Overview
When it comes to the world of machining and tooling, the choice of materials can make or break your operations. One such material that stands out in terms of durability and efficiency is carbide. Specifically, finish grind carbide strips are a staple in industries requiring precise cutting and shaping. These strips are essential components in various tools and machines, offering unparalleled hardness, strength, and wear resistance.
So, what exactly makes finish grind carbide strips so special? How do you choose the right one for your needs? And what are the different types and applications? This guide will answer all these questions and more, giving you a deep dive into the fascinating world of carbide strips.
Introduction to Finish Grind Carbide Strips
Finish grind carbide strips are essentially thin, rectangular pieces of tungsten carbide, which is a compound made from tungsten and carbon. This compound is renowned for its extreme hardness, which is second only to diamonds, making it ideal for applications that require cutting, grinding, and shaping hard materials.
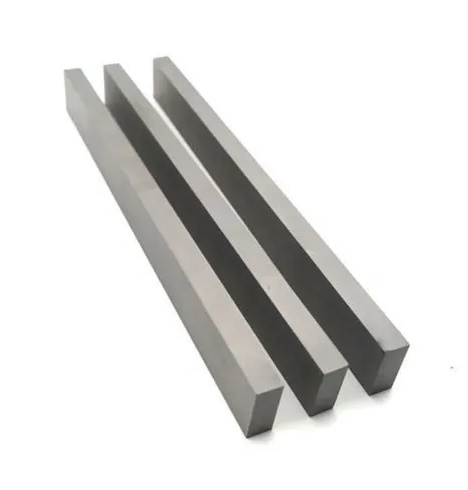
Types of Finish Grind Carbide Strips
When it comes to finish grind carbide strips, variety is key. Here are some specific models you might encounter, each with its unique properties and applications:
Model | Description |
---|---|
K10 | Known for its wear resistance, suitable for cutting non-ferrous metals. |
K20 | Balanced hardness and toughness, ideal for woodworking and light machining. |
K30 | Higher toughness, used in heavy-duty machining and impact applications. |
H10 | Excellent for high-speed cutting, maintaining sharpness over extended periods. |
H20 | Versatile, used in both cutting and shaping applications. |
H30 | Superior strength and durability, for high-impact environments. |
P10 | Perfect for precision tools, offering excellent edge retention. |
P20 | Balanced properties, used in general machining applications. |
P30 | High toughness, used in challenging environments like mining. |
M10 | Specifically designed for metalworking, with high wear resistance. |
M20 | Versatile in metalworking, maintaining balance between wear resistance and toughness. |
S10 | Ideal for stone cutting, offering excellent wear resistance and toughness. |
Applications of Finish Grind Carbide Strips
Finish grind carbide strips find their use in a variety of applications due to their exceptional properties. Here’s a look at some of the common applications:
Application | Description |
---|---|
Woodworking | Used in saw blades and router bits for precise and durable cutting. |
Metalworking | Employed in lathes and milling machines for cutting and shaping metals. |
Mining and Drilling | Utilized in drill bits and mining tools for their wear resistance and toughness. |
Stone Cutting | Used in cutting tools for stone and concrete, thanks to their hardness. |
Automotive Industry | Found in parts that require high durability and wear resistance. |
Aerospace Industry | Used in manufacturing parts that must withstand extreme conditions. |
General Machining | Ideal for precision machining and tool making. |
Plastics and Composites | Employed in cutting and shaping plastic and composite materials. |
Textile Industry | Used in cutting tools for fabrics and other materials. |
Medical Instruments | Utilized in surgical tools that require precision and durability. |
Material Properties of Finish Grind Carbide Strips
The effectiveness of finish grind carbide strips is rooted in their material properties. Here’s a detailed look:
Property | Description |
---|---|
Hardness | Extremely hard, typically ranging from 85 to 95 HRA. |
Toughness | High toughness, making them resistant to breakage. |
Wear Resistance | Exceptional wear resistance, extending the life of tools and parts. |
Thermal Stability | Able to withstand high temperatures without losing their properties. |
Corrosion Resistance | Resistant to corrosion, making them suitable for harsh environments. |
Density | High density, contributing to their strength and durability. |
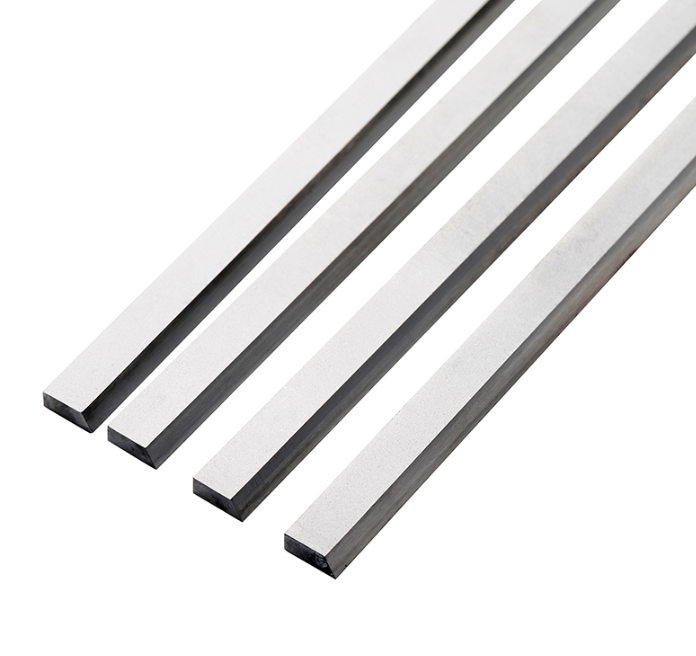
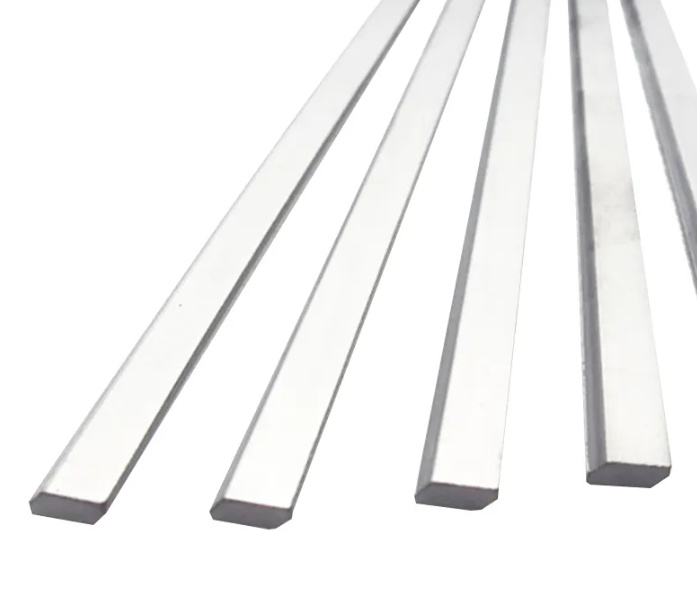
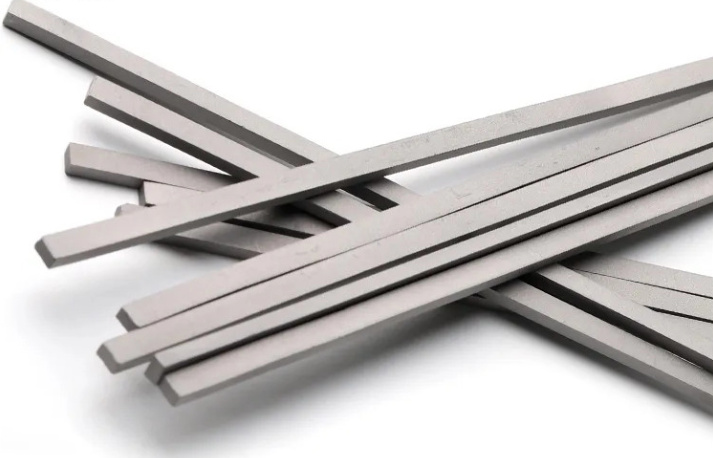
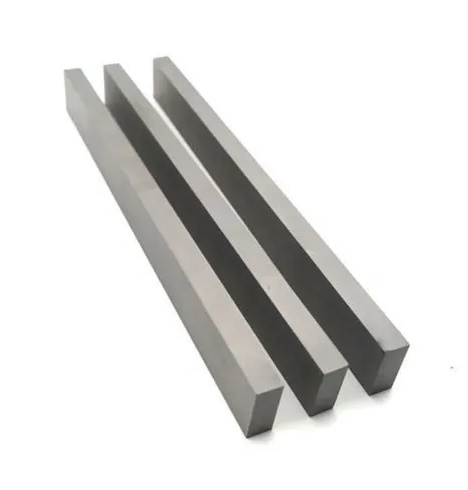
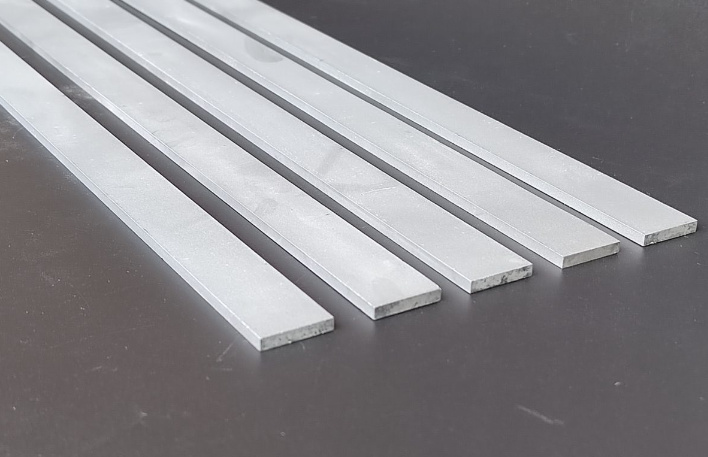
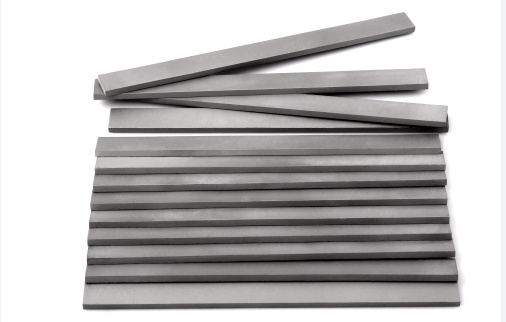
Composition and Characteristics of Finish Grind Carbide Strips
Understanding the composition of finish grind carbide strips can give you insights into their performance and suitability for various applications:
Component | Percentage | Characteristic |
---|---|---|
Tungsten Carbide (WC) | 70-97% | Provides hardness and wear resistance. |
Cobalt (Co) | 3-30% | Acts as a binder, offering toughness and impact resistance. |
Titanium Carbide (TiC) | 0-10% | Enhances corrosion resistance and high-temperature performance. |
Tantalum Carbide (TaC) | 0-10% | Improves wear resistance and toughness. |
Hardness, Strength, and Wear Resistance
Let’s take a closer look at how the hardness, strength, and wear resistance of finish grind carbide strips stack up:
Model | Hardness (HRA) | Toughness | Wear Resistance |
---|---|---|---|
K10 | 90 | Medium | High |
K20 | 88 | Medium-High | Medium |
K30 | 85 | High | Medium |
H10 | 92 | Low-Medium | Very High |
H20 | 89 | Medium | High |
H30 | 86 | High | High |
P10 | 91 | Low-Medium | Very High |
P20 | 89 | Medium | High |
P30 | 87 | High | Medium |
M10 | 90 | Medium | High |
M20 | 88 | Medium-High | Medium-High |
S10 | 90 | Medium | Very High |
Specifications, Sizes, and Standards
The specifications and sizes of finish grind carbide strips are diverse, catering to different needs and applications:
Specification | Details |
---|---|
Length | Typically ranges from 100mm to 600mm. |
Width | Common widths range from 5mm to 50mm. |
Thickness | Varies from 1mm to 10mm, depending on the application. |
Standards | ISO, ANSI, and various industry-specific standards ensure quality and compatibility. |
Suppliers and Pricing Details
Choosing the right supplier is crucial for obtaining quality carbide strips. Here’s a look at some suppliers and pricing details:
Supplier | Location | Price Range (per piece) | Quality Certifications |
---|---|---|---|
Kennametal | USA | $20 – $150 | ISO 9001, ISO 14001 |
Sandvik | Sweden | $25 – $160 | ISO 9001, ISO 14001 |
Zhuzhou Cemented Carbide | China | $15 – $120 | ISO 9001 |
Sumitomo Electric | Japan | $30 – $200 | ISO 9001, ISO 14001 |
Mitsubishi Materials | Japan | $25 – $180 | ISO 9001, ISO 14001 |
How to Select the Right Finish Grind Carbide Strips Company
Choosing the right company can make a significant difference in the quality and performance of your carbide strips. Here’s how you can make an informed decision:
Criteria | Considerations |
---|---|
Reputation | Look for companies with a strong track record and positive customer reviews. |
Certifications | Ensure the company has relevant quality certifications such as ISO 9001. |
Product Range | A wide range of products indicates the company’s capability to meet diverse needs. |
Customization Options | Check if the company offers customization to suit specific requirements. |
Technical Support | Good technical support can help resolve any issues quickly and efficiently. |
Pricing | Compare prices to ensure you are getting value for money. |
Delivery and Logistics | Efficient delivery and logistics are crucial for timely operations. |
Comparing Advantages and Limitations
When choosing finish grind carbide strips, it’s essential to weigh the advantages and limitations:
Aspect | Advantages | Limitations |
---|---|---|
Hardness | Extremely hard, ensuring longevity and durability. | High hardness can sometimes make them more brittle. |
Toughness | High toughness makes them resistant to impact and breakage. | Increased toughness can slightly reduce wear resistance. |
Wear Resistance | Excellent wear resistance, reducing the need for frequent replacements. | Wear resistance can be compromised if not paired with proper toughness. |
Thermal Stability | Can withstand high temperatures, ideal for high-speed machining. | High thermal stability might not be necessary for all applications, adding to the cost. |
Corrosion Resistance | Suitable for harsh environments, reducing maintenance costs. | May not be required in non-corrosive environments, making it an unnecessary feature. |
Cost | Though initially expensive, their durability makes them cost-effective in the long run. | Higher upfront cost compared to other materials like steel or high-speed steel. |
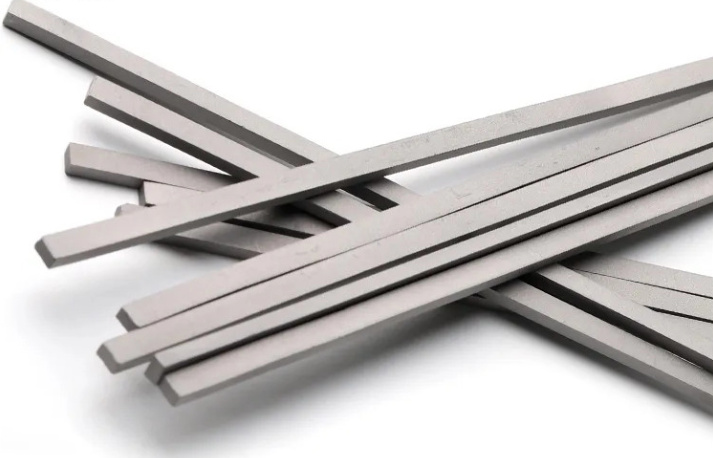
FAQs
Question | Answer |
---|---|
What are finish grind carbide strips used for? | They are used in cutting, shaping, and grinding applications across various industries. |
How do I choose the right carbide strip for my needs? | Consider the specific application, required properties like hardness and toughness, and budget. |
Are carbide strips better than steel? | Carbide strips offer better hardness and wear resistance but are more expensive than steel. |
Can carbide strips be customized? | Yes, many suppliers offer customization options to meet specific needs. |
How long do carbide strips last? | Their lifespan depends on the application and usage but they typically last longer than steel. |
Conclusion
Finish grind carbide strips are an indispensable part of many industrial applications due to their exceptional properties like hardness, toughness, and wear resistance. While they come with a higher upfront cost, their durability and efficiency make them a cost-effective choice in the long run. By understanding the different types, applications, material properties, and how to choose the right supplier, you can make an informed decision that meets your specific needs.