Introduction
The construction industry has witnessed remarkable advancements with the integration of innovative materials. Among these, cemented carbide plates stand out due to their unparalleled hardness, wear resistance, and durability. This blog delves into the world of cemented carbide plates, exploring their applications, benefits, and the transformative impact they have on modern construction projects.
Understanding Cemented Carbide Plates
What Are Cemented Carbide Plates?
Cemented carbide plates, often referred to as tungsten carbide plates, are composite materials made from tungsten carbide particles bonded together with a metallic binder, typically cobalt. This combination results in a material that is extremely hard and resistant to wear and deformation.
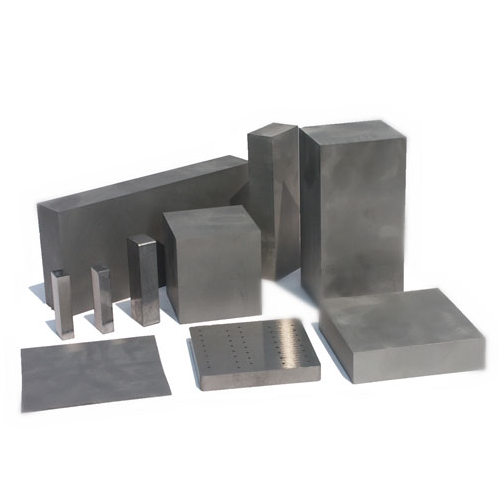
Key Properties
- Hardness: Cemented carbide plates are among the hardest materials available, making them ideal for heavy-duty applications.
- Wear Resistance: They exhibit exceptional wear resistance, prolonging the lifespan of tools and components.
- Durability: Their robust structure ensures they can withstand extreme conditions and high-stress environments.
Applications in Construction
Cutting and Drilling Tools
Cemented carbide plates are extensively used in the manufacturing of cutting and drilling tools. Their hardness and wear resistance make them perfect for:
- Drill Bits: Used for drilling through tough materials like concrete and steel.
- Saw Blades: Employed in cutting applications requiring precision and long tool life.
Wear Parts
In construction machinery, cemented carbide plates are used as wear parts to protect critical components from abrasion:
- Excavator Teeth: Enhance the durability of excavators by resisting wear and tear.
- Crusher Liners: Protect crushers from the abrasive nature of materials being processed.
Forming and Shaping Tools
The construction industry also benefits from cemented carbide plates in the manufacturing of forming and shaping tools:
- Wire Drawing Dies: Used in the production of steel wires and cables.
- Extrusion Dies: Employed in shaping materials like aluminum and steel into desired profiles.
Surface Coatings
Cemented carbide plates are used as surface coatings to enhance the wear resistance of construction tools and equipment:
- Concrete Mixers: Coated with carbide plates to extend their lifespan.
- Pavement Milling Tools: Improved durability in road construction and maintenance.
Advantages of Cemented Carbide Plates in Construction
Enhanced Tool Life
The exceptional wear resistance and hardness of cemented carbide plates significantly extend the life of construction tools, reducing the frequency of replacements and maintenance.
Improved Efficiency
The high performance of cemented carbide plates leads to more efficient construction processes. Tools made from these materials maintain their sharpness and effectiveness over prolonged periods, ensuring consistent performance.
Cost-Effectiveness
Although the initial cost of cemented carbide plates might be higher compared to other materials, their longevity and reduced need for replacements make them a cost-effective choice in the long run.
Versatility
Cemented carbide plates can be tailored to specific applications, offering versatility in various construction tasks. Their adaptability makes them suitable for both heavy-duty industrial applications and precision tasks.
Comparative Analysis: Cemented Carbide Plates vs. Other Materials
Property | Cemented Carbide Plates | Steel | Ceramics |
---|---|---|---|
Hardness | Extremely High | Moderate | High |
Wear Resistance | Excellent | Moderate | Excellent |
Durability | Very High | High | Moderate |
Cost | Higher Initial Cost | Lower Initial Cost | Moderate Initial Cost |
Application Range | Versatile | Versatile | Limited to Specific Uses |
Future Trends and Innovations
Advanced Coating Technologies
- Diamond Coatings: Enhancing the wear resistance and durability of cemented carbide plates.
- Nano-Coatings: Providing superior performance and extending tool life even further.
Sustainable Practices
- Recycling Programs: Implementing recycling programs for used carbide plates to reduce environmental impact.
- Eco-Friendly Manufacturing: Developing greener manufacturing processes for cemented carbide plates.
Integration with Smart Technologies
- IoT-Enabled Tools: Incorporating sensors and IoT technology to monitor the condition and performance of tools made from cemented carbide plates.
- AI-Powered Maintenance: Utilizing artificial intelligence to predict maintenance needs and optimize the performance of construction tools.
FAQ
Q1: How do carbide plates improve the efficiency of cutting and drilling tools in construction?
A1: Carbide plates improve the efficiency of cutting and drilling tools by maintaining their sharpness and effectiveness over extended periods. Their exceptional hardness and wear resistance reduce the need for frequent replacements and maintenance, ensuring consistent performance and reducing downtime during construction projects.
Q2: What are the primary advantages of using carbide plates in wear parts for construction machinery?
A2: The primary advantages of using carbide plates in wear parts for construction machinery include enhanced durability and prolonged lifespan. These plates can withstand high-stress environments and resist abrasion, protecting critical components like excavator teeth and crusher liners from wear and tear. This results in fewer replacements, lower maintenance costs, and improved overall efficiency.
Q3: Why are carbide plates considered a cost-effective choice despite their higher initial cost?
A3: carbide plates are considered a cost-effective choice because their exceptional wear resistance and durability significantly reduce the frequency of tool replacements and maintenance. Although the initial cost is higher compared to other materials, the long-term savings from extended tool life and improved efficiency make them a more economical option in the long run.
Q4: How are advanced coating technologies enhancing the performance of carbide plates?
A4: Advanced coating technologies, such as diamond coatings and nano-coatings, are enhancing the performance of carbide plates by further improving their wear resistance and durability. These coatings provide an additional protective layer, reducing the rate of wear and extending the lifespan of the tools. This leads to even greater efficiency and cost savings in construction applications.
Q5: What future trends can we expect in the development and use of carbide plates in construction?
A5: Future trends in the development and use of carbide plates in construction include the adoption of sustainable practices, such as recycling programs and eco-friendly manufacturing processes. Additionally, the integration of smart technologies, like IoT-enabled tools and AI-powered maintenance, will optimize the performance and monitoring of construction tools. Advanced coating technologies will continue to evolve, further enhancing the wear resistance and lifespan of carbide plates.
Want to buy affordable carbide plates with excellent quality? please click here.