Overview
Carbide plates are a cornerstone in the world of precision machining and manufacturing, known for their unmatched hardness, wear resistance, and durability. But how does the manufacturing process of carbide plates differ from that of other carbide components? This blog will take you on a fascinating journey through the unique processes involved in crafting these essential tools, highlighting the crucial distinctions that set them apart.
Detailed Introduction
What Are Carbide Plates?
Carbide plates are flat, rectangular pieces made from tungsten carbide, a composite material known for its extreme hardness and resistance to wear. These plates are used in various applications, including cutting tools, molds, and wear parts, where precision and durability are paramount.
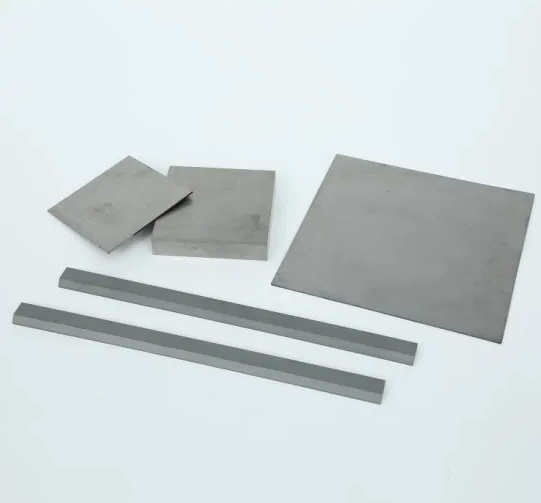
Other Carbide Components
Other carbide components include drills, end mills, inserts, and wear parts, each serving different purposes in various industries. While all these components share the basic material properties of tungsten carbide, their manufacturing processes can differ significantly due to their shapes, sizes, and specific functional requirements.
Manufacturing Process of Carbide Plates
The manufacturing process of carbide plates involves several key steps, each meticulously designed to ensure the highest quality and performance. Let’s explore these steps in detail and see how they differ from the processes used for other carbide components.
Powder Preparation
- Raw Material Selection: The process begins with selecting high-purity tungsten carbide powder and a binder, usually cobalt.
- Mixing: The tungsten carbide powder is mixed with the cobalt binder to create a homogenous mixture. This mixture is critical for ensuring the plate’s uniform hardness and strength.
Pressing
- Forming the Plates: The mixture is pressed into flat, rectangular shapes using high-pressure presses. This step is where the first major difference between carbide plates and other components arises. Unlike complex shapes such as drills or inserts, plates require uniform thickness and flatness, necessitating specialized pressing techniques.
- Green Machining: After pressing, the plates, still in their “green” (unsintered) state, may undergo green machining to achieve precise dimensions and surface finishes.
Sintering
- High-Temperature Sintering: The pressed plates are then sintered in a furnace at temperatures exceeding 1400°C. This process causes the tungsten carbide particles to bond together, creating a dense, hard material. The sintering process for plates is carefully controlled to prevent warping and ensure uniform density, which differs from the sintering of more complex shapes that might require supports or different temperature profiles.
- Cooling: After sintering, the plates are slowly cooled to room temperature to avoid thermal stresses that could cause cracking or distortion.
Finishing
- Grinding and Polishing: The sintered plates undergo grinding and polishing to achieve the desired surface finish and precise dimensions. This step is crucial for plates, as they often serve as reference surfaces or wear parts where flatness and smoothness are critical.
- Inspection: Each plate is inspected for defects, dimensional accuracy, and surface finish. Rigorous quality control ensures that only plates meeting strict standards proceed to final packaging.
Finishing Techniques
The finishing techniques for carbide plates are particularly rigorous. Given their application in precision tooling and as wear plates, achieving a high degree of flatness and surface finish is paramount. This often involves multiple stages of grinding and lapping, using diamond abrasives to achieve the desired tolerances.
Coating (Optional)
Some carbide plates receive additional coatings, such as titanium nitride or diamond-like carbon. These coatings enhance the wear resistance and reduce friction, further extending the plate’s lifespan. The coating process involves physical vapor deposition (PVD) or chemical vapor deposition (CVD), techniques that are less commonly applied to more complex-shaped components due to the difficulty in achieving uniform coverage.
Comparison with Other Carbide Components
Manufacturing Process Differences
Process Step | Carbide Plates | Other Carbide Components |
---|---|---|
Pressing | High-pressure pressing for flat shapes | Complex molds for diverse shapes |
Green Machining | Precision machining for flatness | Varies based on component shape |
Sintering | Controlled to prevent warping | May require supports for complex shapes |
Finishing | Multiple stages of grinding and lapping | Varies, often simpler for less critical parts |
Coating | Often coated for enhanced performance | Less common, more complex to coat uniformly |
Other Carbide Components Manufacturing
The manufacturing process for other carbide components, such as drills and inserts, shares some similarities with carbide plates but also includes significant differences:
- Complex Pressing: Unlike the uniform pressing of plates, other components require complex molds to achieve their intricate shapes.
- Specialized Sintering: The sintering process for complex shapes may involve special supports to prevent deformation.
- Tool Grinding: For cutting tools, additional grinding steps are necessary to form cutting edges and flutes, a process not required for plates.
- Coating Challenges: Coating complex shapes uniformly is more challenging, leading to different approaches compared to the relatively straightforward coating of flat plates.
Applications
Carbide plates are integral to various industries due to their exceptional properties. Here are some key applications:
- Tool Making
- Precision cutting tools
- Wear-resistant inserts
- Mold Manufacturing
- Injection molds
- Die casting molds
- Wear Parts
- Wear-resistant surfaces
- Industrial machinery parts
- Electronics
- Semiconductor manufacturing
- PCB drilling
- Aerospace
- High-precision components
- Engine parts
Advantages and Limitations
Advantages and Limitations of Carbide Plates
Aspect | Advantages | Limitations |
---|---|---|
Durability | High hardness and wear resistance ensure long tool life. | Higher initial cost compared to standard plates. |
Performance | Maintains sharp edge at high temperatures, suitable for high-speed machining. | Requires precise alignment and setup. |
Precision | Provides excellent dimensional accuracy and surface finish. | Brittle nature can lead to chipping. |
Versatility | Applicable to a wide range of materials and industries. | Not suitable for very soft materials. |
Related Topics
Advanced Coatings for Carbide Plates
Advanced coatings such as titanium nitride and diamond-like carbon significantly enhance the performance of carbide plates. These coatings provide additional wear resistance, reduce friction, and extend the lifespan of the plates, ensuring higher efficiency and cost-effectiveness.
Custom Carbide Plates
Custom carbide plates are tailored to meet specific requirements in terms of size, shape, and performance. This customization ensures that the plates perfectly fit the intended application, providing optimal performance and durability.
Innovations in Carbide Plate Manufacturing
Recent innovations in the manufacturing of carbide plates include the use of additive manufacturing techniques, improved sintering processes, and the development of new carbide composites. These advancements aim to enhance the properties of carbide plates, making them more efficient and cost-effective.
Why Choose Carbide Plates?
Choosing carbide plates for your manufacturing needs ensures access to high-quality, precision-engineered tools that meet the stringent demands of modern industries. The benefits include:
- Superior Quality: Manufactured to the highest standards with rigorous quality control.
- Custom Solutions: Ability to tailor plates to specific applications and requirements.
- Innovation: Continuous development of new geometries and coatings to enhance performance.
- Support: Comprehensive customer service and technical support to assist with product selection and usage.
FAQ
Q1: What materials can carbide plates machine?
A1: Carbide plates can machine a wide range of materials, including metals, composites, and ceramics. Their high hardness and wear resistance make them particularly effective for creating intricate and precise shapes in tough and abrasive materials.
Q2: How do I choose the right carbide plate for my application?
A2: Consider the material you are machining, the type of operation, and the desired surface finish. Consult the manufacturer’s guidelines and specifications to select a plate with the appropriate size, grade, and coating.
Q3: How often should carbide plates be replaced?
A3: The replacement frequency depends on the material being machined, the operating conditions, and the plate’s wear resistance. Regular inspections are essential to identify signs of wear, such as edge chipping or loss of cutting effectiveness.
Q4: Can carbide plates be resharpened?
A4: Yes, carbide plates can be resharpened, but the process requires specialized equipment and expertise. Resharpening can extend the tool’s life and maintain cutting performance, but it is often more cost-effective to replace the plates.
Q5: What are the benefits of coated carbide plates?
A5: Coated carbide plates offer enhanced wear resistance, reduced friction, and improved heat resistance. These benefits result in longer tool life, better surface finishes, and the ability to machine at higher speeds and feeds.
Want to buy affordable carbide plates with excellent quality? please click here.