Carbide button bits are an integral component in drilling and machining applications across various industries. This article provides a detailed overview of carbide button bits, their composition, properties, manufacturing process, grades, standards, applications, selection criteria, suppliers, and more.
Overview of Carbide Button Bits
Carbide button bits, also known as button bit cutters, are indexable inserts that are brazed or clamped onto the drill bit body. They are made of tungsten carbide for high wear resistance and are used for drilling holes in rock, masonry, concrete and other hard, abrasive materials.
Some key features of carbide button bits include:
- Extremely hard cutting surface for drilling hard, brittle materials
- Indexable inserts can be replaced when worn out instead of the entire drill bit
- Available in a range of sizes, shapes and grades to suit different drilling needs
- Advanced geometries and coatings for optimized drill bit performance
Table 1: Types of Carbide Button Bits
Type | Description |
---|---|
Brazed Button Bits | Carbide buttons brazed to a steel shank |
Clamped Button Bits | Carbide buttons clamped into place by a retainer ring |
Underreamer Button Bits | For enlarging boreholes to a bigger diameter |
Core Drill Button Bits | For extracting core samples from rocks/concrete |
Auger Button Bits | For making deep holes in the ground for pile foundations etc |
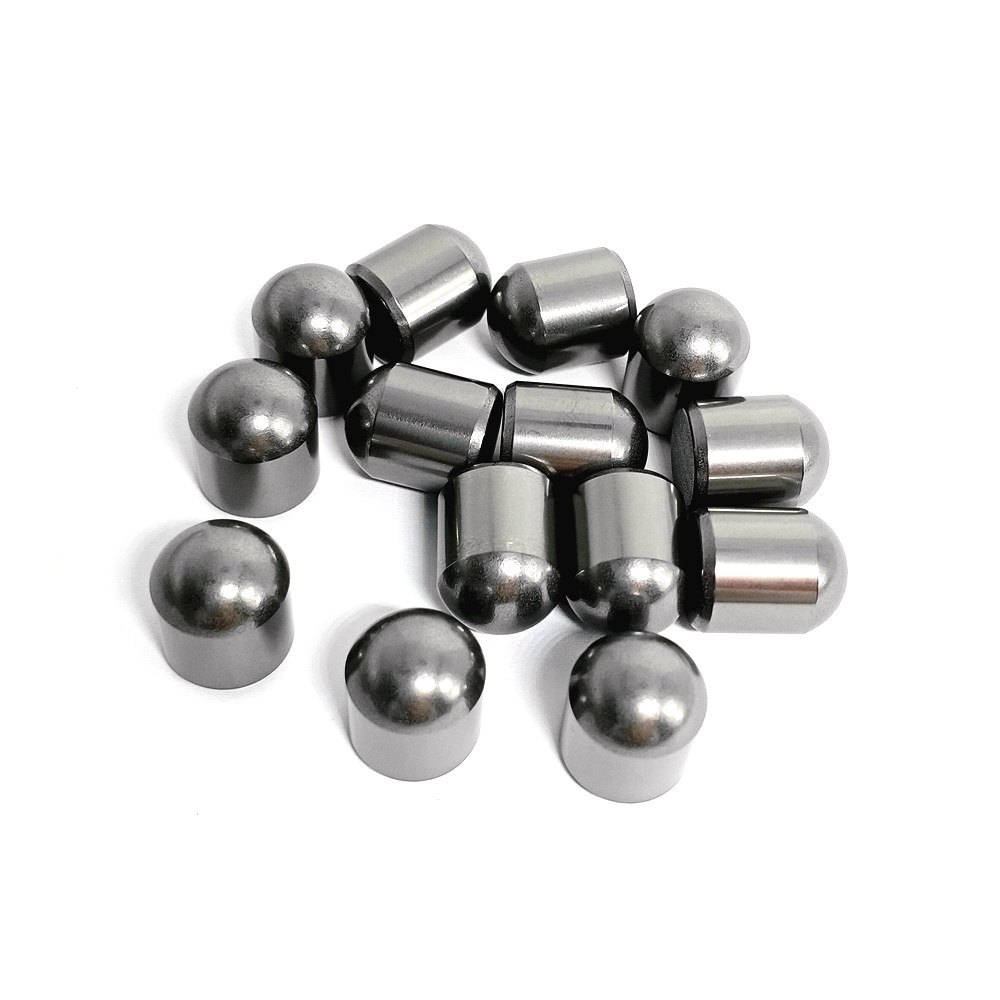
Composition of Carbide Button Bits
Carbide button bits gets their wear resistance, hardness and strength from tungsten carbide along with small amounts of other elements used as binders.
Table 2: Chemical Composition
Material | Composition |
---|---|
Cemented carbide grade | 94% tungsten carbide (WC) + 6% cobalt binder (Co) |
Steel shank | Iron, carbon, chromium, manganese, silicon etc. |
Brazing alloy | Copper, zinc, nickel, silver etc. |
The exact composition and percentages can vary between different carbide grades and manufacturers. The cobalt binder that holds the WC grains together also plays a key role in strength, fracture toughness and wear properties.
Properties of Carbide Button Cutters
Carbide button inserts exhibit an excellent combination of properties that make them suitable for drilling, cutting and machining extremely hard materials:
Table 3: Properties of Carbide Button Bits
Property | Value | Significance |
---|---|---|
Hardness | 1600 – 2200 Vickers | Allows cutting of hard materials like rock or concrete |
Compressive strength | 5500-6500 MPa | Withstands high pressures during drilling |
Transverse rupture strength | 3000-4800 MPa | Resistance to fracturing under bending loads |
Toughness | Up to 30 MPa√m | Resistance to crack propagation |
Wear resistance | Excellent | Long working life before replacement needed |
Chemical inertia | Highly inert | Unreactive to most chemicals at room temperature |
Thermal conductivity | Lower than steel | Can get hot at the cutter edges during machining |
The properties can be tuned based on composition, grain size, binder content, manufacturing method and post-treatments.
Manufacturing Process
Carbide button inserts go through a complex series of steps during manufacturing:
Table 4: Typical Manufacturing Process
Step | Details |
---|---|
Milling and blending | Blending of tungsten carbide, cobalt, other powders |
Compaction | Pressing powders into a mold under high pressures |
Debinding | Removing binders at approx 300-600°C |
Pre-sintering | Heating compacted powders to 1000-1500°C to strengthen |
Edge preparation | Grinding insert edges into the required geometry |
Surface treatments | Coatings, heat treatment etc. applied to inserts |
Brazing/clamping | Attaching inserts to the steel drill bit body |
Finishing | Final grinding and quality checks before shipment |
The powder metallurgy process allows properties and quality to be closely controlled. Customized geometries, coatings and post-treatments further enhance functionality.
Grades of Carbide Button Bits
Carbide grades are classified based on properties like wear resistance, toughness and hardness which are tailored to suit different applications.
Table 5: Standard Grades and Applications
Grade | Hardness | Toughness | Typical Applications |
---|---|---|---|
C1-C3 | Highest | Low | Machining grey cast iron or non-ferrous metals |
C5-C8 | Very high | Medium | Continuous cutting of hardened steels or cast iron |
C8-C9 | Extremely high | Low | Interrupted machining of hardened steels |
P10-P50 | Medium to very high | Medium to high | Rock drilling tools, oil/gas drilling buttons |
Custom grades outside standard classifications are also offered by several manufacturers nowadays.
International Standards
Key standards that specify requirements, test methods and quality parameters for indexable carbide inserts relevant to button bits include:
- ISO 513: Classification and application of hard cutting materials based on hardness
- ANSI B212.15: Carbide inserts standards in the USA covering geometry, identification, tolerances and testing
- ISO 1832: Drawings, dimensions and marking conventions for indexable inserts
- ISO 8249-1: Tool life testing standards for single point turning tools
Reputable carbide button bit manufacturers would comply with these or equivalent national/international standards during manufacturing and quality testing.
Typical Sizes and Dimensions
Carbide button bits are available in a wide range of standard and custom sizes tailored to customer requirements:
Table 6: Standard Button Bit Dimensions
Parameter | Size Range |
---|---|
Button diameter | 8 mm to 150 mm |
Button thickness | 2 mm to 20 mm |
Drill diameter | Up to 1200 mm |
Hole depth | Up to 30 m |
Number of buttons | Up to 30 |
Button edge radius | 0.4 mm to 3 mm |
Button center angle | Usually 90° or 115° |
Applications and Industries
Some leading application areas and industry verticals for carbide button bits include:
Table 7: Applications of Carbide Button Bits
Sector | Typical Applications |
---|---|
Construction | Drilling concrete, masonry, natural stone, tiles |
Mining | Coal, ore exploration drilling, taking core samples |
Oil/gas | Downhole button bits for well drilling |
Quarrying | Granite, limestone, sandstone drilling |
Geothermal | Deep well drilling through hard rock |
Foundation work | Bored pile construction |
Archaeology | Taking samples from structures or rock |
Carbide button bits are indispensable across industries whenever drilling, boring or coring needs to be performed in extra hard materials.
How to Select Carbide Button Bits
Proper selection of composition, size and design is vital for carbide button bits to deliver optimal lifetime and performance.
Table 8: Carbide Button Bit Selection Criteria
Parameter | Factors to Consider |
---|---|
Bit diameter | Size of hole, depth of borehole/pile |
Number of buttons | Weight on bit, drill power, bore diameter |
Button size | Size and position of buttons for even wear and load distribution |
Button grade | Abrasion, impact strength needs |
Bit type | Based on machine/mounting method – clamped vs brazed |
Coatings | Uncoated, TiN, TiCN etc. coatings for toughness or lubricity |
Coolant compatibility | Ensure carbide grade and coatings withstand coolant |
Consult manufacturers providing computer modeling services to simulate button bit performance for optimal selection.
Leading Manufacturers and Suppliers
Some top carbide button bit brands across the globe include:
Table 9: Major Carbide Button Bit Manufacturers
Company | Location |
---|---|
Atlas Copco Secoroc | Sweden |
Palbit | India |
Mincon | Ireland |
Rockmore International | USA |
Numa Tool Company | USA |
DrillcoTools | UK |
Rock Eye | South Africa |
Pricing
Carbide button bit pricing depends on size, grade, coatings and order volumes. Typical price range is USD 4 – 12 per insert. Custom bits are more expensive. Volume discounts apply for bulk orders.
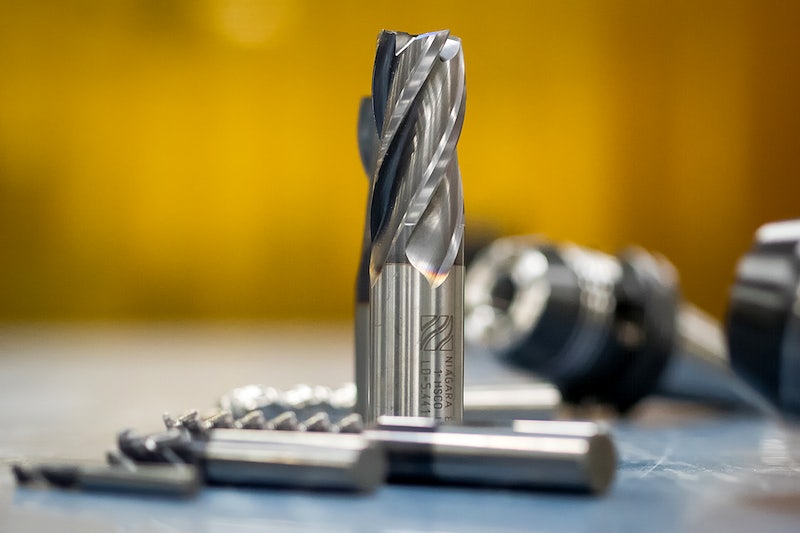
Pros and Cons of Carbide Button Bits
Table 10: Advantages and Limitations
Benefits | Drawbacks |
---|---|
Extremely hard cutting surface | Brittle materials prone to cracking under impact loads |
Higher drilling rates in hard materials | More expensive than steel button bits |
Indexable inserts are replaceable | Not recommended for drilling soft formation |
Wide range of grades and geometries | Requires rigidity in mounting and machine tool |
Advanced coatings resist wear and heat | Coolants required for temperature control |
Consistent hole diameters | Holes may deviate if bits are unevenly worn |
FAQs
Q: Are carbide button bits better than roller cone bits?
A: Carbide button bits offer higher penetration rates in hard, abrasive formations like granite or concrete compared to roller cone bits which perform better in softer sedimentary rocks. They have different optimum applications.
Q: How long can carbide button bits last?
A: Carbide grade, drilling application and operating conditions dictate working lifetimes. On average, carbide button bits can drill 50-200 linear feet before requiring replacement whereas roller cone bits may only last 25-100 feet.
Q: Can carbide inserts be resharpened and reused?
A: No, carbide buttons cannot be resharpened after becoming blunt unlike steel bits. The whole insert has to be discarded and replaced with a fresh indexable carbide button for continued drilling.
Q: How are carbide buttons attached to drill bits?
A: Carbide buttons may be brazed into precisely machined grooves on the drill bit steel shank. Alternatively, clamping systems using rings or blocks are used to hold inserts in place for easy indexability.
Q: What drill bits can bore through reinforced concrete?
A: Carbide button bits with ultra hard grades like C6-C8 with TiCN coatings are commonly used for drilling reinforced concrete. Diamond core bits are also suitable but more expensive.