Carbide blanks are essential components in various industrial applications, including cutting tools, wear parts, and mining tools. In this guide, we’ll delve into the world of carbide blank manufacturers, providing detailed insights into their products, applications, and more.
Overview
Carbide blanks are typically composed of tungsten carbide, cobalt, and other metallic powders, which are pressed and sintered into specific shapes and sizes. These blanks are then further processed into tools or components used across different industries. This guide aims to provide an in-depth look at carbide blanks, their manufacturers, applications, and selection criteria.
What Are Carbide Blanks?
Carbide blanks are pre-formed shapes made from carbide materials, primarily tungsten carbide. These blanks are used as the starting material for manufacturing various industrial tools and components. They offer excellent hardness, wear resistance, and toughness, making them ideal for demanding applications.
Key Features of Carbide Blanks
- Hardness: Exceptional hardness ensures longer tool life.
- Wear Resistance: High wear resistance for prolonged usage.
- Toughness: Capable of withstanding high stress and impact.
- Precision: Manufactured to precise dimensions for accurate tool making.
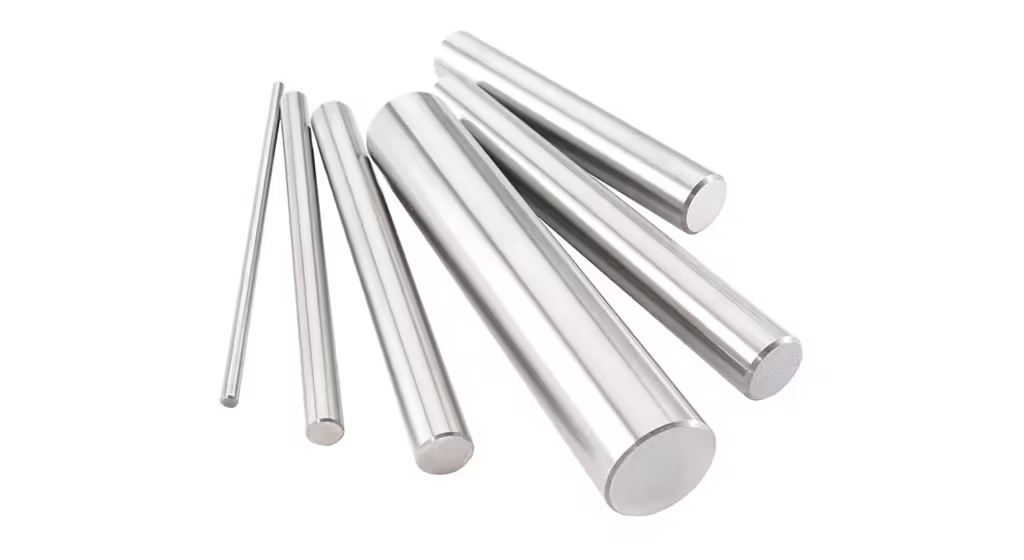
Types of Carbide Blanks
Carbide blanks come in various types, each designed for specific applications. Here’s a detailed look at some common types:
Type of Carbide Blank | Description |
---|---|
Rod Blanks | Used in the production of end mills, drills, and other rotary tools. |
Rectangular Blanks | Commonly used for manufacturing cutting tools like inserts and blades. |
Preformed Blanks | Custom shapes pre-formed for specific applications, reducing machining time. |
Spherical Blanks | Used in the production of balls for ball bearings and other spherical components. |
Wear Parts Blanks | Blanks designed for wear-resistant parts in various machinery. |
Mining Tool Blanks | Used in the production of mining and drilling tools. |
Nozzle Blanks | Blanks for manufacturing nozzles used in high-pressure applications. |
Grinding Media Blanks | Used in the production of grinding balls for mills and other grinding applications. |
Customized Blanks | Tailored to specific customer requirements for unique applications. |
Cutting Tool Blanks | Specifically designed for various cutting tools like reamers, cutters, and saw blades. |
Applications of Carbide Blanks
Carbide blanks are used in numerous applications across different industries. Here’s a table highlighting their primary uses:
Application | Description |
---|---|
Cutting Tools | Production of end mills, drills, inserts, and other cutting tools. |
Wear Parts | Manufacturing of components exposed to high wear and tear. |
Mining and Drilling | Tools for mining, drilling, and tunneling operations. |
Automotive | Engine components, fuel injector parts, and wear-resistant parts. |
Aerospace | Components for aircraft engines and structural parts. |
Medical Devices | Surgical instruments and wear-resistant medical tools. |
Oil and Gas | Tools and components used in exploration and extraction operations. |
Precision Bearings | Spherical blanks for high-precision ball bearings. |
Abrasives and Grinding | Grinding media for mills and abrasives for various applications. |
General Machining | General-purpose tools and components for machining operations. |
Material Properties of Carbide Blanks
Carbide blanks are known for their outstanding material properties. Here’s a breakdown of their key characteristics:
Property | Description |
---|---|
Hardness | Extremely high hardness, typically between 85-95 HRA. |
Wear Resistance | High resistance to abrasion and wear. |
Toughness | Good toughness to withstand impact and shock. |
Thermal Conductivity | Excellent thermal conductivity, reducing heat buildup. |
Corrosion Resistance | Resistant to corrosion, making them suitable for harsh environments. |
Density | High density, typically between 14-15 g/cm³. |
Compressive Strength | Very high compressive strength, ideal for high-stress applications. |
Fracture Toughness | Good fracture toughness, preventing sudden breakage. |
Magnetic Properties | Depending on composition, can be magnetic or non-magnetic. |
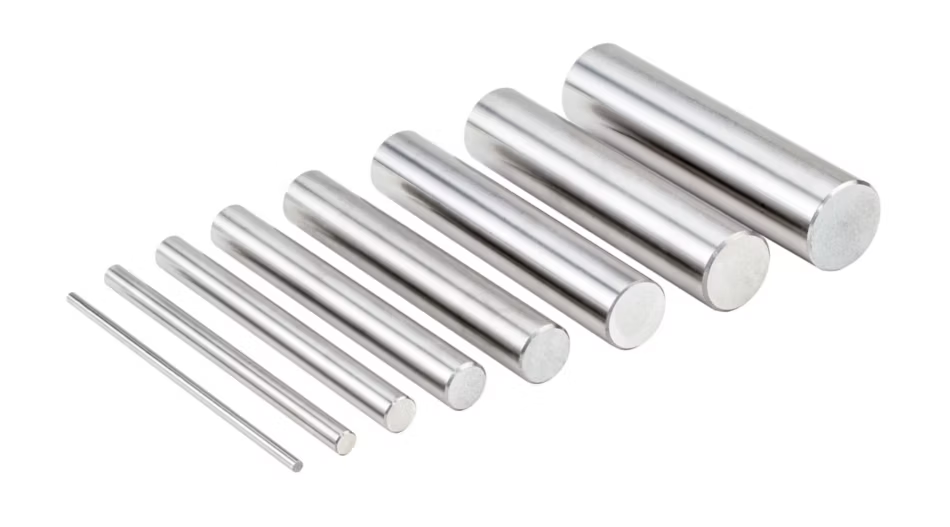
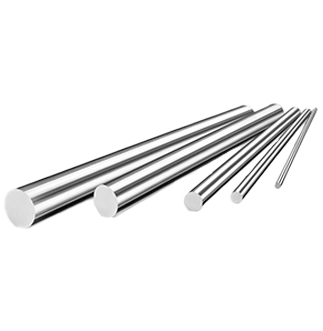
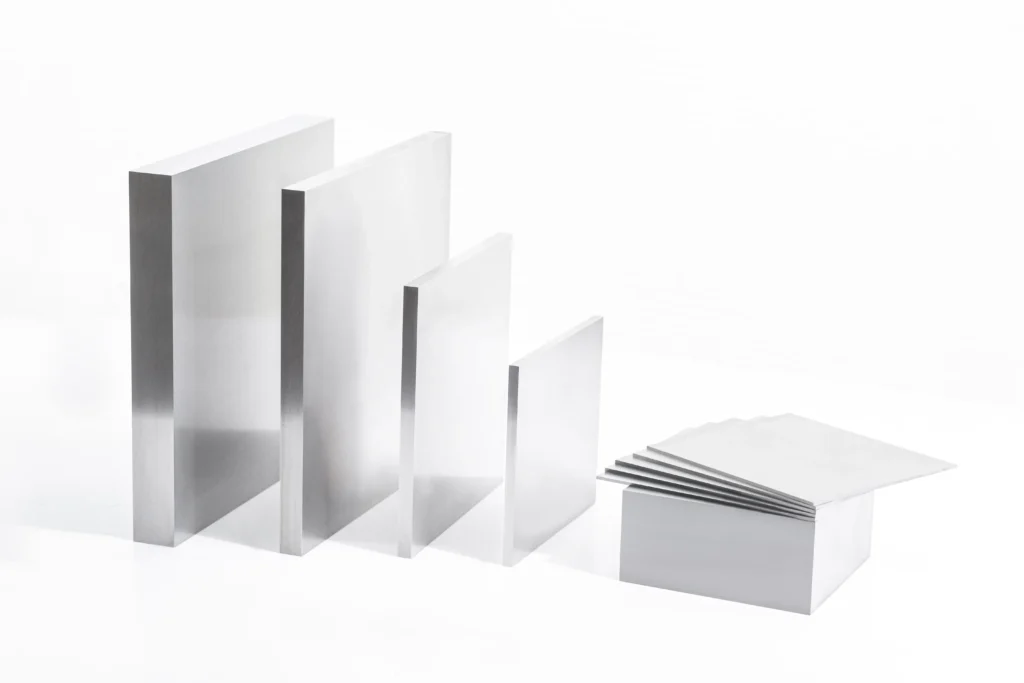
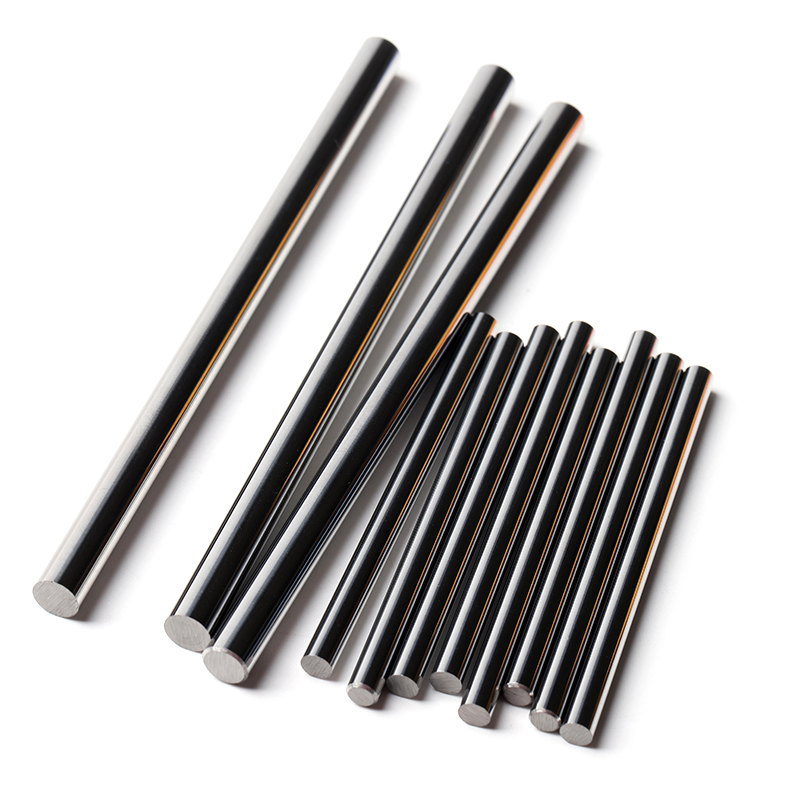
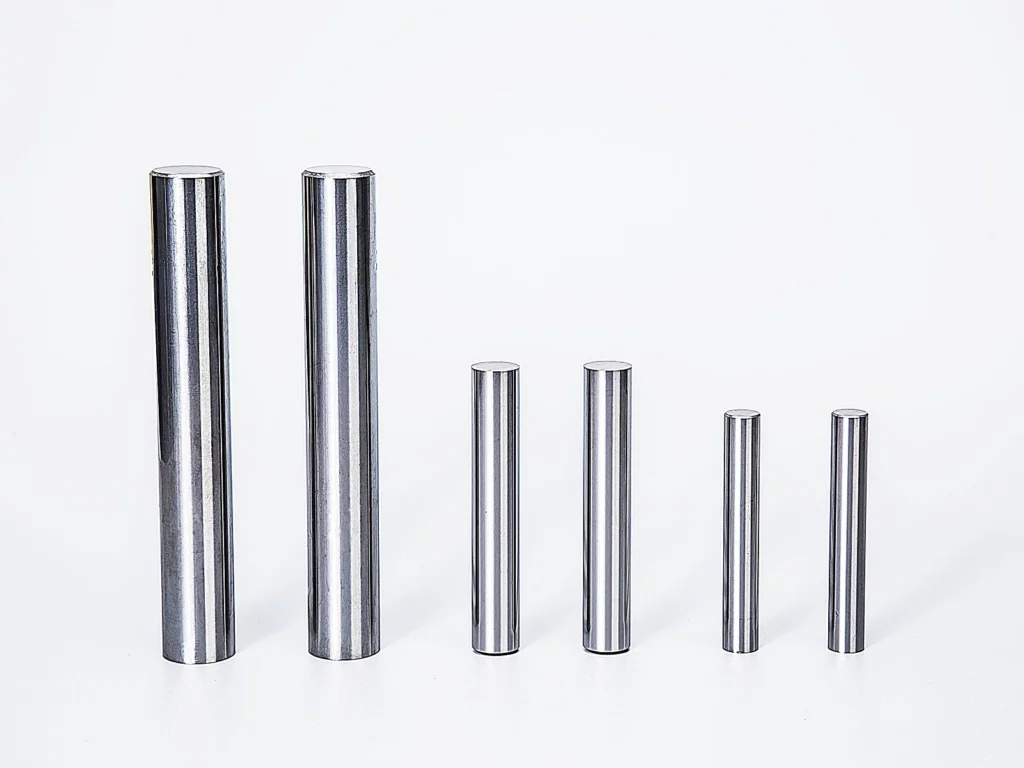
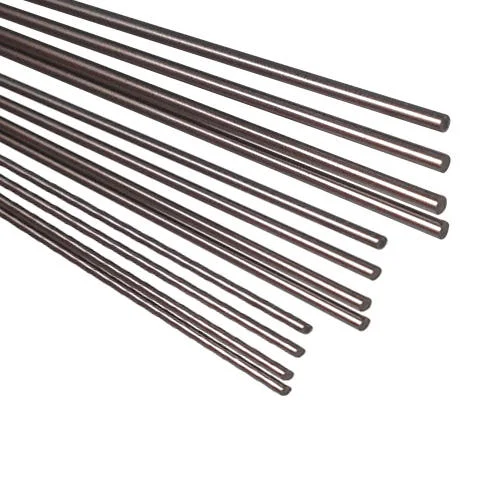
Composition, Properties, and Characteristics
Carbide blanks are composed of various metallic powders, each contributing to their overall properties. Here’s a detailed table:
Composition | Properties | Characteristics |
---|---|---|
Tungsten Carbide (WC) | Hardness, Wear Resistance | Main component, provides high hardness and wear resistance. |
Cobalt (Co) | Toughness, Binder | Acts as a binder, providing toughness and impact resistance. |
Nickel (Ni) | Corrosion Resistance | Sometimes used as a binder for improved corrosion resistance. |
Chromium Carbide (CrC) | Wear Resistance | Enhances wear resistance in specific applications. |
Tantalum Carbide (TaC) | High Temperature Stability | Provides stability at high temperatures. |
Titanium Carbide (TiC) | Wear Resistance, Hardness | Adds to the hardness and wear resistance. |
Vanadium Carbide (VC) | Grain Growth Inhibitor | Controls grain size during sintering, enhancing mechanical properties. |
Hardness, Strength, and Wear Resistance
The mechanical properties of carbide blanks make them suitable for various demanding applications:
Property | Description |
---|---|
Hardness (HRA) | 85-95 |
Compressive Strength | 3000-7000 MPa |
Wear Resistance | Extremely high, varies based on composition and application. |
Specifications, Sizes, Shapes, and Standards
Carbide blanks come in various specifications to meet different industry standards and requirements:
Specification | Description |
---|---|
Sizes | Available in various sizes, from small rods to large blocks. |
Shapes | Rods, blocks, spheres, custom shapes. |
Standards | ISO, ANSI, DIN, and other international standards. |
Tolerances | Manufactured to tight tolerances for precision applications. |
Suppliers and Pricing Details
Here are some notable suppliers of carbide blanks and their pricing details:
Supplier | Location | Products | Pricing (Approx.) |
---|---|---|---|
Kennametal | USA | Rods, blocks, wear parts | $10 – $100 per piece |
Sandvik | Sweden | Cutting tool blanks, mining tool blanks | $15 – $120 per piece |
CeramTec | Germany | Custom carbide blanks | $20 – $150 per piece |
Sumitomo Electric | Japan | Wear-resistant parts, cutting tool blanks | $25 – $200 per piece |
Guhring | Germany | Rod blanks, preformed blanks | $12 – $110 per piece |
Seco Tools | Sweden | Rectangular blanks, wear parts | $18 – $130 per piece |
Carbide Depot | USA | Various carbide blanks | $8 – $90 per piece |
Ceratizit | Luxembourg | High-performance carbide blanks | $30 – $250 per piece |
Zhuzhou Cemented Carbide | China | Standard and custom blanks | $5 – $80 per piece |
Hyperion Materials & Technologies | USA | Cutting and wear-resistant blanks | $22 – $160 per piece |
Selecting the Right Carbide Blank
Choosing the right carbide blank involves several factors. Here’s a guide to help you make the right decision:
Criteria | Considerations |
---|---|
Application | Identify the specific application to choose the right type of blank. |
Material Properties | Consider hardness, toughness, and wear resistance based on the application. |
Size and Shape | Ensure the blank size and shape match your requirements. |
Tolerances | Check for the required tolerances for precision applications. |
Supplier Reputation | Choose reputable suppliers known for high-quality products. |
Cost | Balance cost with performance requirements. |
Customization | Consider if custom shapes or sizes are needed for your application. |
Standards Compliance | Ensure the blanks meet relevant industry standards |
Comparing Advantages and Limitations
Understanding the pros and cons of carbide blanks can help in making an informed decision:
Aspect | Advantages | Limitations |
---|---|---|
Hardness | Very high hardness | Can be brittle in some applications |
Wear Resistance | Exceptional wear resistance | May require specialized machining |
Toughness | Good toughness | Higher cost compared to other materials |
Thermal Conductivity | Excellent heat dissipation | Requires precise manufacturing processes |
Corrosion Resistance | Resistant to corrosion | Not all carbide blanks offer the same level |
Customizability | Can be tailored to specific needs | Custom shapes may increase lead time |
Famous Carbide Blank Manufacturers
Several manufacturers stand out in the carbide blank industry. Here are some of the most renowned:
- Kennametal
- Known for high-quality carbide products, including rods, blocks, and wear parts.
- Sandvik
- Offers a wide range of carbide blanks, including cutting tool and mining tool blanks.
- CeramTec
- Specializes in custom carbide blanks for various industrial applications.
- Sumitomo Electric
- Provides a range of wear-resistant parts and cutting tool blanks.
- Guhring
- Known for precision rod blanks and preformed blanks.
- Seco Tools
- Offers rectangular blanks and wear parts for different industries.
- Carbide Depot
- Supplies various standard and custom carbide blanks.
- Ceratizit
- Focuses on high-performance carbide blanks for demanding applications.
- Zhuzhou Cemented Carbide
- A major supplier of standard and custom carbide blanks.
- Hyperion Materials & Technologies
- Known for high-quality cutting and wear-resistant carbide blanks.
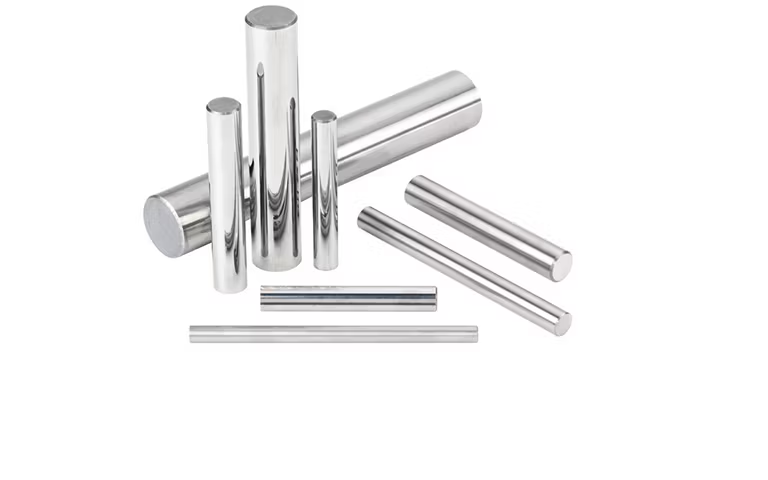
FAQs
Question | Answer |
---|---|
What are carbide blanks used for? | Carbide blanks are used in the production of cutting tools, wear parts, mining tools, and more. |
How are carbide blanks made? | They are made by pressing and sintering metallic powders, primarily tungsten carbide and cobalt. |
What are the advantages of using carbide blanks? | High hardness, excellent wear resistance, and good toughness. |
Can carbide blanks be customized? | Yes, they can be tailored to specific shapes and sizes based on application requirements. |
Which industries use carbide blanks? | Industries such as automotive, aerospace, medical devices, mining, and general machining. |
What factors should be considered when selecting carbide blanks? | Application, material properties, size, shape, tolerances, and supplier reputation. |
Are carbide blanks expensive? | They can be more expensive than other materials due to their superior properties. |
Do carbide blanks meet industry standards? | Yes, reputable manufacturers ensure compliance with relevant industry standards. |
How are carbide blanks processed into tools? | They are further machined, ground, and polished to create the final tool or component. |
What is the typical hardness of carbide blanks? | Typically between 85-95 HRA. |
Conclusion
Carbide blanks play a crucial role in various industrial applications, offering unmatched hardness, wear resistance, and toughness. Understanding the types, applications, material properties, and selection criteria is essential for choosing the right carbide blank for your needs. With this comprehensive guide, you now have the knowledge to make an informed decision and explore the world of carbide blanks with confidence.