Introduction
Carbide plates are renowned for their exceptional hardness, wear resistance, and durability. These properties make them indispensable in various industries, especially when dealing with extreme environments. But how do carbide plates perform under high temperatures, in corrosive conditions, or when handling abrasive materials? This blog will delve into the fascinating world of carbide plates, exploring how they maintain their integrity and efficiency across different challenging environments.
Understanding Carbide Plates
What Are Carbide Plates?
Carbide plates are flat pieces made from tungsten carbide, a composite material formed by combining tungsten carbide particles with a metallic binder, typically cobalt. This combination results in a material that is incredibly hard and wear-resistant, suitable for demanding applications in manufacturing, machining, and other industrial processes.
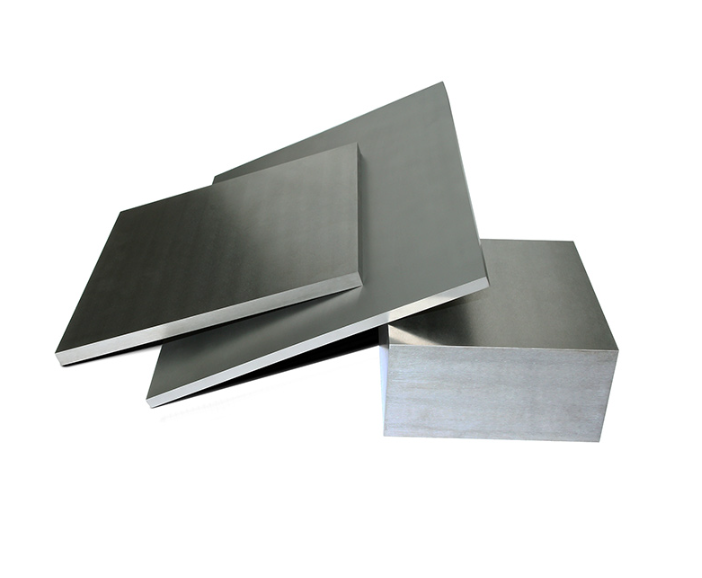
Key Properties
- Hardness: Tungsten carbide is one of the hardest materials available, second only to diamond.
- Wear Resistance: Outstanding resistance to abrasion and wear.
- Thermal Stability: Maintains properties at high temperatures.
- Corrosion Resistance: Depending on the binder and coatings used, carbide plates can resist corrosive environments.
Performance in High-Temperature Environments
Thermal Stability
Carbide plates are designed to withstand high temperatures without losing their hardness or structural integrity. This property is crucial for applications such as:
- Cutting Tools: High-speed machining generates significant heat, and carbide plates remain stable, ensuring precise cuts and extended tool life.
- Molds and Dies: Used in high-temperature forming processes, carbide plates maintain their shape and performance.
Heat Resistance
The combination of tungsten carbide and cobalt binder provides excellent heat resistance. However, the performance can be further enhanced with specific coatings, such as:
- Titanium Nitride (TiN): Improves heat resistance and reduces friction.
- Aluminum Titanium Nitride (AlTiN): Provides superior oxidation resistance at high temperatures.
Effects of High Temperatures
While carbide plates perform well at elevated temperatures, prolonged exposure can lead to:
- Oxidation: Surface oxidation can degrade the material over time.
- Thermal Shock: Rapid temperature changes can cause cracking or chipping.
Applications in High-Temperature Environments
- Aerospace: Engine components and heat shields.
- Automotive: High-performance engine parts.
- Metalworking: High-speed cutting tools and dies.
Performance in Corrosive Conditions
Corrosion Resistance
Carbide plates exhibit excellent corrosion resistance, making them suitable for harsh environments. This resistance is primarily due to the properties of tungsten carbide and can be enhanced with appropriate binders and coatings.
Binder Selection
The choice of binder material significantly impacts corrosion resistance:
- Cobalt: Offers good corrosion resistance but can be susceptible to certain acids.
- Nickel: Provides enhanced corrosion resistance, especially in acidic environments.
Protective Coatings
Applying protective coatings can further improve corrosion resistance:
- Nickel Plating: Commonly used to protect carbide plates from corrosive substances.
- Diamond-Like Carbon (DLC): Provides a hard, corrosion-resistant layer.
Effects of Corrosive Environments
Exposure to corrosive environments can lead to:
- Pitting: Localized corrosion can cause small pits on the surface.
- Surface Degradation: Continuous exposure can gradually degrade the material.
Applications in Corrosive Environments
- Chemical Processing: Components exposed to acids and other corrosive substances.
- Oil and Gas: Downhole tools and equipment.
- Marine: Parts subjected to seawater and harsh marine conditions.
Performance with Abrasive Materials
Wear Resistance
Carbide plates are particularly valued for their wear resistance, making them ideal for handling abrasive materials. The hardness of tungsten carbide ensures minimal wear and tear, even under constant abrasion.
Hardness and Toughness
The balance between hardness and toughness is critical:
- Hardness: Ensures resistance to abrasive wear.
- Toughness: Prevents cracking and chipping under stress.
Effects of Abrasive Materials
Handling abrasive materials can lead to:
- Surface Wear: Gradual wearing down of the surface.
- Edge Chipping: Edges can chip under heavy abrasion.
Applications with Abrasive Materials
- Mining: Cutting and drilling tools.
- Construction: Wear parts in heavy machinery.
- Manufacturing: Abrasive machining and grinding tools.
Comparative Performance Analysis
Performance Comparison in Different Environments
Environment | Key Challenges | Carbide Plate Performance |
---|---|---|
High Temperatures | Thermal stability, oxidation | Excellent heat resistance, enhanced with coatings |
Corrosive Conditions | Chemical attack, surface degradation | Good corrosion resistance, improved with nickel binders and coatings |
Abrasive Materials | Wear and tear, edge chipping | Superior wear resistance, maintained hardness and toughness balance |
Enhancements for Specific Environments
- Coatings: Applying specific coatings can tailor carbide plates for particular environments.
- Binder Selection: Choosing the right binder material enhances performance in corrosive conditions.
- Design Modifications: Custom designs can improve performance in high-stress applications.
Advantages and Limitations
Advantages of Carbide Plates in Extreme Environments
- Durability: Long-lasting performance reduces the need for frequent replacements.
- Versatility: Suitable for a wide range of challenging applications.
- Efficiency: Maintains high performance, ensuring operational efficiency.
Limitations
- Cost: Higher initial cost compared to other materials.
- Brittleness: Can be prone to chipping under extreme stress or thermal shock.
Why Choose TRUER?
Choosing carbide plates for your manufacturing needs ensures access to high-quality, precision-engineered tools that meet the stringent demands of modern industries. The benefits include:
- Superior Quality: Manufactured to the highest standards with rigorous quality control.
- Custom Solutions: Ability to tailor plates to specific applications and requirements.
- Innovation: Continuous development of new geometries and coatings to enhance performance.
- Support: Comprehensive customer service and technical support to assist with product selection and usage.
FAQ
Q1: How do carbide plates compare to other materials in high-temperature applications?
A1: Carbide plates offer superior thermal stability and maintain their hardness at high temperatures, outperforming many other materials such as high-speed steel.
Q2: Can carbide plates be used in marine environments?
A2: Yes, carbide plates with appropriate coatings and binders can withstand the corrosive effects of seawater, making them suitable for marine applications.
Q3: Are there any special maintenance requirements for carbide plates in abrasive environments?
A3: Regular inspections and timely replacement of worn plates are essential to maintain performance. Using coated plates can also extend their lifespan.
Q4: What are the latest innovations in carbide plate manufacturing?
A4: Innovations include advanced coatings, new carbide composites, and sustainable manufacturing practices aimed at enhancing performance and reducing environmental impact.
Q5: How can I enhance the performance of carbide plates for my specific application?
A5: Selecting the right binder, applying appropriate coatings, and considering custom designs tailored to your application can significantly enhance the performance of carbide plates.