blank carbide strip customized refer to unfinished flat tungsten carbide strips that are customized and precision ground to specified dimensions for making cutting tool inserts and wear parts. Proper selection of blank size, composition and grinding technique is vital.
This guide covers everything related to blank carbide strips including customization options, applications, specifications, suppliers, and more.
Introduction to blank carbide strip customized
- Unfinished tungsten carbide strips before grinding
- Made of tungsten carbide particles in cobalt binder matrix
- Available in standard or custom sizes and alloy grades
- Supplied based on application requirements
- Ground to precise dimensions for making inserts, dies, wear parts
Customizing blank composition and dimensions optimizes performance and tool design.
Blanks Customization Options
Blank carbide strips can be customized by:
Parameter | Options |
---|---|
Alloy grade | Unique composites and grain sizes |
Strip dimensions | Width, thickness, length |
Flatness/straightness | Tight tolerances available |
Surface finish | Customized roughness |
Edge preparation | Chamfering, honing, deburring |
Hardness | Range from soft to extremely hard |
Coating | TiCN, TiAlN, diamond coatings |
Work with supplier to optimize blank features for your tooling design and application needs.
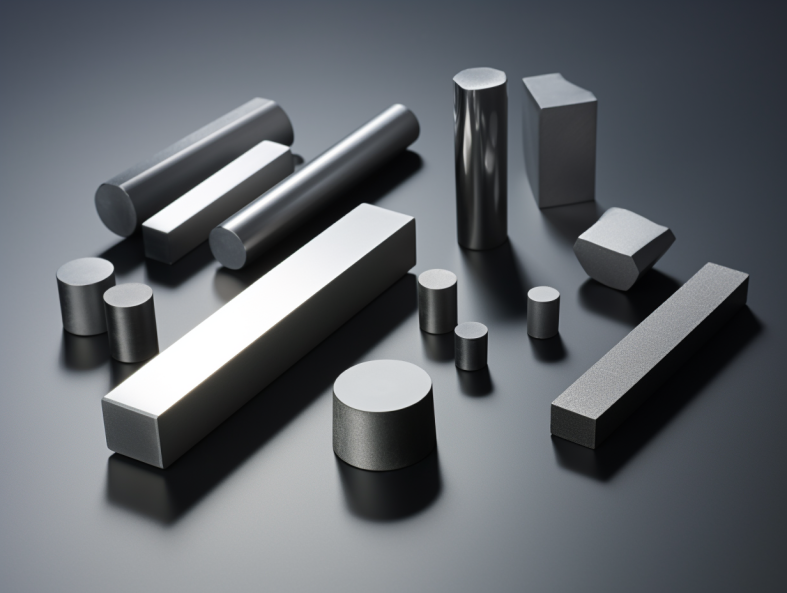
Applications of Carbide Strip Blanks
Common applications of customized carbide strip blanks:
- Cutting tool inserts for machining
- Drawing dies for wire manufacturing
- Extrusion dies for profiles/rods
- Pelletizing rollers and dies
- Slitters, choppers, crushers
- Wear parts and tooling
- Recycling equipment parts
- Food processing blades and knives
Carbide blank selection directly impacts tool and equipment durability, productivity and lifetime.
Types of blank carbide strip customized
Major types of tungsten carbide strip blanks:
Blank | Description | Applications |
---|---|---|
Cobalt-bonded | Most common WC-Co blanks | General machining inserts, dies |
Titanium-bonded | WC-TiC-Ti blanks | High speed machining |
Cermet | WC-TiC-TaC-NbC-Co | Friction parts, low wear tooling |
Carbonitride | WC-TiCN-TaC-Co/Ni | High speed/temp alloys |
Cubic boron nitride | PcBN composite blanks | Hardened steels, cast irons |
Special alloys | Innovative grades and binders | Customized uses |
Work closely with your supplier to select the optimal blank composition.
Key Specifications of Carbide Blanks
Critical parameters when ordering blank carbide strips:
Parameter | Selections |
---|---|
Composition | Carbide, binder, grain size |
Dimensions | Width, thickness, length |
Flatness | Target flatness tolerance |
Surface finish | As-sintered or ground finish |
Edges | Square, beveled, rounded |
Hardness | From soft to very hard |
Coatings | Uncoated, TiCN, TiAlN, CVD diamond |
Testing | Chemistry, microstructure, hardness |
Certification | Material certification |
Specifying appropriate parameters ensures blanks meet design expectations.
Dimensional Tolerances for Carbide Blanks
Typical dimensional tolerances achievable:
Parameter | Tolerance Range |
---|---|
Thickness | +/- 0.001″ to 0.005″ |
Width | +/- 0.001″ to 0.005″ |
Length | +/- 0.020″ |
Flatness | 0.001″ to 0.006″ per inch |
Squareness | +/- 0.001″ to 0.005″ |
Surface finish | Up to 3 microinch Ra |
Tighter tolerances are possible. Confirm capabilities with your supplier.
Grades of Carbide Blanks
Various standard and custom carbide grades are available:
Grade | Description |
---|---|
C1, C2 | 6% cobalt grades for steel |
C3, C4 | 10% cobalt high toughness grades |
C5, C6 | Mixed carbide grades for alloys |
C7, C8 | 12% cobalt difficult machining |
C9, P10 | Fine grain high edge strength |
P20-P60 | Special binders/carbides for specific applications |
Different compositions offer optimal performance for specific work materials.
How Carbide Blanks are Customized
Methods for customizing blank carbide strips:
- Alloying – Formulating composition for application
- Sintering – Controls carbide grain size and properties
- Grinding – Profile, finish, edge prep
- Edge honing – Smooth edge finish
- Chamfering and deburring – For safety and performance
- Laser cutting – Precision blank cutting
- Coatings – Improve wear, lubricity and toughness
Advanced processing technologies enable detailed customization.
Supply Chain for Carbide Blanks
Typical carbide blank supply chain:
- Powder suppliers – Carbides, cobalt, binders, grain growth inhibitors
- Manufacturers – Pressing, sintering, grinding blanks
- Coating applicators – Add surface coatings
- Distributors – Supply to end users
- Grinding shops – Finish blanks into tooling
- End users – Consume tools and dies
Collaboration between supply chain partners is vital to deliver high performance blanks that become long-lasting tools.
Global Suppliers of Carbide Blanks
Leading global suppliers of blank carbide strips:
Company | Locations | Products | Pricing |
---|---|---|---|
Kennametal | USA, Europe, China | Standard and custom blanks | $$$ |
Mitsubishi Materials | Japan, Global | Broad grade range | $$$ |
Sandvik | Sweden, Brazil, India | Advanced nano-structured grades | $$$ |
Iscar | Israel, Global | Customized geometries | $$$ |
Tungaloy | Japan, USA | Custom profiles and coatings | $$$ |
Korloy | Korea | Cost effective carbide blanks | $$ |
Pricing ranges from $5 – $50 per inch depending on size, grade, tolerance and order volume.
Regional carbide manufacturers also supply blanks tailored for local markets.
Selecting a Carbide Blank Supplier
Key considerations when selecting a carbide blank supplier:
- Technical expertise in grades for your specific application
- Capability to customize composition, dimensions, tolerances, features
- Consistent and well-controlled manufacturing process
- Reasonable minimum order quantities
- Competitive and transparent pricing
- High quality standards and inspection
- Local availability or reasonable lead times
- Strong technical support and customer service
Finding the optimal balance of blank quality and economics requires careful supplier evaluation.
How to Grind Carbide Blanks
Methods for precision grinding carbide blank strips:
Method | Overview |
---|---|
Surface grinding | Produces tight tolerances and fine finishes |
EDM grinding | Complex shapes and profiles; fine control |
HEDM grinding | Fast removal for indexable inserts |
Abrasive belt grinding | Flexible hand grinding of blanks |
Double disc grinding | Simultaneous opposing sides grinding |
Proper grinding equipment, techniques and parameters are required to achieve specifications without micro-cracking or damaging blanks.
Installing Carbide Blank Fixtures
Accurate blank fixturing is critical for precision grinding:
- Use robust and vibration damping fixture design
- Precisely align guides and locators
- Incorporate vacuum clamping for thin/fragile parts
- Allow for coolant drainage
- Enable ergonomic loading/unloading
- Facilitate inspection accessibility
- Design modular/flexible workholding
Well designed fixtures enable fast, accurate, and reproducible blank positioning for grinding.
Benefits of Customized Carbide Blanks
Advantages versus off-the-shelf blank sizes:
- Optimized dimensions for your tooling design needs
- Composition tailored to your machining application
- Tighter tolerances support precision grinding
- Specific surface finish requirements achieved
- Edge preparation done to your specifications
- Just-in-time delivery of ready blanks
- Avoid overgrinding and scrap from standard sizes
- Consistent tooling performance and lifetime
Properly customized carbide blanks are vital for cost-effective tooling production.
Limitations of Carbide Blanks
- Higher upfront costs versus standard sizes
- Minimum order quantities may apply
- Lead times for customized items
- Potential for excessive customization
- Over-dependency on specific supplier
- Testing needed to confirm performance
- Change management if altering sources
Understand your volume needs and cost constraints before committing to custom carbide blanks.
Cost Analysis of Carbide Blanks
- Carbide strip cost:
- Size, grade, tolerances
- $5-$50 per inch blank
- Customization costs:
- Composition development
- Tighter tolerances
- Special processing
- Inventory holding costs
- Grinding wheel consumption
- Testing and qualification
- Shipping considerations
Weigh customization benefits against total costs for your production volumes.
Future Outlook for Carbide Blanks
Future carbide blank trends:
- New advanced grades and nano-structured powders
- Custom-designed alloys using modeling
- Tighter tolerances and finer surface finishes
- Just-in-time supply chain management
- More recycling and re-use programs
- Automated grinding technologies
- Inventory optimization using ERP systems
- Consolidation among major carbide producers
- Expanded use of safety-edge preparation
- Growth in indexable tooling segments
Innovations in materials, manufacturing, and inventory control will yield improved performance and economics.
FAQ
Q: What are carbide blanks used for?
A: Mainly for manufacturing cutting tool inserts, dies, and wear parts requiring high hardness and wear resistance.
Q: How are carbide blanks made?
A: By compacting carbide/binder powders into a mold, then sintering to form a solid carbide strip blank.
Q: What is the difference between cobalt and titanium carbide blanks?
A: Cobalt-bonded blanks offer toughness while titanium-bonded grades provide high heat and wear resistance.
Q: What tolerances are achievable for carbide blanks?
A: Blanks can be ground to tight dimensional tolerances down to +/- 0.001″ or better.
Q: How long does it take to produce customized carbide blanks?
A: Lead times range from 2-8 weeks typically depending on supplier schedules and customization complexity.
Q: What coatings are used on carbide blanks?
A: Common coatings are titanium carbonitride (TiCN), titanium aluminum nitride (TiAlN), titanium nitride (TiN), and diamond.
Q: What causes micro-cracking in carbide blanks?
A: Excessive grinding forces, poor wheels, overheating, or improper process parameters lead to edge micro-cracks.
Q: How are carbide blanks packaged for shipping?
A: Careful packaging in rigid boxes with separator sheets prevents damage during handling and transportation.
Q: What safety precautions are needed when grinding carbide blanks?
A: Proper wheel guards, ventilation, protective eyewear, mask, containment, coolant management, and safe operating procedures.
Q: How can carbide blank inventory be optimized?
A: Strategies like just-in-time delivery, vendor managed inventory, and connected ERP systems minimize working capital needs.