Why is the Cutting of Carbide Rod Challenging?
Cutting carbide rods is kind of like trying to carve through a diamond with a butter knife—yeah, it’s that tough. Carbide, especially tungsten carbide, is incredibly hard and brittle. It’s designed to withstand intense wear and tear, which makes it a rockstar in industrial applications.
The main issue is that carbide doesn’t play nice with traditional cutting tools. Standard tools often wear out quickly or can’t handle the high pressure and heat generated during the cutting process. That’s why choosing the right method and equipment isn’t just a suggestion—it’s a necessity.
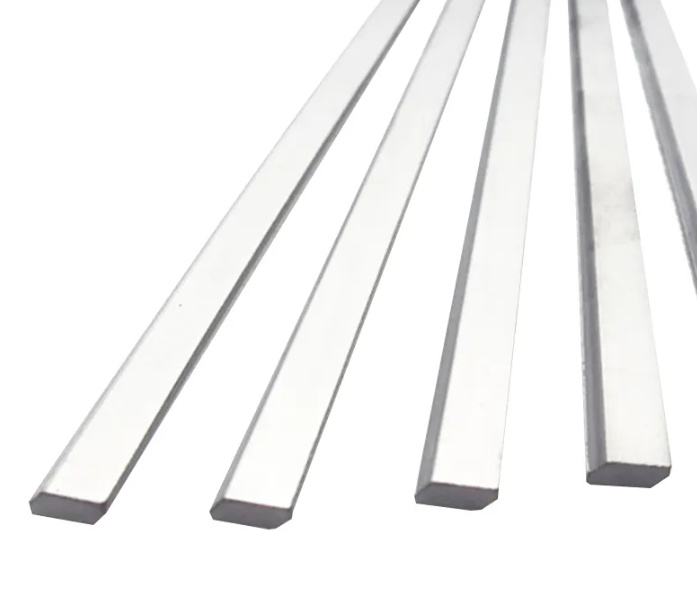
Properties of Carbide Rods
Before we jump into slicing techniques, let’s talk chemistry and physics. Carbide rods are typically made from tungsten carbide (WC) mixed with a binder like cobalt (Co). This blend gives them a unique combo of extreme hardness, high melting point, and resistance to abrasion and deformation.
Here are a few properties that stand out:
- Hardness: Around 1600–2200 HV (Vickers Hardness)
- Compressive Strength: Up to 7000 MPa
- Thermal Conductivity: 70–100 W/m·K
- Elastic Modulus: 530–700 GPa
- Fracture Toughness: Relatively low (4–15 MPa·m½), which is why they crack easily
These properties are fantastic for tool performance but a headache when it comes to machining. The hardness can kill tooling, while the brittleness demands a feather-light touch and laser precision.
Common Cutting Methods for Carbide Rod
Let’s talk tactics. Cutting carbide isn’t a one-size-fits-all operation. There are multiple ways to do it, and each has its own set of pros and cons depending on what you’re trying to achieve.
1. EDM (Electrical Discharge Machining)
- Best for: Intricate cuts and tight tolerances
- Pros: No mechanical stress, great surface finish
- Cons: Slow process, high cost
2. Diamond Wheel Grinding
- Best for: High-volume production
- Pros: High accuracy, durable tooling
- Cons: Expensive equipment, high maintenance
3. Laser Cutting
- Best for: Complex geometries and micro-cutting
- Pros: No contact, ultra-precise
- Cons: Risk of thermal damage, costly setup
4. Water Jet Cutting
- Best for: Heat-sensitive materials
- Pros: No thermal effect, eco-friendly
- Cons: Lower precision, rougher finish
5. Sawing with Diamond Blades
- Best for: Straight cuts in short rods
- Pros: Cost-effective, easy setup
- Cons: Limited to less intricate designs
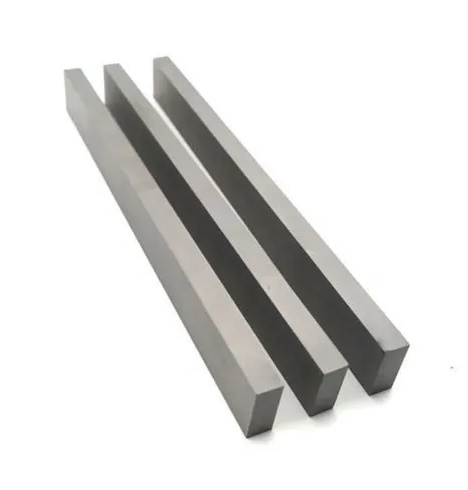
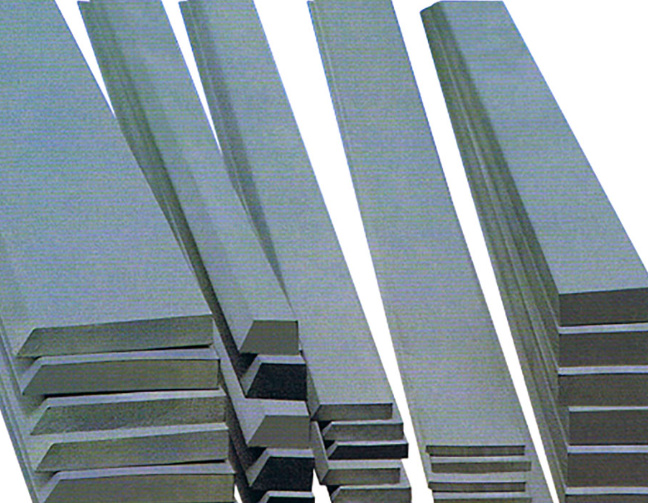
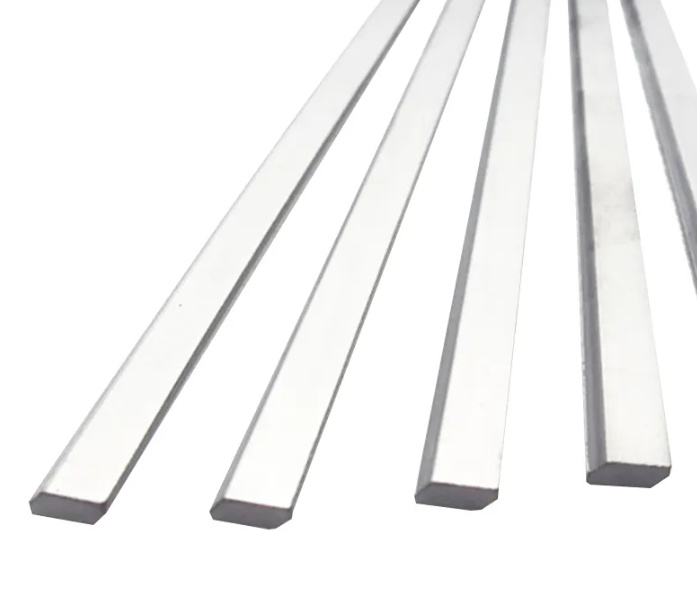
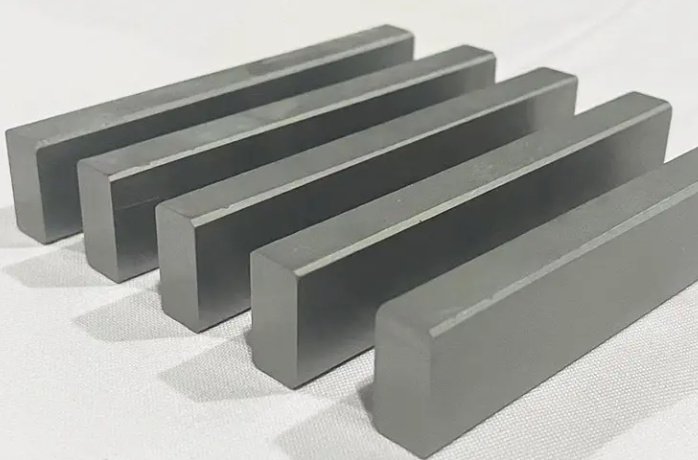
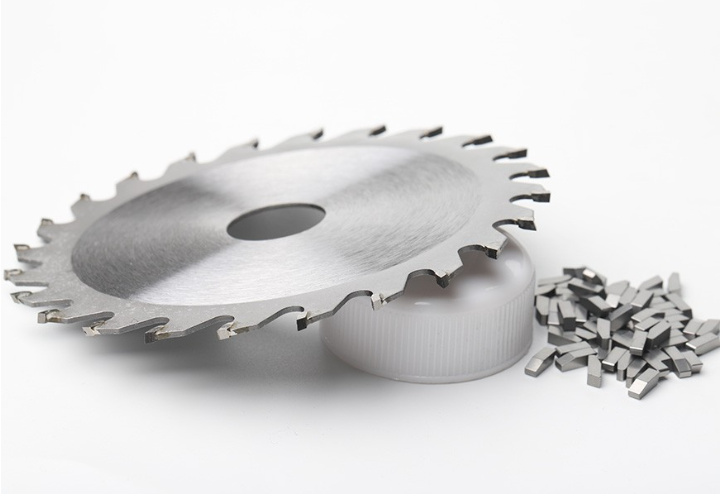
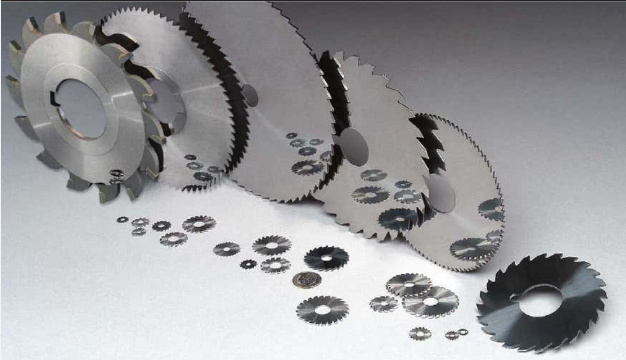
Best Practices for Cutting Carbide Rods
Cutting Method | Best Use Case | Precision Level | Tool Life | Speed | Surface Finish |
---|---|---|---|---|---|
EDM | Complex shapes, tight tolerances | Very High | Long (electrode dependent) | Slow | Excellent |
Diamond Wheel Grinding | High-volume production | High | Long | Fast | Excellent |
Laser Cutting | Thin rods, complex patterns | Very High | Medium | Medium | Good |
Water Jet Cutting | Heat-sensitive applications | Medium | Long | Medium | Fair |
Sawing w/ Diamond Blades | Quick straight cuts, short rods | Medium | Medium | Fast | Good |
Equipment and Tools Recommended
You wouldn’t bring a spoon to a sword fight, right? Same goes for carbide cutting. You need the right gear:
- Precision Diamond Cut-Off Machines – Offers low-vibration, high-accuracy cuts.
- Wire EDM Machines – Perfect for intricate, high-tolerance jobs.
- Laser Cutters with Cooling Systems – Keeps thermal deformation in check.
- Water Jet Cutters with Abrasives – Great for temperature-sensitive tasks.
- High-Quality Diamond Blades – Essential for longevity and surface integrity.
Brands like AccuteX, GF Machining, and Sodick make world-class EDM systems, while TRUMPF and Amada dominate in laser cutting tech.
How to Avoid Edge Breakage When Cutting Carbide Rods
Think of carbide like glass—it doesn’t bend, it breaks. So, if you rush the process or apply uneven pressure, snap, there goes your pristine edge.
To keep things smooth:
- Use sharp, diamond-coated tools to reduce vibration.
- Secure the rod firmly but without excessive force.
- Use coolants to minimize heat build-up.
- Cut incrementally rather than in one aggressive pass.
Patience is your best friend here. It’s all about finesse, not brute force.
How to Cut Slender Rods Without Deformation When Cutting Carbide Rods
Cutting thin carbide rods is like trying to split a toothpick with a samurai sword—it’s super easy to mess up.
Here’s how to stay on point:
- Support the rod fully throughout its length to prevent bending.
- Use fine-grit diamond wheels for gentle, accurate cuts.
- Go slow and steady with feed rates and avoid lateral pressure.
- Consider laser or EDM if you need ultra-fine precision.
Specific Metal Powder Models for Carbide Rods (With Descriptions)
Powder Model | Composition | Grain Size | Applications | Strengths |
---|---|---|---|---|
WC-Co APT 88/12 | 88% WC, 12% Co | 0.8 µm | Drills, reamers | High wear resistance |
WC-Co H10F | 90% WC, 10% Co | 0.6 µm | Cutting tools | High hardness |
WC-Co K20 | 93% WC, 7% Co | 1.0 µm | Mining tools | Toughness + wear resistance |
WC-Co K30 | 94% WC, 6% Co | 1.2 µm | End mills | Superior edge retention |
WC-Co H13A | 87% WC, 13% Co | 1.6 µm | Heavy-duty tools | Impact resistance |
WC-Ni | 85% WC, 15% Ni | 1.0 µm | Corrosive environments | Corrosion resistance |
WC-Co Ultra Fine | 92% WC, 8% Co | 0.4 µm | Precision parts | Highest hardness |
WC-TiC-Co | WC + TiC + Co | 1.2 µm | Aerospace parts | Thermal stability |
WC-Co C2 | 94% WC, 6% Co | 1.1 µm | Die tools | Surface finish quality |
WC-Co C10 | 90% WC, 10% Co | 0.7 µm | Micro-tools | Micro-edge sharpness |
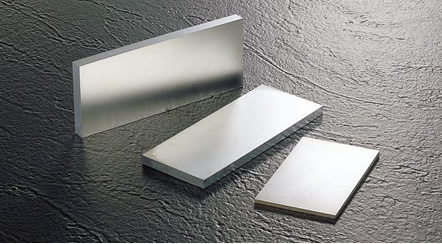
FAQ
Question | Answer |
---|---|
What’s the best way to cut carbide rods at home? | Use a diamond saw blade and go slow. Avoid heat buildup and always wear protection. |
Can carbide rods be laser cut without cracking? | Yes, but only with high-end systems that control heat well. Otherwise, cracking is a risk. |
Why do carbide rods chip at the edges? | Usually from improper clamping, uneven pressure, or dull tools. |
Is water jet cutting effective for carbide rods? | It works, especially when you want to avoid heat. Just don’t expect super-smooth finishes. |
Which metal powder is best for precision carbide tools? | WC-Co Ultra Fine for its superior hardness and fine grain. |
What safety gear is essential when cutting carbide? | Eye protection, gloves, and dust extraction systems to avoid breathing in fine particles. |
Can EDM be used on all carbide rods? | Mostly, yes. Just ensure the rod isn’t too conductive if using certain binders. |
Do I need coolant when cutting carbide? | Yes! Coolant reduces heat and extends tool life significantly. |
How long do diamond blades last when cutting carbide? | Depends on quality and use, but generally 10–20 times longer than standard blades. |
Are there portable tools for carbide cutting? | Some compact diamond saws and mini EDM units are available for specialized use. |