Overview
Carbide brazed tips are an essential component in cutting tools used across various industries. These tips are made from tungsten carbide, known for its exceptional hardness and resistance to wear. The process of brazing involves joining the carbide tip to a tool body made of a different material, typically steel, using a filler metal. This ensures a strong bond that can withstand the high stresses and temperatures encountered during cutting operations.
In this article, we will dive deep into the world of carbide brazed tips, exploring their types, applications, material properties, composition, and more. We’ll also provide insights on how to select the right carbide brazed tips for your specific needs, and we’ll compare different products on the market. Let’s get started!
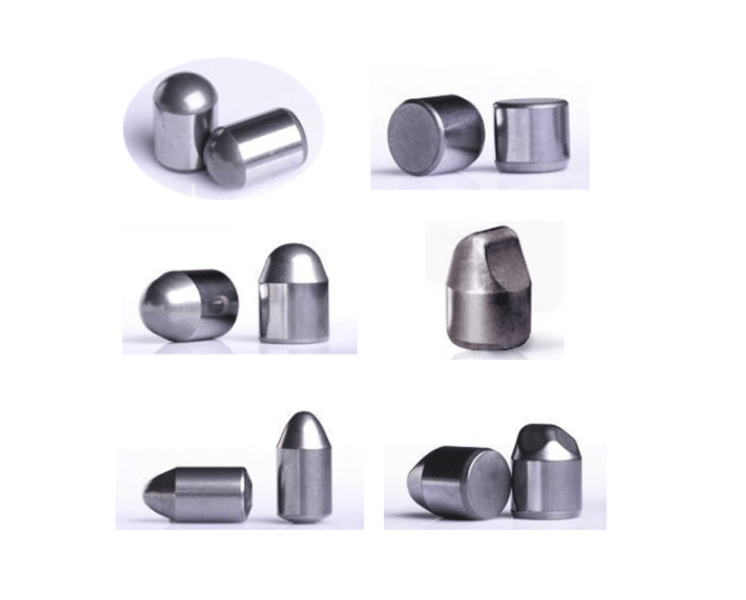
Types of Carbide Brazed Tips
A Detailed Look at Different Types of Carbide Brazed Tips
When it comes to carbide brazed tips, there is a wide variety to choose from, each suited to specific applications and materials. Below is a detailed breakdown of the most common types of carbide brazed tips:
Type of Carbide Brazed Tip | Description |
---|---|
C2 Grade Tips | Designed for general-purpose cutting, milling, and turning of non-ferrous metals and cast iron. |
C5 Grade Tips | Suitable for heavy-duty cutting and interrupted cuts in tougher materials like alloy steels. |
C6 Grade Tips | Ideal for finishing operations on harder materials, providing a fine surface finish. |
K10 Grade Tips | Commonly used for cutting non-metallic materials, such as wood, plastics, and composites. |
P10 Grade Tips | Optimized for high-speed steel (HSS) applications, offering improved performance and longevity. |
P20 Grade Tips | Versatile tips for general-purpose machining of steel and cast iron with moderate cutting speeds. |
M40 Grade Tips | Best for machining stainless steel and other tough alloys, ensuring minimal wear. |
T15 Grade Tips | Tailored for machining at extremely high speeds, offering high heat resistance. |
H10 Grade Tips | Specially designed for applications requiring high toughness and impact resistance. |
K20 Grade Tips | Provides excellent performance in finishing and semi-finishing operations on hard metals. |
Applications of Carbide Brazed Tips
Where Are Carbide Brazed Tips Used?
Carbide brazed tips find applications in a wide array of industries due to their durability and effectiveness. The table below highlights some of the primary applications:
Application | Industry | Example Usage |
---|---|---|
Turning and Boring Operations | Automotive and Aerospace | Engine parts machining, such as pistons and cylinders. |
Milling Operations | Metalworking | Fabrication of metal parts, like brackets and frames. |
Drilling and Reaming | Oil and Gas | Pipe and wellhead component manufacturing. |
Cutting and Grooving | Woodworking | Crafting wooden furniture and decorative items. |
Shaping and Forming | Plastics and Composites | Producing plastic and composite molds and components. |
Profile Cutting | Tool and Die | Manufacturing complex dies and mold inserts. |
Heavy-Duty Cutting | Mining | Rock and ore cutting tools for mining equipment. |
Precision Machining | Medical Device Manufacturing | Machining components for surgical instruments and implants. |
High-Speed Machining | Electronics | Creating precise electronic components and housings. |
General-Purpose Machining | General Engineering | Production of various machine parts and components. |
Material Properties of Carbide Brazed Tips
Understanding the Material Properties
Carbide brazed tips are composed of materials that offer specific properties tailored to different applications. Here’s a breakdown of the key material properties:
Property | Description |
---|---|
Hardness | The ability to withstand surface wear and deformation under high pressure. |
Toughness | The capacity to absorb energy and resist fracture during machining. |
Wear Resistance | Resistance to material loss due to abrasion during cutting operations. |
Heat Resistance | Ability to retain strength and hardness at elevated temperatures. |
Corrosion Resistance | Resistance to chemical degradation in harsh environments. |
Thermal Conductivity | The ability to conduct heat away from the cutting edge, reducing tool wear. |
Density | The mass per unit volume, which affects the tool’s strength and rigidity. |
Modulus of Elasticity | The measure of stiffness or rigidity of the material. |
Coefficient of Expansion | The rate at which the material expands or contracts with temperature changes. |
Electrical Conductivity | Although less critical for cutting tools, it can affect certain applications. |
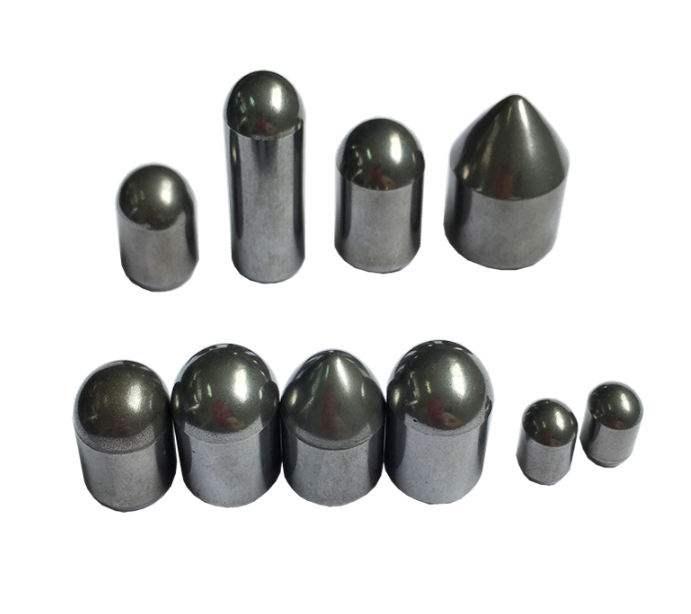
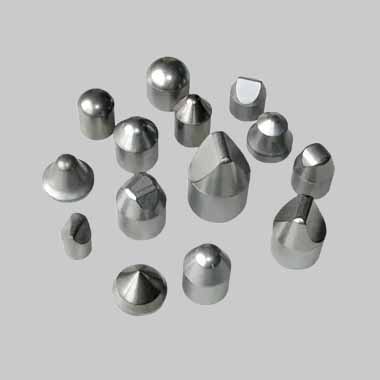
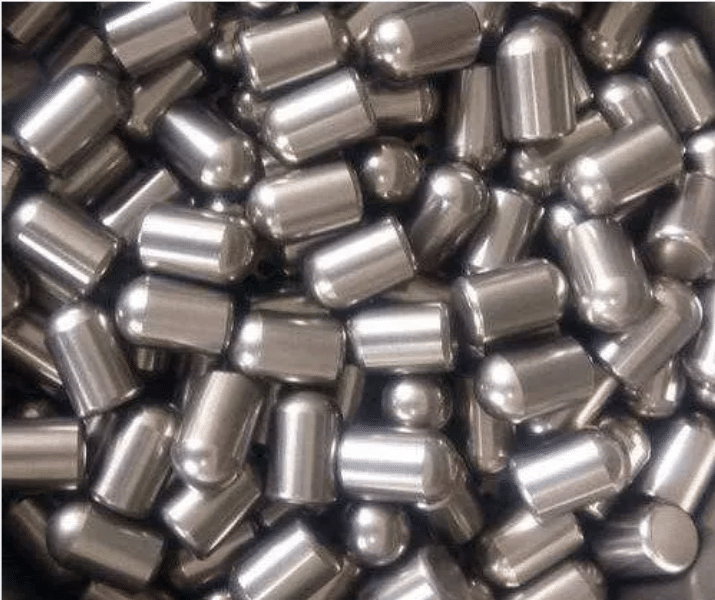
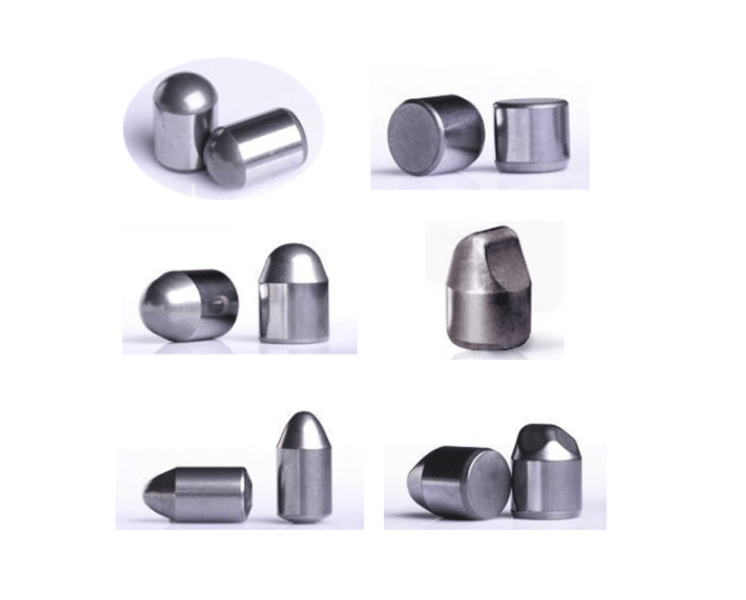
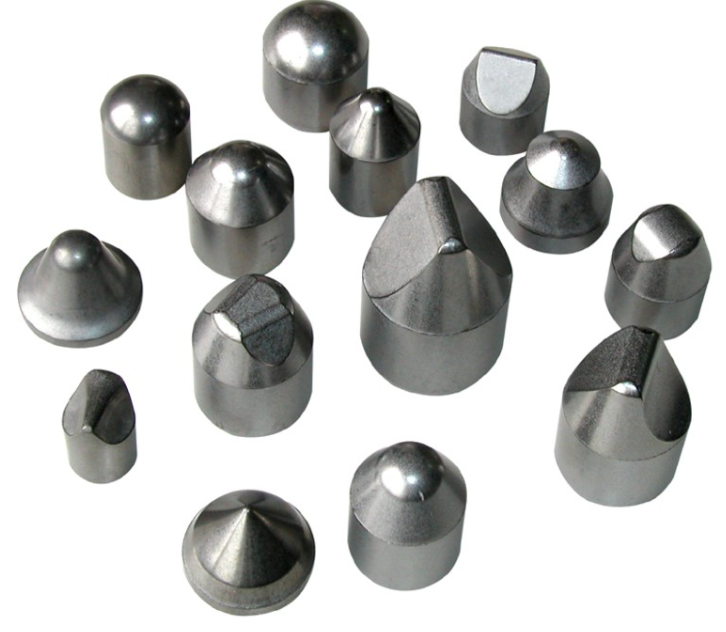
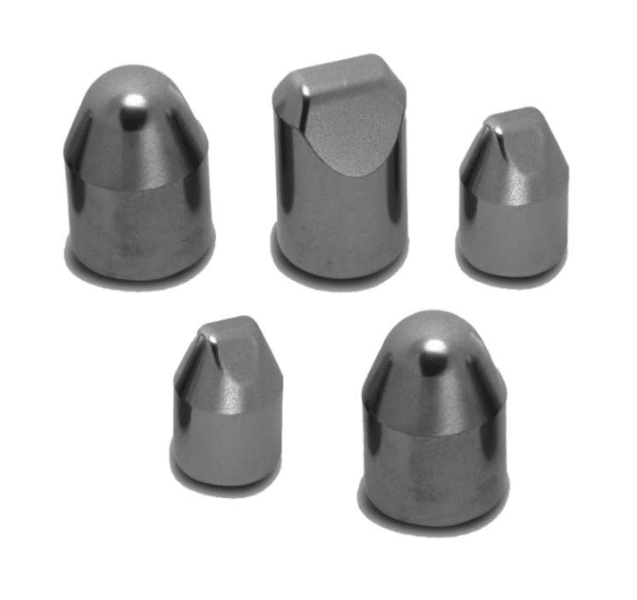
Composition, Properties, and Characteristics
A Closer Look at Composition
The performance of carbide brazed tips is largely dependent on their composition. The table below outlines the typical composition and associated characteristics:
Material Component | Percentage Composition | Characteristics |
---|---|---|
Tungsten Carbide (WC) | 70-94% | Provides hardness and wear resistance. |
Cobalt (Co) | 5-20% | Acts as a binder, offering toughness and shock resistance. |
Titanium Carbide (TiC) | 1-10% | Enhances cutting performance in ferrous materials. |
Tantalum Carbide (TaC) | 1-5% | Improves heat resistance and hardness. |
Niobium Carbide (NbC) | 1-5% | Contributes to high-temperature stability and wear resistance. |
Vanadium Carbide (VC) | 0.5-2% | Increases hardness and edge retention. |
Chromium Carbide (CrC) | 0.5-2% | Provides oxidation resistance, improving tool life. |
Nickel (Ni) | 0.5-2% | Adds corrosion resistance and enhances toughness. |
Hardness, Strength, and Wear Resistance
Why These Properties Matter
Hardness, strength, and wear resistance are critical factors that define the performance of carbide brazed tips. Here’s a comparison of these properties across different grades:
Grade | Hardness (HRA) | Tensile Strength (MPa) | Wear Resistance |
---|---|---|---|
C2 Grade | 88-90 | 1370-1510 | Moderate |
C5 Grade | 85-87 | 1450-1600 | High |
C6 Grade | 90-92 | 1330-1480 | Very High |
K10 Grade | 89-91 | 1400-1550 | Moderate |
P10 Grade | 87-89 | 1350-1500 | High |
P20 Grade | 86-88 | 1380-1530 | Moderate |
M40 Grade | 88-90 | 1420-1570 | Very High |
T15 Grade | 91-93 | 1300-1450 | Extremely High |
H10 Grade | 86-88 | 1450-1600 | High |
K20 Grade | 90-92 | 1370-1510 | Very High |
Specifications, Sizes, Shape, and Standards
Getting the Right Fit: Specifications of Carbide Brazed Tips
Selecting the right carbide brazed tips involves considering various specifications, including size, shape, and adherence to standards. Here’s a comprehensive guide:
Specification | Details |
---|---|
Standard Sizes | Tips are available in standard sizes ranging from 1/8″ to 2″ in width. |
Shape Options | Square, triangular, round, and custom shapes available. |
Thickness Range | Typically ranges from 0.05″ to 0.25″, depending on the application. |
Edge Configuration | Sharp, chamfered, or radiused edges to suit different cutting needs. |
Tolerance Levels | Strict tolerances (±0.001″) to ensure precise fits and optimal performance. |
Industry Standards | Conforms to ISO, ANSI, and DIN standards for quality and consistency. |
Coating Options | Available with coatings like TiN, TiC, or diamond for enhanced performance. |
Suppliers and Pricing Details
Where to Buy Carbide Brazed Tips and What to Expect to Pay
Finding a reliable supplier and understanding the pricing of carbide brazed tips is crucial for making informed purchasing decisions. Below is a list of some top suppliers and their pricing details:
Supplier | Location | Product Range | Price Range (per tip) |
---|---|---|---|
Kennametal | USA | Wide range of grades and sizes. | $5 – $25 |
Sandvik Coromant | Sweden | High-performance tips for specialized applications. | $10 – $35 |
Seco Tools | Sweden | General-purpose and high-speed tips. | $8 – $30 |
Sumitomo Electric | Japan | Advanced tips with custom options. | $12 – $40 |
ISCAR | Israel | Precision tips for demanding applications. | $15 – $50 |
Kyocera | Japan | Wide selection with competitive pricing. | $7 – $28 |
Tungaloy | Japan | Tips with high wear resistance. | $9 – $32 |
Walter Tools | Germany | Premium-grade tips with custom solutions. | $14 – $45 |
Carbide Depot | USA | Economical options for standard applications. | $6 – $20 |
Mitsubishi Materials | Japan | High-precision tips for complex machining. | $10 – $38 |
Selecting the Right Carbide Brazed Tips
How to Choose the Best Carbide Brazed Tips for Your Needs
Choosing the right carbide brazed tips can make a significant difference in performance and cost-efficiency. Here are key considerations:
Consideration | Explanation |
---|---|
Material Being Machined | Different tips are optimized for different materials; choose based on the specific material you’re working with. |
Cutting Speed | High-speed operations require tips with high heat resistance, such as T15 Grade. |
Surface Finish | For a fine surface finish, opt for tips like C6 Grade designed for finishing operations. |
Tool Life | Consider tips with high wear resistance, like M40 Grade, for extended tool life in harsh conditions. |
Cost vs. Performance | Balance between cost and performance by selecting the tip grade that offers the best ROI for your application. |
Supplier Reliability | Choose reputable suppliers known for consistent quality and reliable delivery. |
Standard Compliance | Ensure the tips meet industry standards like ISO or ANSI for quality assurance. |
Customization Needs | For specialized tasks, consider suppliers that offer custom shapes and sizes. |
Advantages and Limitations of Carbide Brazed Tips
Comparing the Pros and Cons
Carbide brazed tips come with their own set of advantages and limitations, making it essential to weigh these factors when deciding on the right tool for your needs:
Advantages | Limitations |
---|---|
High Hardness and Wear Resistance | Higher initial cost compared to other materials. |
Excellent Performance in High-Temperature Environments | May require specialized brazing skills for proper attachment. |
Versatility Across Various Materials | Less forgiving in terms of impact and shock, leading to potential fracture. |
Longer Tool Life | Limited availability in some custom sizes and shapes. |
Improved Cutting Efficiency | Requires precise setup and alignment for optimal performance. |
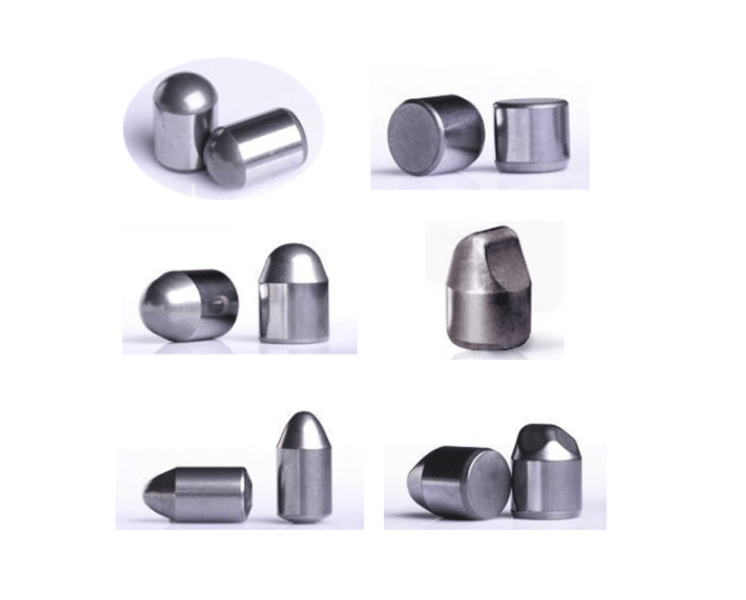
FAQs
Question | Answer |
---|---|
What are carbide brazed tips made of? | They are primarily made of tungsten carbide, cobalt, and other metallic carbides. |
How do carbide brazed tips differ from other cutting tools? | They offer higher hardness, wear resistance, and can handle high temperatures compared to HSS tools. |
Can carbide brazed tips be resharpened? | Yes, but resharpening should be done carefully to maintain the original geometry and cutting edge. |
What is the typical lifespan of a carbide brazed tip? | The lifespan varies depending on the material being machined and the cutting conditions, but they generally last longer than HSS tools. |
How do I know which grade of carbide brazed tip to use? | Choose the grade based on the material you’re machining, the cutting speed, and the desired surface finish. |
Are there any specific safety precautions when using carbide brazed tips? | Ensure proper tool setup and alignment, use appropriate speeds and feeds, and wear protective gear. |
What factors affect the cost of carbide brazed tips? | Factors include the grade, size, shape, supplier, and any customizations required. |
Can I use carbide brazed tips on non-metallic materials? | Yes, certain grades like K10 are specifically designed for non-metallic materials. |
What is the process of brazing the tips onto the tool body? | Brazing involves heating the filler metal to bond the carbide tip to the tool body, ensuring a strong, durable joint. |
Where can I purchase high-quality carbide brazed tips? | Reputable suppliers include Kennametal, Sandvik Coromant, and ISCAR, among others. |
Conclusion
Carbide brazed tips are a cornerstone in the machining industry, offering unparalleled hardness, wear resistance, and performance in a variety of applications. Understanding the different types, applications, material properties, and how to select the right tip for your needs can significantly impact the efficiency and cost-effectiveness of your operations. Whether you’re working with metal, wood, or composites, choosing the right carbide brazed tip can make all the difference in achieving optimal results.
Remember to consider all the factors discussed in this article, from material composition to supplier reliability, and ensure you are using tips that meet industry standards for the best outcomes. With the right knowledge and tools at your disposal, you’re well-equipped to tackle any machining challenge that comes your way.