The aerospace industry has long been a cornerstone of innovation and precision engineering. Among the many materials that play a vital role in this sector, carbide stands out as a powerhouse. Known for its unmatched strength, hardness, and durability, carbide has become a critical component in manufacturing aerospace tools and parts. But what makes carbide so special? Why is it preferred over other materials? Let’s dive deep into the fascinating world of carbide in the aerospace industry, unraveling its secrets one layer at a time.
What is Carbide?
Carbide is a compound consisting of carbon combined with a metal or metalloid. The most commonly used carbide in aerospace is tungsten carbide, which combines tungsten and carbon atoms to create a material that’s incredibly hard and resistant to wear. But it doesn’t stop there; carbide’s versatility allows for various formulations and applications tailored to meet specific demands in aerospace engineering.
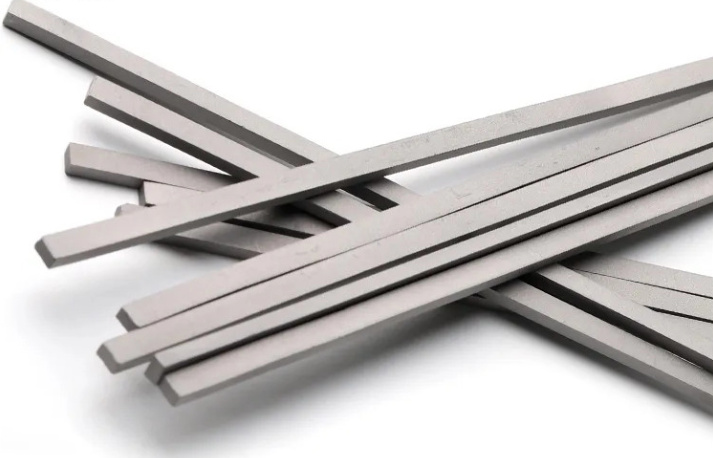
Types of Carbide Used in Aerospace Industry
Here’s a breakdown of different carbides used in aerospace applications, each with unique properties and uses:
Type of Carbide | Composition | Applications |
---|---|---|
Tungsten Carbide (WC) | Tungsten + Carbon | Cutting tools, wear-resistant coatings |
Silicon Carbide (SiC) | Silicon + Carbon | Thermal shielding, structural components |
Boron Carbide (B4C) | Boron + Carbon | Abrasive nozzles, lightweight armor |
Titanium Carbide (TiC) | Titanium + Carbon | Coatings, high-temperature components |
Chromium Carbide (CrC) | Chromium + Carbon | Corrosion-resistant coatings |
Niobium Carbide (NbC) | Niobium + Carbon | High-temperature applications |
Vanadium Carbide (VC) | Vanadium + Carbon | Cutting tools, hard coatings |
Molybdenum Carbide (MoC) | Molybdenum + Carbon | Catalysts, high-strength components |
Hafnium Carbide (HfC) | Hafnium + Carbon | Heat shields, rocket nozzles |
Zirconium Carbide (ZrC) | Zirconium + Carbon | Nuclear reactors, aerospace engines |
Each type of carbide has a role to play, tailored to specific performance needs such as thermal resistance, lightweight construction, or extreme hardness.
Raw Material and Composition Analysis
Primary Components
Carbides used in the aerospace industry are meticulously engineered, and their composition is critical to performance. Let’s break down some key components:
- Tungsten Carbide: A combination of tungsten and carbon that offers extreme hardness and wear resistance.
- Silicon Carbide: Made from silicon and carbon, this material boasts excellent thermal properties and resistance to oxidation.
- Boron Carbide: Exceptionally lightweight and robust, ideal for impact-resistant applications.
Material | Elemental Composition | Key Features |
---|---|---|
Tungsten Carbide | 94% Tungsten, 6% Carbon | Hardness, durability |
Silicon Carbide | 70% Silicon, 30% Carbon | Heat resistance, lightweight |
Boron Carbide | 80% Boron, 20% Carbon | Lightweight, extreme hardness |
Titanium Carbide | 99% Titanium, 1% Carbon | High strength, thermal stability |
Chromium Carbide | 80% Chromium, 20% Carbon | Corrosion resistance |
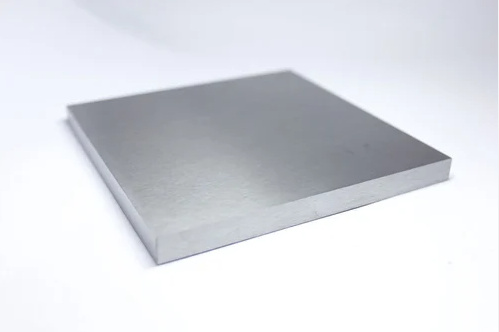
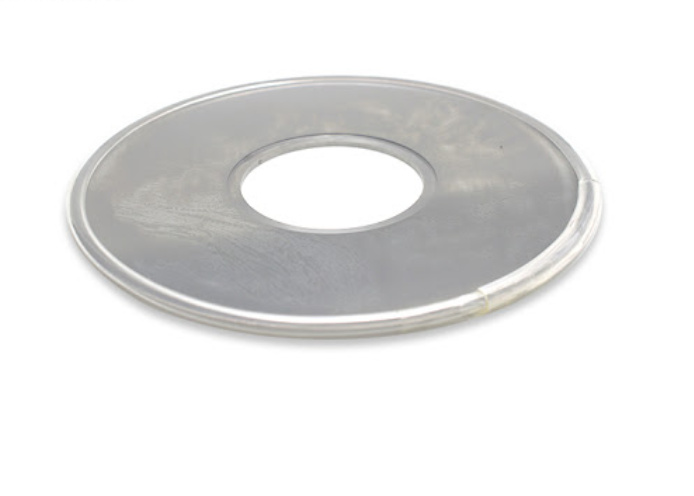
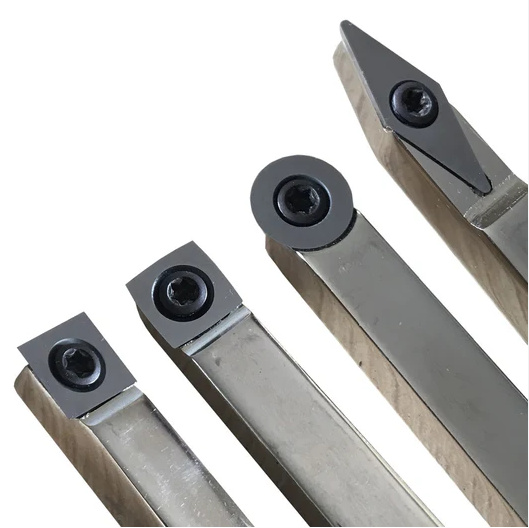
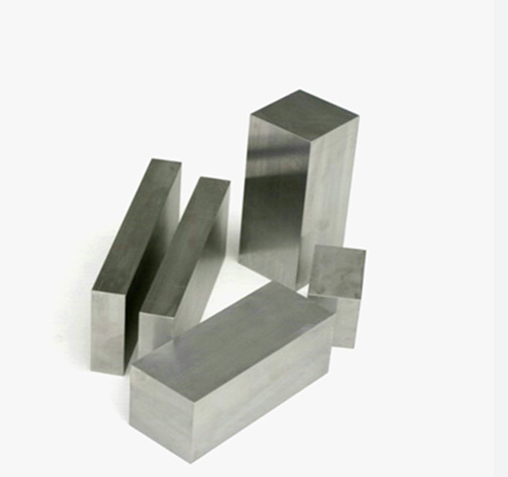
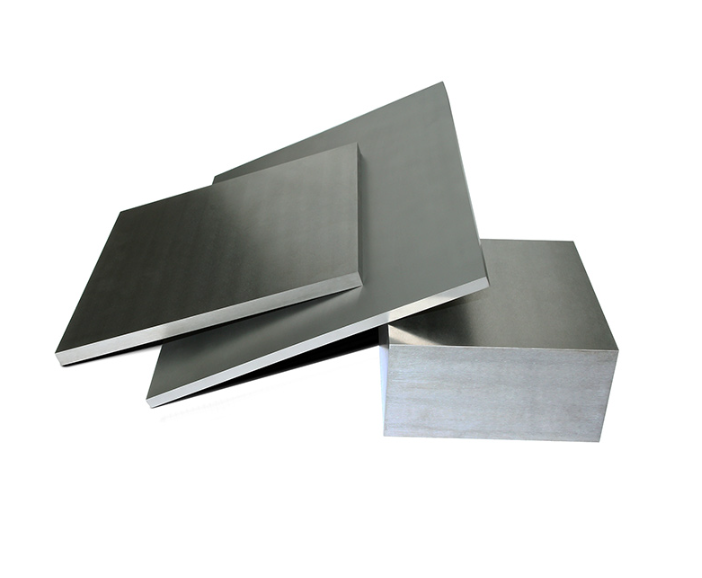
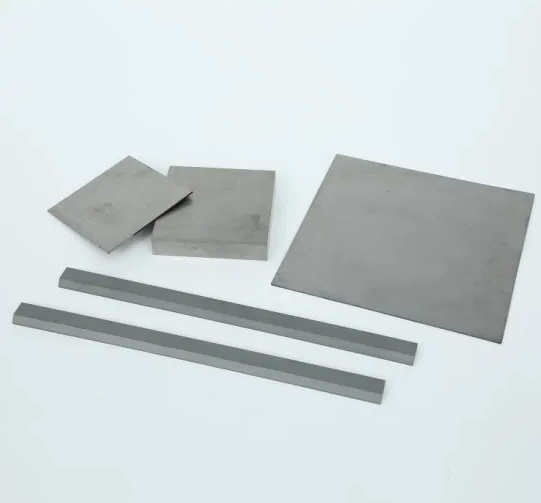
Applications of Carbide in Aerospace Industry
Application Area | Type of Carbide Used | Purpose |
---|---|---|
Cutting Tools | Tungsten, Vanadium Carbide | Precision machining of aerospace parts |
Thermal Shields | Silicon, Hafnium Carbide | Heat protection during re-entry |
Engine Components | Zirconium, Titanium Carbide | High-temperature resistance |
Abrasive Nozzles | Boron Carbide | Durable nozzles for fuel injection |
Wear-Resistant Coatings | Chromium, Tungsten Carbide | Increased lifespan of tools and components |
Carbides are indispensable in making everything from cutting tools that shape aerospace parts to the heat shields protecting spacecraft.
Production Process Flow of Carbide in Aerospace Industry
Producing carbide for aerospace applications involves multiple stages to ensure its quality and performance:
- Raw Material Sourcing: Extraction and refinement of metals like tungsten, silicon, or titanium.
- Mixing and Blending: Combining the metal with carbon in precise proportions.
- Sintering: Applying heat and pressure to fuse the components into a solid mass.
- Shaping and Machining: Forming the carbide into desired shapes and sizes.
- Coating (if applicable): Adding protective layers for enhanced performance.
- Quality Control: Rigorous testing to meet aerospace standards.
Material Properties of Carbide in Aerospace Industry
Property | Typical Range | Relevance to Aerospace |
---|---|---|
Hardness (Vickers) | 1200 – 2500 HV | Extreme wear resistance |
Density | 2.1 – 15.6 g/cm³ | Lightweight to ultra-dense applications |
Thermal Conductivity | 20 – 120 W/mK | Heat management |
Melting Point | 2800 – 3900°C | High-temperature applications |
Tensile Strength | 300 – 800 MPa | Structural stability |
Comparative Table of Composition, Properties, and Characteristics
Carbide Type | Composition | Hardness | Strength | Wear Resistance | Thermal Stability |
---|---|---|---|---|---|
Tungsten Carbide | W + C | High | Very High | Excellent | Moderate |
Silicon Carbide | Si + C | Medium | High | Good | Excellent |
Boron Carbide | B + C | Very High | Moderate | Excellent | Good |
Titanium Carbide | Ti + C | High | High | Good | High |
Hardness, Strength, and Wear Resistance Comparison
Carbide Type | Hardness (Vickers) | Strength (MPa) | Wear Resistance |
---|---|---|---|
Tungsten Carbide | 2000 HV | 750 MPa | Excellent |
Silicon Carbide | 1500 HV | 600 MPa | Good |
Boron Carbide | 2500 HV | 400 MPa | Excellent |
Titanium Carbide | 1800 HV | 700 MPa | Good |
Specifications, Sizes, Shapes, and Standards
Specification | Details |
---|---|
Sizes | Powder sizes from 0.1 μm to 5 μm |
Shapes | Cylindrical rods, sheets, custom geometries |
Standards | ISO 9001, ASTM B777, AMS-T-21014 |
Choosing Carbide in Aerospace Industry and Pricing Details
Consideration | Details |
---|---|
Application Type | Cutting, coating, structural |
Performance Needs | Wear resistance, thermal stability |
Pricing | $50 – $500 per kg, depending on grade |
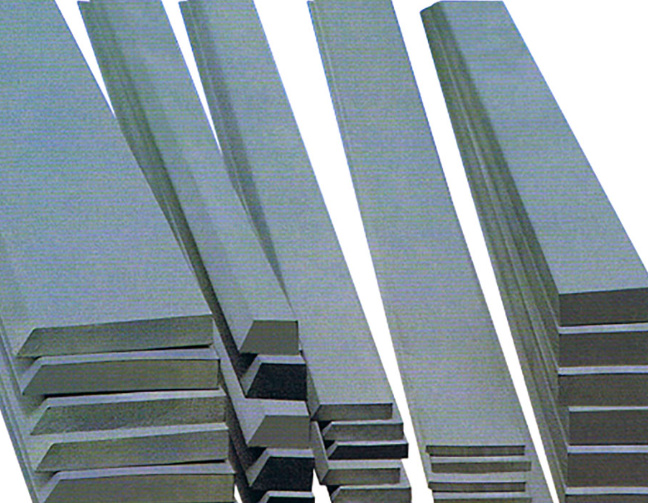
Advantages and Limitations of Carbide in Aerospace
Advantages | Limitations |
---|---|
Exceptional hardness and durability | Higher cost compared to traditional metals |
Superior thermal and wear resistance | Brittle in certain formulations |
Versatile applications | Requires specialized manufacturing |
FAQs
Question | Answer |
---|---|
What makes carbide ideal for aerospace tools? | Its unmatched hardness, strength, and wear resistance. |
How is tungsten carbide different from silicon carbide? | Tungsten carbide is harder; silicon carbide is better at handling heat. |
Is carbide environmentally friendly? | Production involves energy-intensive processes, but recycling is possible. |
What is carbide, and why is it used in aerospace? | Carbide is a compound composed of carbon and a metal, such as tungsten or titanium. It is widely used in aerospace for its exceptional hardness, high melting point, resistance to wear and corrosion, and ability to withstand extreme temperatures and pressures. These properties make it ideal for critical components like cutting tools, engine parts, and coatings. |
Is carbide environmentally sustainable in aerospace applications? | Carbide’s longevity and resistance to wear reduce the need for frequent replacements, contributing to sustainability by lowering material waste. However, its manufacturing process can be energy-intensive, and recycling options are still evolving. |