Overview
Carbide blanks are the unsung heroes of the machining world. They are the foundation for a wide range of cutting and drilling tools, providing the necessary strength and durability required for high-performance applications. In this article, we will delve into the workings of a carbide blanks factory, exploring the types of metal powders used, their properties, and the applications of these versatile materials. We’ll also provide detailed comparisons, tables, and insights into selecting the right carbide blanks for your needs.
What are Carbide Blanks?
Carbide blanks are raw materials made from cemented carbide, which is a composite material consisting of fine particles of carbide cemented into a metallic binder. They are essential in the manufacturing of cutting tools, dies, and wear-resistant parts due to their exceptional hardness and resistance to wear and deformation. Think of carbide blanks as the raw dough in the bakery of industrial manufacturing; they are molded, shaped, and refined into the precise tools and components needed across various industries.
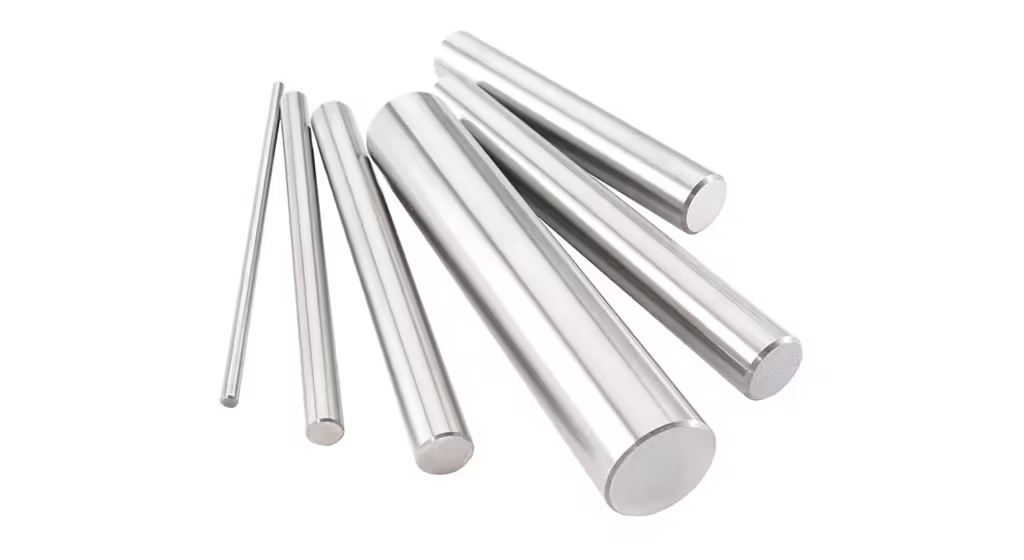
Types of Carbide Blanks
Carbide blanks come in various types, each designed for specific applications and made from different metal powder models. Below is a detailed table highlighting some of the most common types:
Type of Carbide Blank | Description | Metal Powder Models |
---|---|---|
Tungsten Carbide Blanks | High hardness and wear resistance. Ideal for cutting tools. | WC, W2C |
Cobalt-Carbide Blanks | Enhanced toughness and strength. Used in mining tools. | Co, CoCr |
Titanium Carbide Blanks | Excellent thermal stability. Used in aerospace. | TiC, TiCN |
Tantalum Carbide Blanks | High melting point. Suitable for high-temperature applications. | TaC, TaCN |
Niobium Carbide Blanks | Good corrosion resistance. Used in chemical industries. | NbC, NbCN |
Chromium Carbide Blanks | High hardness and corrosion resistance. Used in coatings. | Cr3C2, Cr7C3 |
Vanadium Carbide Blanks | Improves wear resistance of steel. Used in tool steels. | VC, VCN |
Molybdenum Carbide Blanks | Good toughness and hardness. Used in electronics. | Mo2C, MoC |
Zirconium Carbide Blanks | High resistance to thermal shock. Used in nuclear applications. | ZrC, ZrCN |
Hafnium Carbide Blanks | Highest melting point. Used in extreme environments. | HfC, HfCN |
Applications of Carbide Blanks
The versatility of carbide blanks allows them to be used in a wide array of applications. The following table summarizes their primary uses:
Application | Description | Type of Carbide Blank |
---|---|---|
Cutting Tools | Used in drills, end mills, and cutting inserts. | Tungsten Carbide, Cobalt-Carbide |
Mining Tools | Essential for drilling and excavation. | Cobalt-Carbide, Titanium Carbide |
Aerospace Components | High precision and thermal stability required. | Titanium Carbide, Tantalum Carbide |
Chemical Processing | Corrosion-resistant tools and components. | Niobium Carbide, Chromium Carbide |
Coatings | Wear-resistant coatings for various tools. | Chromium Carbide, Vanadium Carbide |
Tool Steels | Enhance wear resistance and hardness. | Vanadium Carbide, Molybdenum Carbide |
Electronics | Components requiring good toughness and hardness. | Molybdenum Carbide, Zirconium Carbide |
Nuclear Applications | Materials with high thermal shock resistance. | Zirconium Carbide, Hafnium Carbide |
Extreme Environment Tools | Tools for high-temperature and harsh conditions. | Hafnium Carbide, Tantalum Carbide |
Material Properties of Carbide Blanks
Understanding the material properties of carbide blanks is crucial for selecting the right type for your application. The table below outlines the key properties:
Property | Description | Typical Values |
---|---|---|
Hardness | Resistance to deformation and wear. | 1500-2000 HV (Vickers) |
Density | Mass per unit volume. | 14-15 g/cm³ |
Compressive Strength | Ability to withstand loads. | 4000-6000 MPa |
Fracture Toughness | Resistance to crack propagation. | 8-12 MPa√m |
Thermal Conductivity | Ability to conduct heat. | 80-120 W/m·K |
Melting Point | Temperature at which material melts. | 2500-3000°C |
Young’s Modulus | Measure of stiffness. | 550-700 GPa |
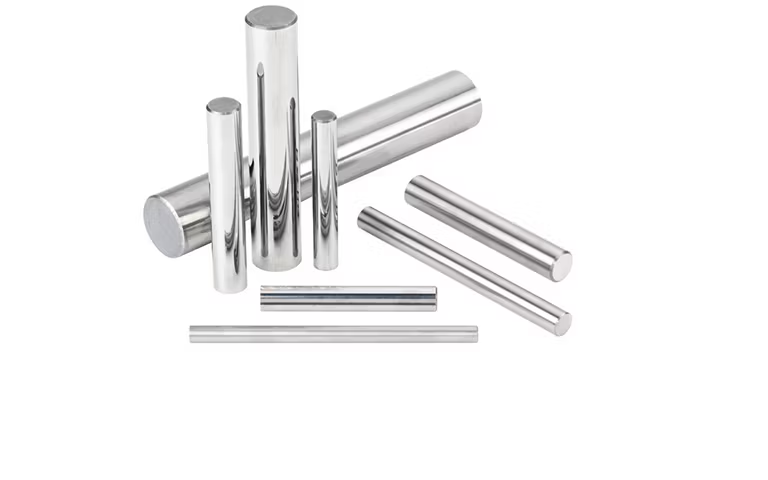
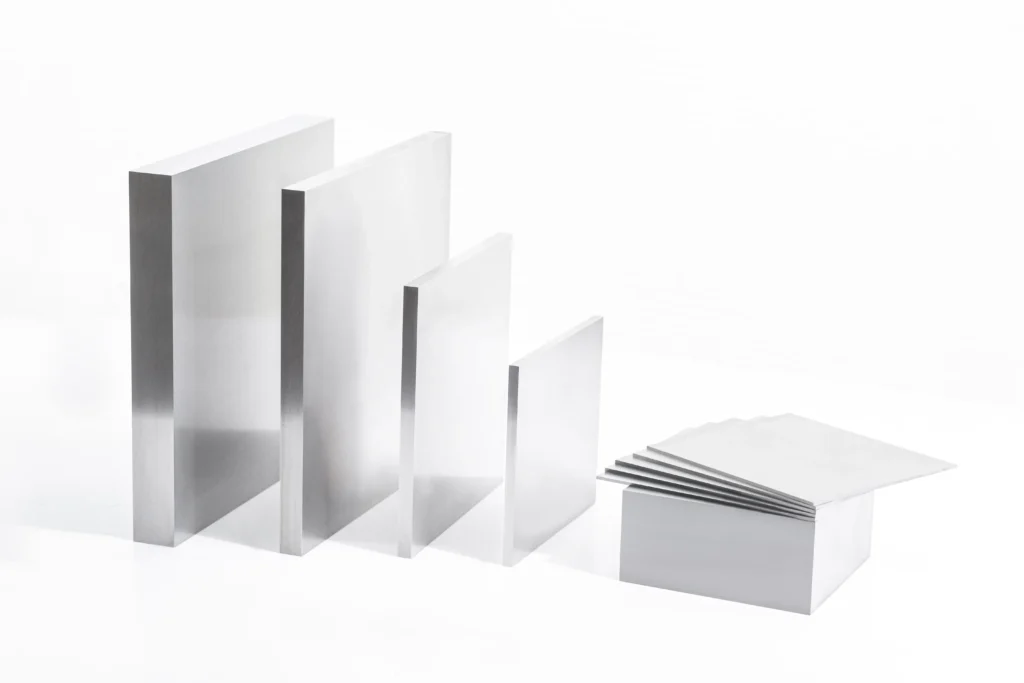
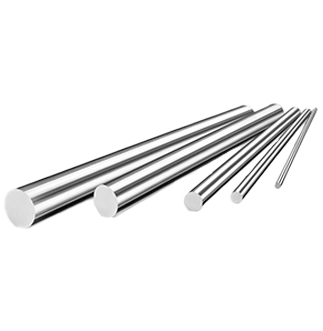
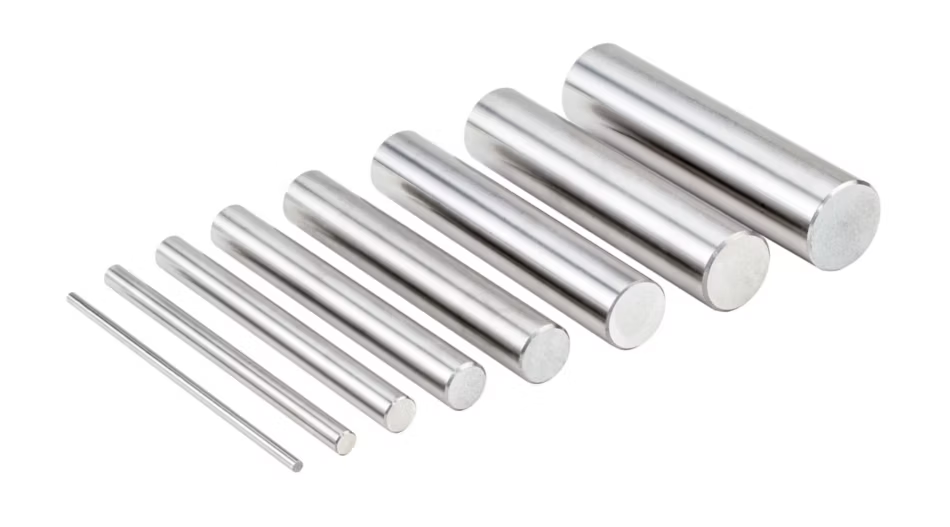
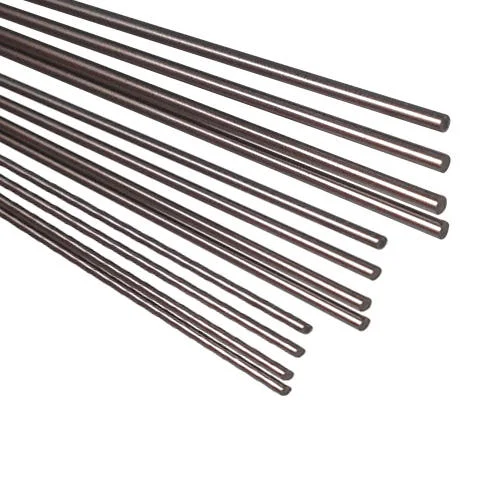
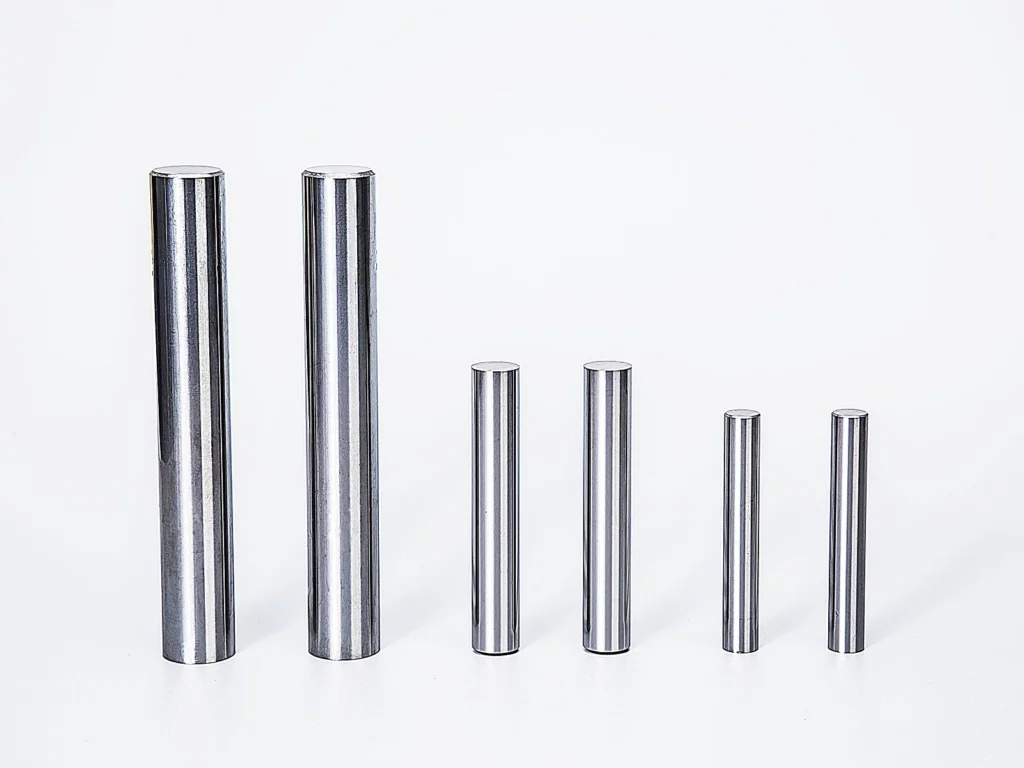
Composition, Properties, and Characteristics
Each type of carbide blank has a unique composition and set of properties. The table below details these aspects:
Type of Carbide Blank | Composition | Properties | Characteristics |
---|---|---|---|
Tungsten Carbide | WC + Co binder | High hardness, wear resistance | Ideal for cutting tools |
Cobalt-Carbide | Co + WC | Toughness, strength | Used in mining tools |
Titanium Carbide | TiC + Ni binder | Thermal stability, hardness | Aerospace applications |
Tantalum Carbide | TaC + Co binder | High melting point, hardness | High-temperature tools |
Niobium Carbide | NbC + Ni binder | Corrosion resistance, hardness | Chemical industry tools |
Chromium Carbide | Cr3C2 + NiCr binder | Hardness, corrosion resistance | Coatings and wear parts |
Vanadium Carbide | VC + Fe binder | Wear resistance, toughness | Tool steels |
Molybdenum Carbide | Mo2C + Ni binder | Toughness, hardness | Electronics components |
Zirconium Carbide | ZrC + NiCr binder | Thermal shock resistance, hardness | Nuclear applications |
Hafnium Carbide | HfC + Co binder | Highest melting point, hardness | Extreme environment tools |
Hardness, Strength, and Wear Resistance
The performance of carbide blanks depends heavily on their hardness, strength, and wear resistance. The table below compares these properties:
Type of Carbide Blank | Hardness (HV) | Compressive Strength (MPa) | Wear Resistance |
---|---|---|---|
Tungsten Carbide | 1600-2000 | 5000-6000 | Excellent |
Cobalt-Carbide | 1500-1800 | 4000-5500 | Good |
Titanium Carbide | 1800-2200 | 5000-6000 | Excellent |
Tantalum Carbide | 1700-2100 | 4500-6000 | Very Good |
Niobium Carbide | 1600-1900 | 4200-5800 | Good |
Chromium Carbide | 1800-2200 | 4600-6000 | Excellent |
Vanadium Carbide | 1700-2000 | 4500-5800 | Very Good |
Molybdenum Carbide | 1600-2000 | 4300-5700 | Good |
Zirconium Carbide | 1700-2100 | 4400-5900 | Very Good |
Hafnium Carbide | 2000-2300 | 4800-6200 | Excellent |
Specifications, Sizes, Shapes, and Standards
Carbide blanks are available in various specifications, sizes, shapes, and standards. Here is a detailed table:
Specification | Description | Sizes | Shapes | Standards |
---|---|---|---|---|
ISO | International standards for dimensions and properties. | 5-100 mm | Round, square, rectangular | ISO 9001 |
ANSI | American standards for quality and consistency. | 5-100 mm | Round, square, rectangular | ANSI B94.27M |
DIN | German standards for precision and tolerance. | 5-100 mm | Round, square, rectangular | DIN 4964 |
JIS | Japanese standards for high-quality carbide products. | 5-100 mm | Round, square, rectangular | JIS B4053 |
GB | Chinese standards for carbide tooling. | 5-100 mm | Round, square, rectangular | GB/T 4354 |
Custom | Tailored specifications based on customer requirements. | Customizable | Various | Customer-specific |
Suppliers and Pricing Details
Finding the right supplier for carbide blanks is crucial for ensuring quality and reliability. Here’s a look at some prominent suppliers and general pricing details:
Supplier | Description | Pricing |
---|---|---|
Supplier A | Global supplier with ISO-certified products. | $50-100 per kg |
Supplier B | Specializes in high-performance carbide blanks. | $80-120 per kg |
Supplier C | Offers customized solutions and bulk discounts. | $60-90 per kg |
Supplier D | Known for competitive pricing and quick delivery. | $70-110 per kg |
Selecting the Right Carbide Blank
Choosing the appropriate carbide blank involves considering several factors such as application, material properties, and budget. Here are some tips to guide your selection:
- Identify Your Application Needs: Determine the specific requirements for hardness, wear resistance, and thermal stability based on your application.
- Consider Material Properties: Compare the properties of different carbide blanks to match them with your operational demands.
- Evaluate Supplier Capabilities: Assess suppliers based on their reputation, certifications, and ability to meet your volume and quality requirements.
- Budget and Cost Analysis: Balance performance requirements with budget constraints to optimize cost-effectiveness.
Advantages and Limitations of Carbide Blanks
Understanding the pros and cons of carbide blanks helps in making informed decisions. Here’s a comparative view:
Aspect | Advantages | Limitations |
---|---|---|
Strength | High hardness and strength for durable tools. | Brittle nature requires careful handling. |
Wear Resistance | Excellent wear resistance extends tool life. | Higher cost compared to conventional tool materials. |
Versatility | Suitable for a wide range of applications and environments. | Initial machining complexity due to hardness. |
Temperature Stability | Maintains performance at high temperatures. | Limited impact resistance in some applications. |
Customization | Can be tailored to specific application needs. | Longer lead times for customized orders. |
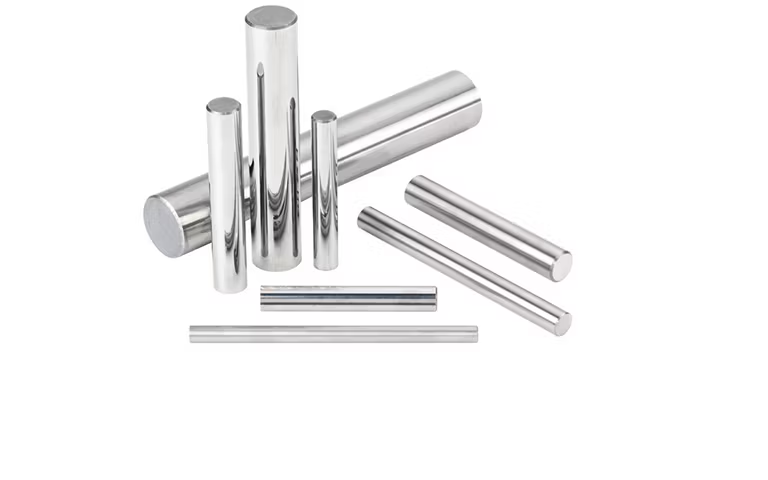
FAQ
Here are some common questions about carbide blanks:
Question | Answer |
---|---|
What are carbide blanks used for? | Carbide blanks are used primarily in cutting tools, wear-resistant parts, and components requiring high hardness and wear resistance. |
How do I choose the right carbide blank? | Consider your application needs, material properties like hardness and wear resistance, supplier capabilities, and budget constraints. |
Are carbide blanks expensive? | Carbide blanks can be more expensive than traditional tool materials due to their superior properties and manufacturing process. |
What are the advantages of using carbide blanks over steel? | Carbide blanks offer higher hardness, wear resistance, and temperature stability compared to steel, making them ideal for demanding applications. |
How are carbide blanks manufactured? | Carbide blanks are typically manufactured through powder metallurgy processes where carbide powders are mixed with binders, compacted, and sintered at high temperatures. |
This comprehensive guide provides a detailed overview of carbide blanks, from their composition and properties to practical applications and purchasing considerations. Whether you’re a manufacturer looking to enhance tool performance or a researcher exploring advanced materials, understanding the nuances of carbide blanks is essential for making informed decisions and achieving optimal results in industrial applications.