Common Applications of Carbide Plates in Manufacturing, Molds, and Cutting Tools
Carbide plates are a staple in heavy-duty operations, cutting tools, die and mold making, wear parts, and aerospace precision components. Their unrivaled hardness, resistance to heat and wear, and sheer longevity make them the go-to material for high-performance industrial parts.
In molds, especially injection molds and die-casting tools, carbide plates help extend service life and reduce downtime due to maintenance. In cutting applications—think CNC tools, saw blades, or lathe inserts—they slice through metal like a hot knife through butter.
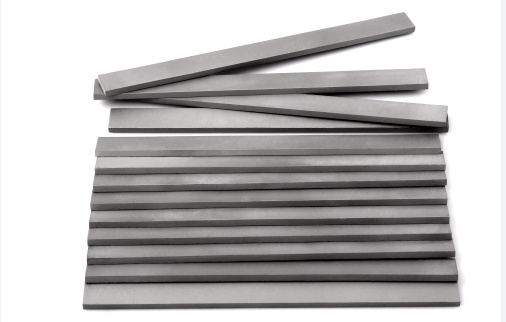
What is a Carbide Plate?
Carbide plates are flat components made primarily from tungsten carbide (WC), often mixed with a binder metal like cobalt (Co). This compound results in a material that’s harder than nails—literally. Tungsten carbide ranks close to diamond on the Mohs scale, making it one of the toughest materials commercially available.
The real magic comes from how these plates are manufactured. Metal powders (more on those later) are compacted under immense pressure, then sintered at high temperatures. The result? Plates that are dense, nearly unbreakable, and ready to face industrial-level stress without blinking.
Why Design Optimization Matters
Here’s the thing: just slapping a chunk of carbide into a machine doesn’t cut it—pun fully intended. Design optimization is the secret sauce that ensures carbide plates are doing their best work.
Optimizing a carbide plate’s design can:
- Improve performance under stress
- Extend tool life
- Reduce failure rates and chipping
- Cut manufacturing costs
- Boost energy efficiency
Without optimization, you’re essentially putting a Formula 1 engine in a shopping cart. Sure, it might work for a bit, but it’s going to fall apart fast and waste a ton of resources.
Optimization helps engineers decide the best shape, composition, thickness, and application method for carbide plates. This can involve tweaking geometry, refining powder blend ratios, improving binder dispersion, or even adding layered coatings.
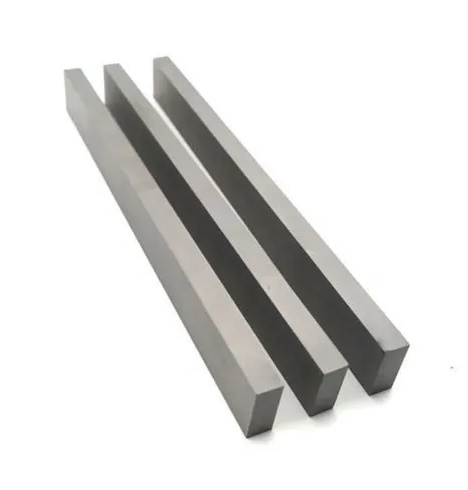
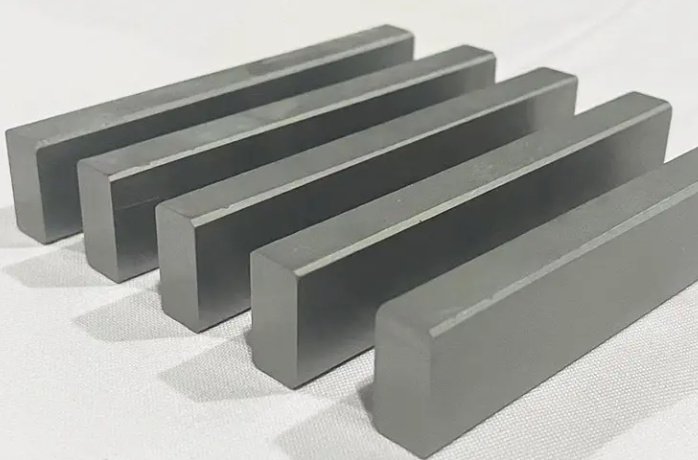
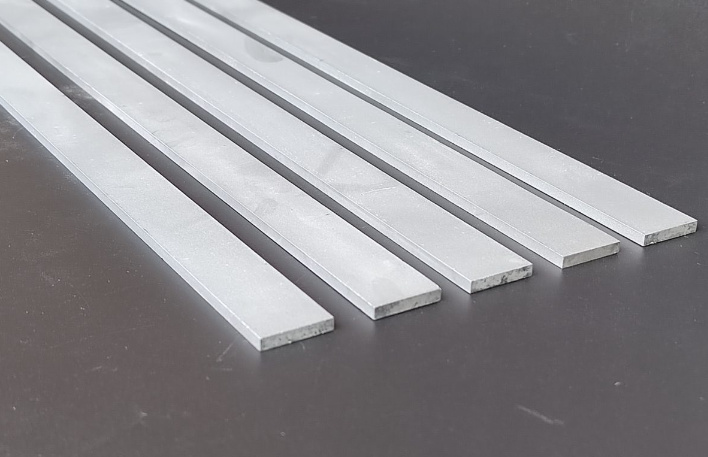
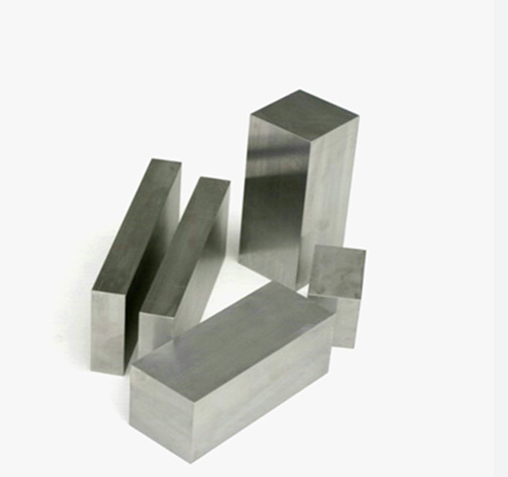

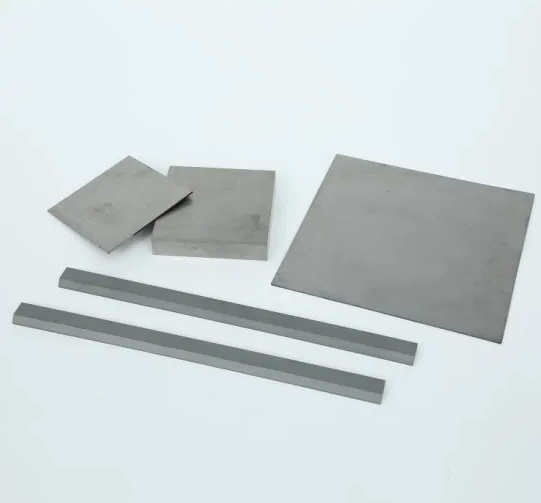
Key Factors in Carbide Plate Design Optimization
Below is a table that breaks down the core parameters and how they affect carbide plate performance.
Key Design Considerations and Their Impact
Factor | Why It Matters | Optimization Strategy |
---|---|---|
Plate Thickness & Dimensions | Affects stress resistance and fitting in assemblies | Match size with load distribution and application geometry |
Powder Composition | Impacts hardness, toughness, corrosion resistance | Blend multiple powders; balance WC and binder content |
Sintering Conditions | Influences grain size, porosity, and bonding | Optimize time/temp balance; use pressure sintering |
Coating or Surface Treatment | Reduces wear, friction, and corrosion | Apply PVD, CVD coatings; add lubricative or anti-corrosive finishes |
Geometry and Shape | Determines load distribution and cutting efficiency | Design with FEM simulations for stress distribution |
Cooling & Heat Management | Impacts tool life under thermal stress | Integrate coolant channels or heat-dissipating layers |
Application-Specific Loads | Determines fatigue life and fracture points | Model real-world mechanical loading scenarios |
Grain Size Control | Smaller grains increase strength, larger grains increase toughness | Choose grain size based on priority—strength vs. impact resistance |
Binder Phase Homogeneity | Poor dispersion leads to weak points and cracking | Use high-energy ball milling and uniform sintering techniques |
Compatibility with Inserts/Tools | Poor fits cause chatter, misalignment, or tool breakage | Coordinate with tool design for perfect mating geometry |
Case Studies and Application Examples of Optimized Carbide Plate Design
High-Speed CNC Machining Tool Manufacturer
A German tool company used standard tungsten carbide plates in their lathe tools. However, they noticed tool wear rates climbing fast. They switched to an optimized carbide plate design with a fine WC grain structure, cobalt binder, and TiAlN coating. Result? A 40% increase in tool life and a 25% boost in cutting speed.
Mold Base Supplier for Automotive Parts
An Asian mold manufacturer experienced premature failure in their stamping die base. After FEM simulation analysis and supplier collaboration, they implemented a custom-designed carbide plate with a layered composite structure. The new design resisted cracking and extended tool life by 2x.
Design Software, Simulation Technology, and Selection of Cooperative Suppliers for Carbide Plate
Welcome to the digital age of carbide plate design. Say goodbye to guesswork and hello to precision. Engineers today rely on advanced CAD/CAM software, Finite Element Method (FEM) simulations, and Material Property Databases to virtually test designs before they hit production.
Popular Tools Include:
- Autodesk Fusion 360 – Combines CAD/CAM with generative design for optimized layouts.
- ANSYS Mechanical / COMSOL Multiphysics – Ideal for thermal, structural, and fatigue simulation.
- JMatPro & Thermo-Calc – For modeling phase diagrams and material behavior under temp/pressure.
And don’t underestimate the power of collaboration. Partnering with specialized powder metallurgy suppliers and coating providers can make a massive difference. Trusted partners help you select the right powder blends, suggest heat treatment schedules, and even co-develop custom sintering programs.
10+ Specific Metal Powder Models Used in Carbide Plate Production
Let’s get nerdy. Here are 12 of the most commonly used metal powder models for carbide plates, complete with descriptions:
Powder Model | Primary Use | Properties | Advantages | Best For |
---|---|---|---|---|
WC-10Co | Standard toolmaking | Hard, moderate toughness | Well-balanced wear resistance | General machining |
WC-6Co | Finishing tools | Higher hardness | Better edge retention | High-speed tools |
WC-Ni | Corrosion-prone areas | Cobalt-free | Non-magnetic, corrosion-resistant | Chemical & food processing |
WC-TiC-Co | Abrasive applications | Enhanced hardness | Good against wear | Mining and drilling tools |
WC-12Co | Impact resistance | High toughness | Shock absorption | Forging dies |
WC-Cr3C2-Ni | High temp settings | Thermal resistance | Maintains hardness when hot | Aerospace turbines |
WC-Co+VC (Vanadium) | Crack resistance | Grain refiner additive | Improves fracture toughness | Thin plates & inserts |
WC-Co-TaC | Custom blend | High strength & edge durability | Balanced performance | Mill cutters |
WC-Co-Mo | Experimental tools | Molybdenum binder | Fine-grain structure | Micro-drills |
WC-NiCr | Harsh environments | High corrosion and wear resistance | Non-cobalt option | Oil & gas tooling |
WC-Co-Al | Lightweight needs | Slight weight reduction | Trade-off with strength | Light metal forming |
WC-Co-ZrC | Extreme wear | Reinforced with ZrC | Exceptional abrasion resistance | Dry machining |
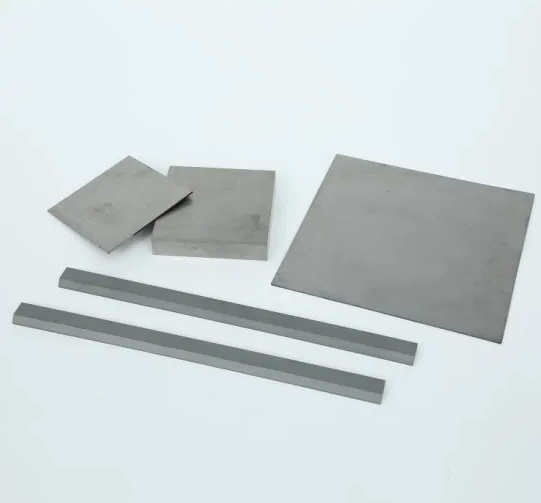
FAQ
Question | Answer |
---|---|
What is the ideal carbide composition for general use? | WC-10Co is widely considered the best balance of hardness and toughness for most applications. |
How do coatings improve carbide plates? | Coatings like TiAlN or DLC reduce friction, wear, and heat buildup, extending lifespan. |
What’s the biggest design mistake? | Not accounting for thermal expansion and mechanical stress under load. Always simulate first. |
Can I reuse or regrind carbide plates? | Yes, many plates can be re-ground or recoated, but ensure original integrity isn’t compromised. |
Is cobalt always necessary? | No—Ni and NiCr alternatives exist for corrosion-prone environments or health concerns. |
What software is best for simulation? | ANSYS and COMSOL are gold standards for physical simulation, especially under thermal and mechanical loads. |
How do I choose the right supplier? | Look for partners offering full-spectrum support: powder, design, sintering, and coating. |
Are there eco-friendly carbide options? | Yes, manufacturers are experimenting with recycled WC and low-Co alternatives. |