Overview
Tungsten carbide inserts are the cornerstone of modern machining, offering unparalleled durability and precision. This comprehensive guide delves into the world of tungsten carbide inserts, from their fundamental properties to their diverse applications. Whether you’re a seasoned machinist or an industry newcomer, this article will provide valuable insights into these essential tools.
Detailed Introduction
What Is a Tungsten Carbide Insert?
A tungsten carbide insert is a cutting tool made from tungsten carbide, a material known for its incredible hardness and wear resistance. These inserts are used in machining processes to cut, shape, and finish various materials, including metals and composites. They are highly valued for their ability to maintain a sharp cutting edge even under extreme conditions.
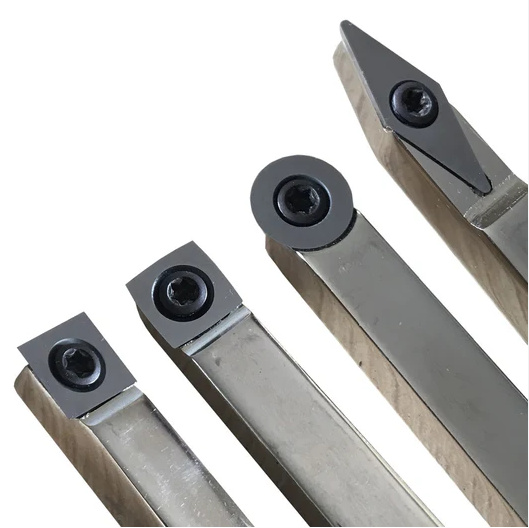
Working Principle
Tungsten carbide inserts function by utilizing their hard cutting edges to remove material from a workpiece. They are typically mounted on tool holders and rotated at high speeds. The hardness of tungsten carbide allows the insert to cut through tough materials, producing precise and clean finishes. The insert’s geometry and coating further enhance its cutting efficiency and longevity.
How to Use Tungsten Carbide Inserts
Using tungsten carbide inserts involves several critical steps:
- Tool Selection: Choose an insert with the appropriate geometry and grade for the material and type of machining operation.
- Setup: Secure the insert in the tool holder and ensure it is properly aligned.
- Machine Parameters: Set the machine’s speed, feed rate, and depth of cut according to the insert’s specifications.
- Machining: Perform the machining operation, monitoring for any signs of wear or damage to the insert.
- Inspection: Regularly check the machined workpiece for dimensional accuracy and surface finish.
Manufacturing Process
The manufacturing of tungsten carbide inserts involves several precise steps:
- Powder Preparation: Tungsten carbide powder is mixed with a binder, typically cobalt.
- Pressing: The mixture is pressed into the desired shape using a high-pressure press.
- Sintering: The pressed inserts are heated in a furnace to bond the particles together.
- Grinding: The inserts are ground to precise dimensions and geometries.
- Coating: Advanced coatings are applied to enhance wear resistance and performance.
Types and Categories
Tungsten carbide inserts come in various types and categories, each designed for specific applications. Understanding these types is crucial for selecting the right insert for your machining needs.
Turning Inserts
Turning inserts are specifically designed for lathe operations. They are used to remove material from rotating workpieces and come in various shapes such as:
- Square Inserts: Ideal for general-purpose turning and facing operations.
- Triangle Inserts: Provide multiple cutting edges and are suitable for profiling and finishing.
- Diamond Inserts: Used for precision turning and finishing applications due to their sharp cutting edges.
Milling Inserts
Milling inserts are used in milling machines to remove material from a workpiece. They come in different configurations to handle various milling operations:
- Square Milling Inserts: Commonly used for face milling and provide multiple cutting edges.
- Round Milling Inserts: Ideal for contour milling and creating smooth finishes.
- High-Feed Milling Inserts: Designed for high-speed material removal and greater productivity.
Drilling Inserts
Drilling inserts are used in drill bits for creating holes in workpieces. They are designed to handle high axial forces and provide excellent chip evacuation:
- Standard Drilling Inserts: Suitable for a wide range of materials and general-purpose drilling.
- Deep Hole Drilling Inserts: Designed for drilling deep holes with high precision and stability.
- Indexable Drilling Inserts: Allow for easy replacement of the cutting edge without changing the entire tool.
Grooving Inserts
Grooving inserts are used to cut grooves into workpieces. They are available in various shapes and sizes to accommodate different groove profiles and depths:
- Single-Edge Grooving Inserts: Provide precise groove cutting with minimal material removal.
- Multi-Edge Grooving Inserts: Offer multiple cutting edges for increased productivity and reduced downtime.
- Threading Inserts: Specialized grooving inserts used to cut threads into workpieces.
Market Trends
The market for tungsten carbide inserts is driven by the demand for high-precision machining tools. Key trends include the development of advanced coatings, the creation of specialized geometries for different materials, and the increasing use of CNC machines in various industries.
Specifications
Basic Information of Tungsten Carbide Inserts
Parameter | Description |
---|---|
Type | Turning, Milling, Drilling, Grooving |
Composition | Tungsten Carbide, Cobalt Binder |
Properties | High Hardness, Wear Resistance, Thermal Stability |
Features | Sharp Cutting Edge, Precise Geometries, Various Coatings |
Specifications | ISO, ANSI, DIN Standards |
Sizes | Varying Lengths, Widths, and Thicknesses |
Grades | Various Grades Based on Hardness, Toughness, and Wear Resistance |
Standards | ISO 9001, ASME B94.55M, ANSI B212.4 |
Comparative Analysis of Similar Products
Attribute | Tungsten Carbide Insert | High-Speed Steel (HSS) Insert | Ceramic Insert |
---|---|---|---|
Hardness | Very High | Moderate | High |
Wear Resistance | Excellent | Moderate | Excellent |
Heat Resistance | High | Moderate | High |
Cost | Moderate to High | Low | High |
Applications | Precision Machining | General Machining | High-Temperature Applications |
Applications
Tungsten carbide inserts are used across a wide range of industries due to their versatility and performance. Their ability to maintain sharp cutting edges and resist wear makes them invaluable in various applications:
- Automotive Industry
- Engine Component Machining
- Transmission Part Manufacturing
- Aerospace Industry
- Aircraft Structural Component Fabrication
- Turbine Blade Machining
- Medical Device Manufacturing
- Surgical Instrument Production
- Implant Manufacturing
- Oil and Gas Industry
- Drill Bit Production
- Pipe Threading
- General Manufacturing
- Precision Part Machining
- Tool and Die Making
Comparison of TRUER and Other Suppliers
Supplier Comparison for Tungsten Carbide Inserts
Supplier | Location | Price Range per Piece | Specialties |
---|---|---|---|
TRUER | USA | $10 – $20 | Custom Solutions, Advanced Coatings, High Precision |
Sandvik | Sweden | $12 – $25 | High Wear Resistance, Wide Range of Geometries |
Kennametal | USA | $15 – $30 | Durable Inserts, Innovative Designs |
ISCAR | Israel | $10 – $22 | Efficient Chip Control, High Performance |
Advantages and Limitations
Advantages and Limitations of Tungsten Carbide Inserts
Aspect | Advantages | Limitations |
---|---|---|
Durability | High hardness and wear resistance ensure long tool life. | Higher initial cost compared to standard tools. |
Performance | Maintains cutting edge at high temperatures, suitable for high-speed machining. | Requires precise alignment and setup for optimal performance. |
Precision | Provides excellent dimensional accuracy and surface finish. | Brittle nature can lead to chipping if not used correctly. |
Versatility | Applicable to a wide range of materials and industries. | Not suitable for all materials, particularly very soft or extremely hard materials. |
Why Choose TRUER
Choosing TRUER for your tungsten carbide insert needs ensures access to high-quality, precision-engineered tools that meet the stringent demands of modern machining. TRUER offers:
- Superior Quality: Manufactured to the highest standards with rigorous quality control.
- Custom Solutions: Ability to tailor inserts to specific applications and requirements.
- Innovation: Continuous development of new geometries and coatings to enhance performance.
- Support: Comprehensive customer service and technical support to assist with product selection and usage.
FAQ
Q1: What materials can tungsten carbide inserts machine?
A1: Tungsten carbide inserts can machine a wide range of materials, including steels, cast irons, non-ferrous metals, plastics, and composites. Their high hardness makes them particularly effective for cutting tough and abrasive materials.
Q2: How do I choose the right tungsten carbide insert for my application?
A2: Consider the material you are machining, the type of machining operation, and the desired surface finish. Consult the manufacturer’s guidelines and specifications to select an insert with the appropriate geometry, grade, and coating.
Q3: How often should tungsten carbide inserts be replaced?
A3: The replacement frequency depends on the material being machined, the machining parameters, and the insert’s wear resistance. Regular inspections are essential to identify signs of wear, such as edge chipping or loss of cutting effectiveness.
Q4: Can tungsten carbide inserts be resharpened?
A4: Yes, tungsten carbide inserts can be resharpened, but the process requires specialized equipment and expertise. Resharpening can extend the tool’s life and maintain cutting performance, but it is often more cost-effective to replace the inserts.
Q5: What are the benefits of coated tungsten carbide inserts?
A5: Coated tungsten carbide inserts offer enhanced wear resistance, reduced friction, and improved heat resistance. These benefits result in longer tool life, better surface finishes, and the ability to machine at higher speeds and feeds.