Carbide coatings are a fascinating area of material science, with applications spanning from aerospace to automotive to manufacturing. These coatings, typically created using hard materials like tungsten carbide, offer unparalleled durability, hardness, and wear resistance. In this guide, we’ll take a deep dive into the world of carbide coatings, examining their composition, applications, production methods, and much more.
What are Carbide Coatings?
Carbide coatings are thin layers of extremely hard and durable materials, often composed of carbide-based compounds, applied to various substrates. These coatings enhance the mechanical properties of tools, components, and equipment, providing resistance to wear, corrosion, and high temperatures.
Think of carbide coatings as the armor your tools and components wear to battle harsh environments. They improve efficiency, extend lifespan, and often reduce operational costs.
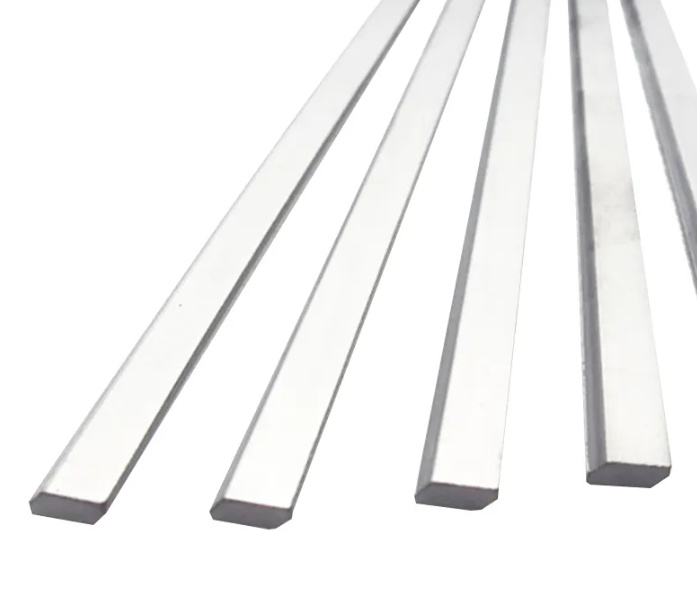
Types of Carbide Coatings
Different types of carbide coatings serve unique purposes depending on their composition and application. Here’s a table summarizing the main types of carbide coatings.
Type of Coating | Primary Composition | Key Characteristics |
---|---|---|
Tungsten Carbide (WC) | WC particles in cobalt | High hardness, excellent wear resistance, good toughness |
Chromium Carbide (CrC) | CrC in nickel or cobalt | Exceptional corrosion and oxidation resistance |
Titanium Carbide (TiC) | TiC matrix | High temperature performance, lightweight |
Silicon Carbide (SiC) | SiC ceramic | Outstanding thermal stability, extreme hardness |
Boron Carbide (B4C) | B4C compound | Lightweight, highly abrasion-resistant |
Vanadium Carbide (VC) | VC in steel substrates | Enhanced sliding wear resistance |
Hafnium Carbide (HfC) | HfC ceramics | Ultra-high-temperature resistance |
Molybdenum Carbide (Mo2C) | Mo2C matrix | Good thermal conductivity, oxidation resistance |
Niobium Carbide (NbC) | NbC alloys | Combines toughness and high-temperature stability |
Zirconium Carbide (ZrC) | ZrC ceramics | Exceptional hardness and chemical resistance |
Raw Materials and Composition Analysis of Carbide Coatings
Carbide coatings are primarily composed of metal carbide powders suspended in a binding matrix. The choice of raw materials depends on the required properties:
- Carbide Powders: These include tungsten carbide, chromium carbide, and silicon carbide. Each offers unique properties tailored for specific uses.
- Binders: Cobalt, nickel, and iron are common binders, which provide ductility and toughness to the coatings.
- Additives: Elements like boron, titanium, or vanadium can be introduced to enhance specific characteristics like hardness or corrosion resistance.
The quality of raw materials directly impacts the performance of the coating. For instance, high-purity powders lead to fewer defects and better wear resistance.
Applications of Carbide Coatings
Carbide coatings are used across numerous industries for their ability to withstand extreme conditions. Here’s a detailed table showcasing their applications:
Industry | Application | Benefits |
---|---|---|
Aerospace | Jet engine components, turbine blades | High-temperature resistance, wear resistance |
Automotive | Piston rings, fuel injectors, turbochargers | Reduced friction, extended component life |
Oil and Gas | Drill bits, pump components, pipeline protection | Corrosion resistance, durability under harsh conditions |
Manufacturing | Cutting tools, dies, molds | Enhanced tool life, precision machining |
Medical | Surgical instruments, implants | Biocompatibility, wear resistance |
Electronics | Semiconductor components, precision instruments | Heat dissipation, wear protection |
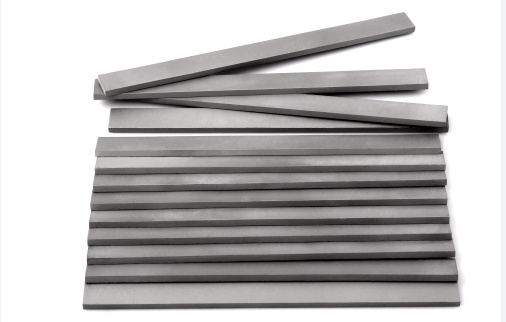
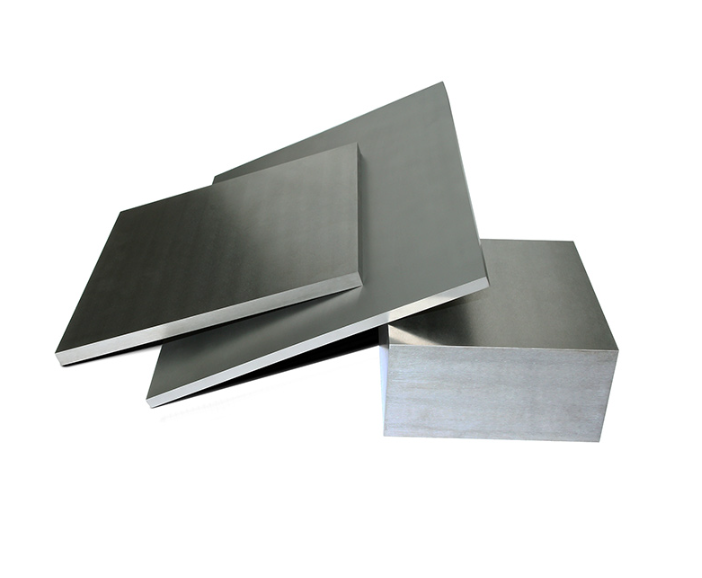
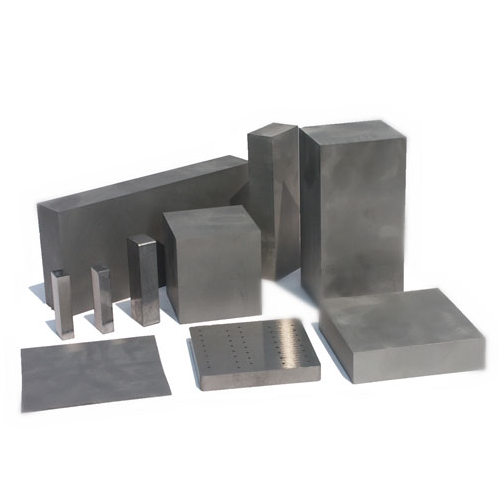
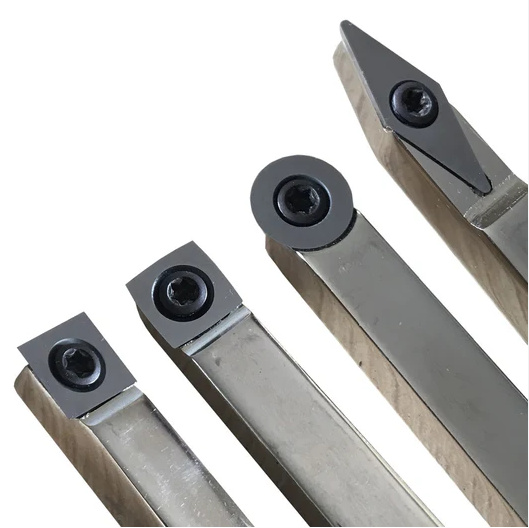
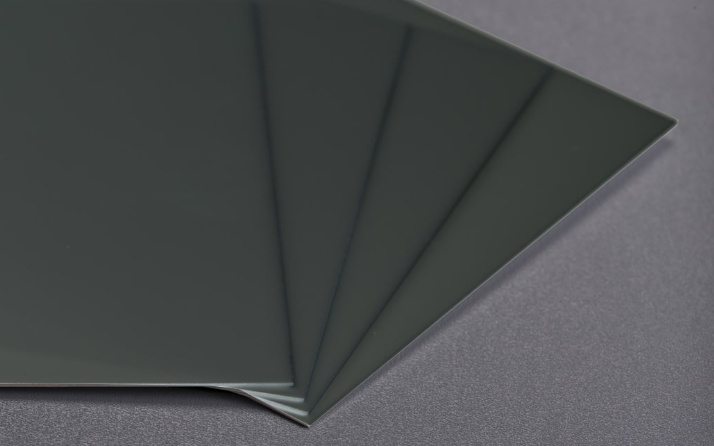
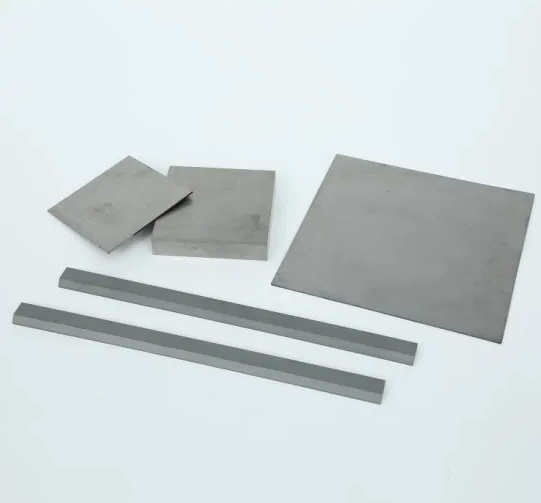
Production Process Flow of Carbide Coatings
The production of carbide coatings involves several key steps to ensure optimal performance. Here’s a simplified flow of the process:
- Powder Preparation: High-purity carbide powders are selected, mixed with binders, and milled for uniformity.
- Application Technique:
- Thermal Spray: Includes High-Velocity Oxygen Fuel (HVOF) or Plasma Spray methods.
- Chemical Vapor Deposition (CVD): Deposits a thin carbide layer in a vacuum chamber.
- Physical Vapor Deposition (PVD): Uses evaporation or sputtering to create the coating.
- Curing and Sintering: The coated material is heated to high temperatures to solidify and bond the layers.
- Finishing: Polishing or grinding ensures the desired surface finish and dimensions.
Material Properties of Carbide Coatings
The unique properties of carbide coatings make them indispensable. Here’s a table summarizing key material properties:
Property | Range |
---|---|
Hardness | 1500 – 3000 HV |
Density | 14.5 – 15.8 g/cm³ |
Wear Resistance | Excellent |
Corrosion Resistance | Varies (Good to Excellent) |
Thermal Conductivity | 60 – 100 W/mK |
Operating Temperature Range | -200°C to 1200°C |
Specifications, Sizes, Shapes, and Standards
Carbide coatings come in a variety of specifications to meet industry requirements. Here’s a summary table:
Parameter | Details |
---|---|
Coating Thickness | 10 – 500 µm |
Substrate Materials | Steel, aluminum, ceramics |
Standards Compliance | ASTM B653, ISO 9001, MIL-C-81769 |
Shapes Supported | Cylindrical, flat, complex geometries |
Choosing Carbide Coatings Suppliers and Pricing Details
Choosing the right supplier is critical to ensure consistent quality. Here are factors to consider:
Factor | Details |
---|---|
Supplier Reputation | Experience in the field, client reviews |
Certifications | ISO certifications, quality assurances |
Customization Options | Tailored compositions and thicknesses |
Pricing | $50 – $300 per square meter, depending on complexity |
Selecting the Right Carbide Coatings
Choosing the best carbide coating involves balancing several factors. Here’s a comparison table to help guide your decision:
Consideration | Options | Best For |
---|---|---|
Hardness vs. Toughness | WC vs. CrC | Wear resistance vs. corrosion |
Temperature Requirements | SiC vs. TiC | High-heat vs. moderate-heat |
Cost | Boron Carbide vs. Tungsten Carbide | Lightweight vs. durability |
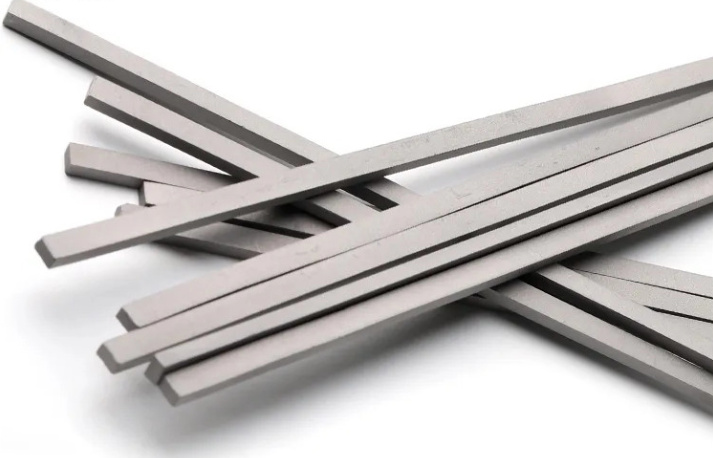
Advantages and Limitations of Carbide Coatings
Advantages | Limitations |
---|---|
Exceptional hardness and durability | High initial cost |
Resistance to wear, heat, and corrosion | Requires specialized equipment for application |
Prolongs the lifespan of components | Limited flexibility in certain geometries |
FAQs
Question | Answer |
---|---|
What are carbide coatings? | Hard layers applied to surfaces to enhance durability. |
How are carbide coatings applied? | Techniques like thermal spray, CVD, and PVD. |
What industries use carbide coatings? | Aerospace, automotive, manufacturing, and more. |
Can carbide coatings resist corrosion? | Yes, especially chromium and silicon carbide types. |
Are carbide coatings expensive? | Costs vary but offer long-term savings due to durability. |