Cutting metal isn’t as simple as it sounds, is it? Choosing the right tools and materials can make or break your operation—literally. That’s why carbide for metal cutting is such a big deal in the manufacturing and machining industries. It’s durable, precise, and a game-changer when you need clean cuts and long-lasting tools. But what makes carbide so special? Let’s dig into the nitty-gritty details.
What Is Carbide for Metal Cutting?
Carbide, or more accurately tungsten carbide, is a compound made of tungsten and carbon. It’s incredibly hard and wear-resistant, making it ideal for cutting and machining metal. Often, cobalt or nickel is added as a binder to enhance toughness. The result? A material that’s stronger than steel and holds its cutting edge under extreme conditions.
If you’re wondering, “Why not just use steel?” the answer is simple: carbide tools cut faster, last longer, and deliver higher precision. Think of it as the difference between a butter knife and a chef’s knife—sure, both can cut, but one does the job better and with finesse.
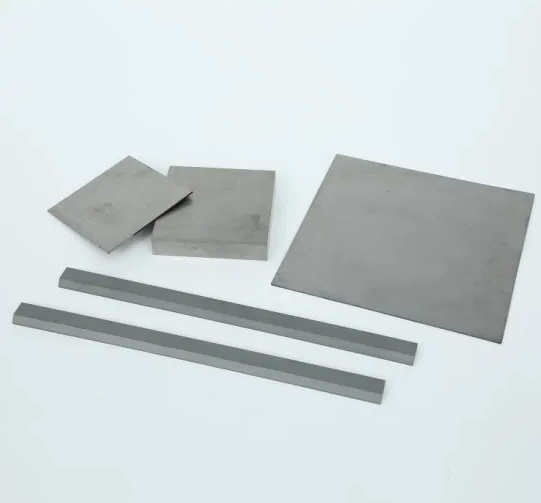
Types of Carbide for Metal Cutting
Not all carbide is created equal. Depending on your application, you might need a different type of carbide with specific properties. Here’s a detailed table of common types and their uses:
Type of Carbide | Composition | Applications | Key Benefits |
---|---|---|---|
Tungsten Carbide (WC) | Tungsten + Carbon | General-purpose cutting, wear-resistant tools | High hardness, excellent wear resistance |
Titanium Carbide (TiC) | Titanium + Carbon | Cutting high-strength alloys | Heat resistance, maintains sharp edges |
Tantalum Carbide (TaC) | Tantalum + Carbon | High-temperature cutting | Superior thermal stability |
Cermet | Ceramic + Metallic Binder | Fine finishing tasks | Smooth surface finish, reduced wear |
Submicron Grain Carbide | Ultra-fine tungsten carbide | Micro-machining and intricate cuts | Exceptional precision, longer tool life |
Coated Carbide | Carbide with PVD or CVD Coating | Cutting ferrous and non-ferrous metals | Improved toughness, reduced friction |
Dual Carbide Grade | Two layers of carbide | Heavy-duty cutting | Combines wear resistance and toughness |
Raw Material and Composition Analysis of Carbide for Metal Cutting
Carbide starts with two primary ingredients: tungsten and carbon. These are combined under high pressure and temperature to form tungsten carbide, one of the hardest materials known to man. To enhance its properties, binders like cobalt or nickel are added. Let’s break down the typical composition:
Component | Percentage Range | Function |
---|---|---|
Tungsten Carbide | 70% – 97% | Provides hardness and wear resistance |
Cobalt or Nickel | 3% – 30% | Acts as a binder, adding toughness |
Other Additives | <5% | Improves specific properties like heat resistance |
The balance of these elements determines the carbide’s properties, such as hardness, toughness, and thermal stability.
Production Process Flow of Carbide for Metal Cutting
How do you turn raw materials into cutting-edge carbide tools? It’s a meticulous process:
- Powder Mixing: Tungsten, carbon, and binders are mixed to form a uniform powder.
- Compacting: The powder is pressed into shapes under high pressure.
- Sintering: These preforms are heated in a furnace to bond the materials, creating a dense and solid structure.
- Shaping and Finishing: The sintered parts are ground to precise dimensions and sometimes coated for additional properties.
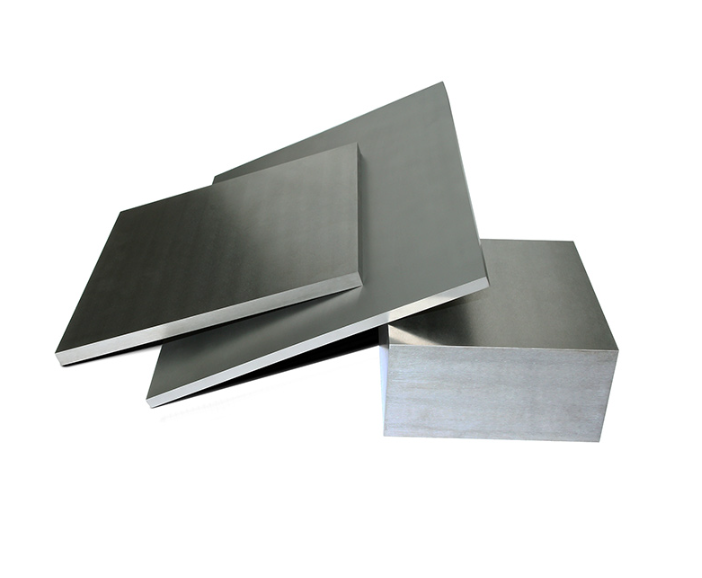
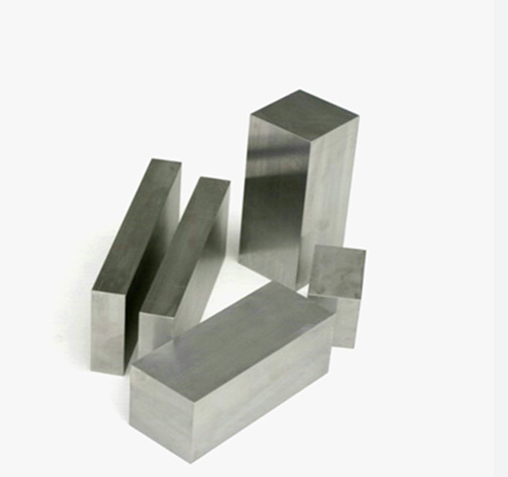
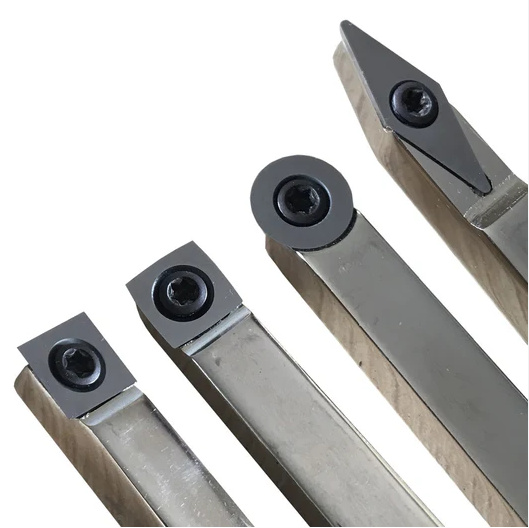
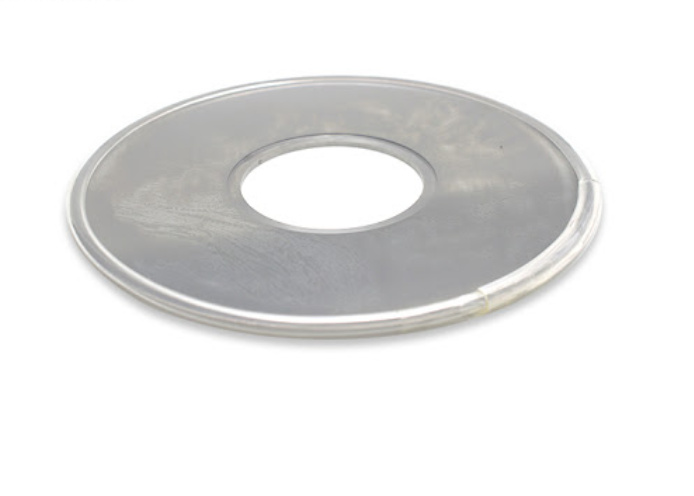
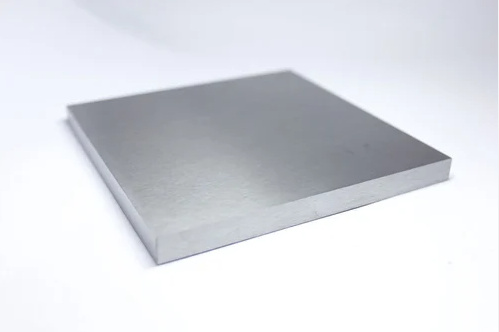
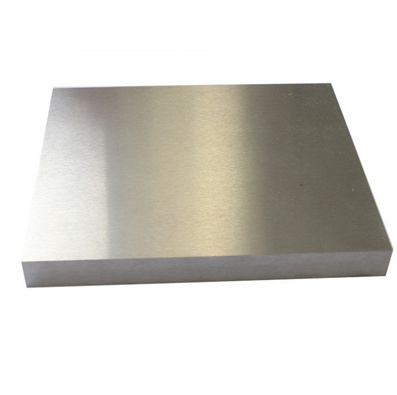
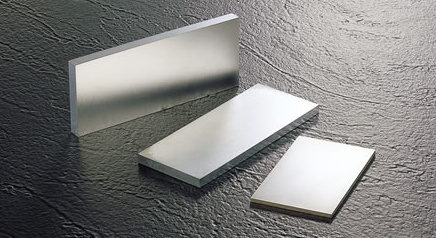
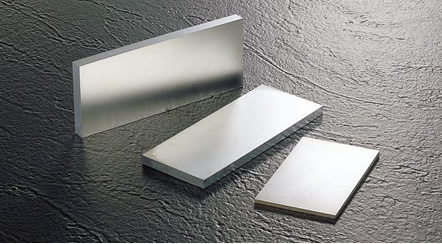
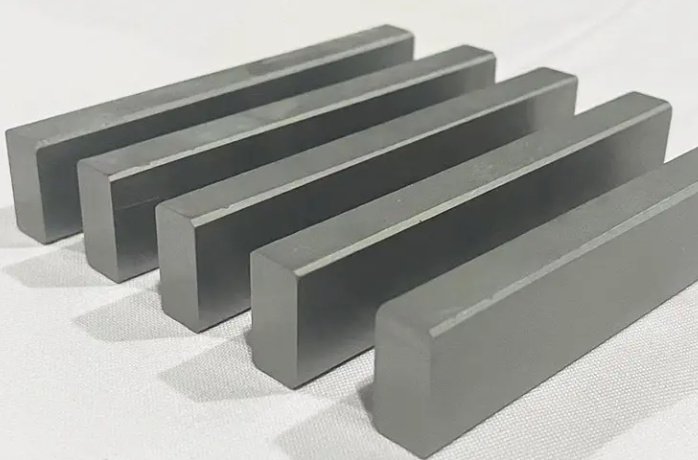
Applications of Carbide for Metal Cutting
Carbide tools are versatile and used across various industries. Here’s a table summarizing their applications:
Industry | Application | Examples |
---|---|---|
Automotive | Engine part machining | Cylinder heads, crankshafts, gears |
Aerospace | High-strength alloy cutting | Turbine blades, structural components |
Medical Devices | Precision tooling | Surgical instruments, implants |
Construction | Hard material cutting | Concrete drilling, masonry cutting |
Oil and Gas | Drilling tools and wear parts | Drill bits, valve trims |
Electronics | Micro-component manufacturing | Circuit boards, connectors |
Material Properties of Carbide for Metal Cutting
Here’s a quick look at the remarkable properties of carbide:
Property | Value Range | Importance |
---|---|---|
Hardness | 1600 – 2000 HV (Vickers Scale) | Ensures wear resistance and durability |
Density | 14.0 – 15.7 g/cm³ | Contributes to stability during machining |
Melting Point | ~2870 °C | Allows high-temperature applications |
Compressive Strength | ~6000 MPa | Handles extreme cutting forces |
Thermal Conductivity | 50 – 100 W/mK | Dissipates heat efficiently during cutting |
Specifications, Sizes, and Shapes of Carbide Tools
Carbide cutting tools come in various specifications tailored to different applications. Here’s an overview:
Specification | Details |
---|---|
Standard Shapes | Round, square, triangular, custom |
Size Range | Diameter: 1 mm – 100 mm |
Coating Options | Titanium Nitride (TiN), Titanium Carbonitride (TiCN) |
Tolerances | As low as ±0.001 mm |
Cutting Edge Styles | Single-edge, double-edge, multi-flute |
Choosing a Carbide for Metal Cutting Supplier
Not all suppliers are equal. Here’s what to look for:
Factor | What to Check |
---|---|
Quality Standards | ISO certifications, material traceability |
Customization Options | Ability to create tailored tools |
Pricing | Competitive rates without quality compromise |
Delivery Times | Reliable lead times for manufacturing needs |
Support Services | Technical guidance, post-sales support |
Selecting the Right Carbide for Your Needs
Choosing the right carbide tool depends on your specific requirements. Consider:
Criteria | Key Questions |
---|---|
Material Being Cut | Is it steel, aluminum, or a superalloy? |
Cutting Conditions | High-speed or low-speed machining? |
Desired Finish | Do you need a smooth surface or rough cuts? |
Budget Constraints | What’s your cost-to-benefit ratio? |
Tool Life Expectations | How long do you need the tool to last? |
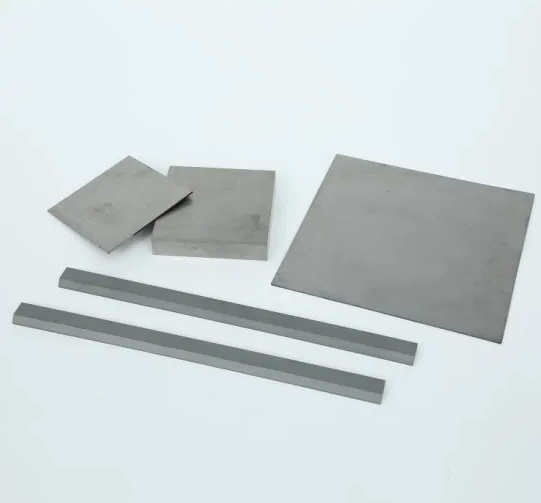
Advantages and Limitations of Carbide for Metal Cutting
Advantages | Limitations |
---|---|
Superior hardness and wear resistance | Higher upfront cost |
Maintains sharpness under extreme conditions | Brittle compared to steel |
Faster cutting speeds | Requires precise handling |
Versatile for different applications | Limited flexibility in shaping complex parts |
FAQs
Question | Answer |
---|---|
What is carbide’s biggest advantage? | Its superior hardness and wear resistance. |
Can carbide tools be reused? | Yes, they can often be resharpened. |
Are coated carbides better? | Yes, coatings improve durability and heat resistance. |
How do I maintain carbide tools? | Use proper cooling and avoid unnecessary shocks. |
What industries benefit the most from carbide? | Aerospace, automotive, and medical devices. |
Carbide for metal cutting is a marvel of engineering, offering precision, durability, and efficiency. Whether you’re crafting intricate micro-components or cutting through tough alloys, there’s a carbide tool designed for your needs. The key is knowing your requirements and selecting the right tool and supplier.