Carbide button bits, also known as roller bits or button shank bits, are the workhorses of the drilling industry. Imagine yourself as a modern-day explorer, venturing deep into uncharted territories. Your trusty drill is your key to unlocking the secrets hidden beneath the earth’s surface. But what equips your drill to conquer tough rock formations? Enter carbide button bits – the drill’s unassuming hero, silently taking on the brunt of the drilling force.
A Look Inside Carbide Button Bits
Carbide button bits are a marvel of engineering, combining the strength of steel with the unparalleled wear resistance of tungsten carbide. Here’s a breakdown of their key components:
- Steel Body: The foundation of the bit is a high-strength steel body, designed to handle the immense torque and impact forces generated during drilling. Think of it as the sturdy frame of your explorer’s vehicle.
- Carbide Buttons: Embedded within the steel body are tungsten carbide buttons. These are the real MVPs, boasting exceptional hardness and abrasion resistance. Imagine them as the drill’s pickaxes, relentlessly chipping away at the rock.
- Shank: The shank is the business end of the bit that connects it to the drill hammer. It ensures a secure and powerful transfer of drilling force.
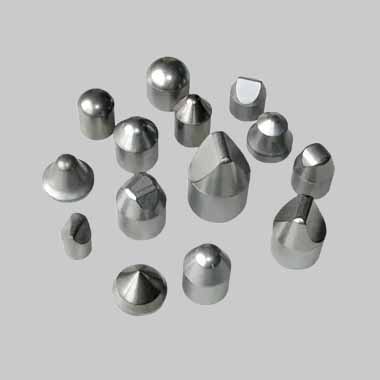
Metal Powder Makes the Difference
The specific type of tungsten carbide used in the buttons significantly impacts the bit’s performance. Here’s a closer look at ten prominent metal powder models, each with its own strengths:
- Cenos (WC-Co 6%): A versatile option offering a good balance between wear resistance and impact toughness. It’s suitable for medium-hard to hard rock formations.
- Deloro (WC-Co 8%): This metal powder excels in applications demanding high impact resistance. It tackles tough, abrasive formations with aplomb.
- Fanum (WC-Co 10%): Prioritizes extreme impact resistance, making it ideal for highly fractured and broken rock conditions.
- Gartac (WC-Co 12%): The undisputed champion of impact strength. It’s specifically designed for the most challenging drilling scenarios, like heavily fragmented rock.
- Kennametal (WC-Co 6-8%): Offers a well-rounded performance, suitable for a wide range of rock strengths.
- Sandvik (WC-Co 8-10%): Renowned for its excellent wear resistance and good balance with impact toughness. It’s a popular choice for medium-hard to hard rock drilling.
- Seco (WC-Co 6-10%): Provides a balance of wear resistance and impact strength, making it adaptable to various rock conditions.
- Sumitomo (WC-Co 6-8%): A versatile grade offering a good balance between wear and impact properties. It’s suitable for medium-hard to hard rock formations.
- TaeguTec (WC-Co 6-10%): This metal powder delivers a balance of wear resistance and impact toughness, making it a dependable choice for various drilling applications.
- Valenite (WC-Co 8-12%): Prioritizes high impact resistance, making it suitable for challenging rock formations with frequent fracturing.
Various Applications of Carbide Button Bits
Carbide button bits are the go-to solution for a wide range of drilling tasks. Here’s a glimpse into their versatility:
- Mining: From extracting precious metals and minerals to creating tunnels for underground operations, carbide button bits make their mark. They efficiently penetrate hard rock formations, enabling miners to access valuable resources.
- Quarrying: These bits are instrumental in quarrying operations, facilitating the extraction of construction materials like granite, limestone, and sandstone. Their ability to handle tough and abrasive rocks makes them an invaluable asset.
- Construction: Carbide button bits play a crucial role in various construction projects. They power through tough terrain for tasks like foundation drilling, road construction, and trenching.
- Water Well Drilling: Drilling boreholes for water wells requires reliable equipment. Carbide button bits excel in this domain, ensuring efficient penetration through diverse rock layers to reach water sources.
- Geotechnical Investigations: These bits are employed in geotechnical investigations, where engineers need to gather data on soil and rock composition. Their ability to drill through various formations facilitates the collection of vital information.
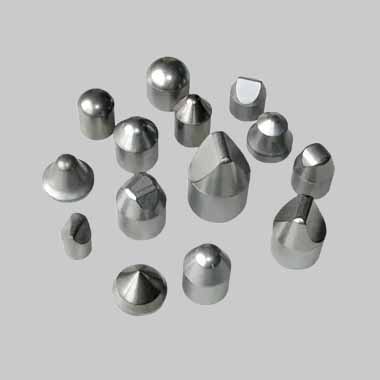
Multiple Advantages of Carbide Button Bits
Carbide button bits offer a compelling set of advantages over traditional drill bits:
- Superior Wear Resistance: Tungsten carbide’s exceptional hardness translates to unparalleled wear resistance. Compared to traditional steel bits, carbide button bits last significantly longer, reducing downtime and overall drilling costs. Imagine your explorer venturing deep into the earth – carbide button bits ensure they don’t need to constantly replace their pickaxes!
- Enhanced Penetration Rates: The hardness of carbide buttons allows for faster drilling speeds through tough rock formations. This translates to increased productivity and faster completion of drilling projects.
- Reduced Downtime: With their extended lifespan, carbide button bits require less frequent replacements. This reduces downtime associated with bit changes, keeping your drilling operations running smoothly.
- Versatility Across Applications: As explored earlier, the diverse range of metal powder models allows carbide button bits to tackle various drilling tasks effectively. One type of bit might be the ideal pickaxe for a granite mountain, while another conquers the challenges of fractured limestone.
- Cost-Effectiveness in the Long Run: While the initial cost of carbide button bits might be higher compared to traditional bits, their extended lifespan and reduced downtime translate to significant cost savings in the long run.
The Price Range of Carbide Button Bits
The price of carbide button bits depends on several factors, including:
- Size: Larger diameter bits naturally come at a premium due to the increased amount of material used.
- Carbide Grade: Metal powders with higher cobalt content, prioritizing impact resistance, tend to be more expensive.
- Number of Buttons: Bits with a higher number of buttons generally cost more, but they can also offer improved drilling performance in certain applications.
- Brand Reputation: Established brands with a proven track record might command a slightly higher price tag.
Here’s a ballpark range to provide a general idea:
- Small Button Bits (e.g., 38mm diameter): $20 – $50
- Medium Button Bits (e.g., 50mm diameter): $50 – $100
- Large Button Bits (e.g., 76mm diameter): $100 – $200
It’s important to remember that the initial cost should be evaluated in conjunction with the bit’s lifespan and overall drilling efficiency. Carbide button bits, despite a potentially higher upfront cost, can deliver significant cost savings over time due to their extended wear life and reduced downtime.
Pros and Cons of Carbide Button Bits
Pros
- Superior wear resistance for longer bit life
- Faster penetration rates for increased productivity
- Reduced downtime due to less frequent bit changes
- Versatility across various drilling applications
- Cost-effective in the long run
Cons
- Higher initial cost compared to traditional steel bits
- May not be ideal for very soft rock formations where wear resistance isn’t a primary concern
- Require a compatible drill hammer for proper operation
Carbide Button Bits vs DTH Hammer Bits: A Ring in the Arena
When it comes to drilling tough rock, another contender emerges – the DTH (Down-The-Hole) hammer bit. Here’s a breakdown of how these two titans compare:
- Functionality: Carbide button bits rely on rotary drilling with the buttons crushing the rock. DTH bits employ a hammering action combined with rotation for rock breakage.
- Applications: Carbide button bits excel in applications requiring precise hole diameters, like blasthole drilling and core drilling. DTH bits are better suited for high-production drilling of larger diameter holes, such as water well drilling and foundation drilling.
- Durability: Both bit types offer excellent durability, with carbide button bits boasting superior wear resistance and DTH bits unggul [Indonesian for excelling] in high-impact scenarios.
Ultimately, the choice between carbide button bits and DTH bits depends on the specific drilling project requirements. Consider factors like hole diameter, rock formation, and desired drilling speed to make an informed decision.
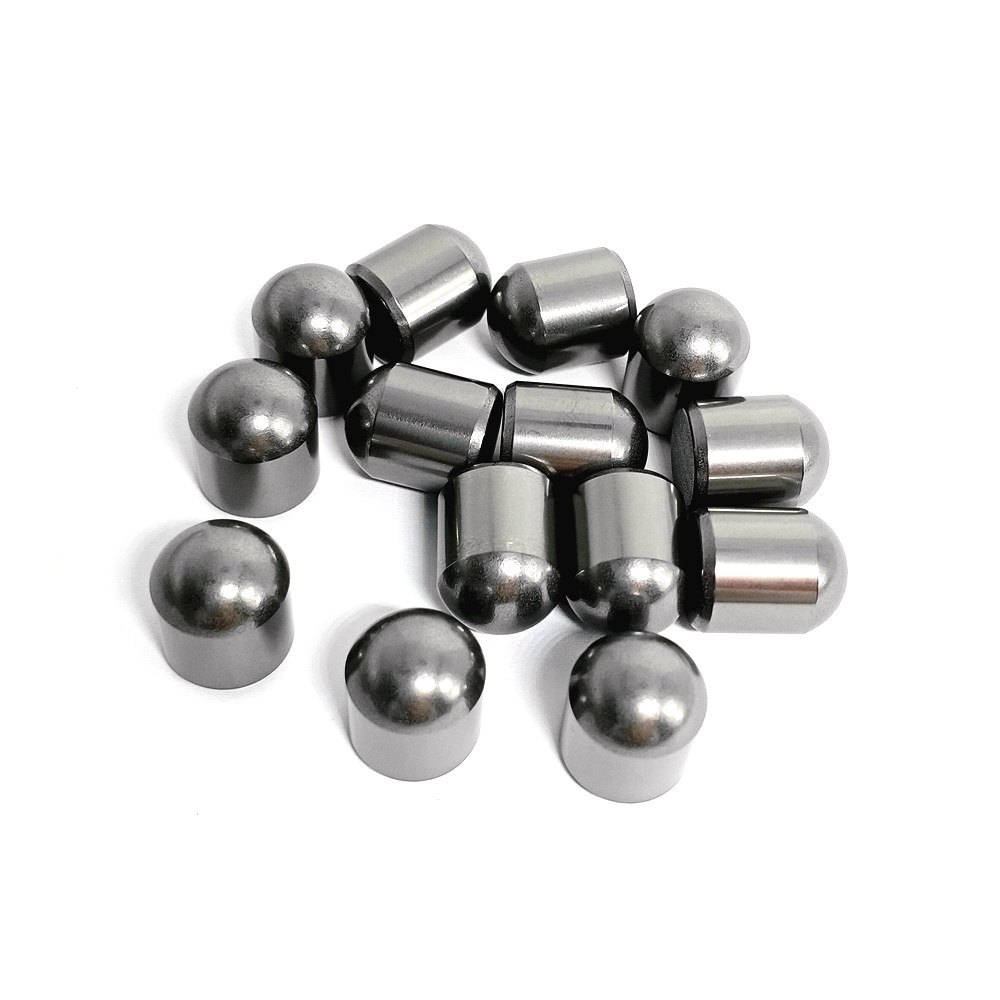
FAQ
Q: What are the different types of carbide button bits?
A: Carbide button bits are categorized based on the number of buttons they have (e.g., single button, double button, three cone) and the type of metal powder used in the buttons (e.g., Cenos, Deloro, Sandvik).
Q: How long do carbide button bits last?
A: The lifespan of a carbide button bit depends on various factors like rock formation, drilling parameters, and bit size. However, they generally last significantly longer than traditional steel bits, reducing downtime and replacement costs.
Q: Can I use carbide button bits for soft rock drilling?
A: While carbide button bits excel in tough rock formations due to their exceptional wear resistance, they can be used for soft rock drilling as well. However, in such applications, the primary advantage of wear resistance becomes less significant. Other bit types, like drag bits, might be more cost-effective for soft rock drilling.
Q: Where can I buy carbide button bits?
A: Carbide button bits can be purchased from various industrial equipment suppliers, drilling tool manufacturers, and online retailers specializing in drilling supplies. It’s recommended to choose a reputable supplier that offers high-quality bits and can provide technical guidance if needed.
Q: How do I choose the right carbide button bit for my application?
A: Selecting the right carbide button bit requires considering several factors:
- Hole diameter: Choose a bit with the appropriate diameter to match your drilling needs.
- Rock formation: Different metal powder grades offer varying degrees of wear resistance and impact strength. Consider the rock’s hardness and abrasiveness to select the optimal grade.
- Drill hammer compatibility: Ensure the bit shank design is compatible with your specific drill hammer model.
- Desired drilling performance: Evaluate factors like penetration rate and overall drilling efficiency when making your choice.
Consulting with a drilling equipment supplier or a drilling specialist can be helpful in selecting the most suitable carbide button bit for your project.
Conclusion
Carbide button bits are a testament to human ingenuity. By combining the strength of steel with the unparalleled wear resistance of tungsten carbide, they have revolutionized the drilling industry. These unassuming heroes conquer challenging rock formations, enabling us to extract valuable resources, build essential infrastructure, and unlock the secrets hidden beneath the earth’s surface. So, the next time you witness a powerful drill chewing through tough rock, remember the silent heroes within – the carbide button bits, relentlessly pushing the boundaries of what’s possible.