Carbide materials are the unsung heroes of modern engineering, renowned for their exceptional wear resistance and versatility. But what exactly makes them so special? Let’s dive into the fascinating world of carbide wear resistance, exploring its raw materials, composition, production process, applications, and more. We’ll even break down the best options in detailed tables, making this guide both educational and practical.
Understanding Wear Resistance of Carbide
Wear resistance refers to the ability of a material to withstand surface degradation due to mechanical friction, abrasion, or chemical interactions. Carbide, known for its durability, sets the gold standard in applications where longevity and toughness are non-negotiable.
Types of Wear Resistance in Carbide
Type | Description |
---|---|
Abrasive Wear Resistance | Resists damage from hard particles or surfaces rubbing against the carbide. |
Adhesive Wear Resistance | Prevents material transfer or sticking under high pressure or temperature. |
Corrosive Wear Resistance | Endures chemical attacks or oxidation in aggressive environments. |
Impact Wear Resistance | Absorbs and dissipates shock from repetitive strikes or heavy impacts. |
Erosive Wear Resistance | Stands up to material loss from high-speed particles or fluid impacts. |
Each type serves unique applications, but carbide’s innate versatility often combines several wear-resistant properties.
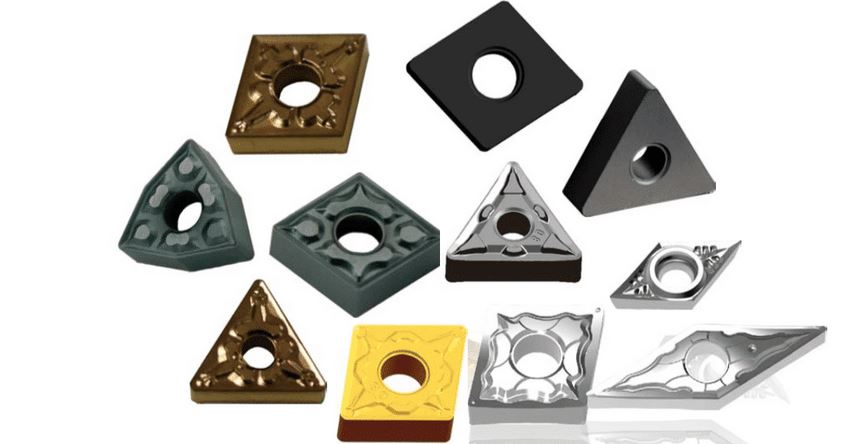
Raw Materials and Composition of Carbide Wear Resistance
Carbide primarily consists of tungsten carbide (WC) particles bound together by a metallic binder like cobalt (Co). The ratio of these components determines key material properties such as hardness, toughness, and wear resistance.
Key Components:
- Tungsten Carbide (WC): The primary constituent, known for its exceptional hardness.
- Cobalt (Co): A metallic binder offering toughness and flexibility.
- Other Additives: Tantalum carbide (TaC), titanium carbide (TiC), and nickel (Ni) enhance specific properties like corrosion resistance or thermal stability.
The magic lies in balancing these components for the intended application.
Applications of Wear-Resistant Carbide
Carbide materials are indispensable in industries where durability and precision are crucial. Here’s a snapshot of where carbide shines:
Industry | Application Examples |
---|---|
Mining and Drilling | Rock-cutting tools, drill bits, and wear plates. |
Metalworking | Cutting tools, punches, dies, and mill rolls. |
Aerospace | Abrasion-resistant seals and components for high-stress environments. |
Oil and Gas | Nozzles, valves, and wear-resistant bearings. |
Automotive | Engine components, wear-resistant gears, and shafts. |
Construction | Wear plates for heavy machinery and tools for stone cutting. |
These applications highlight the versatility of carbide, proving it’s more than just a hard material—it’s a cornerstone of modern engineering.
Production Process Flow of Wear-Resistant Carbide
Creating wear-resistant carbide is a sophisticated process involving several steps:
- Powder Preparation: Tungsten and cobalt powders are milled to achieve uniform particle size and composition.
- Mixing and Pressing: The powders are mixed with binders and compacted into the desired shape under high pressure.
- Sintering: The pressed parts are heated to just below their melting point, creating a dense, strong material.
- Post-Processing: Grinding, polishing, or coating enhances surface properties for specific applications.
- Quality Control: Rigorous testing ensures the material meets the required wear resistance standards.
This meticulous process explains why carbide is unparalleled in performance.
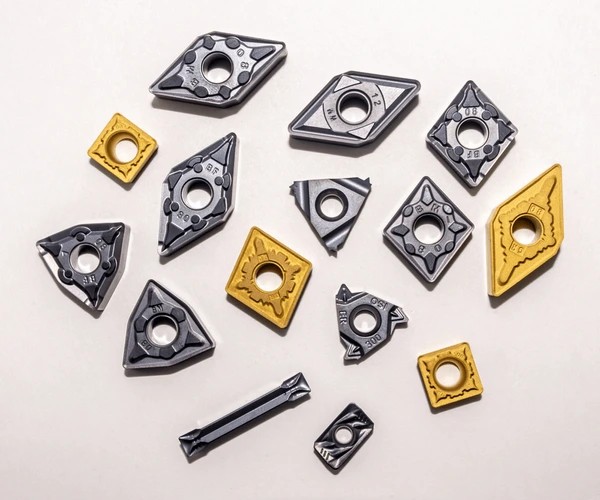
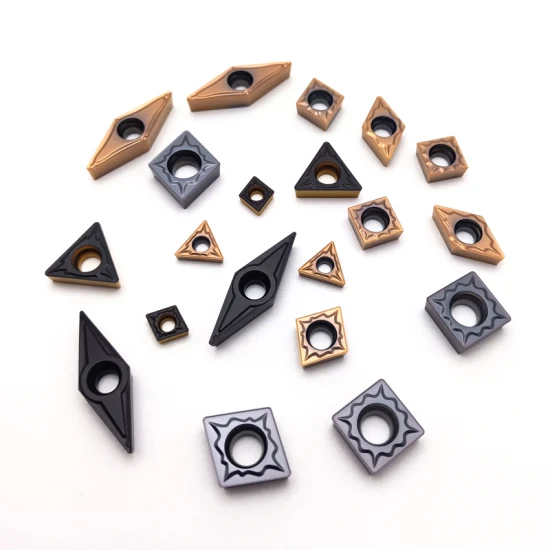
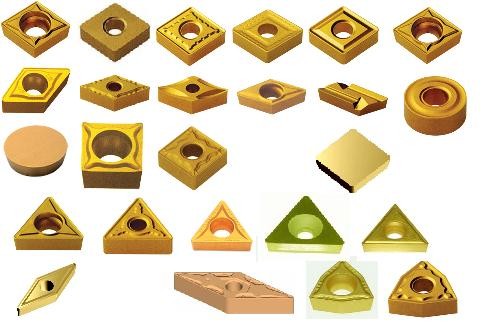
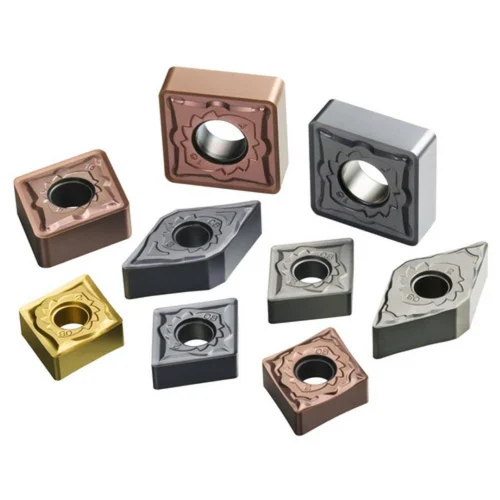
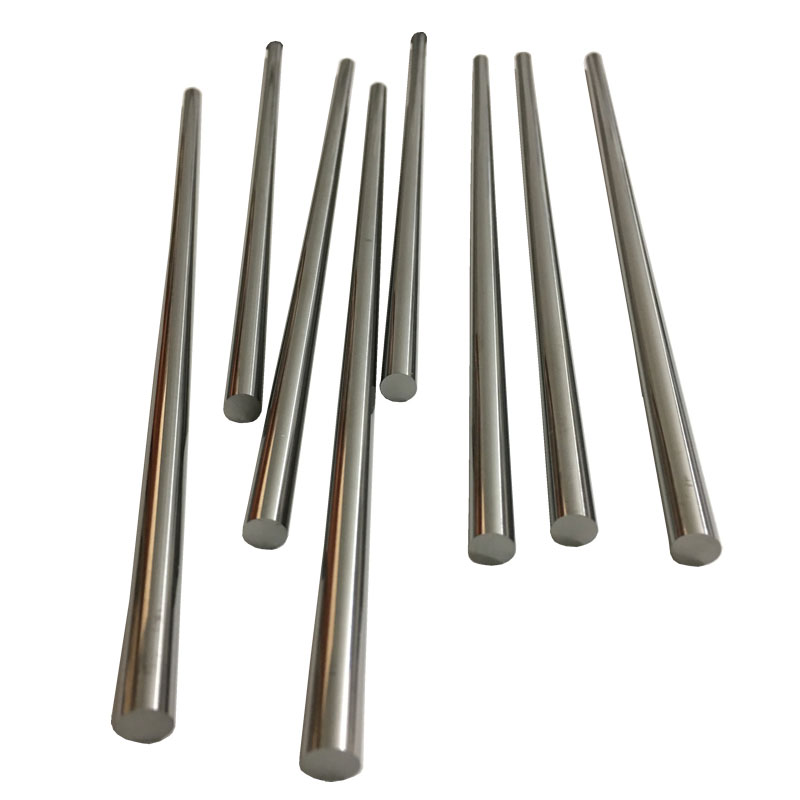
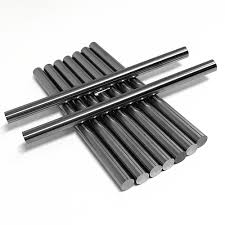
Material Properties of Carbide Wear Resistance
Property | Value Range | Impact on Wear Resistance |
---|---|---|
Hardness (HV) | 1500-2200 | Higher hardness resists abrasive wear. |
Fracture Toughness (MPa·m^1/2) | 7-20 | Balances resistance to cracking under high stress. |
Density (g/cm³) | 14.5-15.5 | Indicates material compactness, correlating with strength. |
Binder Content (%) | 5-20 | Lower binder increases hardness; higher binder improves toughness. |
Wear Rate (mm³/Nm) | 0.01-0.1 | Lower values indicate better wear resistance. |
Composition, Properties, and Characteristics
Composition | Hardness | Toughness | Wear Resistance | Applications |
---|---|---|---|---|
WC-6%Co | High | Medium | Excellent | Cutting tools, wear-resistant parts |
WC-10%Co | Medium | High | Good | Mining tools, high-impact parts |
WC-12%Co + TaC/TiC | Medium | High | Excellent | Aerospace components |
WC-Ni | High | Low | Excellent | Corrosion-resistant parts |
Hardness, Strength, and Wear Resistance
Grade | Hardness (HV) | Fracture Toughness (MPa·m^1/2) | Wear Resistance |
---|---|---|---|
WC-6%Co | 1800 | 9 | Excellent |
WC-10%Co | 1500 | 12 | Good |
WC-12%Ni | 1700 | 7 | Excellent |
Specifications, Sizes, Shapes, and Standards
Parameter | Options |
---|---|
Standard Sizes | Rods (3mm-50mm), Plates (1mm-20mm thickness), Custom shapes |
Shapes | Cylinders, squares, hexagons, custom precision parts |
Surface Finish | Ground, polished, or coated with TiN, TiC, or diamond layers |
Standards Compliance | ISO 513, ISO 9001, ASTM B777, DIN ISO 3874 |
Suppliers and Pricing Details
Supplier | Region | Pricing (per kg) | Specialty |
---|---|---|---|
Sandvik | Global | $50-$80 | Cutting tools, wear parts |
Kennametal | North America | $45-$90 | High-performance alloys |
Zhuzhou Cemented Carbide | China | $30-$70 | Cost-effective custom grades |
Selecting the Right Wear-Resistant Carbide
Criteria | Recommended Grade | Why? |
---|---|---|
High Abrasion | WC-6%Co | Outstanding hardness for abrasive conditions. |
High Impact | WC-10%Co | Superior toughness against mechanical shock. |
Corrosion Resistance | WC-12%Ni | Excellent in chemically aggressive settings. |
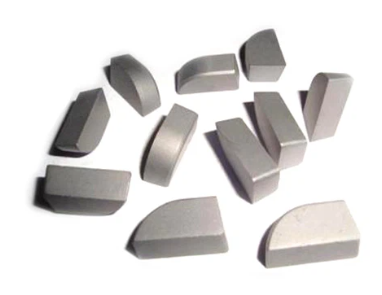
Advantages and Limitations of Wear-Resistant Carbide
Advantages | Limitations |
---|---|
Exceptional hardness and durability | High initial cost |
Versatility across industries | Brittle under extreme tensile stress |
Long service life | Requires precision manufacturing |
FAQs
Question | Answer |
---|---|
What is carbide wear resistance? | The ability of carbide materials to resist degradation under mechanical or chemical stress. |
What industries use wear-resistant carbide? | Mining, metalworking, aerospace, automotive, oil and gas, and more. |
How do I choose the right carbide grade? | Consider application-specific factors like abrasion, impact, and corrosion resistance. |
Wear-resistant carbide is more than just a durable material—it’s the backbone of countless industries. By understanding its properties, composition, and applications, you can make informed decisions for your projects, ensuring both performance and longevity. Ready to pick the perfect carbide for your needs?