What is Carbide and Why It Excels Under High Pressure?
Carbide is a game-changer when it comes to extreme environments. But what makes it so special? Imagine a material so tough that it can handle insane pressures without breaking a sweat. That’s carbide for you! Essentially, carbide is a composite material made from metal carbides (like tungsten carbide, titanium carbide, or tantalum carbide) bonded with a metallic binder such as cobalt or nickel.
What sets carbide apart is its extreme hardness and ability to maintain structural integrity under high pressure, high temperature, and corrosive conditions. Unlike steel, which deforms under pressure, carbide stands its ground, making it the go-to choice for industries that push materials to their limits.
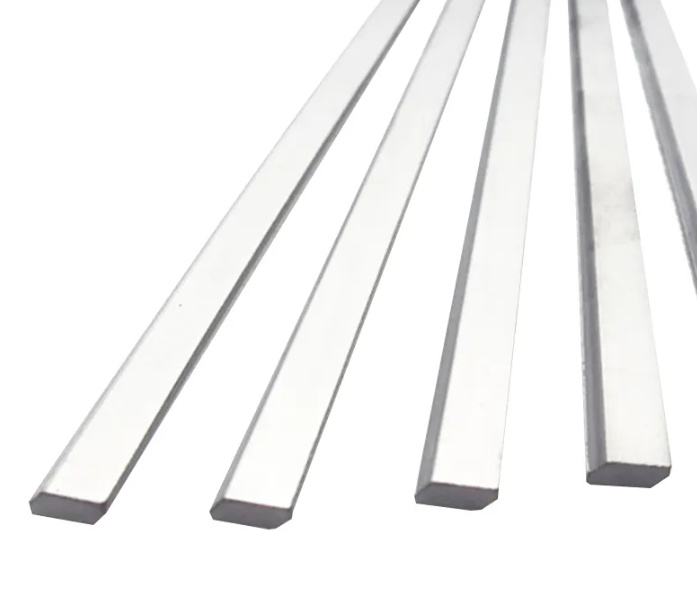
Key Properties of Carbide for Extreme Conditions
When it comes to high-pressure applications, carbide boasts a set of properties that make it indispensable:
- Exceptional Hardness: Carbide is nearly as hard as diamond, ensuring durability under extreme stress.
- High Compressive Strength: Unlike other metals, carbide can withstand massive forces without deforming.
- Superior Wear Resistance: Ideal for cutting, drilling, and high-friction environments.
- Thermal Stability: Withstanding temperatures over 1000°C without losing its properties.
- Corrosion Resistance: Essential for harsh chemical environments, especially in oil and gas drilling.
Applications of Carbide in High-Pressure Environments
Carbide’s robustness makes it the material of choice for industries facing extreme pressures. Let’s dive into some key applications:
Oil and Gas Drilling
- Used in drill bits, nozzles, and wear parts where high-pressure underground conditions demand unyielding strength.
Aerospace Engineering
- Essential for turbine components, cutting tools, and protective coatings in high-pressure jet engines.
Mining and Earth Drilling
- Rock-crushing bits, drill inserts, and cutting edges use carbide to withstand the intense forces of underground excavation.
Manufacturing and Metalworking
- Cutting tools, forming dies, and extrusion dies leverage carbide’s resistance to deformation under high mechanical stress.
Automotive Industry
- High-performance engines rely on valve seats, injectors, and precision machining tools to endure extreme pressure and temperature fluctuations.
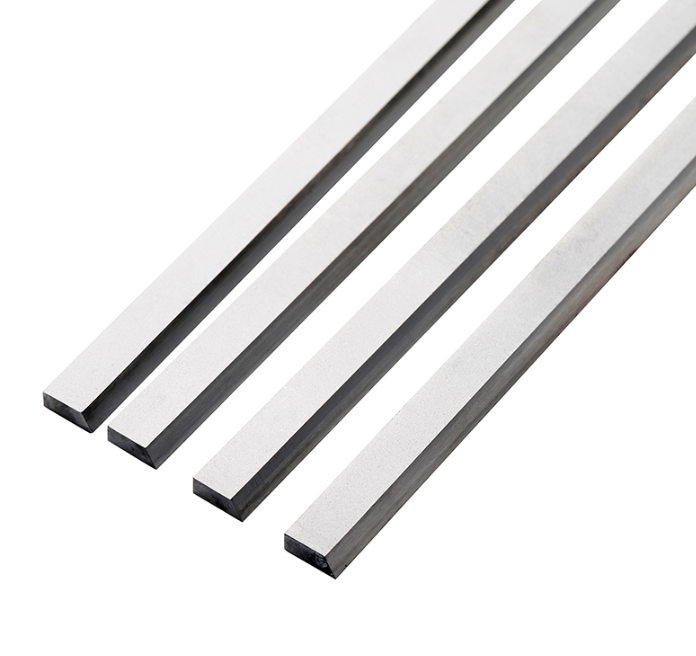
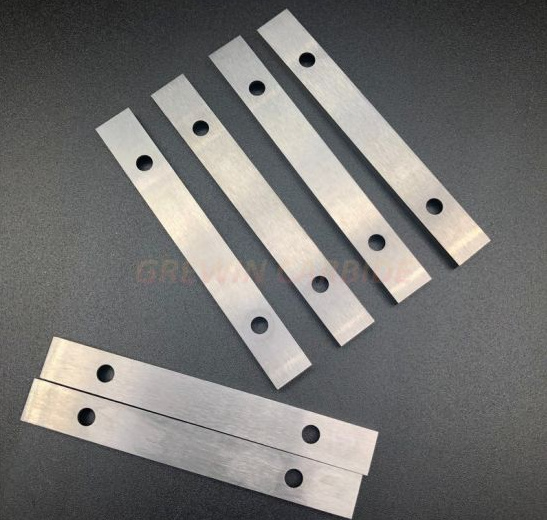
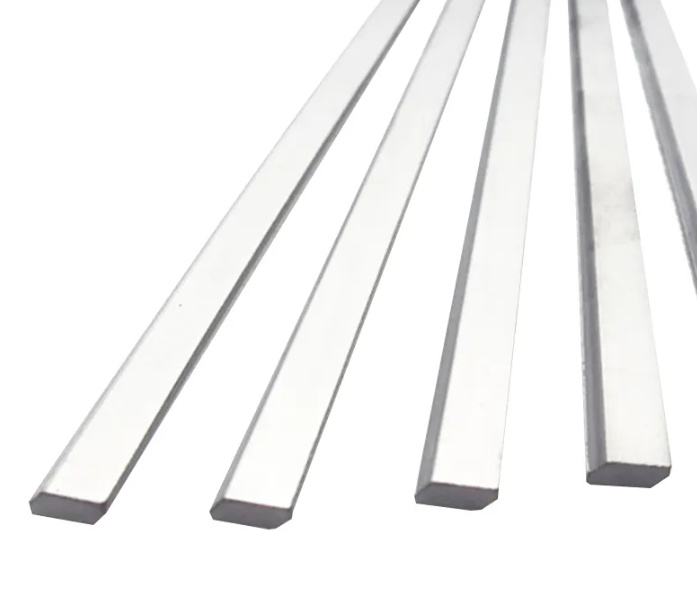
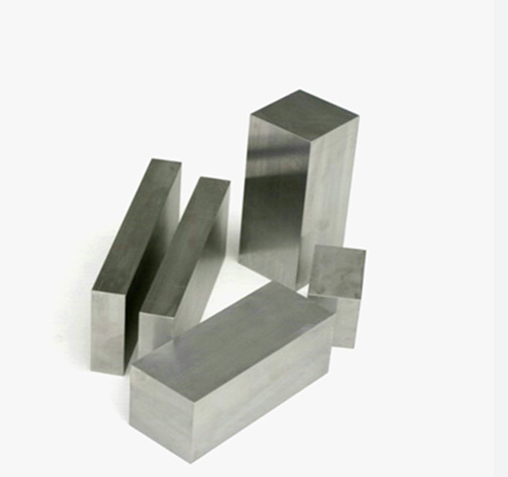
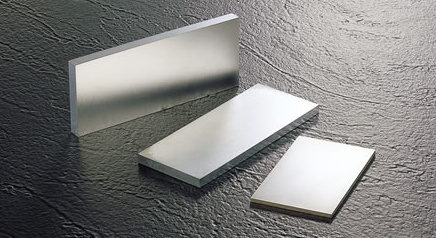
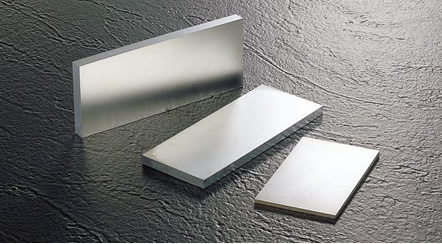
How to Choose the Right Carbide for Your Application
Carbide Type | Hardness (HV) | Compressive Strength (MPa) | Best For |
---|---|---|---|
Tungsten Carbide (WC-Co) | 1400-2000 | 4000-6000 | Drilling, mining, machining |
Titanium Carbide (TiC) | 1800-2800 | 4500-6000 | Cutting tools, aerospace applications |
Tantalum Carbide (TaC) | 2000-3000 | 5000-6500 | High-temperature environments |
Chromium Carbide (CrC) | 1200-2000 | 3000-5000 | Wear-resistant coatings |
Niobium Carbide (NbC) | 1800-2800 | 4500-6000 | Thermal barrier coatings, cutting tools |
Future Trends in High-Pressure Carbide Development
Trend | Description |
---|---|
Nano-structured Carbides | Enhanced strength and wear resistance at a micro-level. |
Hybrid Carbides | Combining multiple carbide types for optimal performance. |
3D-Printed Carbides | Customizable shapes for specialized high-pressure applications. |
Coating Technologies | Advanced coatings to improve corrosion and wear resistance. |
Eco-Friendly Binders | Reducing the use of cobalt and nickel for sustainable production. |
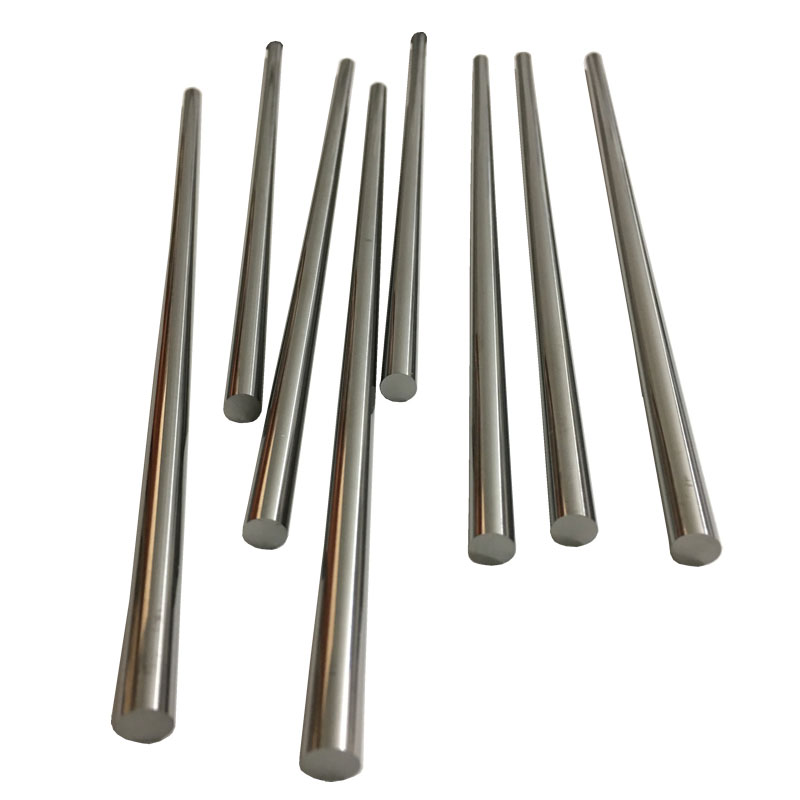
FAQ
Question | Answer |
---|---|
What is the strongest type of carbide? | Tungsten carbide (WC) is widely considered the strongest, offering the best combination of hardness and toughness. |
Can carbide break under pressure? | While carbide is incredibly strong, it is also brittle. If subjected to sudden impact, it can crack. However, in controlled high-pressure environments, it outperforms most metals. |
How does carbide compare to steel? | Carbide is significantly harder and more wear-resistant than steel, but it is also more brittle. This makes it ideal for specific applications like cutting tools and drilling. |
Is carbide expensive? | Yes, carbide tends to be more expensive than steel due to its superior properties. However, its durability often offsets the cost in long-term applications. |
What industries rely on carbide the most? | Aerospace, oil & gas, mining, manufacturing, and automotive industries depend on carbide for its unparalleled strength and durability. |