Understanding Tungsten Carbide Plates
Tungsten carbide plates are essential in industrial applications requiring extreme hardness, wear resistance, and durability. Composed of tungsten carbide powder combined with a binder like cobalt or nickel, these plates exhibit high strength and performance, making them ideal for heavy-duty applications.
Application Areas of Tungsten Carbide Plates
Tungsten carbide plates are widely used across industries due to their unmatched durability. Some of the key application areas include:
- Molds and Dies: Used in stamping, forming, and extrusion dies for superior wear resistance.
- Cutting Tools: Essential in machining, drilling, and milling applications for long-lasting tool life.
- Wear-Resistant Parts: Applied in industrial machinery, mining tools, and agricultural equipment to withstand harsh environments.
- Aerospace and Defense: Used in high-performance components where strength and resistance to deformation are critical.
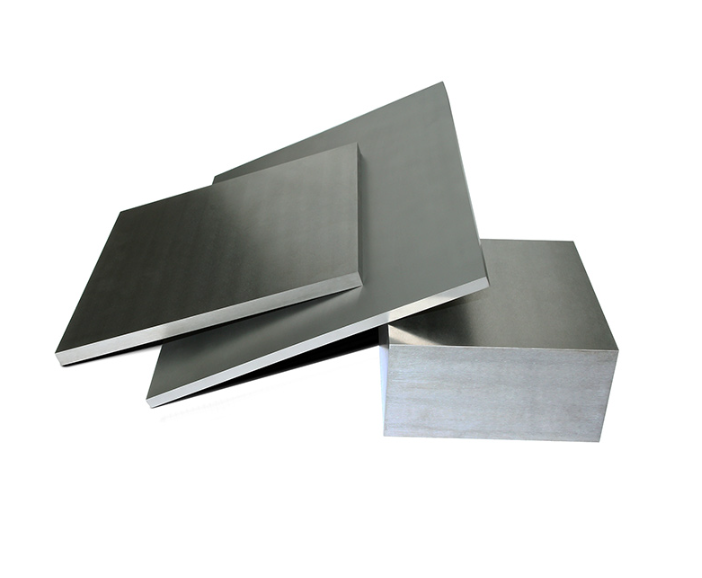
Why is Hardness Testing Necessary?
Hardness testing is crucial in ensuring the quality and performance of tungsten carbide plates. But why exactly does it matter?
- Ensures Quality Control: Detects inconsistencies in material composition.
- Enhances Service Life: Predicts how well the material will perform in real-world conditions.
- Compliance with Industry Standards: Meets regulations and certifications required for various applications.
Common Hardness Testing Methods for Carbide Plates
Various testing methods are used to measure the hardness of tungsten carbide plates. Below is a breakdown of the most commonly used techniques:
Testing Method | Principle | Best Suited For | Advantages | Disadvantages |
---|---|---|---|---|
Rockwell Hardness (HRA) | Measures indentation depth using a steel ball or diamond cone | General carbide testing | Fast and easy | Less precise for very hard materials |
Vickers Hardness (HV) | Uses a diamond pyramid to measure micro-hardness | Small and thin samples | Highly accurate | Time-consuming |
Knoop Hardness (HK) | Similar to Vickers but with an elongated diamond indenter | Ultra-thin coatings | Detailed surface analysis | Not suitable for bulk materials |
Brinell Hardness (HB) | Uses a tungsten carbide ball to indent material | Softer carbides | Good for large-grain structures | Not ideal for very hard carbides |
Mohs Hardness Test | Scratch test ranking materials from 1-10 | Quick comparative analysis | Simple and non-destructive | Lacks precision |
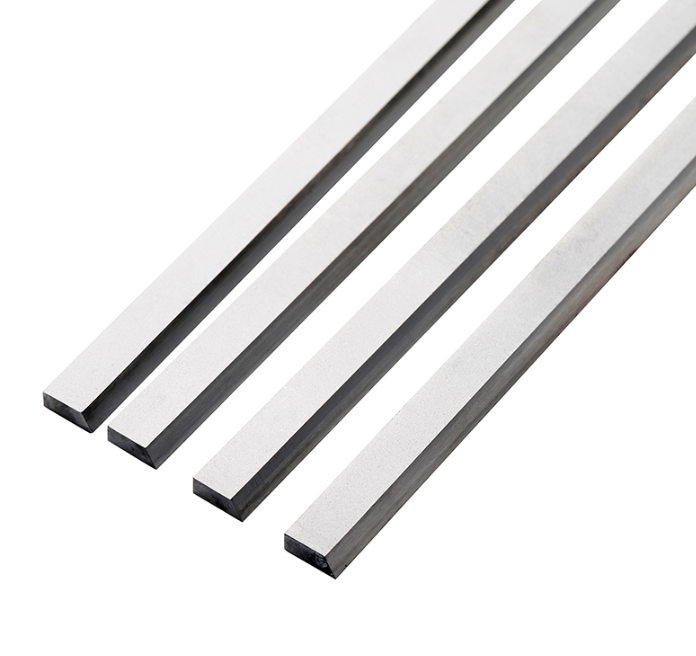
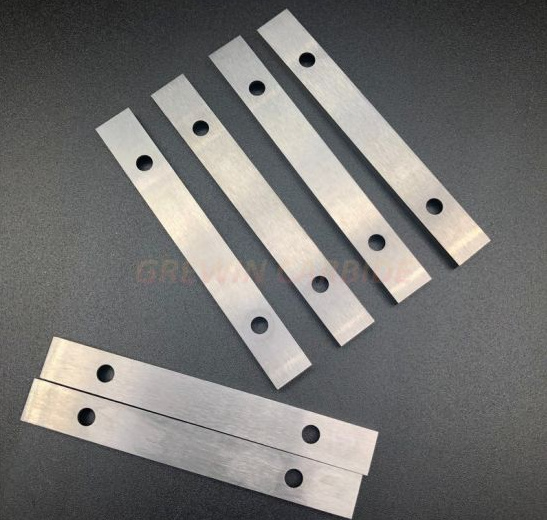
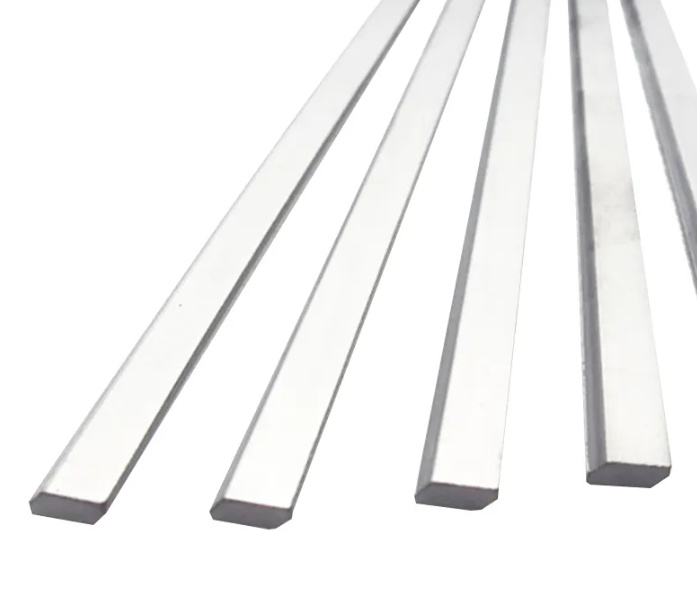
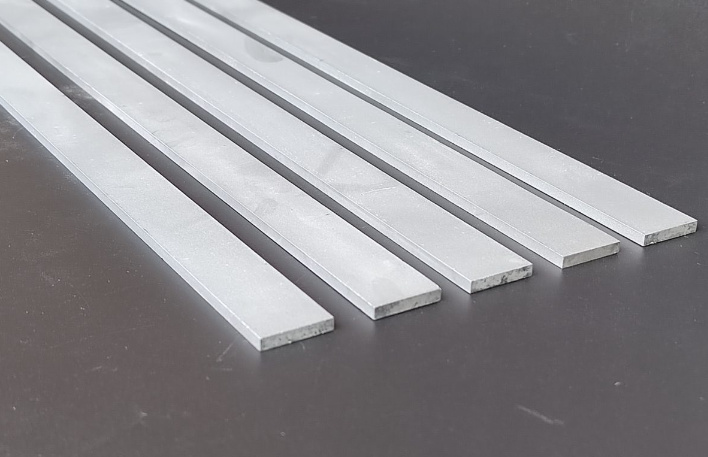
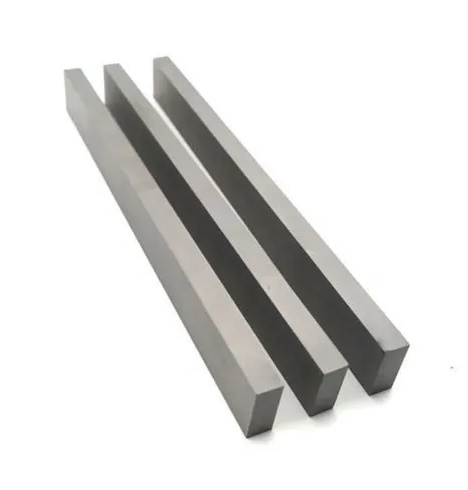
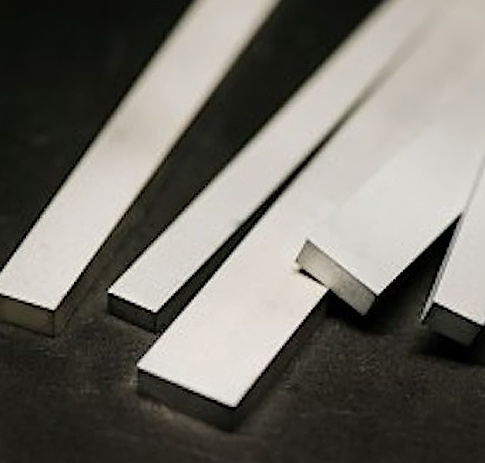
Factors Affecting Hardness Testing Accuracy
Many factors influence the accuracy of hardness testing for tungsten carbide plates. Here’s a closer look:
Factor | Impact on Testing |
---|---|
Material Composition | The presence of cobalt or nickel can influence test results. |
Surface Finish | A rough surface may lead to inconsistent readings. |
Testing Load | Higher loads may cause deeper indentations, affecting accuracy. |
Temperature Conditions | Extreme temperatures can alter material hardness. |
Operator Skill | Human error can introduce inconsistencies in manual tests. |
Industry Standards and Certifications for Hardness Testing
Ensuring compliance with industry standards is essential for carbide plate manufacturers. The most recognized standards include:
- ISO 6507 – Vickers hardness testing standards.
- ASTM E18 – Rockwell hardness testing standard.
- ISO 3878 – Testing procedures for cemented carbides.
- ASTM B294 – Hardness testing of cemented carbide materials.
How to Choose the Right Hardness Testing Method?
Selecting the right method depends on several factors, including material properties, application requirements, and testing precision. Here’s a quick guide:
- For general industrial applications: Rockwell (HRA) is the fastest and most commonly used.
- For microstructural analysis: Vickers (HV) provides the most detailed results.
- For large-grain structures: Brinell (HB) is ideal.
- For thin coatings or coatings analysis: Knoop (HK) is preferred.
Specific Metal Powder Models for Carbide Plates
Different tungsten carbide powder models influence plate hardness. Here are ten widely used models:
- WC-Co 94/6 – High toughness, ideal for impact applications.
- WC-Co 90/10 – Good balance between hardness and durability.
- WC-Co 85/15 – Higher cobalt content for increased toughness.
- WC-Ni 92/8 – Corrosion-resistant alternative to cobalt binders.
- WC-CoCr 88/12 – Enhanced resistance to oxidation.
- WC-VC 97/3 – Superior grain refinement for ultra-hard applications.
- WC-TiC-Co 92/8 – Improved thermal stability for high-speed machining.
- WC-TaC-Co 95/5 – Increased wear resistance in abrasive environments.
- WC-NbC-Co 93/7 – Better fracture toughness for demanding conditions.
- WC-ZrC-Co 91/9 – High strength and anti-corrosion properties.
FAQ
Question | Answer |
---|---|
What is the best method for carbide plate hardness testing? | Rockwell (HRA) is commonly used for general testing, while Vickers (HV) is preferred for microstructural analysis. |
How does cobalt content affect hardness? | Higher cobalt content increases toughness but reduces overall hardness. |
Can hardness testing damage carbide plates? | Most methods leave minor indentations but do not significantly affect performance. |
Why does temperature affect hardness testing? | Elevated temperatures can soften carbide, leading to inaccurate results. |
What certifications are required for carbide plates? | ISO 6507 (Vickers), ASTM E18 (Rockwell), and ISO 3878 (cemented carbide testing) are standard. |