Introduction: The Machining Powerhouse – 3 Flute End Mills
3 flute end mills are essential tools in the world of machining, prized for their ability to efficiently remove material and create a variety of features in workpieces. Their versatility and effectiveness have secured their place across industries ranging from aerospace and automotive to mold making and beyond. This comprehensive guide delves into the intricacies of 3 flute end mills, exploring their design, applications, advantages, and how to select the perfect tool for your machining needs.
Understanding the Fundamentals: What is a 3 Flute End Mill?
Defining the Tool:
A 3 flute end mill is a rotary cutting tool characterized by its three helical cutting edges, or flutes, which spiral along its body. These flutes not only facilitate material removal but also efficiently channel chips away from the cutting zone. The end mill’s design allows it to cut both axially, like a drill bit, and laterally, like a milling cutter, making it highly versatile for various machining operations.
Key Components of a 3 Flute End Mill:
- Cutting Edges: The three precisely ground edges, typically made from carbide or high-speed steel, responsible for cutting the workpiece.
- Flutes: The helical grooves running along the body of the end mill, providing pathways for chip evacuation. Three flutes offer a balance between chip removal and surface finish.
- Shank: The cylindrical portion of the end mill that is secured in the tool holder of a milling machine.
- Body: The main section of the end mill, housing the flutes and connecting the shank to the cutting edges.
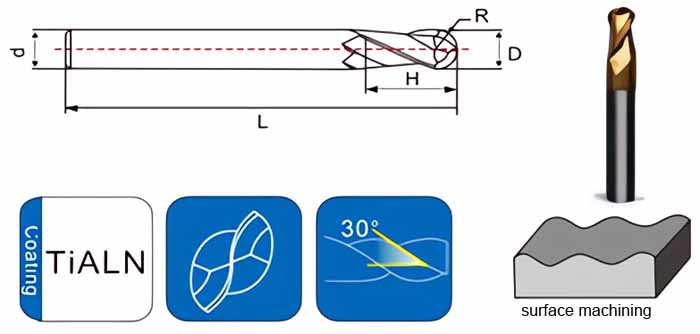
Delving Deeper: How 3 Flute End Mills Work
The Mechanics of Material Removal:
When a 3 flute end mill rotates at high speed within a milling machine, its cutting edges engage the workpiece material. As the tool moves along a programmed path, it removes material with each rotation, creating the desired features. The helical flutes play a crucial role in directing the chips upward and away from the cutting zone, preventing chip recutting and ensuring efficient material removal.
Manufacturing Process: From Raw Material to Precision Tool
- Material Selection: 3 flute end mills are commonly manufactured from solid carbide or high-speed steel (HSS), each offering different properties for specific applications. Carbide is known for its hardness, wear resistance, and ability to withstand high temperatures, making it suitable for machining harder materials. HSS, while not as hard as carbide, is more cost-effective and well-suited for machining softer materials.
- Blank Preparation: A cylindrical blank of the chosen material is cut to the desired length, forming the basis of the end mill.
- Grinding Operations: Precision grinding machines, often utilizing diamond grinding wheels, shape the blank into the final end mill geometry. This includes creating the cutting edges, flutes, shank, and overall dimensions with high accuracy.
- Heat Treatment (HSS Only): HSS end mills undergo heat treatment processes to enhance their hardness, toughness, and wear resistance, improving their performance during machining.
- Coating Application (Optional): To further enhance tool life, hardness, and performance, various coatings, such as Titanium Nitride (TiN), Titanium Carbonitride (TiCN), or Aluminum Titanium Nitride (AlTiN), can be applied using techniques like Chemical Vapor Deposition (CVD) or Physical Vapor Deposition (PVD).
- Quality Control and Inspection: Rigorous quality control measures are implemented throughout the manufacturing process to ensure the end mills meet stringent dimensional tolerances, surface finish requirements, and performance standards.
Navigating the Specifications: Choosing the Right 3 Flute End Mill
Understanding Key Parameters:
Feature | Description | Typical Values |
---|---|---|
Number of Flutes | Determines the number of cutting edges and influences chip evacuation and surface finish. | 3 |
Shank Diameter | The diameter of the cylindrical shank, determining the tool holder compatibility. | 1/8″, 3/16″, 1/4″, 3/8″, 1/2″, etc. |
Cutting Diameter | The diameter of the cutting portion of the end mill, determining the width of cut. | 1/8″, 3/16″, 1/4″, 3/8″, 1/2″, etc. |
Overall Length (OAL) | The total length of the end mill, from the tip of the cutting edge to the end of the shank. | 1″, 1-1/2″, 2″, 2-1/2″, 3″, 4″, etc. |
Flute Length | The length of the cutting portion of the flutes. | Varies based on overall length and tool design |
Helix Angle | The angle of the flutes relative to the axis of the end mill, influencing chip evacuation and cutting action. | 30 degrees, 45 degrees |
Material | The material from which the end mill is manufactured, impacting hardness, wear resistance, and cutting performance. | Solid Carbide, High-Speed Steel (HSS) |
Coating | A thin layer applied to the end mill to enhance tool life, hardness, and performance. | TiN, TiCN, AlTiN, Uncoated |
Applications Across Industries: The Versatility of 3 Flute End Mills
Unlocking Potential in Diverse Sectors:
- General Machining: Widely used for creating slots, pockets, profiles, chamfers, and various other features in a wide range of materials.
- Mold Making: Creating intricate mold cavities, details, and features that require a balance of material removal and surface finish.
- Aerospace: Machining lightweight, high-strength alloys like aluminum and titanium for aerospace components, where precision is paramount.
- Automotive: Producing engine components, transmission parts, and other automotive parts requiring precise tolerances and smooth finishes.
- Medical Device Manufacturing: Creating medical implants, surgical instruments, and devices that demand high precision and biocompatibility.
- Prototyping: Used in rapid prototyping to quickly create functional prototypes from various materials, allowing for design iterations and testing.
Weighing the Pros and Cons: Advantages and Limitations of 3 Flute End Mills
Making Informed Machining Decisions:
Advantages | Limitations |
---|---|
Balanced Chip Evacuation and Surface Finish: Three flutes provide a good balance between efficient chip removal and a relatively smooth surface finish. | Not as aggressive in chip removal as two flute end mills, especially in softer materials where chip welding can be a concern. |
Versatile Cutting Tool: Suitable for a wide range of machining operations and materials, making them a valuable asset in various industries. | Not as robust as four or more flute end mills for heavy-duty roughing operations, where increased cutting edges provide more stability and chip clearance. |
Good Surface Finish: Three flutes generally produce a smoother surface finish compared to two flute end mills, making them suitable for finishing operations or when a higher quality surface is desired. | Can be prone to chatter or vibration in certain applications, especially with longer tool lengths or when machining harder materials. |
Beyond the Basics: Interesting Facts about 3 Flute End Mills
Exploring the Nuances:
- Center Cutting vs. Non-Center Cutting: 3 flute end mills can be center cutting, with cutting edges that extend to the center of the tool, allowing for plunging operations, or non-center cutting, which are ideal for profiling and slotting.
- Variable Helix vs. Constant Helix: The helix angle of the flutes can be constant or variable. Variable helix designs help to reduce chatter and vibration during machining, improving surface finish and tool life.
- Corner Radius: The corner radius of the cutting edges influences the sharpness of corners and the tool’s ability to handle side loads. A larger corner radius provides more strength but may result in a less sharp corner.
Why Choose TRUER for Your 3 Flute End Mill Needs?
Partnering with a Leader in Precision Machining:
- Unwavering Commitment to Quality: TRUER maintains stringent quality control measures throughout the manufacturing process, from material selection to final inspection, to ensure exceptional tool performance and longevity.
- Application-Specific Expertise: Our team of experienced engineers understands the nuances of various machining applications and can guide you in selecting the optimal 3 flute end mill for your specific needs, maximizing efficiency and results.
- Competitive Pricing and Timely Delivery: TRUER offers competitive pricing and strives to deliver orders promptly, minimizing downtime and maximizing your productivity. We understand that time is money in the manufacturing world.
Frequently Asked Questions: Addressing Your 3 Flute End Mill Queries
1. What are the primary advantages of using a 3 flute end mill compared to a 2 flute end mill?
3 flute end mills offer a better balance between chip evacuation and surface finish compared to 2 flute end mills. They generally produce a smoother surface finish while still providing efficient chip removal in many materials, making them versatile for various applications.
2. When would I choose a 3 flute end mill over a 4 flute end mill?
Choose a 3 flute end mill when you need a balance of chip evacuation and surface finish, particularly in softer materials or when a slightly smoother finish is desired. Opt for a 4 flute end mill for increased rigidity, reduced chatter, and improved surface finish in harder materials or when performing heavier cuts.
3. Can I use a 3 flute end mill for roughing operations?
While 3 flute end mills can be used for light roughing, they are generally better suited for finishing operations or lighter cuts. For heavy-duty roughing, end mills with four or more flutes and a more robust design are recommended to handle the increased cutting forces and chip loads.
4. What is the significance of the helix angle on a 3 flute end mill?
The helix angle influences chip evacuation and cutting action. A higher helix angle promotes more aggressive chip removal, while a lower helix angle provides a smoother cut but with less efficient chip evacuation. Selecting the appropriate helix angle depends on the material being machined and the desired surface finish.
5. What are some common signs of wear on a 3 flute end mill, and how can I extend tool life?
Common wear signs include increased cutting forces, poor surface finish, excessive heat generation, and chipping or breakage of the cutting edges. To extend tool life, use appropriate cutting parameters for the material being machined, apply coolant effectively to reduce heat and friction, maintain a rigid setup to minimize vibration, and avoid excessive tool deflection.
Want to buy a great quality end mill at the right price? Click here.