When it comes to industrial applications, durability and performance are non-negotiable. Whether you’re in mining, construction, or manufacturing, the wear and tear on your equipment can make or break your operations. That’s where carbide wear parts come into play. These components are the unsung heroes of heavy-duty industries, offering unmatched resistance to abrasion, corrosion, and impact. But what exactly are carbide wear parts, and why are they so crucial?
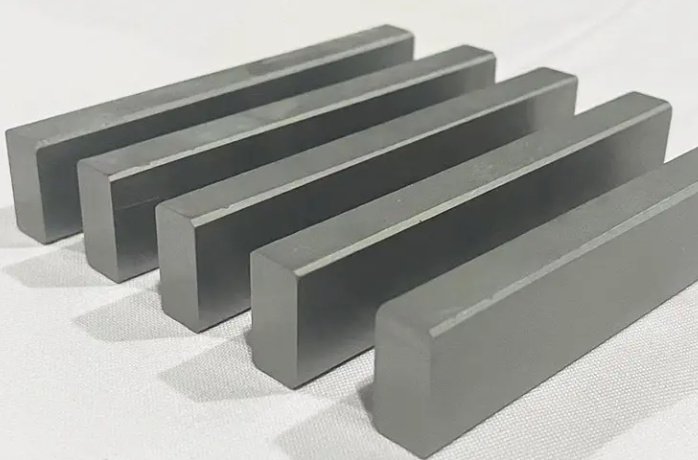
The Importance of Carbide Wear Parts
Imagine running a marathon in flip-flops. Sounds painful, right? That’s exactly what it’s like using subpar materials in high-stress industrial environments. Carbide wear parts are like the high-performance running shoes of the industrial world—they’re designed to withstand extreme conditions without breaking a sweat.
These parts are essential because they significantly extend the lifespan of machinery, reduce downtime, and improve overall efficiency. Think about it: if your equipment fails prematurely, you’re not just dealing with replacement costs; you’re also losing valuable time and productivity. Carbide wear parts act as a shield, protecting your machinery from the relentless forces of friction, heat, and pressure.
But why carbide? Well, carbide, particularly tungsten carbide, is a composite material made from tungsten and carbon. It’s incredibly hard—second only to diamonds—and offers exceptional wear resistance. This makes it ideal for applications where other materials would simply crumble under pressure.
Application Areas of Carbide Wear Parts
Carbide wear parts aren’t just for one industry—they’re versatile players in a wide range of fields. Here’s a quick rundown of where you’ll find these rugged components in action:
- Mining and Drilling: From drill bits to crusher parts, carbide components are essential for breaking through tough rock and mineral formations.
- Construction: Excavator teeth, bulldozer blades, and concrete cutters all benefit from the durability of carbide.
- Manufacturing: In industries like automotive and aerospace, carbide tools are used for cutting, shaping, and finishing metal parts.
- Agriculture: Plow blades, tiller teeth, and other farming equipment often rely on carbide for longevity.
- Oil and Gas: In the harsh environments of oil rigs and pipelines, carbide parts resist corrosion and wear.
These are just a few examples, but the list goes on. Essentially, if an industry involves heavy machinery and tough conditions, carbide wear parts are likely playing a critical role.
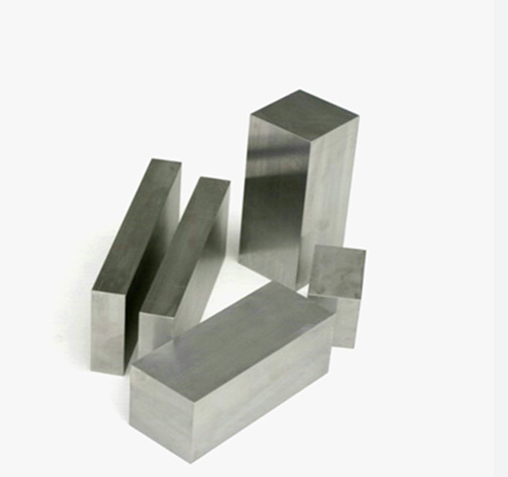

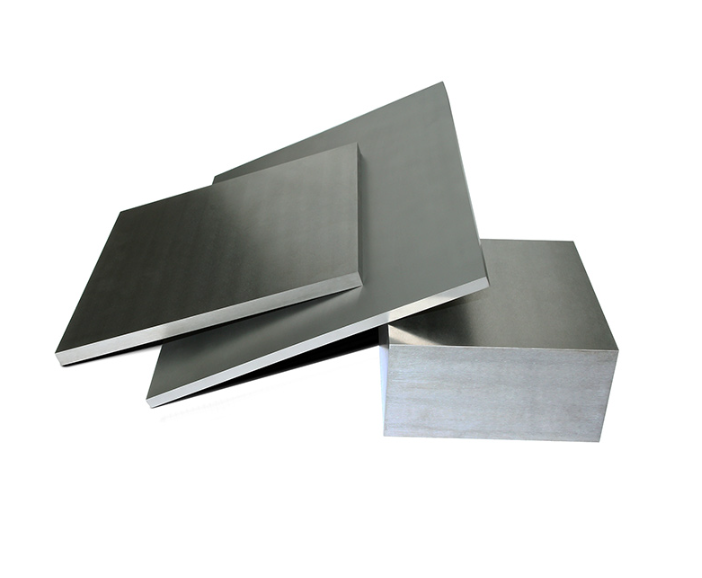
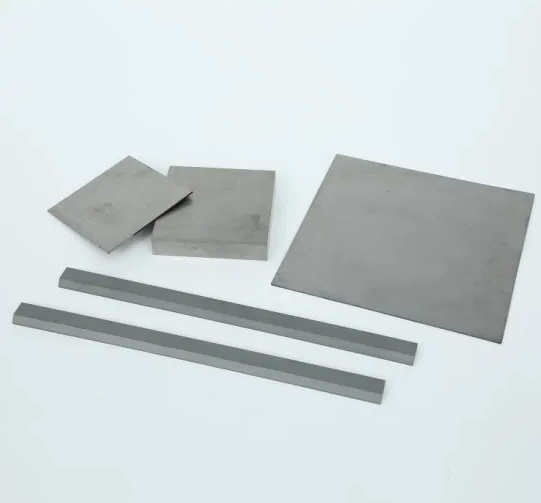
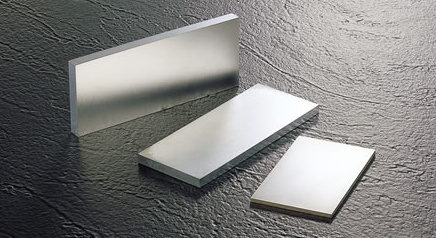
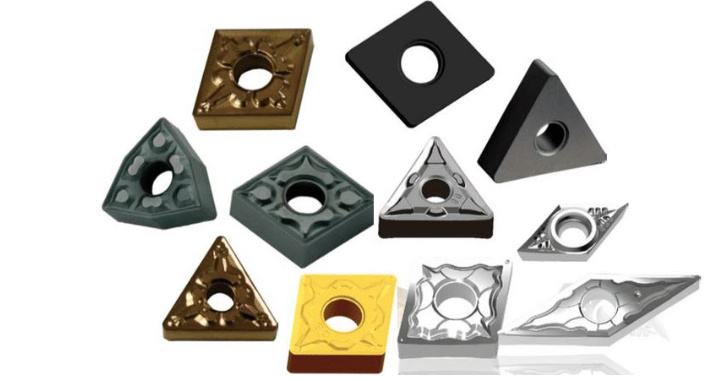
Why Choose Tungsten Carbide as a Wear-Resistant Component Material?
So, what makes tungsten carbide the go-to material for wear-resistant parts? Let’s break it down:
- Hardness: As mentioned earlier, tungsten carbide is incredibly hard. This means it can withstand abrasive forces that would wear down other materials in no time.
- Durability: It doesn’t just resist wear—it also holds up under extreme pressure and impact. This makes it perfect for high-stress applications.
- Corrosion Resistance: Unlike some metals, tungsten carbide doesn’t rust or corrode easily, even in harsh environments.
- Heat Resistance: It can handle high temperatures without losing its structural integrity, which is crucial for applications like metal cutting and drilling.
- Longevity: Thanks to its durability, carbide parts last significantly longer than those made from other materials, reducing the need for frequent replacements.
In short, tungsten carbide is like the superhero of materials—strong, resilient, and ready to tackle any challenge.
What Are Carbide Wear Parts?
To understand carbide wear parts better, let’s take a closer look at what they are and how they’re made.
Aspect | Description |
---|---|
Composition | Made from tungsten carbide particles bonded with a metal binder, usually cobalt. |
Manufacturing Process | Powder metallurgy: Tungsten and carbon powders are mixed, pressed, and sintered. |
Properties | High hardness, wear resistance, and toughness. |
Common Forms | Inserts, tips, blades, dies, and nozzles. |
Applications | Used in cutting tools, wear plates, and industrial machinery components. |
Advantages of Tungsten Carbide Wear Parts
Why should you choose tungsten carbide over other materials? Here’s a quick comparison:
Advantage | Description |
---|---|
Superior Wear Resistance | Outlasts steel and other materials in abrasive environments. |
High Strength | Can withstand extreme pressure and impact without cracking. |
Corrosion Resistance | Performs well in wet or chemically aggressive environments. |
Heat Tolerance | Maintains performance at high temperatures. |
Cost-Effective | Longer lifespan means fewer replacements and lower long-term costs. |
Applications of Carbide Wear Parts
Carbide wear parts are everywhere, but let’s zoom in on some specific applications:
- Drill Bits: Used in mining and oil drilling, carbide-tipped drill bits can cut through rock and metal with ease.
- Cutting Tools: In manufacturing, carbide inserts are used for precision cutting and shaping of metals.
- Wear Plates: These are used in conveyor systems and chutes to protect against abrasion.
- Nozzles: In industries like sandblasting, carbide nozzles resist wear from abrasive particles.
How to Choose the Best Carbide Wear Parts?
Choosing the right carbide wear parts can feel overwhelming, but here are some tips to guide you:
- Understand Your Needs: What kind of wear are you dealing with? Abrasion, impact, or corrosion?
- Material Quality: Look for high-quality tungsten carbide with a suitable binder (e.g., cobalt or nickel).
- Design and Fit: Ensure the part is designed for your specific application and fits your machinery perfectly.
- Supplier Reputation: Choose a reputable supplier with a track record of delivering durable, high-performance parts.
Carbide Wear Parts vs. Other Materials
How does carbide stack up against other materials? Let’s compare:
Material | Pros | Cons |
---|---|---|
Tungsten Carbide | Extremely hard, wear-resistant, durable. | More expensive upfront. |
Steel | Affordable, widely available. | Prone to wear and corrosion. |
Ceramics | Hard and wear-resistant. | Brittle and prone to cracking under impact. |
Plastics | Lightweight and corrosion-resistant. | Not suitable for high-stress applications. |
Specific Metal Powder Models for Carbide Wear Parts
When it comes to manufacturing carbide wear parts, the quality of the metal powder used is crucial. Here are 10 specific metal powder models, each with its unique properties:
Powder Model | Description |
---|---|
WC-6%Co | Tungsten carbide with 6% cobalt binder. Ideal for general-purpose wear parts. |
WC-10%Co | Higher cobalt content for improved toughness. |
WC-12%Co | Even tougher, suitable for high-impact applications. |
WC-15%Co | Maximum toughness, used in extreme conditions. |
WC-6%Ni | Nickel binder for better corrosion resistance. |
WC-10%Ni | Higher nickel content for highly corrosive environments. |
WC-6%Co-2%Cr | Chromium added for enhanced wear and corrosion resistance. |
WC-8%Co-2%Cr | Balanced toughness and wear resistance. |
WC-10%Co-4%Cr | High chromium content for maximum corrosion resistance. |
WC-12%Co-3%Cr | Combines toughness, wear resistance, and corrosion resistance. |
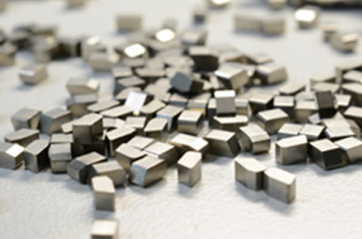
FAQ
Question | Answer |
---|---|
What are carbide wear parts? | Components made from tungsten carbide, known for their durability and wear resistance. |
Why choose tungsten carbide? | It’s extremely hard, wear-resistant, and durable, making it ideal for tough applications. |
How long do carbide wear parts last? | They last significantly longer than steel or other materials, reducing replacement frequency. |
Are carbide wear parts expensive? | They have a higher upfront cost but are cost-effective in the long run due to their longevity. |
Can carbide parts be repaired? | In some cases, yes, but it’s often more cost-effective to replace them. |