Introduction: The Backbone of Efficient Turning Operations
In the world of machining, general turning inserts are the workhorses that shape and refine cylindrical workpieces, driving efficiency and precision across industries. These versatile cutting tools, typically made from tungsten carbide, are essential for a wide range of turning operations, from roughing to finishing. This comprehensive guide delves deep into the realm of general turning inserts, exploring their types, applications, selection criteria, and key considerations for achieving optimal machining performance.
Understanding General Turning Inserts: What are they?
Defining the Cutting Tool:
A general turning insert is a precision-engineered cutting tool designed for use in turning operations, typically held in a tool holder mounted on a lathe. These inserts feature multiple cutting edges, allowing for indexing to a fresh edge as needed, maximizing tool life and minimizing downtime. They are specifically designed to remove material from the outer diameter of rotating workpieces, creating cylindrical shapes, shoulders, grooves, and other features.
Key Advantages of General Turning Inserts:
- Exceptional Hardness and Wear Resistance: Typically made from tungsten carbide, a composite material renowned for its hardness, general turning inserts can withstand the high temperatures and forces generated during machining, ensuring extended tool life and consistent performance.
- Indexable Design for Maximum Tool Utilization: The multiple cutting edges on a single insert allow for indexing, maximizing the use of the insert before replacement is necessary. This design reduces tooling costs and minimizes downtime associated with tool changes.
- Versatility in Turning Operations: General turning inserts are available in a wide range of geometries, grades, and coatings, making them suitable for a variety of turning operations, including roughing, semi-finishing, and finishing, across a wide range of materials.
- Cost-Effectiveness and Efficiency: The combination of extended tool life, versatility, and high cutting speeds offered by general turning inserts contributes to increased machining efficiency and reduced overall manufacturing costs.
Delving Deeper: Types, Geometries, and Grades
A World of Choices:
General turning inserts are available in a variety of types, each optimized for specific materials and machining operations. Some common types include:
- CVD Coated Inserts: Featuring a thin, hard coating applied via Chemical Vapor Deposition (CVD), these inserts offer excellent wear resistance, making them suitable for high-speed machining and demanding applications.
- PVD Coated Inserts: Utilizing Physical Vapor Deposition (PVD), these inserts have a thinner, more conformal coating, often with lower cutting temperatures, making them suitable for applications requiring sharper edges and improved surface finishes.
- Cermet Inserts: Comprising a ceramic-metallic composite, these inserts offer high hardness and wear resistance, particularly at elevated temperatures, making them suitable for machining hardened steels and other difficult-to-cut materials.
- CBN Inserts: Cubic Boron Nitride (CBN) inserts are exceptionally hard and wear-resistant, second only to diamond, making them ideal for machining hardened steels, cast iron, and other abrasive materials.
Decoding Insert Geometries: Shaping the Cut
Insert geometries, including rake angles, clearance angles, and chipbreakers, play a crucial role in chip formation, chip evacuation, and surface finish.
- Rake Angle: The angle between the rake face of the insert and a line perpendicular to the workpiece surface. Positive rake angles reduce cutting forces and generate thinner chips, while negative rake angles increase edge strength and improve chip control.
- Clearance Angle: The angle between the clearance face of the insert and the tangent to the workpiece surface at the cutting point. A sufficient clearance angle prevents rubbing between the insert and the workpiece, reducing heat generation and tool wear.
- Chipbreaker: A groove or indentation on the rake face of the insert that controls chip formation and directs chip flow away from the cutting zone, preventing chip buildup and improving surface finish. Different chipbreaker styles are available for various materials and chip control requirements.
Common General Turning Insert Shapes:
General turning inserts come in a variety of shapes, each designed for specific cutting actions and workpiece geometries. Here are some of the most common shapes:
- Round Inserts (S Shape): Offering a strong cutting edge and good chip evacuation, round inserts are versatile and suitable for continuous cutting operations, particularly for curved surfaces and profiling.
- Square Inserts (S Shape): Providing a straight cutting edge and good surface finish capabilities, square inserts are commonly used for facing, shoulder cutting, and turning operations requiring high accuracy.
- Triangle Inserts (T Shape): Featuring three cutting edges, triangle inserts offer good chip evacuation and are commonly used for medium to heavy-duty turning, particularly for interrupted cuts and roughing operations.
- Diamond Inserts (D Shape): With their sharp cutting edges and ability to handle high feed rates, diamond inserts are often used for finishing operations, achieving excellent surface finishes on various materials.
- Rectangle Inserts (R Shape): Providing a long, straight cutting edge, rectangle inserts are suitable for heavy-duty turning, deep grooving, and parting off operations.
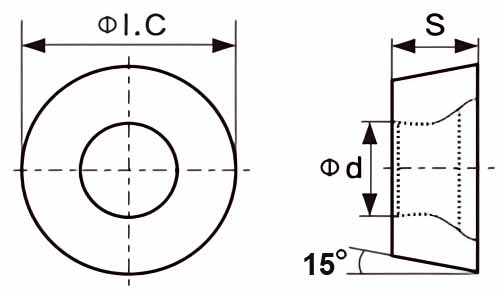
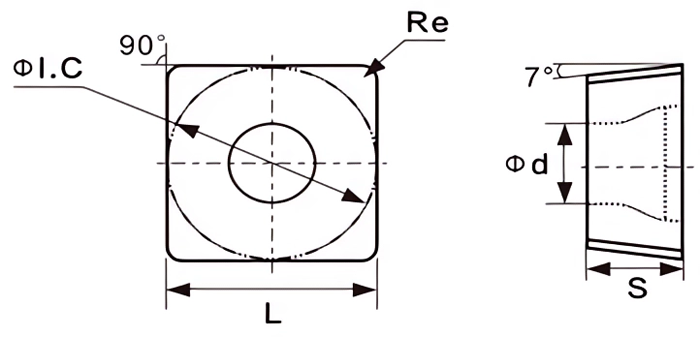
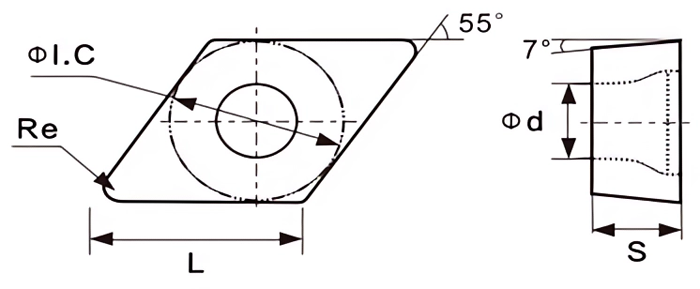
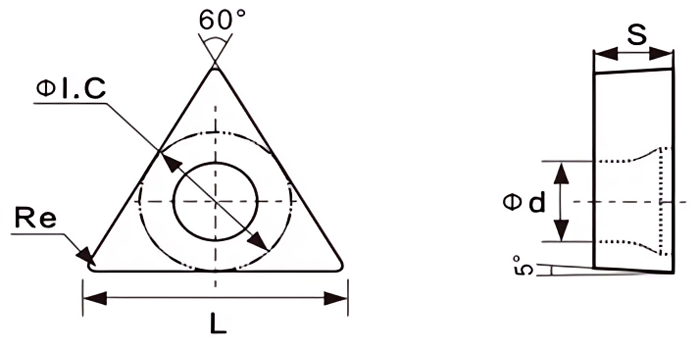
Understanding Carbide Grades: The ISO Classification System
Carbide grades, classified using the International Organization for Standardization (ISO) system, denote the specific properties and applications of tungsten carbide inserts. The ISO classification consists of a letter (application group) and a number (hardness and toughness).
- Application Groups:
- P: For machining steel, steel castings, and long-chipping materials.
- M: For machining stainless steels, high-temperature alloys, and other difficult-to-cut materials.
- K: For machining cast iron, non-ferrous metals, and non-metallic materials.
- Hardness and Toughness: The number following the letter indicates the transverse rupture strength (TRS) in N/mm² and the hardness (HV). Higher numbers generally indicate greater hardness and wear resistance but lower toughness.
Applications Across Industries: Where Precision Meets Performance
Driving Efficiency in Key Sectors:
General turning inserts are indispensable tools across a wide range of industries, including:
- Automotive: Manufacturing engine components, transmission parts, axles, and other critical components requiring high precision and durability.
- Aerospace: Producing landing gear components, engine parts, structural elements, and other parts demanding exceptional strength and reliability.
- Medical Device Manufacturing: Creating implants, surgical instruments, and other medical devices requiring tight tolerances and biocompatibility.
- Energy: Machining components for oil and gas exploration, power generation, and renewable energy systems, often under extreme conditions.
- General Manufacturing: Widely used in machine shops, fabrication facilities, and manufacturing plants for a variety of turning operations on a wide range of materials.
Comparing Suppliers: Navigating the General Turning Insert Market
Supplier | Location | Price Range (per insert) | Specialties |
---|---|---|---|
Sandvik Coromant | Sweden | $8 – $50+ | Wide range of inserts for various applications, advanced coatings, and geometries, known for innovation and high performance. |
Kennametal | USA | $7 – $45+ | High-performance inserts for demanding applications, innovative tooling solutions, and a focus on customer-specific solutions. |
TRUER | China | $6 – $40+ | Diverse insert geometries, cost-effective solutions, and a strong emphasis on research and development, known for its LOGIQ series. |
Walter Tools | Germany | $9 – $55+ | Comprehensive range of inserts, tooling systems, and cutting fluids, focus on precision, performance, and digital solutions. |
Weighing the Pros and Cons: Advantages and Limitations
Advantages | Limitations |
---|---|
Exceptional hardness and wear resistance | Higher initial cost compared to HSS tools but offset by longer tool life |
Indexable design for maximum tool utilization | Require a specific tool holder system and proper clamping |
Wide range of grades, geometries, and coatings to suit various applications | Proper selection and application are crucial for optimal performance and tool life |
High cutting speeds and feed rates for increased productivity | Can be brittle and prone to chipping under impact loads or improper use |
The TRUER Difference: Why Choose Us for Your General Turning Insert Needs?
Partnering with a Leader in Cutting-Edge Technology:
- Uncompromising Quality: We source our general turning inserts from reputable manufacturers, ensuring consistent quality, performance, and reliability for your most demanding machining operations.
- Application-Specific Expertise: Our team of experienced engineers can guide you in selecting the optimal inserts for your specific turning needs, considering materials, operations, desired outcomes, and cost-effectiveness.
- Competitive Pricing and Timely Delivery: We offer competitive pricing and strive to deliver orders promptly, minimizing downtime and maximizing your productivity. Our goal is to be your trusted partner in achieving machining excellence.
Want to buy a great quality Carbide Insert at the right price? Click here.
Frequently Asked Questions: Addressing Your General Turning Insert Queries
1. How do I choose the right carbide grade for my turning application?
Consider the material being machined (hardness, machinability), the type of turning operation (roughing, finishing), the desired tool life, and the cutting parameters (speed, feed, depth of cut). Consult supplier catalogs, online resources, or seek expert advice to determine the most suitable grade.
2. What factors influence the selection of insert geometry for turning?
Factors include the material being machined, the depth of cut, the desired surface finish, the machine tool capabilities (power, rigidity), and the chip control requirements. Each geometry offers advantages and disadvantages, so careful consideration is essential.
3. How do I know when to index or replace a general turning insert?
Signs of wear include increased cutting forces, poor surface finish, excessive heat generation, and chipping or breakage of the cutting edge. Regular inspection of the insert is crucial for preventing catastrophic tool failure and ensuring consistent machining quality.
4. What are the benefits of using coated general turning inserts?
Coatings, such as titanium nitride (TiN), titanium carbonitride (TiCN), and aluminum oxide (Al2O3), enhance tool life, hardness, wear resistance, oxidation resistance, and lubricity. They allow for higher cutting speeds, increased feed rates, and improved chip evacuation, ultimately boosting productivity.
5. How do I properly maintain and store general turning inserts?
Store inserts in a clean, dry environment, protected from impact, moisture, and extreme temperatures. Use appropriate chip brushes and cleaning methods to remove chips and debris after each use. Proper storage and maintenance can significantly extend the life of your inserts and ensure consistent performance.