In the world of high-performance materials, customized carbide solutions stand out for their durability, adaptability, and superior mechanical properties. Whether you’re in aerospace, automotive, mining, or any other demanding industry, carbide components often become the backbone of precision engineering. In this guide, we’ll dive deep into the world of customized carbide solutions—what they are, how they’re made, and why they matter. Let’s unravel the science and art of tailoring carbide to meet specific needs.
What Are Customized Carbide Solutions?
Customized carbide solutions are tailored engineering components made from tungsten carbide (WC) powders mixed with binders like cobalt or nickel. These materials are highly valued for their exceptional hardness, wear resistance, and strength. What makes them “customized”? The ability to tweak properties such as toughness, grain size, or binder percentage to fit specific applications.
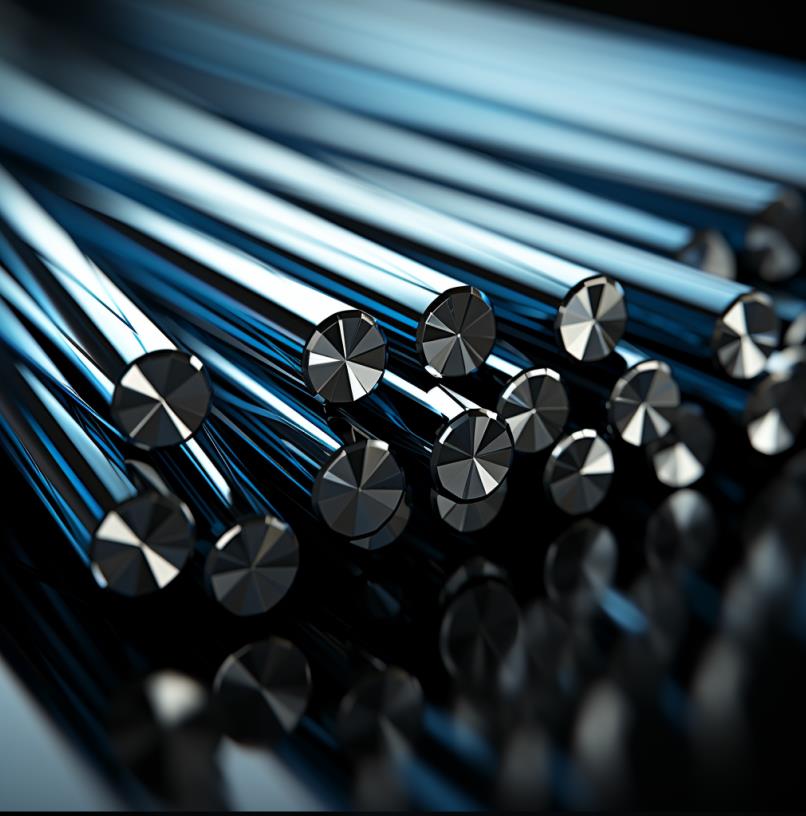
Types of Customized Carbide Solutions
Type | Description | Key Applications |
---|---|---|
Tungsten Carbide-Cobalt | Combines tungsten carbide with cobalt for strength and moderate toughness. | Mining tools, cutting tools |
Tungsten Carbide-Nickel | Resistant to corrosion; excellent in harsh environments. | Chemical processing, oil & gas industries |
Ultrafine Carbide | Features ultra-small grain sizes for high precision and extreme wear resistance. | Microdrills, electronics |
Reinforced Carbide | Includes additives like titanium carbide for increased performance. | High-speed machining |
Corrosion-Resistant Carbide | Uses nickel or chromium binders to resist oxidation and chemical attack. | Marine environments, aggressive chemicals |
Heavy-Duty Carbide | Designed for maximum toughness and fracture resistance. | Mining, crushing, earth-moving equipment |
Ceramic Carbide Hybrids | Combines ceramics for lightweight yet hard-wearing solutions. | Aerospace, advanced robotics |
Thermally Stable Carbide | Engineered for high-temperature environments. | Jet engines, thermal management systems |
Recycled Carbide | Sustainable option using reclaimed materials without compromising quality. | General industrial use |
Nanostructured Carbide | Advanced technology featuring nanoscale grains for extreme precision and wear properties. | Specialized medical instruments, high-tech devices |
Raw Materials and Composition Analysis
Core Ingredients in Customized Carbide Solutions
- Tungsten Carbide (WC): The primary ingredient, offering unparalleled hardness and wear resistance.
- Binder Metals (Cobalt, Nickel): Enhances toughness and binds the carbide grains together.
- Additives: Small quantities of materials like titanium carbide (TiC) or tantalum carbide (TaC) improve thermal stability or wear resistance.
Importance of Material Purity
The quality of carbide components starts with the purity of the raw powders. Impurities can lead to brittleness, inconsistent performance, or shortened lifespan. Advanced material analysis techniques, including X-ray diffraction (XRD) and electron microscopy, ensure the precise composition of powders.
Applications of Customized Carbide Solutions
Industry | Common Applications |
---|---|
Mining | Drill bits, cutting tools, wear-resistant components. |
Aerospace | Heat-resistant parts, lightweight hybrids for engines. |
Oil & Gas | Sealing rings, corrosion-resistant valves, directional drilling tools. |
Medical | Surgical tools, dental drills, and precision cutters. |
Automotive | Wear-resistant gears, high-speed machining tools, fuel injection systems. |
Construction | Rock crushing tools, hammers, and chisels. |
Industrial Manufacturing | Dies, punches, and cutting blades for production lines. |
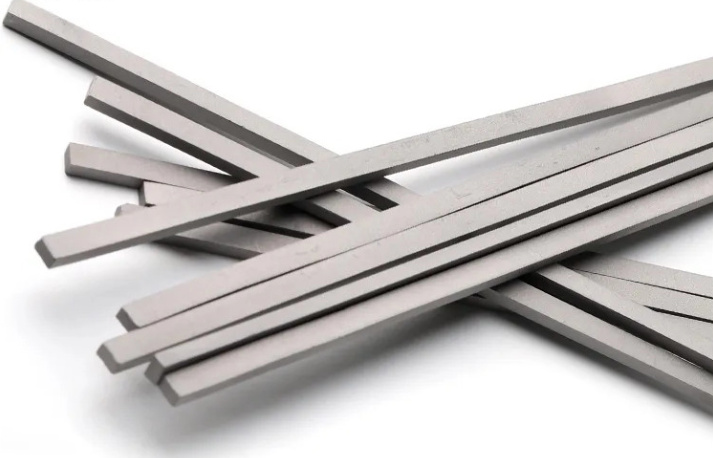
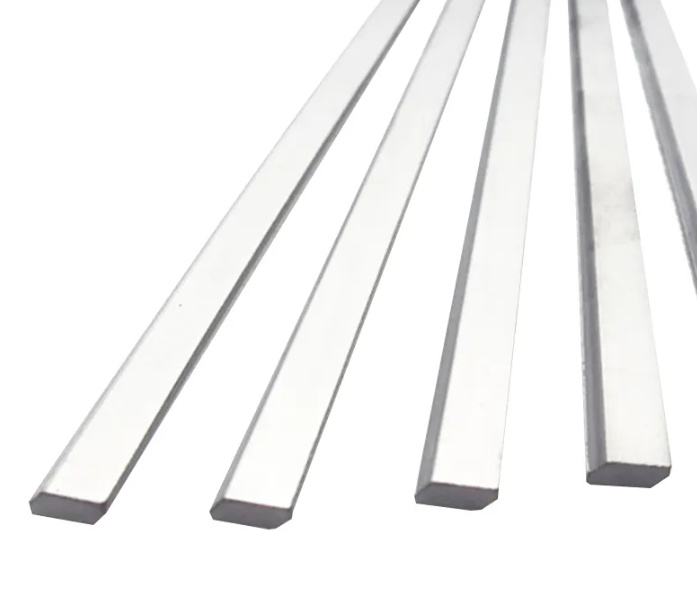
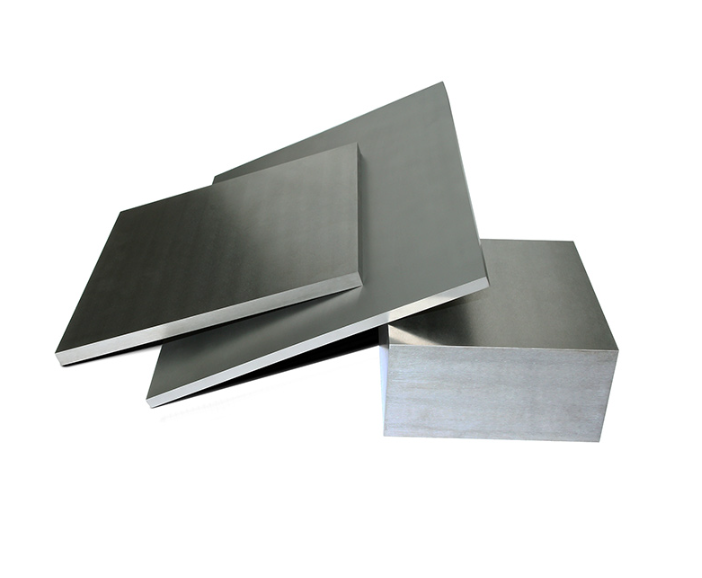
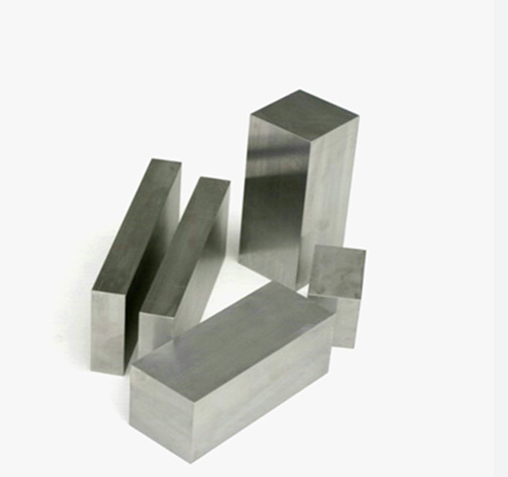
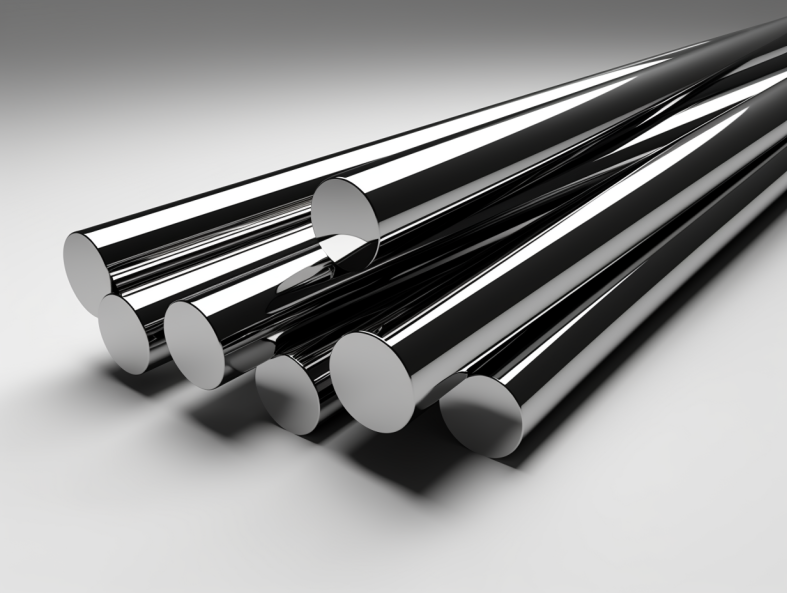
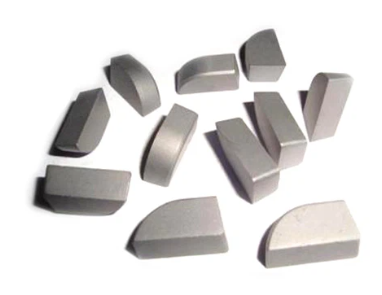
Production Process Flow
- Powder Preparation: Blending tungsten carbide powders with binders and additives.
- Mixing & Milling: Homogeneous distribution of ingredients to achieve consistent properties.
- Pressing: Compaction into desired shapes using isostatic or uniaxial presses.
- Sintering: Heating in a controlled atmosphere to densify the material and enhance its properties.
- Finishing: Grinding, lapping, and coating processes to achieve precise dimensions and surfaces.
Material Properties of Customized Carbide Solutions
Property | Value Range | Impact |
---|---|---|
Hardness (HV) | 800–2000 | Determines resistance to wear and abrasion. |
Fracture Toughness (MPa·m1/2) | 6–15 | Higher values mean better crack resistance. |
Density (g/cm³) | 13.5–15.5 | Affects weight and stability. |
Thermal Conductivity (W/m·K) | 80–120 | Efficiency in heat dissipation. |
Elastic Modulus (GPa) | 500–700 | Indicates stiffness and resistance to deformation. |
Composition, Properties, and Characteristics
Composition | Properties | Characteristics |
---|---|---|
WC + 6% Co | High hardness, moderate toughness. | Ideal for cutting tools. |
WC + 12% Co | Improved toughness, slightly lower hardness. | Suitable for mining tools. |
WC + 10% Ni | Corrosion-resistant, wear-resistant. | Best for chemical applications. |
WC + TiC + Co | Enhanced thermal stability. | Useful for high-speed machining. |
Recycled Carbide + Co | Environmentally friendly, cost-effective. | Retains excellent mechanical properties. |
Hardness, Strength, and Wear Resistance
Property | Range | Influence on Performance |
---|---|---|
Hardness (HV) | 850–2000 | Wear resistance improves with higher values. |
Transverse Rupture Strength | 1500–4000 MPa | Indicates load-bearing capacity. |
Wear Resistance | High/Medium/Low | Depends on grain size and binder percentage. |
Specifications, Sizes, Shapes, and Standards
Specification | Detail |
---|---|
Sizes | Standard: 0.5mm to 50mm; Custom: On request. |
Shapes | Round, rectangular, irregular, or application-specific. |
Standards | ISO 513, ANSI B94.25M, JIS B 4405. |
Suppliers and Pricing Details
Supplier | Region | Price Range ($/kg) | Specialties |
---|---|---|---|
ABC Carbide Ltd. | North America | $50–$120 | Custom shapes, rapid prototyping. |
Global Carbides Inc. | Europe | $60–$140 | Corrosion-resistant grades. |
Asia Metals Group | Asia-Pacific | $40–$100 | Competitive pricing for bulk orders. |
How to Select the Right Customized Carbide Solution
Factor | Considerations |
---|---|
Application | Prioritize hardness for wear, toughness for impact resistance. |
Environment | Corrosion-resistant grades for chemical exposure or marine use. |
Budget | Opt for recycled carbide or standard grades for cost-sensitive projects. |
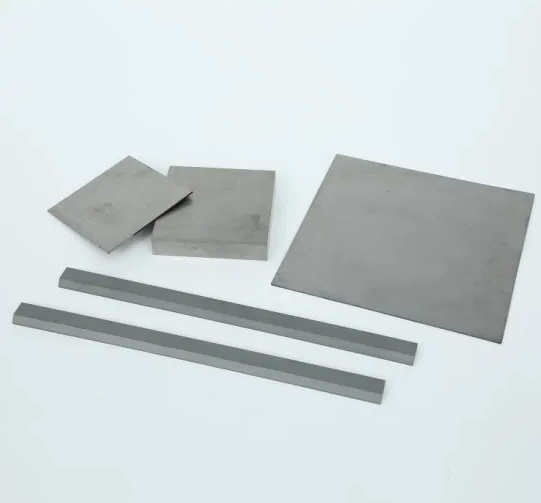
Comparing Advantages and Limitations
Aspect | Advantages | Limitations |
---|---|---|
Hardness | Exceptional wear resistance. | Brittle at very high hardness levels. |
Customizability | Tailored for specific needs. | Longer lead times for customization. |
Cost | Competitive for high-performance materials. | Initial costs higher than traditional metals. |
FAQs
Question | Answer |
---|---|
What industries use carbide solutions? | Aerospace, automotive, mining, medical, oil & gas, and construction. |
Can carbide be recycled? | Yes, recycled carbide retains excellent properties. |
How do I choose the right grade? | Match properties to your application—wear resistance for tools, toughness for mining. |
Are carbide solutions cost-effective? | While initial costs are higher, their durability lowers long-term expenses. |
Customizing carbide isn’t just about materials—it’s about solving problems and optimizing performance. Whether you need the sharpest drill bit or the most wear-resistant part, customized carbide solutions can meet your toughest challenges. With innovations in materials science and engineering, the possibilities are virtually limitless.