Overview of Carbide Blanks
Carbide blanks, also known as tungsten carbide blanks, are foundational materials used in various manufacturing processes. These materials are crafted from carbide powders and are known for their extreme hardness, wear resistance, and ability to maintain a cutting edge longer than most other materials. They play a crucial role in industries ranging from automotive to aerospace, where precision and durability are paramount.
In this guide, we’ll delve into the intricate world of carbide blanks, exploring everything from their composition to their applications. We’ll break down the different types, explain the material properties, and help you choose the right carbide blank for your needs.
Understanding Carbide Blanks
Carbide blanks are produced by combining tungsten carbide powder with a metallic binder, often cobalt. This mixture is then pressed and sintered to create a solid, durable blank that can be further processed into cutting tools, wear parts, and other industrial components.
But what makes carbide blanks so special? It’s their unique combination of hardness, toughness, and wear resistance. This trio of properties allows carbide blanks to withstand the most demanding conditions, making them the material of choice for high-performance applications.
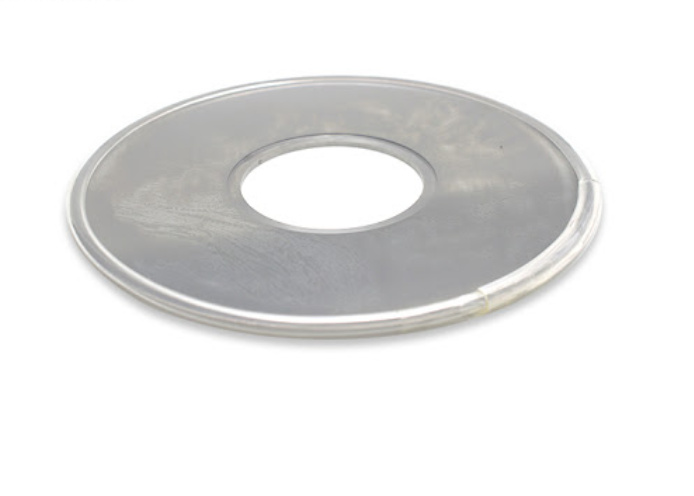
Types of Carbide Blanks
Carbide blanks come in various types, each tailored to specific applications. The differences between these types often lie in the composition of the carbide powder and the binder, resulting in distinct properties.
Type of Carbide Blank | Description |
---|---|
Solid Carbide Blanks | Made entirely of carbide, these blanks offer the highest wear resistance and are often used in cutting tools. |
Carbide-Tipped Blanks | Featuring a carbide tip bonded to a softer substrate, these blanks provide a balance between toughness and wear resistance. |
Cobalt-Bonded Blanks | Using cobalt as a binder, these blanks are known for their toughness and are commonly used in applications requiring high impact resistance. |
Nickel-Bonded Blanks | Nickel provides better corrosion resistance, making these blanks suitable for harsh environments. |
Custom Carbide Blanks | Tailored to specific needs, these blanks can have varying compositions to optimize performance for unique applications. |
Applications of Carbide Blanks
Carbide blanks are versatile and find applications across a wide range of industries. Whether it’s in machining, drilling, or even medical devices, the use of carbide blanks is widespread.
Application | Description |
---|---|
Cutting Tools | Carbide blanks are often used to create precision cutting tools for milling, drilling, and turning. |
Wear Parts | Industries use these blanks to manufacture wear-resistant parts that can withstand high abrasion. |
Aerospace Components | The high strength and durability of carbide blanks make them ideal for critical aerospace parts. |
Automotive Industry | Used in the production of high-performance engine components and other critical automotive parts. |
Mining Tools | Carbide blanks are crucial in creating tools that can withstand the harsh conditions of mining operations. |
Medical Instruments | Due to their precision and durability, carbide blanks are used in various surgical instruments and medical devices. |
Material Properties of Carbide Blanks
The performance of carbide blanks is defined by several key material properties. Understanding these properties is crucial in selecting the right blank for your application.
Property | Description |
---|---|
Hardness | Carbide blanks are extremely hard, typically measuring between 8.5 and 9.5 on the Mohs scale. |
Toughness | Despite their hardness, carbide blanks offer excellent toughness, resisting cracks and fractures. |
Wear Resistance | These blanks are designed to endure high levels of abrasion, extending the life of the tool or part. |
Thermal Conductivity | Carbide blanks have high thermal conductivity, making them suitable for high-temperature applications. |
Corrosion Resistance | Depending on the binder, carbide blanks can offer significant resistance to corrosion. |

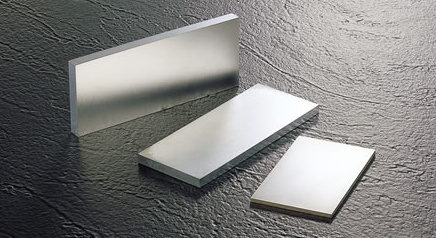
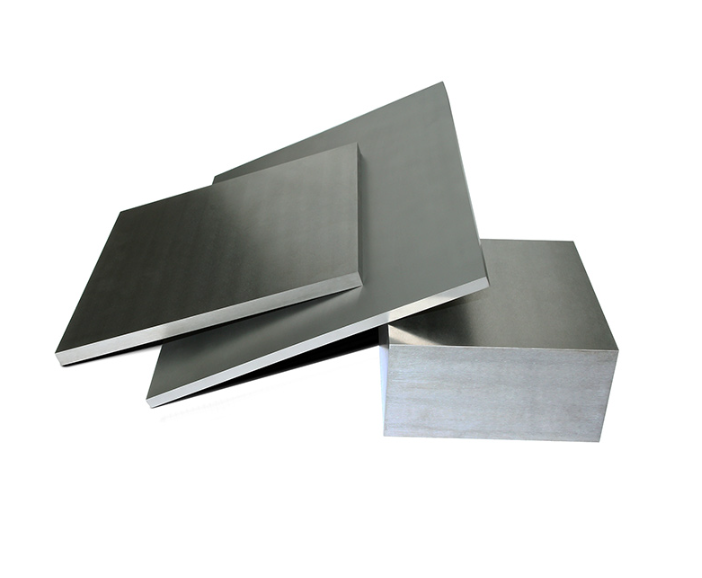
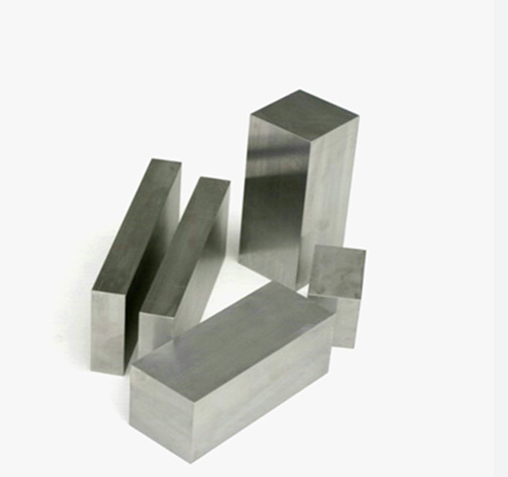
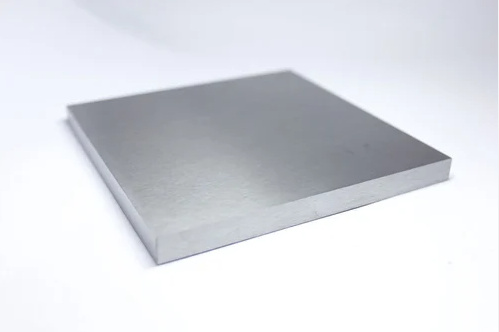
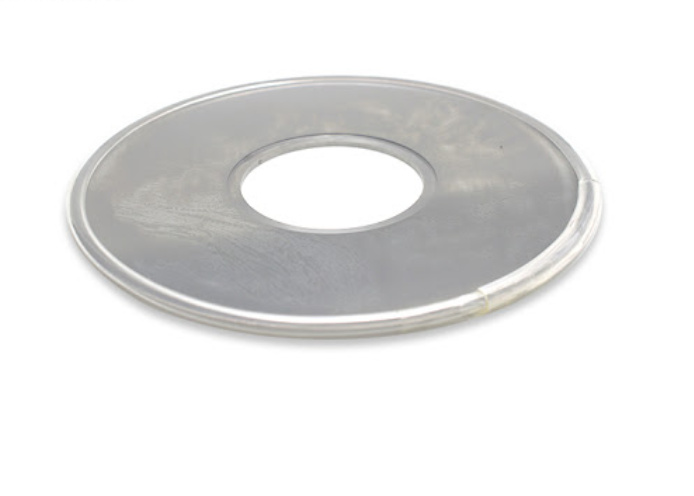
Composition and Characteristics of Carbide Blanks
The composition of carbide blanks varies depending on the intended application. However, tungsten carbide is the primary component, often combined with a metallic binder.
Component | Percentage | Function |
---|---|---|
Tungsten Carbide | 70-97% | Provides the primary hardness and wear resistance. |
Cobalt/Nickel Binder | 3-30% | Binds the carbide particles together, adding toughness. |
Additives | <1% | Improve specific properties like corrosion resistance or thermal stability. |
Hardness, Strength, and Wear Resistance of Carbide Blanks
The interplay between hardness, strength, and wear resistance defines the performance of carbide blanks. Understanding these metrics can help you choose the best blank for your application.
Metric | Measurement | Description |
---|---|---|
Hardness | 1800-2400 HV | Measured on the Vickers scale, this indicates the material’s resistance to indentation. |
Transverse Rupture Strength (TRS) | 300,000-550,000 psi | A measure of the material’s ability to resist breaking under stress. |
Wear Resistance | 10-15 mm³/hr | Assesses the material’s resistance to wear under specific conditions. |
Specifications, Sizes, Shapes, and Standards of Carbide Blanks
Carbide blanks are available in various sizes and shapes, and it’s essential to choose the right specification for your needs.
Specification | Options Available |
---|---|
Sizes | Ranges from micro-sizes for precision tools to larger blanks for industrial applications. |
Shapes | Round, square, rectangular, and custom shapes to suit different tools and parts. |
Standards | ISO, ANSI, DIN standards ensure compatibility and performance in various applications. |
Suppliers and Pricing Details of Carbide Blanks
The market for carbide blanks is vast, with numerous suppliers offering a wide range of products. Pricing can vary depending on the composition, size, and application.
Supplier | Pricing | Description |
---|---|---|
Kennametal | $50 – $500 per blank | A leading supplier known for high-quality carbide blanks. |
Sandvik | $60 – $600 per blank | Offers a wide range of carbide blanks with advanced compositions. |
Ceratizit | $45 – $450 per blank | Known for innovative solutions and custom carbide blanks. |
Sumitomo Electric | $55 – $550 per blank | Specializes in carbide blanks for high-performance cutting tools. |
IMC Group | $40 – $400 per blank | Provides cost-effective carbide blanks for various industrial applications. |
Selecting the Right Carbide Blank
Choosing the right carbide blank can be challenging given the variety of options available. It’s essential to consider your specific needs, including the type of material you’ll be working with, the conditions of use, and your budget.
Criteria | Considerations |
---|---|
Application | Match the blank’s properties (hardness, toughness) to the application’s demands. |
Material Being Worked | Softer materials may not require the hardest blanks, while harder materials demand high wear resistance. |
Budget | Balance cost against the required performance to find the best value. |
Supplier Reputation | Consider suppliers with a proven track record for quality and reliability. |
Comparing Advantages and Limitations of Carbide Blanks
Each type of carbide blank has its advantages and limitations, which should be considered during the selection process.
Type of Carbide Blank | Advantages | Limitations |
---|---|---|
Solid Carbide Blanks | Best wear resistance, long tool life | Higher cost, more brittle than other types |
Carbide-Tipped Blanks | Cost-effective, good balance of toughness | Limited wear resistance compared to solid blanks |
Cobalt-Bonded Blanks | Excellent toughness, good for impact loads | Lower wear resistance than solid carbide |
Nickel-Bonded Blanks | Better corrosion resistance | Typically more expensive, slightly less tough than cobalt-bonded |
How to Select the Right Carbide Blank for Your Needs
When selecting a carbide blank, it’s essential to consider both the application and the material being processed. For instance, if you’re working with hard materials, you might prioritize wear resistance and hardness. Conversely, if you’re dealing with impact loads, toughness might be more critical.
Let’s break this down further:
- Assess Your Application: What are you using the carbide blank for? Cutting tools, wear parts, or another application? The end use dictates the type of carbide blank you’ll need.
- Consider Material Compatibility: What material are you processing? For softer materials, you might not need the hardest carbide blank. However, for harder materials, a high hardness and wear resistance are essential.
- Budget Considerations: High-performance carbide blanks can be expensive. Determine your budget and find the best blank within that range that meets your performance needs.
- Evaluate Supplier Reputation: Not all carbide blanks are created equal. Research suppliers and choose one with a strong reputation for quality and reliability.
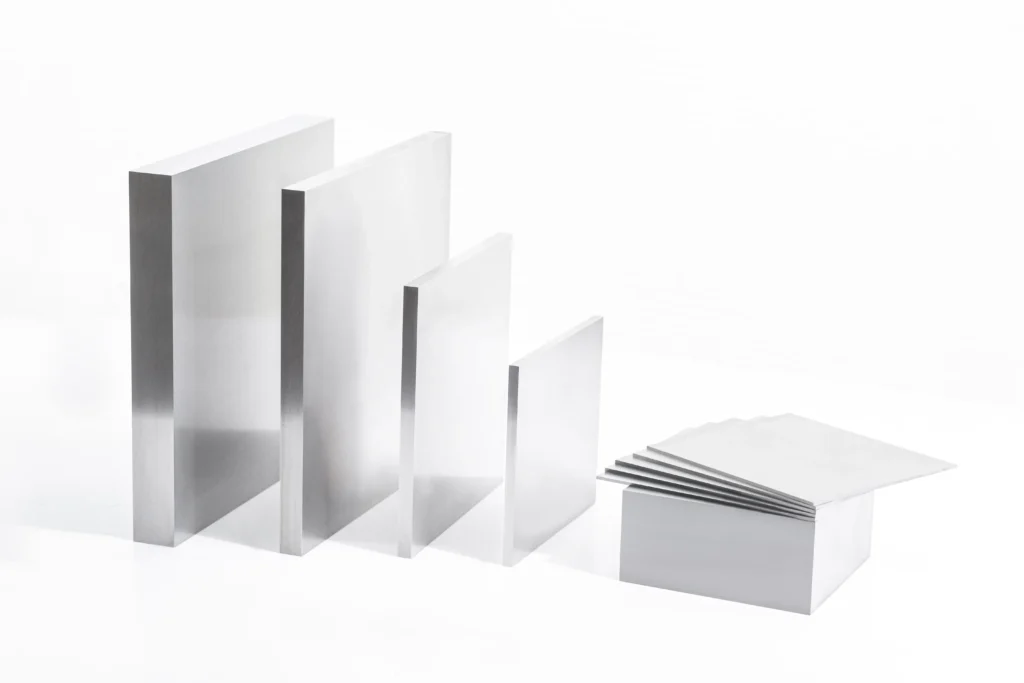
FAQs
Question | Answer |
---|---|
What are carbide blanks used for? | Carbide blanks are used to create cutting tools, wear parts, and other industrial components. |
How do I choose the right carbide blank? | Consider your application’s requirements, the material being processed, and your budget. |
What makes carbide blanks so durable? | The combination of tungsten carbide’s hardness and the toughness provided by the binder material. |
Can carbide blanks be customized? | Yes, many suppliers offer custom carbide blanks tailored to specific needs. |
What is the difference between solid carbide and carbide-tipped blanks? | Solid carbide blanks are entirely made of carbide, while carbide-tipped blanks have a carbide tip bonded to a softer substrate. |
Conclusion
Carbide blanks are indispensable in many industries, offering unparalleled hardness, wear resistance, and toughness. Whether you’re in manufacturing, aerospace, automotive, or any other industry requiring high-performance materials, understanding the different types of carbide blanks, their properties, and how to select the right one is crucial.
This guide has provided an in-depth look at everything you need to know about carbide blanks, from their composition and material properties to their applications and how to choose the right one. Armed with this knowledge, you can make informed decisions that will enhance your processes and ensure you get the best performance out of your tools and parts.
Remember, the key to selecting the right carbide blank lies in understanding your application’s specific needs and choosing a blank that offers the right balance of hardness, toughness, and wear resistance. Whether you’re cutting, drilling, or creating wear-resistant parts, there’s a carbide blank out there that’s perfect for the job.