In the world of precision engineering and manufacturing, even the smallest discrepancies can have significant consequences. That’s where custom-sized carbide shim plates come into play, offering unparalleled accuracy and durability for a wide range of applications. These thin, meticulously crafted plates are essential for achieving precise alignments, compensating for wear, and ensuring optimal performance in demanding environments.
This comprehensive guide delves into the world of custom-sized carbide shim plates, exploring their properties, applications, advantages, and why choosing the right supplier can make all the difference.
What are Custom-Sized Carbide Shim Plates?
Carbide shim plates are precision-engineered components typically made from tungsten carbide, a remarkably hard and wear-resistant material. These plates are available in a wide range of thicknesses, often as thin as a few thousandths of an inch, and can be custom-manufactured to meet specific size and shape requirements.
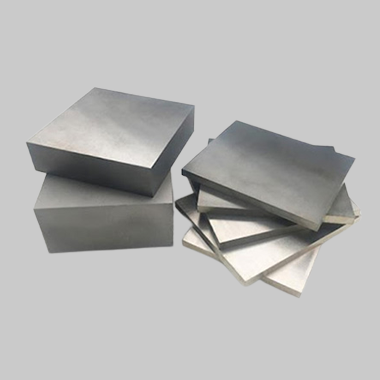
How Carbide Shim Plates Work: The Science of Precision Adjustment
Carbide shim plates function by creating a precise spacing between two components. By inserting a shim plate of a specific thickness, engineers can achieve exact alignments, compensate for manufacturing tolerances, or adjust the clearance between moving parts.
Applications Across Industries: Where Precision Matters Most
Custom-sized carbide shim plates find applications in a diverse range of industries, including:
- Aerospace: Ensuring precise alignments in aircraft engines, turbines, and control systems.
- Automotive: Adjusting valve clearances, bearing tolerances, and other critical components.
- Manufacturing: Used in tooling, fixturing, and machine building to achieve precise alignments and tolerances.
- Medical Devices: Creating precise spacing in surgical instruments, implants, and diagnostic equipment.
- Energy Production: Used in turbines, pumps, and other equipment to maintain optimal clearances and performance.
Carbide Shim Plate Properties: A Closer Look
Feature | Description |
---|---|
Material | Typically tungsten carbide, known for its exceptional hardness and wear resistance. |
Thickness | Available in a wide range of thicknesses, often down to 0.0005 inches (0.0127 mm) or less. |
Surface Finish | Can be ground, lapped, or polished to achieve specific surface roughness requirements. |
Flatness | Extremely flat and parallel surfaces ensure precise alignments and uniform load distribution. |
Accuracy | Manufactured to tight tolerances, often within ±0.0001 inches (0.00254 mm) or better. |
Table 1: Key Properties of Carbide Shim Plates
Advantages of Using Carbide Shim Plates: Why Choose Precision?
- Exceptional Durability: Carbide’s inherent hardness and wear resistance ensure long-lasting performance, even in demanding environments.
- Precise Alignments: Thin, custom-sized plates allow for extremely precise adjustments, critical for optimal equipment function.
- Increased Longevity: Shims help distribute wear evenly, extending the lifespan of components and reducing maintenance costs.
- Versatility: Available in various sizes, shapes, and thicknesses to meet diverse application requirements.
Manufacturing Custom-Sized Carbide Shim Plates: Precision Engineering at its Finest
Producing custom-sized carbide shim plates involves a series of specialized machining processes, including:
- Material Selection: Choosing the appropriate grade of tungsten carbide based on the application’s specific requirements.
- Blanking: Cutting the carbide material into rough blanks slightly larger than the final dimensions.
- Sintering: Heating the blanks to a high temperature under pressure to bond the carbide particles, creating a solid, dense material.
- Grinding: Using precision grinding machines to achieve the desired thickness and surface finish.
- Lapping: Further refining the surface flatness and parallelism to extremely tight tolerances.
- Inspection: Rigorous quality control checks ensure each shim plate meets the specified dimensional and surface finish requirements.
Types of Carbide Shim Plates: Exploring the Options
- Solid Carbide Shim Plates: Made entirely of solid carbide, offering maximum hardness and wear resistance.
- Carbide-Tipped Shim Plates: Feature a carbide tip brazed onto a less expensive substrate material, providing a cost-effective solution for applications requiring wear resistance at a specific point.
Market Trends: The Growing Demand for Precision
The global market for carbide shim plates is experiencing steady growth, driven by:
- Increasing Automation: Automated manufacturing processes demand precise alignments and tolerances, driving the need for high-quality shim plates.
- Stringent Industry Standards: Industries like aerospace and medical devices have stringent quality and safety regulations, requiring the use of reliable and durable components like carbide shim plates.
- Focus on Efficiency: Custom-sized shim plates help optimize equipment performance, reduce downtime, and extend component lifespan, contributing to overall operational efficiency.
Comparing Suppliers: Finding the Right Fit
Supplier | Location | Price Range (per piece, approximate) | Specialties |
---|---|---|---|
TRUER | Global | $10 – $50+ (depending on size, material, and complexity) | Wide range of materials and sizes, rapid prototyping, custom solutions |
Kennametal | US | $15 – $60+ | High-performance coatings, complex geometries |
Sandvik Coromant | Sweden | $20 – $75+ | Advanced materials, application-specific solutions |
ISC Tools | US | $12 – $55+ | Standard and custom sizes, quick turnaround times |
Table 2: Comparing Carbide Shim Plate Suppliers
Advantages and Disadvantages: Weighing the Pros and Cons
Advantages | Disadvantages |
---|---|
High Precision | Higher Cost Compared to Other Materials |
Exceptional Durability | Limited Flexibility |
Wide Range of Applications | Can Be Brittle Under Impact |
Table 3: Advantages and Disadvantages of Carbide Shim Plates
Related Components: Expanding the Precision Toolkit
- Carbide Wear Plates: Larger, thicker plates used to protect surfaces from abrasion and wear.
- Carbide Spacers: Provide precise spacing between components, often used in assemblies.
- Carbide Bushings: Cylindrical components used to reduce friction and wear in rotating applications.
Why Choose TRUER for Your Custom-Sized Carbide Shim Plate Needs?
- Uncompromising Quality: We use only the highest quality carbide materials and employ rigorous quality control measures throughout the manufacturing process.
- Precision Engineering: Our state-of-the-art equipment and experienced engineers ensure precise dimensions and tight tolerances.
- Customization Expertise: We specialize in custom-sized shim plates, working closely with you to meet your unique specifications.
- Competitive Pricing: We offer competitive pricing and strive to provide the best value for your investment.
- Exceptional Customer Service: Our dedicated team is committed to providing responsive and knowledgeable support throughout your experience.
FAQs: Answering Your Carbide Shim Plate Questions
1. What is the thinnest carbide shim plate available?
Carbide shim plates can be manufactured to incredibly thin tolerances, often as thin as 0.0005 inches (0.0127 mm) or even thinner, depending on the specific requirements.
2. How do I determine the correct shim plate thickness for my application?
Determining the ideal thickness involves considering factors like the desired clearance, manufacturing tolerances of mating components, and any anticipated wear. Consulting with a technical expert or using specialized measurement tools can help determine the optimal shim plate thickness.
3. Can carbide shim plates be used in high-temperature environments?
Yes, carbide materials exhibit excellent heat resistance and can withstand high temperatures. However, the specific temperature limit depends on the grade of carbide used.
4. What are the typical lead times for custom-sized carbide shim plates?
Lead times vary depending on factors like order size, complexity, and current production capacity. However, many suppliers strive to provide competitive lead times, often ranging from a few days to a few weeks.
5. How do I request a quote for custom-sized carbide shim plates?
Most suppliers offer online forms or contact information to request a quote. Providing detailed specifications, including material, dimensions, tolerances, and quantity, will help ensure an accurate and timely quote.