Overview
Carbide brazed tips are a cornerstone in the world of machining and cutting tools. They offer exceptional hardness, strength, and wear resistance, making them invaluable in various industrial applications. These tips are manufactured by brazing, where a filler metal is melted and flowed into the joint between two close-fitting parts, creating a strong and durable bond. In this guide, we’ll dive deep into the world of carbide brazed tips, exploring their types, applications, properties, composition, and more. We’ll also provide insights into selecting the right tips for your needs, along with a detailed FAQ section to address common questions.
What Are Carbide Brazed Tips?
Carbide brazed tips are cutting tools made by attaching a carbide tip to a steel body through a brazing process. Carbide, primarily composed of tungsten carbide (WC), is known for its exceptional hardness and ability to maintain a sharp cutting edge even under extreme conditions. This makes carbide brazed tips highly effective in cutting, drilling, and machining operations, especially on hard materials like metals and alloys.
Why Are Carbide Brazed Tips So Popular?
You might wonder, why are these tiny pieces of metal so important? The answer lies in their unique properties. Carbide brazed tips combine the hardness and wear resistance of carbide with the toughness and flexibility of steel. This combination allows for efficient machining with reduced wear, longer tool life, and ultimately, lower operational costs. Whether you’re cutting through stainless steel or machining aluminum, carbide brazed tips ensure precision, durability, and efficiency.
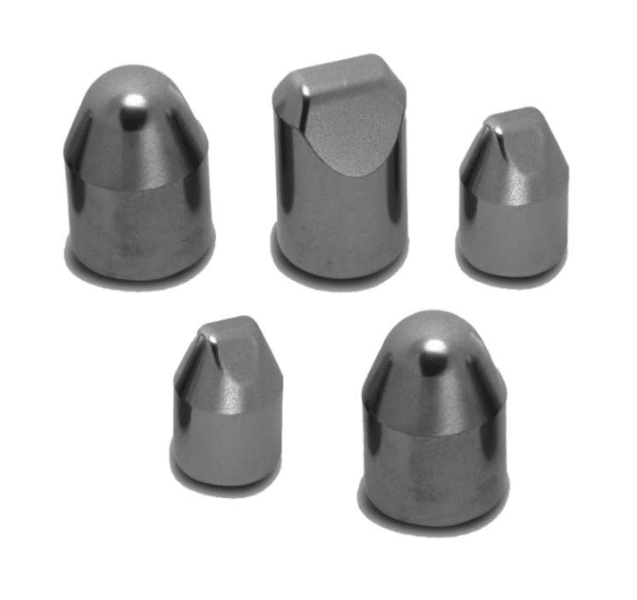
Types of Carbide Brazed Tips
Carbide brazed tips come in various shapes and sizes, each designed for specific applications. Below is a table categorizing different types of carbide brazed tips:
Type | Shape | Application | Common Materials |
---|---|---|---|
Square Tips | Square | General-purpose machining, turning | Tungsten Carbide (WC), Cobalt Binder |
Rectangular Tips | Rectangular | Planing, turning, and facing operations | Tungsten Carbide (WC), Nickel Binder |
Triangular Tips | Triangular | Finishing operations, light machining | Tungsten Carbide (WC), Cobalt Binder |
Round Tips | Round | Milling, light roughing, and semi-finishing | Tungsten Carbide (WC), Titanium Binder |
Diamond Tips | Diamond | High-precision cutting, fine finishing | Tungsten Carbide (WC), Tantalum Binder |
Special Form Tips | Custom Shapes | Specialized machining tasks, custom requirements | Tungsten Carbide (WC), Mixed Binders |
ISO Standard Tips | Various (ISO Standards) | Standardized for universal applications | Tungsten Carbide (WC), Various Binders |
Grooving Tips | Grooved | Precision grooving and threading | Tungsten Carbide (WC), Cobalt Binder |
Brazed Carbide Inserts | Insert-like | Heavy-duty cutting and shaping | Tungsten Carbide (WC), Nickel Binder |
Special Alloy Tips | Alloy-specific | Cutting specific alloys like Inconel or Titanium | Tungsten Carbide (WC), Nickel/Cobalt Binder |
Each type of carbide brazed tip is engineered to optimize performance for its intended use, from roughing to finishing, or cutting complex geometries.
Applications of Carbide Brazed Tips
Carbide brazed tips are versatile and can be used in a wide range of applications. The following table highlights some of the most common applications:
Industry | Application | Preferred Tip Type |
---|---|---|
Automotive | Engine block machining, transmission parts | Rectangular Tips, ISO Standard Tips |
Aerospace | Machining of turbine blades, structural components | Special Alloy Tips, Triangular Tips |
Oil & Gas | Drilling, pipeline machining | Round Tips, Special Form Tips |
Metalworking | General machining, turning, and facing | Square Tips, Rectangular Tips |
Construction | Cutting and shaping of building materials | Diamond Tips, Special Alloy Tips |
Medical Devices | Precision cutting for implants, surgical tools | Grooving Tips, Triangular Tips |
Electronics | Machining of micro-components | Diamond Tips, Round Tips |
Tool & Die | Die and mold making | Special Form Tips, ISO Standard Tips |
Woodworking | Cutting and shaping of hard woods | Rectangular Tips, Square Tips |
Mining | Rock drilling, excavation tools | Special Alloy Tips, Round Tips |
The right selection of carbide brazed tips ensures maximum efficiency and precision in the specific application, whether in high-volume production or specialized machining tasks.
Material Properties of Carbide Brazed Tips
The performance of carbide brazed tips is determined by their material properties. Here’s a breakdown of key material characteristics:
Property | Description |
---|---|
Hardness | Carbide brazed tips typically range from 85 to 92 HRA (Rockwell A Hardness). |
Toughness | The steel body provides toughness, absorbing shocks during machining. |
Wear Resistance | Exceptional due to the high hardness of the carbide material. |
Thermal Stability | Retains hardness and strength at high temperatures, reducing tool wear. |
Chemical Resistance | Resistant to corrosion and chemical wear, especially with cobalt and nickel binders. |
Edge Retention | Maintains a sharp edge longer than other materials, reducing the frequency of tool changes. |
These properties make carbide brazed tips ideal for demanding applications where precision and durability are paramount.
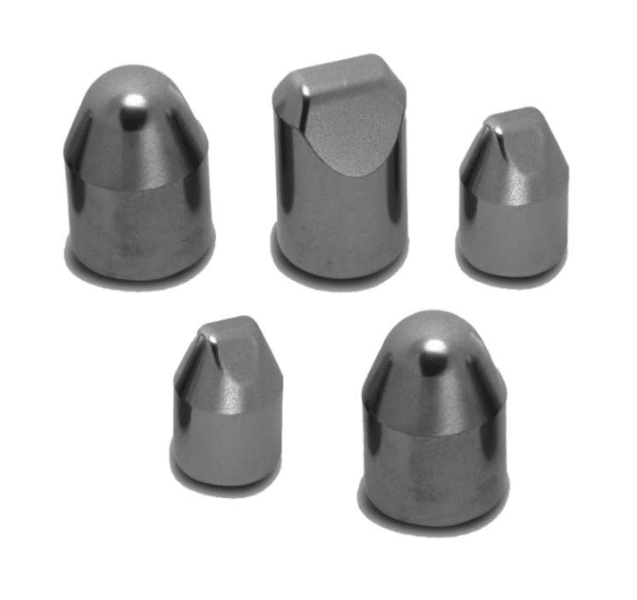
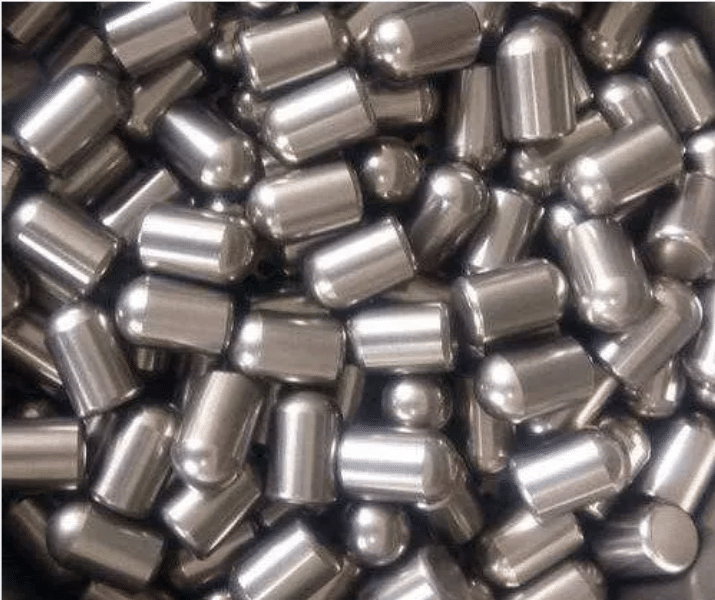
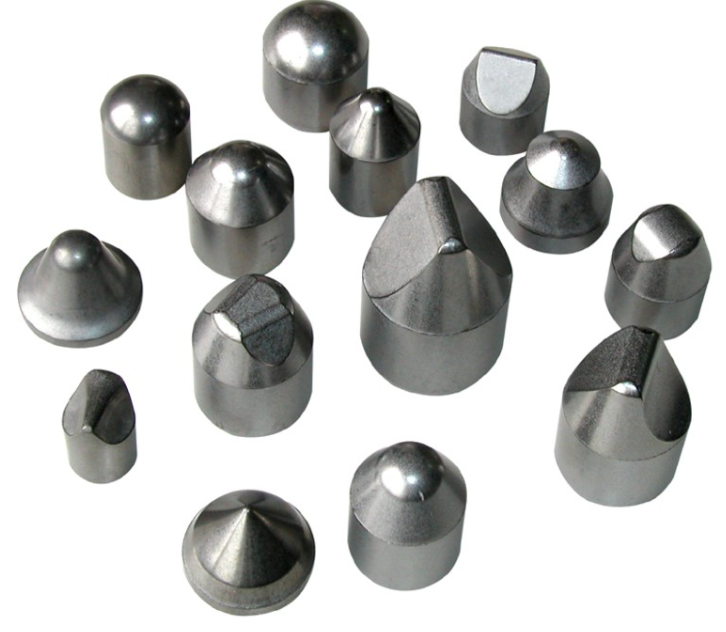
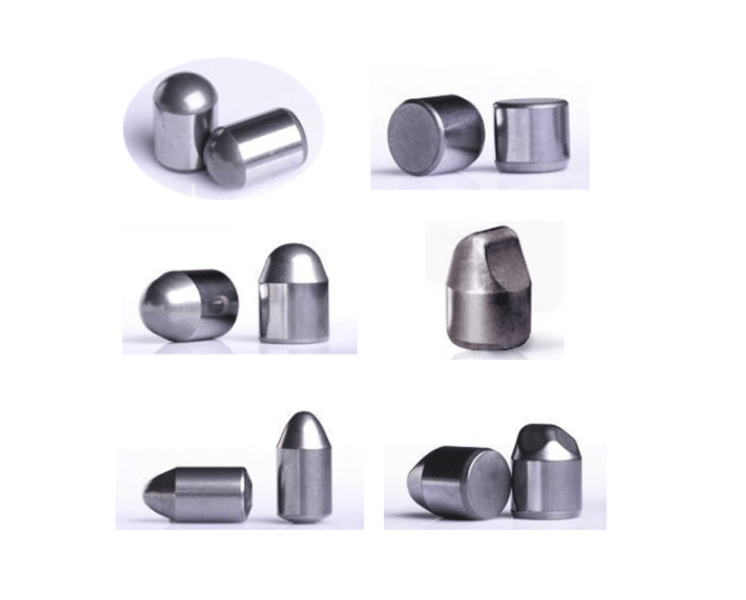
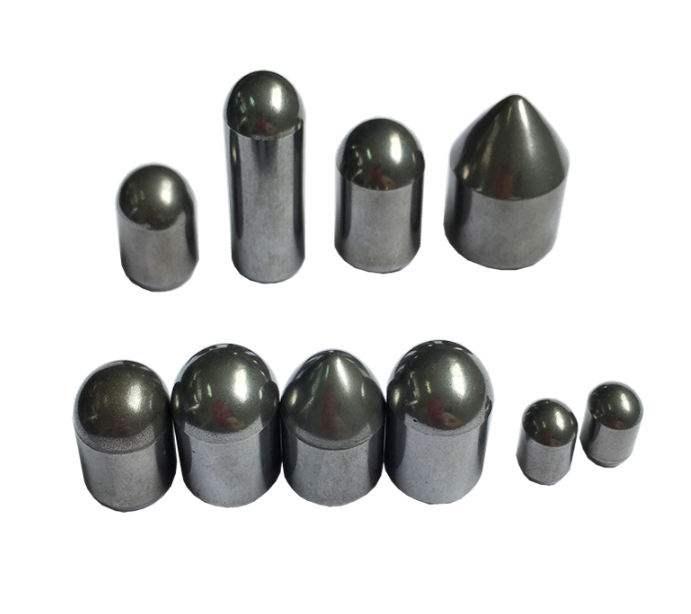
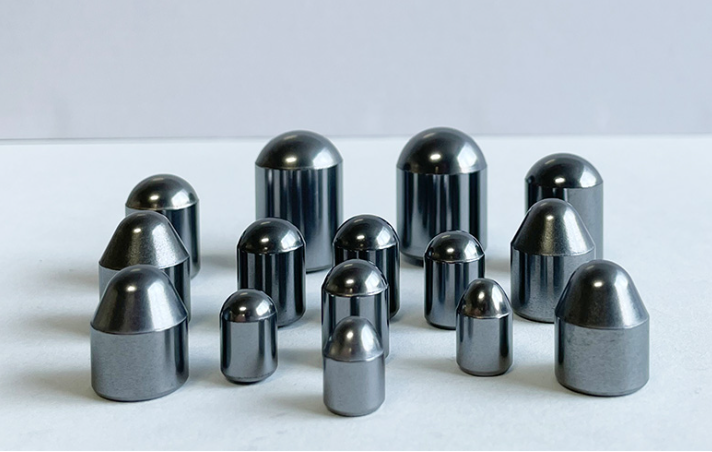
Composition and Characteristics of Carbide Brazed Tips
The composition of carbide brazed tips typically includes a mix of tungsten carbide and a metallic binder. The table below outlines the common compositions and their characteristics:
Component | Percentage | Characteristics |
---|---|---|
Tungsten Carbide (WC) | 85-95% | Provides hardness and wear resistance. |
Cobalt Binder | 5-10% | Enhances toughness and impact resistance. |
Nickel Binder | 3-7% | Improves corrosion resistance and high-temperature performance. |
Tantalum Carbide (TaC) | 1-2% | Enhances resistance to deformation and thermal stability. |
Titanium Carbide (TiC) | 1-2% | Increases wear resistance, particularly in abrasive environments. |
Other Additives | Trace amounts | Various elements can be added to improve specific properties like machinability or adhesion. |
The specific combination of these materials can be tailored to suit different applications, optimizing the performance of the carbide brazed tips.
Understanding Hardness, Strength, and Wear Resistance
When it comes to cutting tools, hardness, strength, and wear resistance are crucial factors that determine performance and longevity. Here’s a detailed comparison:
Metric | Description | Carbide Brazed Tips | High-Speed Steel (HSS) | Ceramics |
---|---|---|---|---|
Hardness | Resistance to deformation | 85-92 HRA | 62-65 HRC | 92-96 HRA |
Strength | Ability to withstand stress | High | Very High | Moderate |
Wear Resistance | Ability to resist wear over time | Excellent | Good | Excellent |
Thermal Stability | Performance under high temperatures | High | Moderate | Very High |
Edge Retention | How long the cutting edge remains sharp | Superior | Good | Superior |
Toughness | Resistance to chipping and cracking | Moderate | High | Low |
Compared to other materials, carbide brazed tips offer an excellent balance of hardness, wear resistance, and thermal stability, though they may be slightly less tough than high-speed steel, making them more suited to certain applications.
Specifications, Sizes, Shapes, and Standards
Selecting the right carbide brazed tip involves understanding its specifications, including size, shape, and industry standards. Here’s a guide:
Specification | Details | Common Standards |
---|---|---|
Size | Length, width, and thickness can vary depending on application | ISO, ANSI, DIN |
Shape | Square, rectangular, round, diamond, triangular, or custom | ISO, ANSI, DIN |
Grade | Indicates the carbide grade used | ISO K10, K20, P10, P20 |
Coating | Some tips are coated for additional wear resistance (e.g., TiN, TiC coatings) | ISO, ANSI, DIN |
Tolerance | Precision of the tip dimensions | ISO H7, H6, J6 |
Tip Angle | The angle of the cutting edge | 30°, 45°, 60°, 90° |
Material Composition | Proportion of carbide to binder | 85% WC / 15% Co, 90% WC / 10% Ni |
Mounting Method | How the tip is attached (brazed, clamped, etc.) | ISO, ANSI, DIN |
Selecting the right combination of these specifications ensures optimal performance for your specific machining needs.
Suppliers and Pricing Details
Finding the right supplier for carbide brazed tips can be a daunting task. Here’s a comparative guide:
Supplier | Product Range | Pricing (Per Unit) | Additional Services |
---|---|---|---|
Kennametal | Wide range of carbide tips, including custom solutions | $10 – $100 | Custom design, technical support |
Sandvik | High-quality standard and ISO tips | $15 – $120 | On-site consultation, rapid delivery |
Mitsubishi Materials | Specialized in alloy-specific tips | $12 – $110 | Application engineering, technical advice |
Ceratizit | Standard and specialized tips | $8 – $95 | Tool management, technical support |
Sumitomo Electric | High-performance tips for precision machining | $20 – $150 | Custom solutions, technical expertise |
ISCAR | Comprehensive range, including heavy-duty tips | $18 – $130 | Tool selection assistance, custom manufacturing |
Walter Tools | Focused on high-precision tips | $25 – $140 | Training, application engineering |
Tungaloy | Heavy-duty and alloy-specific tips | $22 – $135 | Technical consulting, rapid prototyping |
Kyocera | Precision tips for specialized applications | $16 – $125 | Custom tooling, process optimization |
YG-1 | Cost-effective solutions with high quality | $9 – $105 | Technical advice, custom design |
The prices can vary widely based on the tip’s specifications, the volume of purchase, and the additional services offered by the supplier.
How to Select the Right Carbide Brazed Tips
Choosing the right carbide brazed tip is crucial for optimizing performance and ensuring cost-effectiveness. Here’s a guide to help you make the right decision:
Factor | Consideration | Recommendation |
---|---|---|
Material Being Machined | Different materials require different carbide grades | For hard materials like steel, use higher WC content tips; for softer materials, consider lower WC content. |
Machining Operation | Roughing, finishing, drilling, etc. | For roughing, choose tougher, high-impact tips; for finishing, opt for high-hardness tips. |
Machine Power | The power of your machine determines the type of tip needed | For high-power machines, use tips with higher wear resistance. |
Cutting Speed | Higher speeds require better thermal stability | For high-speed operations, choose tips with superior thermal stability. |
Cost Considerations | Balance between cost and performance | If budget allows, invest in higher-quality tips for longer tool life and better performance. |
Tool Holder Compatibility | Ensure the tip is compatible with your tool holder | Check specifications and standards (e.g., ISO) for compatibility. |
Coating Requirements | Some operations benefit from coated tips | For abrasive materials, consider TiN or TiC coated tips for extended tool life. |
Precision Needs | High-precision operations require finer tips | For precision machining, opt for tips with tighter tolerances and higher grades. |
Supplier Support | Consider suppliers that offer technical support | Choose suppliers who provide after-sales support and technical assistance. |
Selecting the right carbide brazed tip involves considering multiple factors, from the material being machined to the specific operation, machine power, and budget.
Advantages and Limitations of Carbide Brazed Tips
Understanding the pros and cons of carbide brazed tips helps in making informed decisions:
Aspect | Advantages | Limitations |
---|---|---|
Hardness | Exceptional hardness allows for precise cutting of hard materials | May be too brittle for some applications |
Wear Resistance | Superior wear resistance extends tool life | Higher cost compared to other materials |
Thermal Stability | Maintains performance under high temperatures | Requires proper cooling to avoid thermal shock |
Edge Retention | Stays sharp longer, reducing the need for frequent tool changes | Difficult to re-sharpen once dulled |
Versatility | Suitable for a wide range of materials and operations | Not as tough as high-speed steel, prone to chipping in some cases |
Cost-Effectiveness | Long tool life reduces overall operational costs | Initial cost is higher than other cutting tools |
Chemical Resistance | Resistant to corrosion and chemical wear | Limited to certain binder compositions for optimal resistance |
Precision | Offers high precision in cutting and machining | Requires careful handling to avoid damage during installation |
Balancing these advantages and limitations is key to optimizing performance and cost-efficiency in your machining operations.
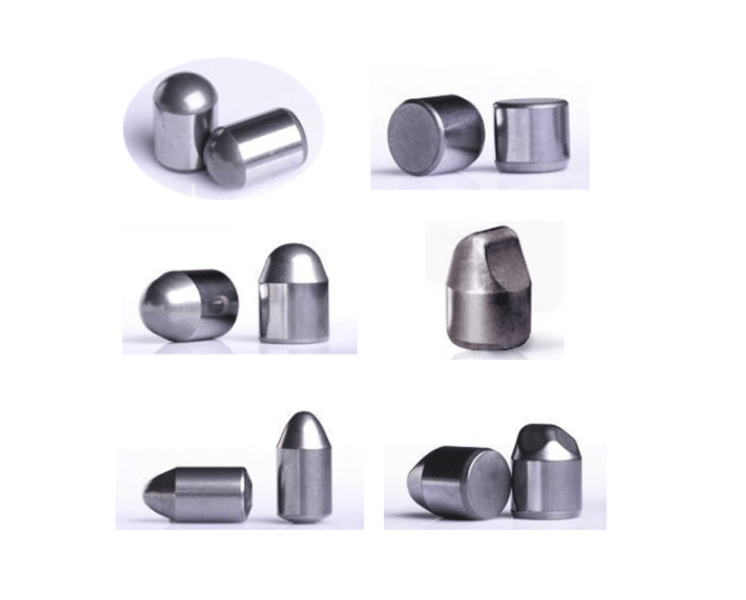
FAQ
Q1: What are carbide brazed tips primarily used for?
A: Carbide brazed tips are used in machining, cutting, and drilling operations, particularly where high hardness and wear resistance are required. They are ideal for working with hard materials like metals, alloys, and some ceramics.
Q2: How do I choose the right carbide brazed tip for my application?
A: Consider the material being machined, the type of operation (e.g., roughing, finishing), machine power, cutting speed, and your budget. It’s also important to ensure compatibility with your tool holder and to consider whether a coated tip is necessary.
Q3: Can carbide brazed tips be re-sharpened?
A: While it is possible to re-sharpen carbide brazed tips, it can be challenging due to their hardness. Often, it is more cost-effective to replace the tip rather than re-sharpen it, especially in high-precision applications.
Q4: How do carbide brazed tips compare to other cutting tools?
A: Compared to high-speed steel (HSS) or ceramic tools, carbide brazed tips offer superior hardness, wear resistance, and thermal stability. However, they may be more brittle and expensive, making them less suitable for certain applications.
Q5: Are there any specific maintenance practices for carbide brazed tips?
A: Yes, carbide brazed tips should be handled carefully to avoid chipping. Proper cooling during machining is also important to prevent thermal shock. Regular inspection for wear and timely replacement is crucial for maintaining optimal performance.