Overview
Tungsten carbide plates are a cornerstone of modern industry, known for their incredible hardness, wear resistance, and durability. These plates are crucial in applications requiring high precision and longevity. This article explores the fascinating world of tungsten carbide plates, detailing their properties, uses, types, and market trends, while also providing a comparative analysis of suppliers and the advantages and limitations of these essential industrial components.
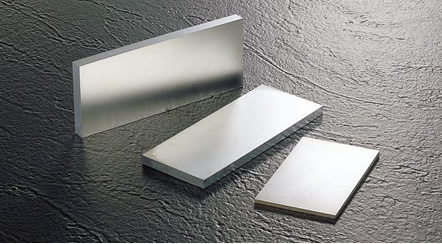
Detailed Introduction
What Is a Tungsten Carbide Plate?
A tungsten carbide plate is a flat, rectangular piece made from tungsten carbide, a compound of tungsten and carbon. This material is celebrated for its extreme hardness, surpassing many other industrial materials. The plates are often utilized in environments where high wear and tear are expected, making them ideal for cutting, grinding, and wear-resistant applications.
Working Principle
The working principle of tungsten carbide plates lies in their composition. Tungsten carbide is formed by combining tungsten powder with carbon at high temperatures, resulting in a material that exhibits remarkable hardness and strength. The plates can endure high-pressure and high-temperature conditions without deforming or losing their cutting edge, making them indispensable in precision machining and other demanding applications.
How to Use Tungsten Carbide Plates
Using tungsten carbide plates involves several steps:
- Selection: Choose the right plate based on the specific application, considering factors such as size, thickness, and grade.
- Installation: Secure the plate in the appropriate machinery or tool holder.
- Operation: Follow the manufacturer’s guidelines to ensure optimal performance.
- Maintenance: Regularly inspect the plates for wear and replace them as needed to maintain effectiveness.
How to Process Tungsten Carbide Plates
Processing tungsten carbide plates requires precision and advanced techniques:
- Powder Preparation: Tungsten powder is mixed with carbon and a binder, typically cobalt.
- Pressing: The mixture is pressed into flat shapes under high pressure.
- Sintering: The pressed plates are heated in a sintering furnace to bond the particles.
- Grinding and Polishing: The plates are ground to precise dimensions and polished for a smooth finish.
- Coating (Optional): Additional coatings, such as titanium nitride, may be applied to enhance performance.
Types and Categories of Tungsten Carbide Plates
Standard Tungsten Carbide Plates
These plates are used in general applications where high wear resistance is required. They come in various sizes and thicknesses to meet different needs.
Pre-Formed Tungsten Carbide Plates
Pre-formed plates are manufactured for specific applications, tailored to fit custom tools and machinery parts.
Coated Tungsten Carbide Plates
These plates have additional layers of materials, such as titanium nitride, to enhance wear resistance and lifespan.
Market Trends
The market for tungsten carbide plates is driven by the demand for durable and precise materials. Key trends include the development of advanced coatings, customization of plate dimensions and shapes, and increasing use in emerging technologies.
Specifications
Basic Information of Tungsten Carbide Plates
Parameter | Description |
---|---|
Type | Standard, Pre-Formed, Coated |
Composition | Tungsten Carbide, Cobalt Binder |
Properties | High Hardness, Wear Resistance, Thermal Stability |
Features | Sharp Cutting Edge, Precise Dimensions, Various Coatings |
Specifications | ISO, ANSI, DIN Standards |
Sizes | Varying Lengths, Widths, and Thicknesses |
Grades | Various Grades Based on Hardness, Toughness, and Wear Resistance |
Standards | ISO 9001, ASME B94.55M, ANSI B212.4 |
Comparative Analysis of Similar Products
Attribute | Tungsten Carbide Plate | High-Speed Steel (HSS) Plate | Ceramic Plate |
---|---|---|---|
Hardness | Very High | Moderate | High |
Wear Resistance | Excellent | Moderate | Excellent |
Heat Resistance | High | Moderate | High |
Cost | Moderate to High | Low | High |
Applications | Precision Machining, Wear Parts | General Machining, Wear Parts | High-Temperature Applications |
Applications
Tungsten carbide plates are versatile and used across various industries due to their robustness and precision. Here are some key applications:
- Metalworking Industry
- Cutting Tools
- Wear Parts
- Mining Industry
- Drill Bits
- Wear Liners
- Construction Industry
- Concrete Cutting Tools
- Flooring Tools
- Aerospace Industry
- High-Precision Components
- Wear-Resistant Parts
- Automotive Industry
- Engine Components
- Transmission Parts
- Medical Industry
- Surgical Instruments
- Implantable Devices
- Oil and Gas Industry
- Drill Bits
- Pump Components
Comparison of TRUER and Other Suppliers
Supplier Comparison for Tungsten Carbide Plates
Supplier | Location | Price Range per Piece | Specialties |
---|---|---|---|
TRUER | China | $25 – $60 | Custom Solutions, Advanced Coatings, High Precision |
Sandvik | Sweden | $30 – $70 | High Wear Resistance, Wide Range of Products |
Kennametal | USA | $35 – $80 | Durable Plates, Innovative Designs |
ISCAR | Israel | $28 – $65 | Efficient Chip Control, High Performance |
Advantages and Limitations
Advantages and Limitations of Tungsten Carbide Plates
Aspect | Advantages | Limitations |
---|---|---|
Durability | High hardness and wear resistance ensure long tool life. | Higher initial cost compared to standard plates. |
Performance | Maintains sharp edge at high temperatures, suitable for high-speed machining. | Requires precise alignment and setup. |
Precision | Provides excellent dimensional accuracy and surface finish. | Brittle nature can lead to chipping. |
Versatility | Applicable to a wide range of materials and industries. | Not suitable for very soft materials. |
Related Topics
Advanced Coatings for Tungsten Carbide Plates
Advanced coatings such as titanium nitride, aluminum oxide, and diamond-like carbon can significantly enhance the performance of tungsten carbide plates. These coatings provide additional wear resistance, reduce friction, and extend the lifespan of the plates. Understanding the benefits and applications of these coatings can help in selecting the right tungsten carbide plate for specific needs.
Custom Tungsten Carbide Plates
Custom tungsten carbide plates are tailored to meet specific requirements in terms of size, shape, and performance. This customization ensures that the plates perfectly fit the intended application, providing optimal performance and durability.
Innovations in Tungsten Carbide Plate Manufacturing
Recent innovations in the manufacturing of tungsten carbide plates include the use of additive manufacturing techniques, improved sintering processes, and the development of new carbide composites. These advancements aim to enhance the properties of tungsten carbide plates, making them more efficient and cost-effective.
Why Choose TRUER
Choosing TRUER for your tungsten carbide plate needs ensures access to high-quality, precision-engineered plates that meet the stringent demands of modern industries. TRUER offers:
- Superior Quality: Manufactured to the highest standards with rigorous quality control.
- Custom Solutions: Ability to tailor plates to specific applications and requirements.
- Innovation: Continuous development of new geometries and coatings to enhance performance.
- Support: Comprehensive customer service and technical support to assist with product selection and usage.
FAQ
Q1: What materials can tungsten carbide plates machine?
A1: Tungsten carbide plates can machine a wide range of materials, including metals, composites, and ceramics. Their high hardness and wear resistance make them particularly effective for cutting and shaping tough and abrasive materials.
Q2: How do I choose the right tungsten carbide plate for my application?
A2: Consider the material you are machining, the type of operation, and the desired surface finish. Consult the manufacturer’s guidelines and specifications to select a plate with the appropriate size, grade, and coating.
Q3: How often should tungsten carbide plates be replaced?
A3: The replacement frequency depends on the material being machined, the operating conditions, and the plate’s wear resistance. Regular inspections are essential to identify signs of wear, such as edge chipping or loss of cutting effectiveness.
Q4: Can tungsten carbide plates be resharpened?
A4: Yes, tungsten carbide plates can be resharpened, but the process requires specialized equipment and expertise. Resharpening can extend the tool’s life and maintain cutting performance, but it is often more cost-effective to replace the plates.
Q5: What are the benefits of coated tungsten carbide plates?
A5: Coated tungsten carbide plates offer enhanced wear resistance, reduced friction, and improved heat resistance. These benefits result in longer tool life, better surface finishes, and the ability to machine at higher speeds and feeds.