When it comes to industrial materials that pack a punch in terms of durability, versatility, and performance, carbide plates stand out. These plates, often made from tungsten carbide or other hard alloys, are at the heart of various applications where wear resistance, hardness, and toughness are crucial. Let’s dive into what makes carbide plates so exceptional and how they’re used across industries.
The High Hardness and Wear Resistance of Carbide Plate
Carbide plates are synonymous with incredible hardness and unmatched wear resistance. Think of them as the superhero of industrial materials, standing firm against abrasion and deformation where others falter. This toughness comes from their unique composition, primarily tungsten carbide bonded with cobalt or nickel.
Why does this matter? Imagine a tool that works tirelessly under extreme conditions without showing signs of wear. Carbide plates achieve this, making them indispensable in machining, construction, and other heavy-duty industries. The hardness level, often rated above 9 on the Mohs scale, is almost diamond-like.
Key Takeaways:
- Carbide plates excel in resisting abrasion and mechanical stress.
- Their hardness ensures longevity, even in harsh environments.
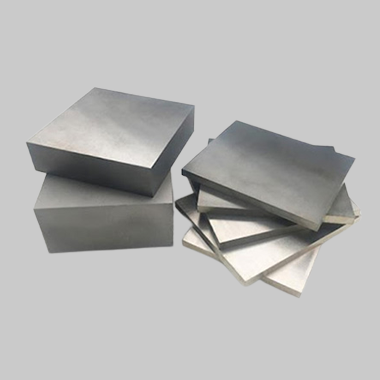
Carbide Plate and Its Excellent High-Temperature Resistance
Carbide plates can laugh in the face of high temperatures where other materials would crumble. Their thermal stability makes them ideal for applications involving heat-intensive processes.
Thermal Performance Comparison of Carbide Plates
Material | Max Operating Temperature (°C) | Thermal Stability | Typical Applications |
---|---|---|---|
Tungsten Carbide | Up to 1,000 | Exceptional | Cutting tools, molds, and dies |
Steel Alloys | 600–800 | Moderate | Structural components |
Ceramic Composites | 1,200–1,500 | Excellent but brittle | Specialized aerospace components |
Notice how carbide plates hold their ground against other contenders? They bridge the gap between ceramics’ high heat tolerance and steel’s mechanical strength.
Why It Matters: Think about a cutting blade in a high-speed machining tool. Heat builds up quickly, but carbide plates keep their shape and sharpness, ensuring precision and efficiency.
Carbide Plate for Diverse Tool Designs
From saw blades to mining drills, carbide plates are molded into a plethora of tools. Their adaptability lies in their ability to be machined and shaped into complex designs, allowing engineers to craft purpose-specific tools.
Consider this: you need a tool that can carve through granite or shape metal with pinpoint accuracy. Carbide plates are your go-to material. They are often found in:
- Precision machining tools: Lathe cutters, milling inserts, and drill bits.
- Construction tools: Concrete chisels and road planers.
- Mining equipment: Tunneling bits and crusher plates.
Advantages:
- Customizable designs cater to specific industry needs.
- High-performance tools reduce downtime and increase efficiency.
Carbide Plate Improves the Field of Worn Parts
Industries that deal with wear and tear daily, like mining and manufacturing, benefit enormously from carbide plates. These plates extend the lifespan of components exposed to abrasive environments.
Durability Enhancement Across Applications
Industry | Common Worn Parts | Carbide Plate Application | Improvement Achieved |
---|---|---|---|
Mining | Conveyor belt liners | Wear-resistant overlays | Longer life, less replacement frequency |
Manufacturing | Punches and dies | Hardened surfaces | Higher production efficiency |
Oil & Gas | Valve components | Corrosion-resistant coatings | Reduced maintenance downtime |
Carbide plates outlast other materials by sheer toughness, offering a cost-effective solution to persistent wear issues.
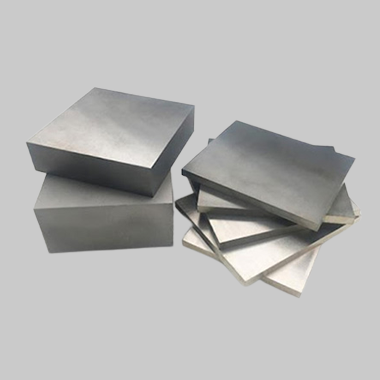
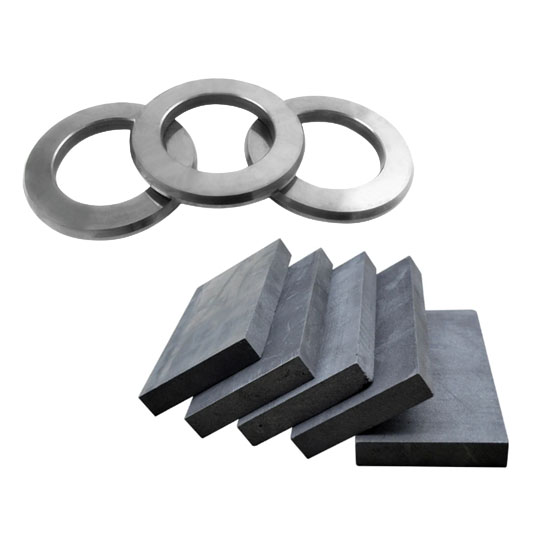
Carbide Plate Has Extremely High Wear Resistance Performance
Wear resistance isn’t just about withstanding abrasion; it’s about maintaining functionality under stress. Carbide plates shine here, handling repetitive impact and prolonged friction without losing their edge—literally and figuratively.
Wear Resistance Comparisons
Material | Wear Resistance Rating | Best Feature | Weakness |
---|---|---|---|
Tungsten Carbide | Excellent | High hardness and toughness | Cost |
Hardened Steel | Moderate | Affordable and readily available | Lower lifespan |
Ceramics | Excellent | High thermal stability | Brittle under impact |
Using carbide plates in high-friction environments like cutting tools or machine components ensures a longer service life, improving productivity.
Enhancing Corrosion and Impact Resistance with Carbide Plate
Carbide plates are not just about surviving abrasions; they also resist corrosion and impacts. In industries where exposure to harsh chemicals or sudden forces is common, this dual resistance becomes invaluable.
Imagine parts in offshore drilling equipment exposed to saltwater and high-pressure impacts. Carbide plates, with their corrosion-resistant bonding agents, excel here.
Corrosion and Impact Benefits:
- Increased durability in harsh environments.
- Lower risk of part failure under sudden loads.
Customization Options for Carbide Plates
Every industry has unique demands, and carbide plates can be tailored to meet them. From thickness variations to specific chemical compositions, these plates offer unparalleled customization.
Common Customization Parameters
Customization Option | Details | Application Example |
---|---|---|
Thickness | 0.5 mm to 50 mm+ | Precision tools, industrial machinery |
Composition | Varying tungsten-cobalt ratios | Corrosion-resistant or ultra-hard plates |
Shape | Rectangular, circular, or complex | Specific tool designs like saw tips |
By matching the material properties to the exact operational requirements, carbide plates achieve peak performance in their intended applications.
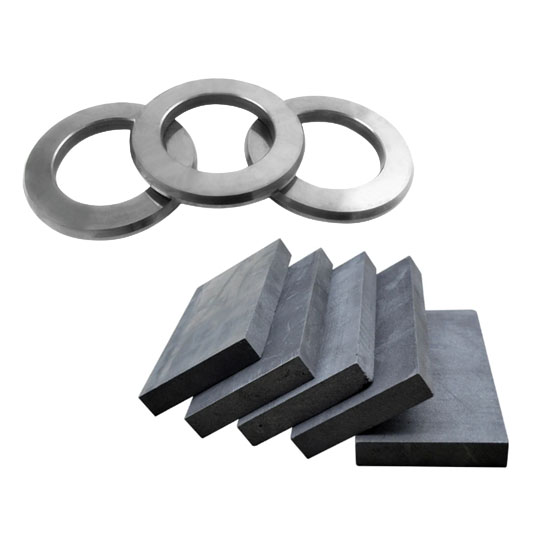
FAQs
Question | Answer |
---|---|
What are carbide plates made of? | They’re primarily tungsten carbide, bonded with metals like cobalt or nickel for strength and durability. |
Are carbide plates expensive? | While costlier upfront than steel, their longevity makes them cost-effective in the long run. |
Can carbide plates be recycled? | Yes, they’re recyclable, often reprocessed to extract valuable tungsten and cobalt. |
How are carbide plates manufactured? | They’re created through powder metallurgy, which involves sintering powders under high heat and pressure. |
What industries benefit most from carbide plates? | Industries like mining, construction, oil & gas, and precision machining see the most significant benefits. |
Conclusion
Carbide plates are the unsung heroes in many industries, offering unmatched hardness, wear resistance, and versatility. Whether you’re designing tools, battling high temperatures, or resisting corrosion, these plates provide solutions that outperform alternatives.
In a world where durability meets customization, carbide plates emerge as the material of choice. Ready to harness their power? Let’s redefine what’s possible!