Overview
Carbide circular saw tips have transformed the cutting industry, providing unparalleled precision and longevity. These small yet powerful components are essential for various cutting tools, enhancing their performance and extending their lifespan. From woodworking to metalworking, carbide circular saw tips are indispensable in ensuring clean, efficient cuts. This comprehensive guide explores the fascinating world of carbide circular saw tips, discussing their properties, working principles, usage, processing methods, classifications, and market trends. Whether you’re a seasoned professional or a curious newcomer, this article offers valuable insights into the superior capabilities of carbide circular saw tips.
Detailed Introduction
What Are Carbide Circular Saw Tips?
Carbide circular saw tips are cutting tool components made from a composite material, primarily tungsten carbide (WC) combined with a binder metal, typically cobalt (Co). These tips are affixed to circular saw blades, significantly improving their cutting efficiency and durability. Tungsten carbide provides exceptional hardness, while cobalt enhances toughness and resilience.
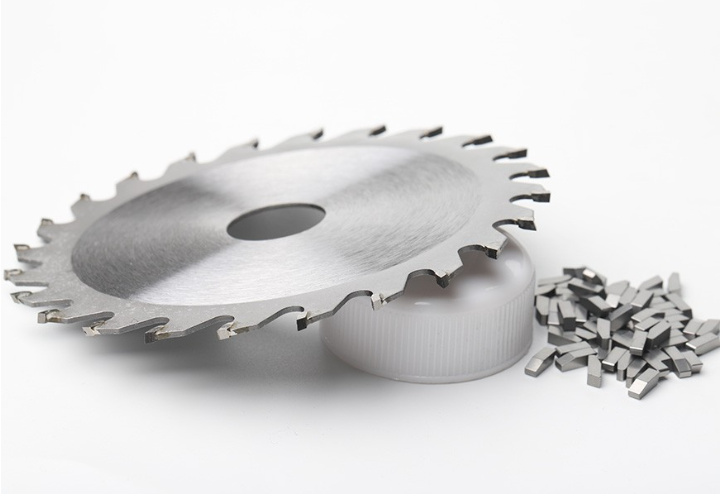
Working Principle
The effectiveness of carbide circular saw tips is attributed to their unique material properties:
- Hardness: Tungsten carbide is one of the hardest materials available, enabling superior cutting and machining capabilities.
- Wear Resistance: High wear resistance ensures these tips can withstand extreme conditions and maintain their performance over extended periods.
- Thermal Stability: These tips retain their hardness even at high temperatures, making them ideal for high-speed cutting and demanding applications.
- Corrosion Resistance: Their resistance to corrosion extends their lifespan, even in harsh environments.
How to Use Carbide Circular Saw Tips
Carbide circular saw tips are versatile and used in numerous applications, including:
- Wood Cutting: Essential in circular saw blades for precise and efficient wood cutting.
- Metal Cutting: Used in saws designed for cutting metals, providing clean and accurate cuts.
- Masonry Cutting: Integrated into tools for cutting bricks, tiles, and other masonry materials.
- Plastics Cutting: Utilized in tools for cutting various plastic materials with precision.
Processing Methods
The manufacturing of carbide circular saw tips involves several critical stages:
- Powder Mixing: Combining tungsten carbide powder with a binder metal, usually cobalt.
- Pressing: Shaping the mixture into tips using a pressing machine.
- Sintering: Heating the pressed tips to a high temperature to bond the particles together.
- Brazing: Attaching the carbide tips to the saw blade body through a brazing process.
- Grinding: Precision grinding to achieve the desired dimensions and surface finish.
- Coating: Applying advanced coatings to enhance performance and longevity.
Classification and Varieties
Carbide circular saw tips are classified based on their composition, grain size, and application. Common classifications include:
- Micro Grain: For applications requiring high precision and sharpness.
- Medium Grain: Balances toughness and wear resistance, suitable for general use.
- Coarse Grain: For applications demanding high toughness and impact resistance.
Market Dynamics
The market for carbide circular saw tips is robust and expanding, driven by increasing demand in manufacturing, construction, and woodworking industries. Key trends include:
- Technological Advancements: Innovations in coating technologies and material formulations.
- Sustainability: Growing emphasis on recycling and eco-friendly production processes.
- Globalization: Expansion of markets in emerging economies, leading to increased competition and innovation.
Product Information
The following table provides detailed information on carbide circular saw tips, including types, composition, properties, features, specifications, sizes, grades, and standards.
Carbide Circular Saw Tips Product Information Table
Type | Composition | Properties | Features | Specifications | Sizes | Grade | Standards |
---|---|---|---|---|---|---|---|
Micro Grain | WC + Co (5-8%) | High hardness | Excellent precision | 1-4 mm thickness | Customizable lengths | Ultra-fine | ISO 9001 |
Medium Grain | WC + Co (6-10%) | Balanced toughness | Versatile applications | 2-6 mm thickness | Customizable lengths | Standard | ISO 9001 |
Coarse Grain | WC + Co (10-15%) | High impact resistance | Toughness and durability | 3-8 mm thickness | Customizable lengths | Heavy-duty | ISO 9001 |
Nano-Coated | WC + Co + Nano coatings | Superior performance | Enhanced wear resistance | 1-5 mm thickness | Customizable lengths | Advanced | ISO 9001 |
Description of Table Content
This table highlights the different types of carbide circular saw tips and their respective characteristics. Each type is tailored for specific applications, offering unique benefits in terms of hardness, toughness, and wear resistance. The specifications and standards ensure that users can find the right tip for their precise needs.
Applications
Carbide circular saw tips are essential in a wide range of industries. Here are some of the primary applications:
- Woodworking: Used in circular saw blades for precise and efficient wood cutting.
- Metalworking: Employed in saws and cutting tools designed for various metals.
- Construction: Integrated into tools for cutting masonry materials like bricks and tiles.
- Plastics Manufacturing: Utilized in tools for cutting and shaping plastic materials.
- Furniture Manufacturing: Essential for precision cutting in the production of furniture.
- Automotive Industry: Used in cutting tools for manufacturing car parts.
- Aerospace Industry: Utilized in high-precision cutting tools for aerospace components.
- Recycling: Employed in cutting tools for recycling various materials.
Pros and Cons
Carbide Circular Saw Tips: Pros and Cons
The following table outlines the pros and cons of carbide circular saw tips, providing a balanced view of their benefits and limitations.
Pros | Cons |
---|---|
Exceptional hardness and wear resistance | Higher initial cost compared to some alternatives |
Long lifespan, reducing replacement frequency | Requires specialized equipment for processing |
High thermal stability | Can be brittle under certain conditions |
Versatile applications across industries | Limited to specific high-precision uses |
Eco-friendly with recycling options | Initial setup costs for advanced coatings |
Description of Table Content
This table outlines the advantages and disadvantages of carbide circular saw tips, providing a balanced view of their benefits and limitations. It helps users understand the trade-offs involved in choosing these tips for their applications.
Related Sections
Advanced Coating Technologies
The development of advanced coatings, such as diamond and nano-coatings, has significantly enhanced the performance of carbide circular saw tips. These coatings provide additional hardness and wear resistance, making the tips even more durable and efficient.
Sustainable Manufacturing Practices
With increasing awareness of environmental sustainability, the production of carbide circular saw tips is shifting towards eco-friendly practices. Recycling programs and greener manufacturing processes are being implemented to reduce the environmental impact.
Integration with Smart Technologies
The integration of smart technologies, such as IoT-enabled tools and AI-powered maintenance systems, is revolutionizing the use of carbide circular saw tips. These technologies enable real-time monitoring and predictive maintenance, optimizing performance and reducing downtime.
FAQ
Q1: What makes carbide circular saw tips superior to other materials for cutting tools?
A1: Carbide circular saw tips are superior due to their exceptional hardness, wear resistance, and thermal stability. These properties allow for precise and efficient cutting, reducing the frequency of tool replacements and maintenance.
Q2: How does the grain size of carbide circular saw tips affect their performance?
A2: The grain size affects the balance between hardness and toughness. Micro grain tips offer high precision and sharpness, medium grain tips provide a balance of toughness and wear resistance, and coarse grain tips are best for high-impact applications.
Q3: Are there eco-friendly options for carbide circular saw tips?
A3: Yes, many manufacturers are adopting sustainable practices and recycling programs to reduce the environmental impact of carbide circular saw tip production. Eco-friendly options are increasingly available.
Q4: What industries benefit the most from using carbide circular saw tips?
A4: Industries such as woodworking, metalworking, construction, plastics manufacturing, furniture manufacturing, automotive, aerospace, and recycling benefit the most from using carbide circular saw tips due to their durability and precision.
Q5: How do advanced coatings enhance the performance of carbide circular saw tips?
A5: Advanced coatings, such as diamond and nano-coatings, enhance the performance of carbide circular saw tips by providing additional hardness, wear resistance, and thermal stability. These coatings extend the lifespan of the tips and improve their efficiency in demanding applications.
Want to buy Carbide Tipped Saw Tips at a good price? Please click here.