Material Innovations in Carbide Rod Industry Innovations
The Carbide Rod industry is undergoing a significant transformation, thanks to cutting-edge material innovations. Modern advancements have led to the development of ultra-fine, high-performance carbide powders that enhance wear resistance, toughness, and thermal stability.
One of the standout innovations in carbide materials is the use of nanostructured carbide powders. These materials improve the hardness and longevity of cutting tools, dies, and wear-resistant components. Binderless carbides have also gained traction, eliminating the need for cobalt or nickel binders, making them suitable for extreme environments like aerospace and medical applications.
Several key metal powder models have emerged as industry leaders:
- WC-10Co-4Cr: A tungsten carbide blend offering excellent corrosion and oxidation resistance.
- WC-12Co: High hardness and fracture toughness, making it ideal for wear parts and tools.
- TiC-NiMo: A titanium carbide blend used in high-speed machining.
- Cr3C2-NiCr: Superior oxidation and corrosion resistance, used in high-temperature applications.
- VC-WC-Co: Vanadium carbide-based powder that enhances cutting tool life.
- NbC-WC-Co: Niobium carbide powders that improve fracture toughness.
- WC-17Co: A tungsten carbide mix with enhanced thermal stability.
- Mo2C-WC-Co: Molybdenum carbide offering improved thermal shock resistance.
- ZrC-WC-Co: Zirconium carbide-infused tungsten carbide for superior hardness.
- HfC-WC-Co: Hafnium carbide-based powders used in extreme wear applications.
These materials have significantly influenced industries such as aerospace, automotive, oil & gas, and mining by enhancing performance, longevity, and efficiency.
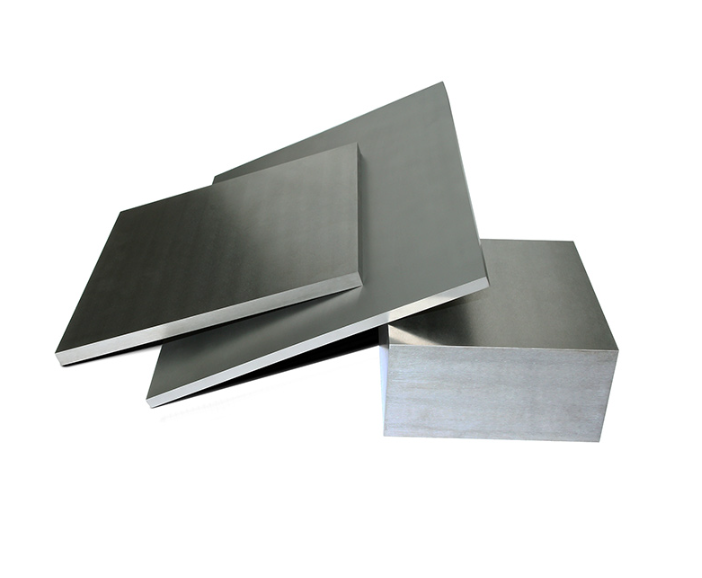
Manufacturing Process Innovations of Carbide Rod Industry Innovations
The evolution of carbide manufacturing techniques has streamlined production, reduced costs, and enhanced product performance. Traditional sintering methods are being replaced by more sophisticated technologies such as spark plasma sintering (SPS) and additive manufacturing (AM).
- Spark Plasma Sintering (SPS): This technique reduces sintering time and increases material density, improving mechanical properties.
- Hot Isostatic Pressing (HIP): This method eliminates internal porosity, enhancing material strength and fatigue resistance.
- Additive Manufacturing (3D Printing): 3D printing of carbide components allows for complex geometries and material efficiency.
- Nano-Coating Techniques: Coatings like TiAlN and AlCrN improve tool longevity and performance in harsh conditions.
- Cryogenic Treatment: Enhances carbide toughness and thermal stability by refining microstructures.
These advancements not only improve product quality but also enable the creation of customized carbide solutions tailored to specific industrial needs.
New Applications in Various Industries of Carbide Industry Innovations
Carbide Rod materials are seeing new applications across multiple industries, expanding beyond traditional cutting tools and wear parts.
- Aerospace: High-performance carbide components are used in turbine blades, nozzles, and structural reinforcements.
- Automotive: Carbide inserts improve engine efficiency and durability in fuel injection systems and valve seats.
- Oil & Gas: Carbide-based drill bits and wear-resistant coatings enhance drilling operations.
- Medical: Tungsten carbide surgical tools and implants provide exceptional wear resistance.
- Electronics: Carbide-based conductive materials are utilized in semiconductor manufacturing.
These new applications underscore the versatility of carbide materials and their expanding role in high-tech industries.
Smart Manufacturing & AI Integration of Carbide Industry Innovations
Technology | Impact on Carbide Manufacturing |
---|---|
AI-Driven Process Optimization | Enhances precision in carbide composition and reduces material waste. |
Automated Quality Control | Ensures consistent quality by detecting defects in real-time. |
Predictive Maintenance | Reduces machine downtime by forecasting maintenance needs. |
IoT-Enabled Supply Chain | Improves efficiency by tracking material movement and production progress. |
Robotic Assembly | Increases productivity and safety in carbide part manufacturing. |
FAQ
Question | Answer |
---|---|
What are the key benefits of using carbide materials? | Carbide offers superior hardness, wear resistance, and thermal stability, making it ideal for demanding applications. |
How does AI improve carbide manufacturing? | AI optimizes production processes, enhances quality control, and predicts maintenance needs. |
What industries benefit most from carbide innovations? | Aerospace, automotive, medical, oil & gas, and electronics industries extensively use carbide materials. |
What is the future of carbide manufacturing? | Advanced sintering techniques, AI integration, and sustainable materials will shape the industry’s future. |
How does 3D printing impact carbide production? | 3D printing allows for complex geometries and material efficiency, reducing waste. |