What Is Carbide Rod Hardness?
Carbide rods are essential components in cutting tools, wear parts, and industrial applications. Their hardness determines their durability, wear resistance, and overall performance. But what exactly is carbide rod hardness? In simple terms, hardness refers to a material’s ability to resist deformation, scratching, or penetration. Tungsten carbide, commonly used in carbide rods, achieves high hardness levels due to its unique composition of tungsten and carbon atoms bonded together to form a dense, crystalline structure.
The hardness of a carbide rod impacts its cutting performance, lifespan, and ability to withstand high-stress environments. However, hardness isn’t the only factor—toughness also plays a crucial role. A balance between hardness and toughness ensures that carbide rods don’t become too brittle under stress.
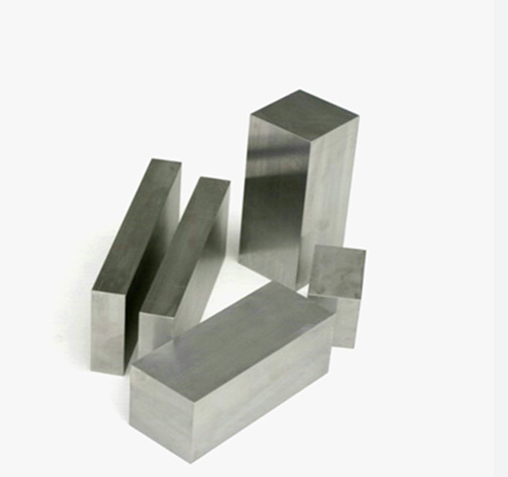
Common Hardness Scales for Carbide Rods
Carbide hardness is measured using different scales, depending on the testing method. The most common ones include:
Rockwell Hardness (HRA, HRB, HRC)
- Used primarily for metal hardness.
- HRA is often used for tungsten carbide.
- HRC applies more to hardened steel.
Vickers Hardness (HV)
- Utilizes a diamond pyramid to measure hardness.
- Commonly used for fine materials like carbide.
Mohs Hardness
- Ranks materials from 1 (talc) to 10 (diamond).
- Tungsten carbide typically scores around 9.
Knoop Hardness (HK)
- Used in microhardness testing for thin materials.
Each scale has its advantages, but for carbide rods, Rockwell (HRA) and Vickers (HV) are the most relevant.
Carbide Grades and Their Hardness
Carbide grades differ based on their cobalt content, grain size, and additional alloying elements. Below is a breakdown of some common carbide grades and their hardness levels:
Carbide Grade | Composition | Rockwell Hardness (HRA) | Vickers Hardness (HV) | Applications |
---|---|---|---|---|
YG6 | 94% WC, 6% Co | 90.5 | 1450 | General-purpose machining |
YG8 | 92% WC, 8% Co | 89.5 | 1350 | Heavy-duty cutting |
YG10 | 90% WC, 10% Co | 88.5 | 1300 | Impact-resistant applications |
YG15 | 85% WC, 15% Co | 86.0 | 1100 | High-impact applications |
YL10.2 | Fine-grained WC, 10% Co | 92.5 | 1600 | High wear resistance |
K10 | 94% WC, 6% Co | 91.0 | 1500 | Precision machining |
K20 | 92% WC, 8% Co | 89.5 | 1400 | General-purpose cutting |
K30 | 90% WC, 10% Co | 88.0 | 1300 | Rough machining |
G10 | Ultra-fine WC, 10% Co | 93.0 | 1650 | High precision tools |
C2 | 93% WC, 7% Co | 90.0 | 1450 | Wear-resistant parts |
Each grade has its advantages: lower cobalt content increases hardness, while higher cobalt content improves toughness.
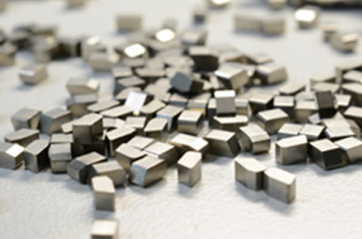
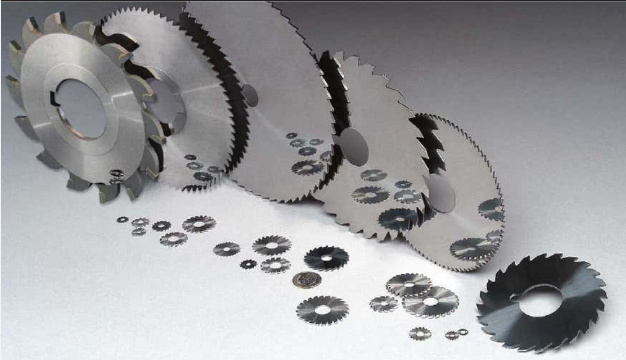
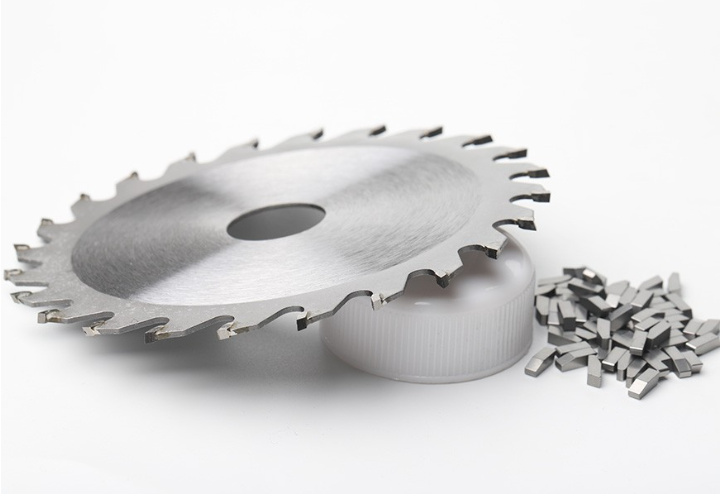
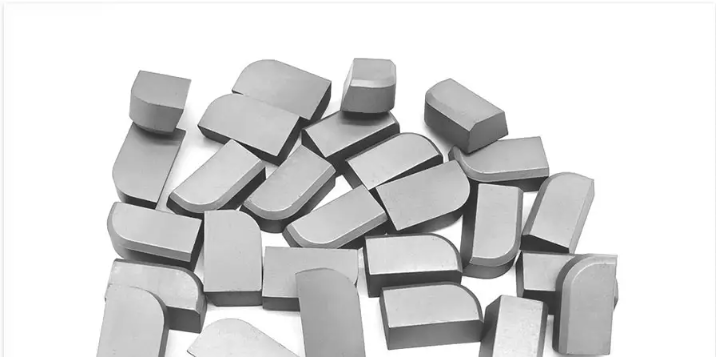
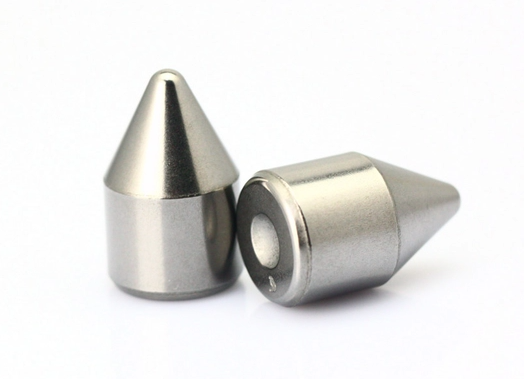
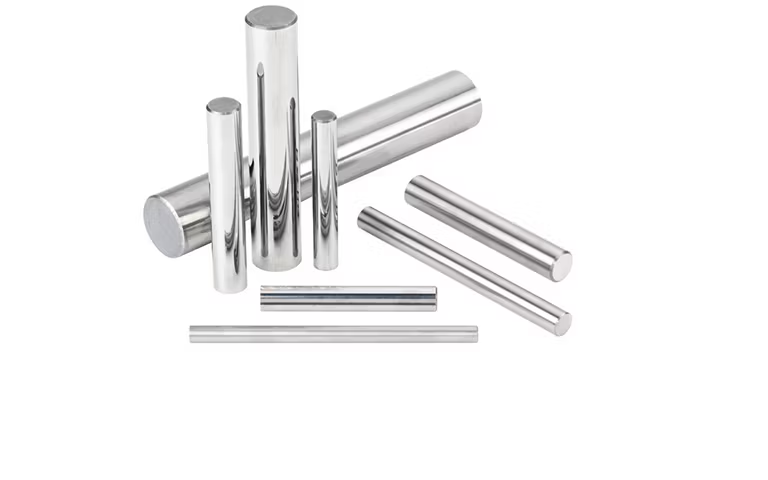
Hardness vs. Toughness: Which One Matters More?
Factor | High Hardness | High Toughness |
---|---|---|
Wear Resistance | Excellent | Moderate |
Impact Resistance | Low | High |
Cutting Edge Retention | Superior | Moderate |
Fracture Resistance | Low | Excellent |
Typical Applications | Precision machining | Heavy-duty applications |
High-hardness carbide rods last longer in wear-intensive applications but may chip under impact. Conversely, high-toughness rods resist breaking but may wear down faster.
How to Choose the Right Carbide Rod Based on Hardness?
Choosing the right carbide rod depends on your application needs. Consider the following:
Application | Recommended Hardness | Best Carbide Grades |
---|---|---|
High-speed cutting | 90+ HRA | YG6, K10, G10 |
Heavy-duty machining | 88-90 HRA | YG8, YG10, K20 |
Impact-resistant tools | 85-88 HRA | YG15, K30 |
Precision tools | 92+ HRA | YL10.2, G10 |
Wear-resistant parts | 90-93 HRA | C2, YG6, K10 |
Higher hardness is ideal for wear resistance, while lower hardness grades provide toughness for impact applications.

FAQ
Question | Answer |
---|---|
What is the hardest carbide rod? | Typically, ultra-fine grain carbide rods like G10 or YL10.2 have the highest hardness. |
How does carbide hardness compare to steel? | Carbide is significantly harder than steel, often exceeding HRC 65. |
Does higher hardness mean better performance? | Not always—higher hardness improves wear resistance but may reduce impact strength. |
How can I measure carbide rod hardness? | Rockwell (HRA) or Vickers (HV) tests are commonly used. |
What affects carbide hardness? | Grain size, cobalt content, and sintering process all influence hardness. |
Which carbide grade is best for high-impact use? | YG15 and K30 offer higher toughness for impact resistance. |
Can I sharpen carbide rods? | Yes, but specialized diamond grinding is required. |