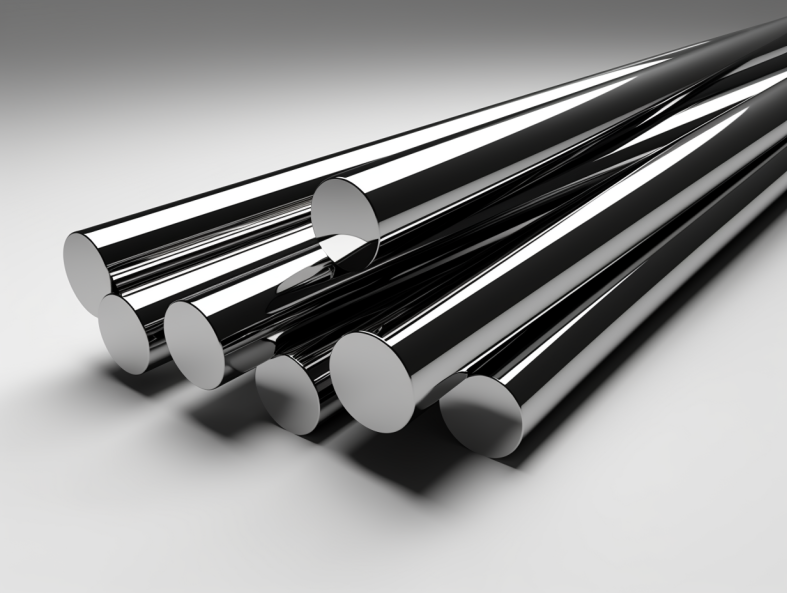
FAQ
What tolerances are typical for carbide die blanks?
Standard machined blanks range from +/- 0.005″ on basic rounds up to +/- 0.0005″ for precision squares and special geometries. Finer EDM machining can achieve +/- 0.0001″ or better as needed.
Which provides better wear resistance: fine or coarse grain carbide?
Finer carbide grain size improves fracture toughness and resistance to both abrasive and adhesive wear mechanisms. However, coarse grain is more resistant to plastic deformation and can be advantageous for high Cr grades.
When would TiCN be used over tungsten carbide?
The corrosion resistance and stable structure of titanium carbonitride are advantageous for super-finishing dies, hydroforming, and chemically aggressive processes like glass molding or resin transfer molding.
What causes sinks and distortions when EDM machining carbide?
Uneven heating of the electrically conductive cobalt binder can create localized thermal expansion effects. Slower cutting and more frequent flushing mitigates distortion when burning fine details.
How large can carbide die blanks be produced?
Standard blank dimensions range up to 30″ diameter and 24″ thick. Larger rectangular formats are possible through specialty suppliers. EDM sectioning can join smaller blanks into large inserts.
What post-sintering treatments improve carbide die blanks?
Hot isostatic pressing (HIP) increases density and removes internal voids. Annealing relieves residual stresses from grinding. Complete sequences enhance structural uniformity and performance consistency.
Conclusion
Carbide die blanks deliver the prerequisite hardness, wear performance, and dimensional precision required for manufacturing tooling that can withstand millions of demanding molding cycles. Matching the carbide’s composition, quality, accuracy, and size to the end application results in robust, long-lasting dies and reduced total lifecycle costs. Ongoing advances in nanostructured grades continue expanding the capabilities of carbide tooling materials.