Carbide recycling is a vital part of the modern material recovery ecosystem, enabling industries to reuse valuable tungsten carbide materials efficiently. But why should we care about recycling carbide? Think of it as giving your tools a second life—the same strength and performance, but with less environmental impact and cost.
Types of Carbide Recycling Processes
Carbide recycling involves several distinct methods, each tailored to specific needs and materials. Here’s a breakdown of the key types:
Type | Description |
---|---|
Direct Recycling | Reclaiming carbide tools by grinding and reshaping for reuse. |
Chemical Recycling | Using chemicals to break down carbide and extract tungsten and other metals. |
Thermal Recycling | Heat treatment to separate carbide components from impurities. |
Physical Separation | Mechanical processes like crushing and sieving to isolate carbide particles. |
Hydrometallurgical Process | Involves acids or alkalis to dissolve and recover tungsten from carbide scrap. |
Sintering Recycling | Melting carbide waste and reshaping it into new products. |
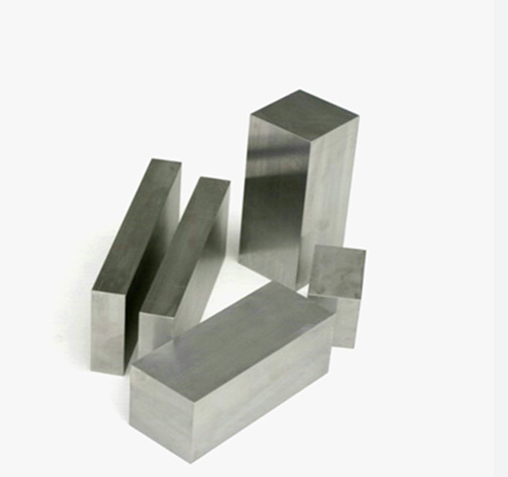
Raw Material and Composition Analysis of Carbide Recycling
Tungsten carbide is the star player in carbide recycling. It’s an alloy made by combining tungsten and carbon, often with cobalt or nickel as a binder. This unique composition provides exceptional hardness, wear resistance, and thermal stability, making it perfect for industrial applications like cutting tools, mining equipment, and wear parts.
Key Raw Materials in Carbide Recycling:
- Tungsten: A rare, heavy metal known for its exceptional hardness and high melting point.
- Cobalt or Nickel: Act as binders, giving the carbide its toughness and structural integrity.
- Reclaimed Scrap: Includes used cutting tools, drill bits, and other carbide-containing components.
Applications of Recycled Carbide
Recycled carbide retains most of its original properties, making it a versatile material for various industries:
Application | Details |
---|---|
Cutting Tools | Reused for manufacturing drills, milling cutters, and saw blades. |
Mining Equipment | Recycled into components like drill tips and wear-resistant plates. |
Industrial Wear Parts | Re-purposed for producing abrasion-resistant parts used in machinery. |
Aerospace Components | Used in high-precision parts where strength and wear resistance are critical. |
3D Printing Powders | Turned into fine powders for additive manufacturing. |
Production Process Flow of Carbide Recycling
The journey of recycling carbide involves several steps that transform used materials into high-performance products:
Step-by-Step Process:
- Collection and Sorting: Scrap carbide is collected from various sources and sorted based on material composition and condition.
- Pre-Treatment: Contaminants like oils and coatings are removed using chemical or thermal methods.
- Crushing and Grinding: Larger pieces of carbide are broken down into smaller particles.
- Chemical Processing: Advanced techniques like acid leaching are used to separate tungsten and cobalt.
- Powder Formation: Recovered metals are processed into fine powders suitable for manufacturing.
- Sintering: Powders are melted and reshaped into new carbide products.
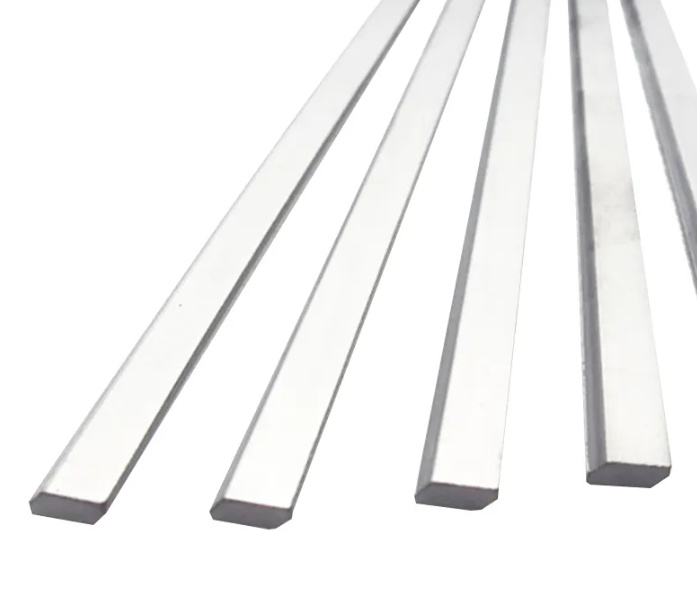
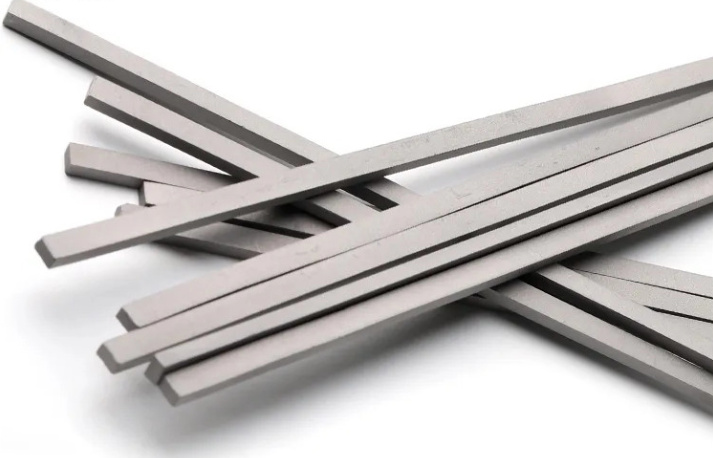
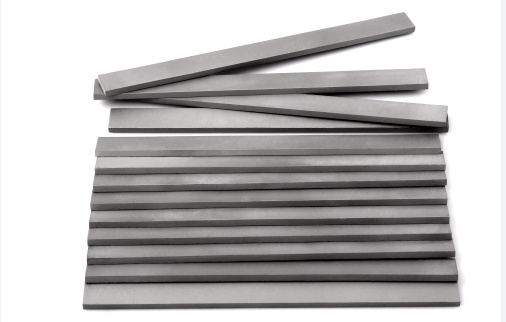
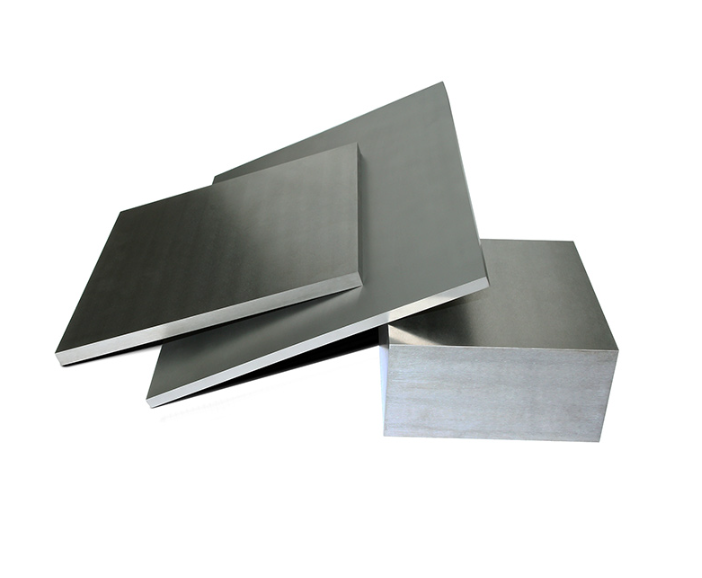
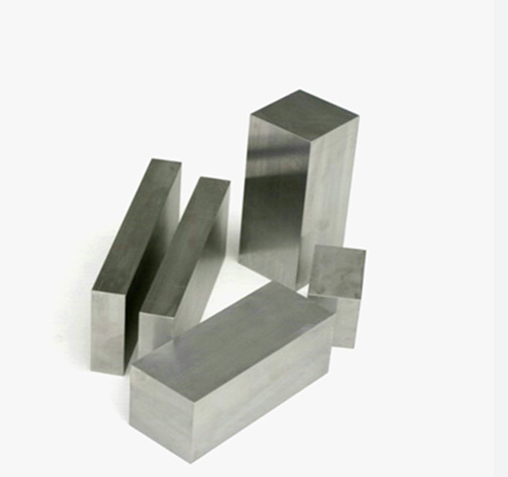
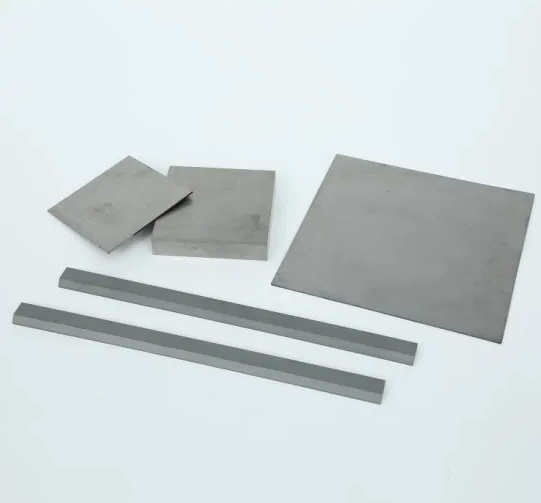
Material Properties of Recycled Carbide
Property | Details |
---|---|
Hardness | Comparable to virgin carbide, ensuring durability in demanding applications. |
Wear Resistance | Retains high resistance to abrasion and erosion. |
Thermal Stability | Excellent performance at elevated temperatures. |
Toughness | Sufficient toughness for industrial use, especially with proper binders. |
Composition, Properties, and Characteristics
Composition | Properties | Characteristics |
---|---|---|
Tungsten (WC) | High hardness and density | Essential for cutting and drilling applications. |
Cobalt (Co) | Acts as a binder for toughness | Increases impact resistance and structural integrity. |
Nickel (Ni) | Alternative binder | Provides corrosion resistance. |
Hardness, Strength, and Wear Resistance
Metric | Recycled Carbide Value | Virgin Carbide Value |
---|---|---|
Hardness (Vickers) | 1500–2000 HV | 1600–2200 HV |
Compressive Strength | 4000 MPa | 4500 MPa |
Wear Resistance | Comparable with proper recycling | Slightly higher for new materials. |
Specifications, Sizes, Shapes, and Standards
Specification | Details |
---|---|
Shapes | Round, square, custom profiles. |
Sizes | From microns (powders) to inches (cutting tools). |
Standards | ISO 513 for tool materials, ASTM B777 for heavy metals. |
Choosing Carbide Recycling Suppliers and Pricing Details
Criteria | Details |
---|---|
Reputation | Look for established suppliers with verified recycling capabilities. |
Customization | Suppliers offering tailored solutions for specific industry needs. |
Cost | Prices range from $10/kg (powder) to $200/kg (finished parts). |
Sustainability | Choose suppliers with eco-friendly processing methods. |
How to Select the Best Carbide Recycling Method
Factor | Considerations |
---|---|
Material Quality | Ensure high recovery rates and minimal contamination. |
Cost Efficiency | Balance recycling costs with material performance. |
Environmental Impact | Opt for methods with reduced chemical waste and energy use. |
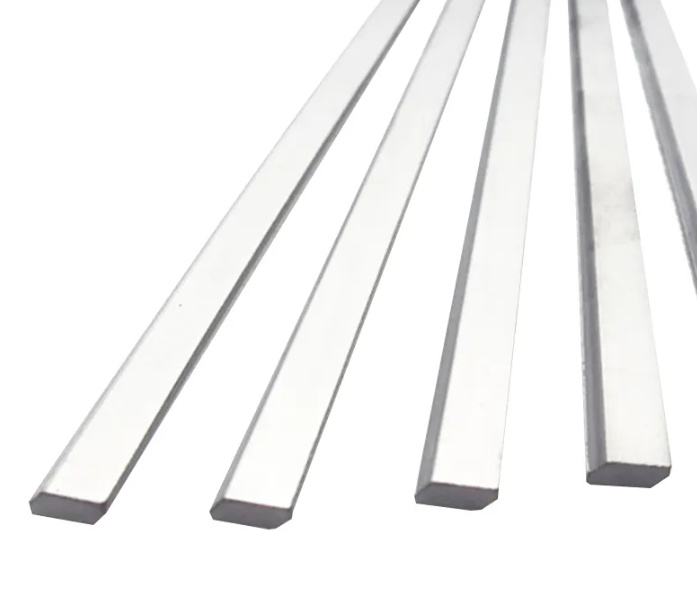
Comparing Advantages and Limitations of Carbide Recycling Methods
Method | Advantages | Limitations |
---|---|---|
Chemical Recycling | High purity recovery, versatile applications. | Requires handling of hazardous chemicals. |
Thermal Recycling | Efficient for bulk materials. | Energy-intensive process. |
Direct Recycling | Cost-effective for reusable tools. | Limited to specific geometries. |
FAQs
Question | Answer |
---|---|
What is tungsten carbide recycling? | It’s the process of recovering tungsten and other materials from scrap. |
Why recycle carbide? | To reduce costs, save resources, and minimize environmental impact. |
How is carbide recycled? | Through methods like chemical processing, grinding, and sintering. |
What are the costs associated with it? | Costs vary based on process and material, ranging from $10 to $200/kg. |