Overview of Tungsten Carbide Cutting Inserts
Tungsten carbide cutting inserts are a cornerstone in the world of machining and manufacturing. These inserts, made from a hard and durable material, offer excellent performance in cutting, shaping, and finishing metal workpieces. If you’re in the market for top-notch cutting tools, understanding the intricacies of tungsten carbide inserts is essential. From their properties to applications, and how to choose the right one, we’ve got you covered in this comprehensive guide.
What Are Tungsten Carbide Cutting Inserts?
Tungsten carbide cutting inserts are small, replaceable cutting tools used in machining to cut and shape metals and other materials. They are favored for their exceptional hardness, wear resistance, and ability to maintain a sharp cutting edge, making them ideal for high-speed and precision machining tasks.
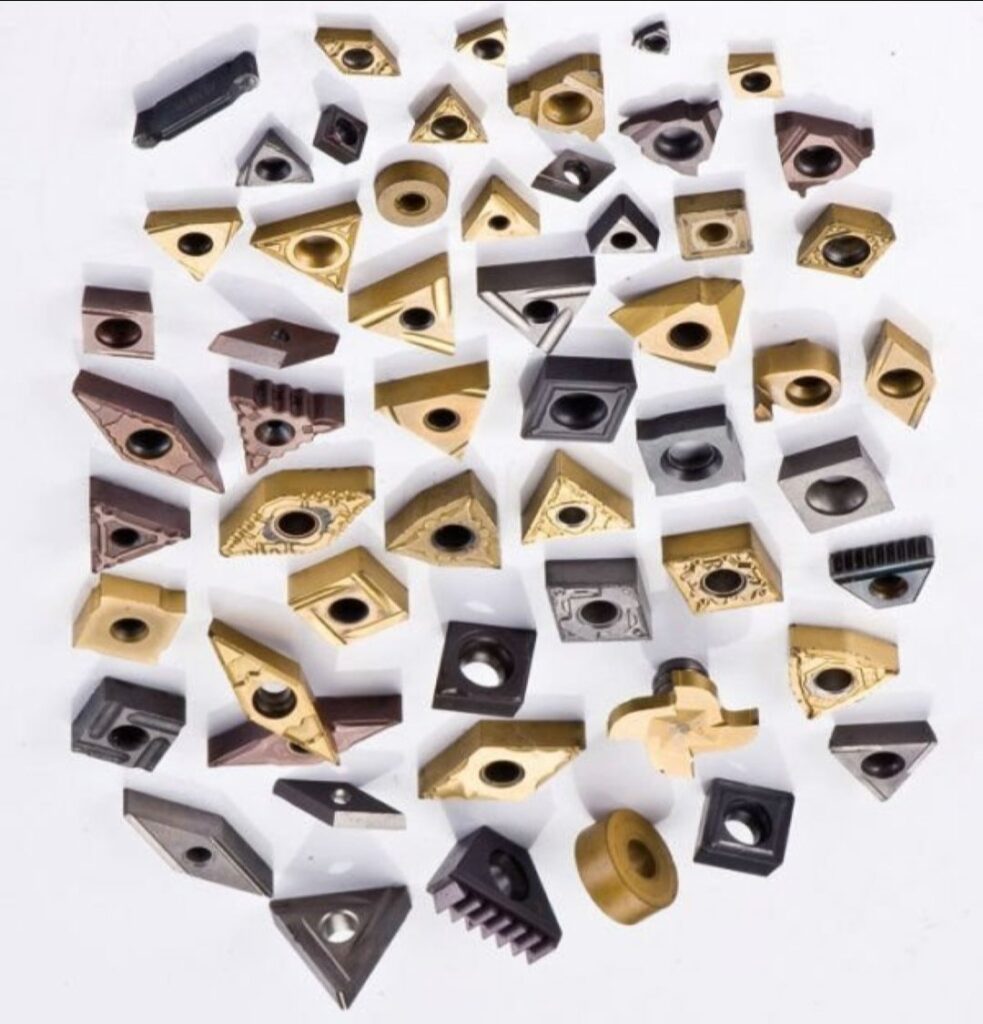
Types of Tungsten Carbide Cutting Inserts
Understanding the different types of tungsten carbide cutting inserts can help you select the best tool for your specific needs. Here are some of the primary types:
Type of Insert | Description |
---|---|
CNMG | Versatile insert with a 80-degree diamond shape, suitable for roughing and finishing operations. |
WNMG | Triangular insert with a 80-degree corner angle, ideal for general turning applications. |
TNMG | Triangular insert with a 60-degree corner angle, great for medium to finishing tasks. |
CCMT | Square insert with a single-sided design, perfect for finishing tasks. |
DCMT | Diamond-shaped insert with a 55-degree angle, used for finishing and precision turning. |
VCMT | Diamond-shaped insert with a 35-degree angle, ideal for fine finishing. |
SNMG | Square insert with a strong cutting edge, suitable for roughing operations. |
APKT | Rectangular insert with an advanced positive geometry, excellent for milling. |
RPMT | Round insert ideal for profile milling and high feed rates. |
SPMG | Square insert with a positive rake, used in grooving and parting applications. |
Applications of Tungsten Carbide Cutting Inserts
Tungsten carbide inserts are used across various industries due to their durability and efficiency. Here are some common applications:
Application | Description |
---|---|
Automotive Industry | Used in the manufacturing of engine components, transmission parts, and other critical systems. |
Aerospace Industry | Essential for precision machining of high-strength alloys used in aircraft components. |
Medical Device Manufacturing | Utilized for crafting intricate and precise medical instruments and implants. |
Oil and Gas Industry | Applied in the production of drilling equipment and other high-wear components. |
Tool and Die Making | Ideal for creating molds and dies used in metal stamping and plastic injection molding. |
General Manufacturing | Versatile for a variety of machining tasks in the production of various metal parts. |
Material Properties of Tungsten Carbide
The effectiveness of tungsten carbide inserts is largely due to their superior material properties. Let’s dive into the specifics:
Property | Description |
---|---|
Hardness | Extremely high, typically between 85-92 HRA, allowing them to cut through tough materials. |
Toughness | Good toughness to withstand impacts and shocks during machining. |
Wear Resistance | Excellent wear resistance, ensuring long tool life and consistent performance. |
Thermal Conductivity | High thermal conductivity helps dissipate heat, maintaining tool integrity and workpiece quality. |
Chemical Stability | Resistant to chemical reactions, making them suitable for machining reactive materials. |
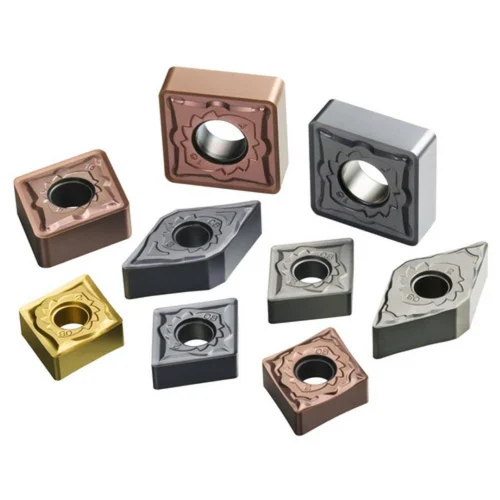
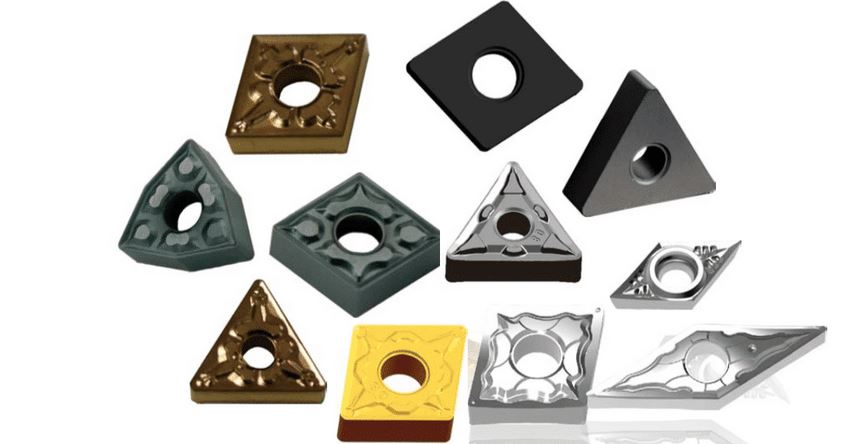
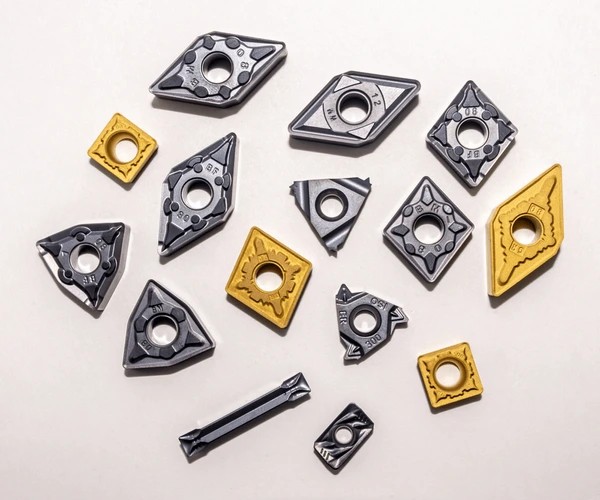
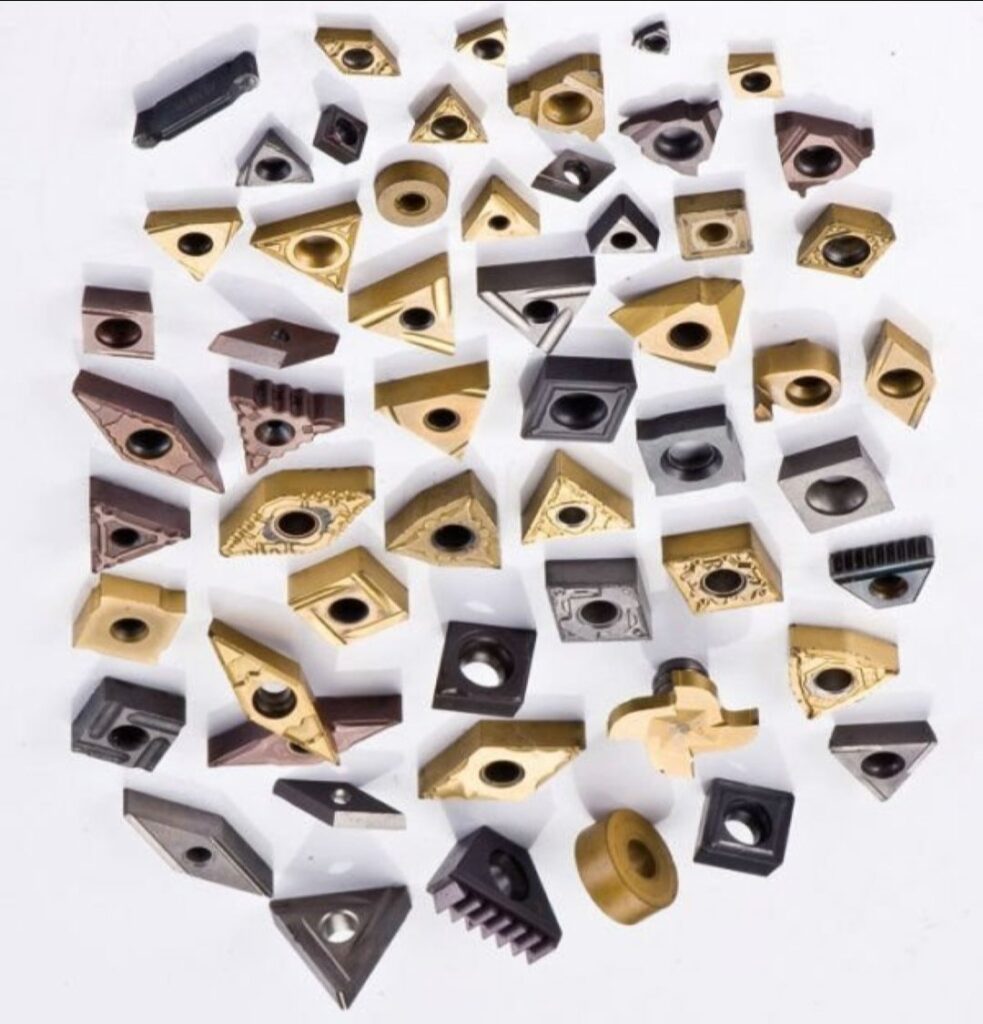
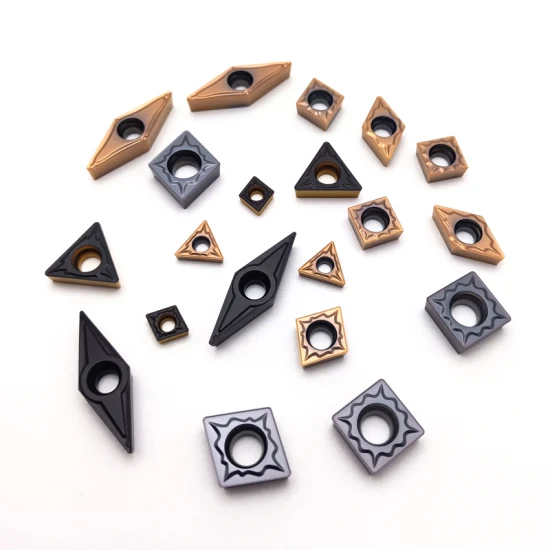
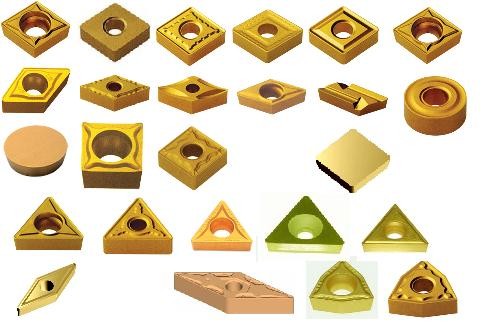
Composition and Characteristics of Tungsten Carbide Inserts
Tungsten carbide inserts are typically composed of tungsten carbide particles bound together with a metal, often cobalt. Here’s a breakdown of their composition and characteristics:
Component | Percentage | Characteristic |
---|---|---|
Tungsten Carbide | 70-94% | Provides hardness and wear resistance. |
Cobalt Binder | 6-30% | Adds toughness and binding strength. |
Other Additives | Up to 5% | Enhances specific properties like resistance to oxidation and grain growth. |
Hardness, Strength, and Wear Resistance
Tungsten carbide cutting inserts are known for their impressive hardness, strength, and wear resistance. Here’s a comparative look:
Metric | Value Range | Significance |
---|---|---|
Hardness (HRA) | 85-92 | Determines the ability to cut hard materials without deformation. |
Compressive Strength | 4000-9000 MPa | Indicates the maximum compressive load the material can withstand. |
Wear Resistance | High | Ensures long-lasting performance and reduced tool changes. |
Specifications, Sizes, Shapes, and Standards
When selecting tungsten carbide cutting inserts, it’s crucial to consider their specifications, sizes, shapes, and relevant standards:
Specification | Detail |
---|---|
ISO Standards | Conforms to international standards such as ISO 1832 for insert shapes and sizes. |
ANSI Standards | Follows American National Standards Institute guidelines for consistency and compatibility. |
Size Range | Available in a wide range of sizes to fit various tool holders and applications. |
Shape Varieties | Includes square, triangular, diamond, and round shapes to suit different machining tasks. |
Suppliers and Pricing Details
The market for tungsten carbide cutting inserts is diverse, with numerous suppliers offering various products. Here are some notable suppliers and pricing details:
Supplier | Price Range | Special Features |
---|---|---|
Kennametal | $10 – $50 per insert | Renowned for high-quality and innovative cutting solutions. |
Sandvik Coromant | $15 – $60 per insert | Offers a wide range of inserts with advanced coatings for enhanced performance. |
Mitsubishi Materials | $12 – $55 per insert | Known for their precision and durability in high-speed machining. |
ISCAR | $10 – $45 per insert | Provides cost-effective solutions with excellent wear resistance. |
Sumitomo Electric | $13 – $50 per insert | Specializes in inserts with high toughness and thermal stability. |
How to Select the Right Tungsten Carbide Cutting Inserts
Choosing the right tungsten carbide cutting inserts involves considering various factors such as material compatibility, machining conditions, and desired surface finish. Here’s a guide to help you make the right choice:
Consideration | Detail |
---|---|
Material to be Machined | Different inserts are optimized for various materials like steel, cast iron, or non-ferrous metals. |
Machining Conditions | Factors like cutting speed, feed rate, and depth of cut influence the selection. |
Tool Holder Compatibility | Ensure the insert fits the tool holder used in your machinery. |
Desired Surface Finish | Choose inserts designed for either roughing or finishing operations to achieve the desired finish. |
Advantages and Limitations of Tungsten Carbide Cutting Inserts
Tungsten carbide cutting inserts come with their own set of advantages and limitations. Understanding these can help you make an informed decision:
Aspect | Advantage | Limitation |
---|---|---|
Hardness | Can machine very hard materials with ease. | May be prone to brittleness under high impact. |
Wear Resistance | Long tool life, reducing the need for frequent replacements. | Higher initial cost compared to other materials. |
Thermal Conductivity | Maintains tool integrity and workpiece quality by dissipating heat. | Requires proper cooling systems to avoid overheating. |
Versatility | Suitable for a wide range of materials and applications. | May require different grades and coatings for specific tasks. |
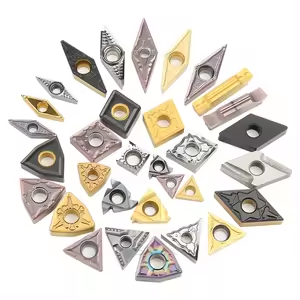
Conclusion
Tungsten carbide cutting inserts are indispensable tools in modern machining, offering unmatched hardness, wear resistance, and versatility. Whether you’re working in the automotive, aerospace, or general manufacturing industry, selecting the right tungsten carbide insert can significantly enhance your machining efficiency and product quality.
FAQs
Question | Answer |
---|---|
What is tungsten carbide? | A hard, wear-resistant material made of tungsten and carbon. |
Why are tungsten carbide inserts preferred in machining? | Due to their exceptional hardness, durability, and ability to maintain a sharp edge. |
Can tungsten carbide inserts be used on all materials? | They are suitable for most metals, but specific grades are optimized for different materials. |
How do I choose the right insert shape? | Based on the machining operation, tool holder compatibility, and desired finish. |
Are there different grades of tungsten carbide? | Yes, varying in hardness and toughness to suit different applications. |
What are the common shapes of tungsten carbide inserts? | Square, triangular, diamond, and round shapes. |
How do I maintain tungsten carbide inserts? | Regular inspection, proper storage, and using appropriate machining parameters. |
Where can I buy tungsten carbide cutting inserts? | From suppliers like Kennametal, Sandvik Coromant, Mitsubishi Materials, ISCAR, and Sumitomo Electric. |