Carbide tool inserts are crucial components in modern machining and metalworking processes. They offer superior cutting performance, longevity, and versatility, making them indispensable in various industrial applications. In this comprehensive guide, we’ll delve into everything you need to know about carbide tool inserts, including their types, applications, material properties, and how to select the right one for your needs.
Overview of Carbide Tool Inserts
Carbide tool inserts are replaceable tips used in machining to cut, shape, and finish materials. They are made from carbide, a composite material consisting of tungsten carbide particles bound together with a metal, usually cobalt. This combination gives carbide inserts their renowned hardness and durability. They are used in turning, milling, and drilling operations across various industries, from automotive to aerospace.
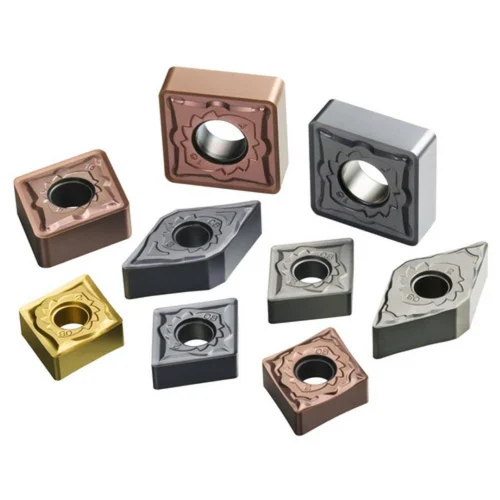
Types of Carbide Tool Inserts
Carbide tool inserts come in numerous shapes, sizes, and compositions, each suited for specific tasks and materials. Here’s a table to present the different types of carbide tool inserts:
Insert Type | Shape | Typical Applications |
---|---|---|
CNMG | Diamond | General turning, facing, and finishing |
TNMG | Triangle | Medium to heavy cutting, general purpose |
SNMG | Square | Roughing, interrupted cuts, heavy-duty applications |
VNMG | V-Shaped | Finishing, profiling, and high-precision applications |
WNMG | Hexagon | Medium to heavy roughing and interrupted cuts |
CCMT | Diamond | Light to medium cutting, high precision, and finishing |
DCMT | Diamond | Finishing and light cutting |
SCMT | Square | Medium to roughing, interrupted cuts, and heavy-duty applications |
RCMT | Round | Light to medium turning, profiling, and high-speed cutting |
APKT | Rectangular | Milling operations, high feed rates, and heavy-duty applications |
Applications of Carbide Tool Inserts
The versatility of carbide tool inserts makes them suitable for a wide range of applications. Here’s a table to present carbide tool insert applications:
Industry | Application |
---|---|
Automotive | Engine components, transmission parts, suspension systems |
Aerospace | Turbine blades, landing gear, structural components |
Medical | Surgical instruments, implants, prosthetics |
Oil & Gas | Drill bits, casing, downhole tools |
Manufacturing | General machining, tool and die making, mold manufacturing |
Electronics | Micro-machining, PCB manufacturing, semiconductor devices |
Material Properties of Carbide Tool Inserts
Understanding the material properties of carbide tool inserts is essential for selecting the right one for your application. Here’s a table to present material properties:
Property | Description |
---|---|
Hardness | High resistance to wear and deformation, typically measured in Rockwell or Vickers |
Toughness | Ability to absorb energy and resist chipping or fracturing |
Heat Resistance | Retains hardness and strength at elevated temperatures |
Chemical Stability | Resistant to corrosion and chemical reactions with work materials |
Thermal Conductivity | Efficiently dissipates heat generated during cutting |
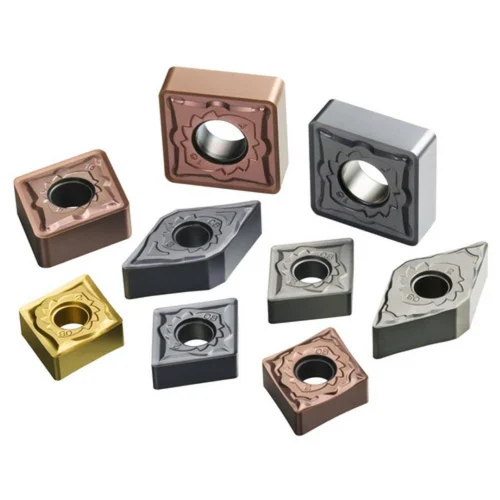
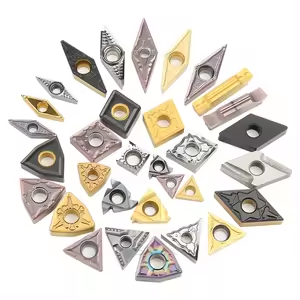
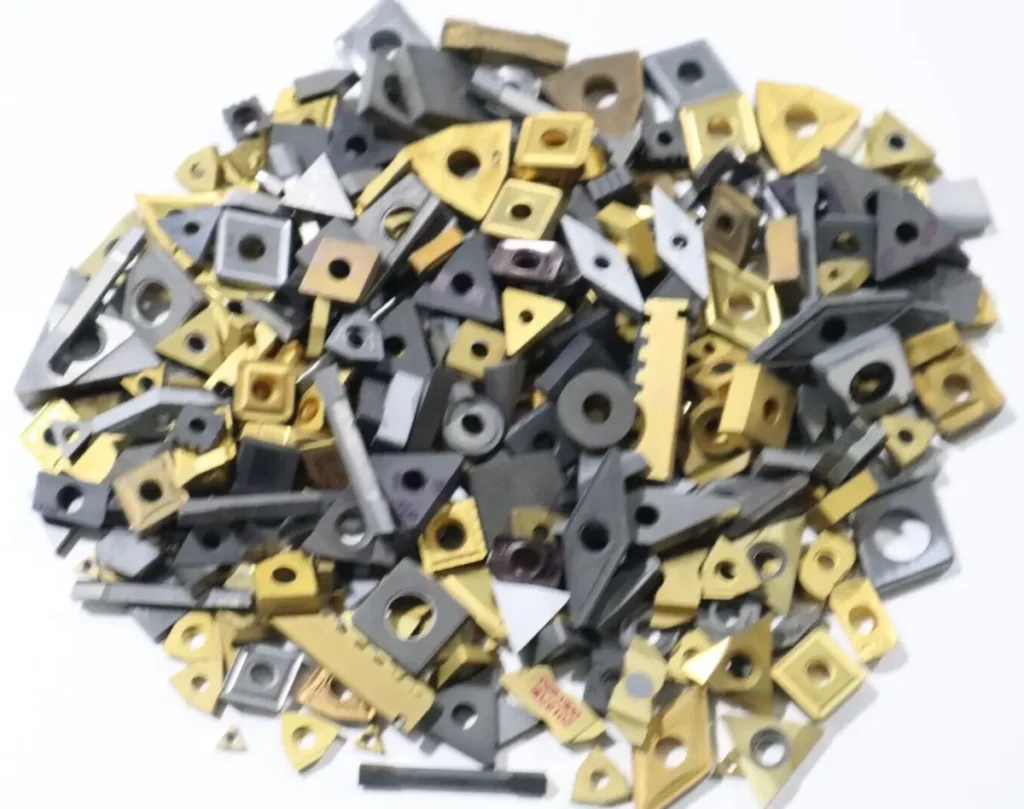
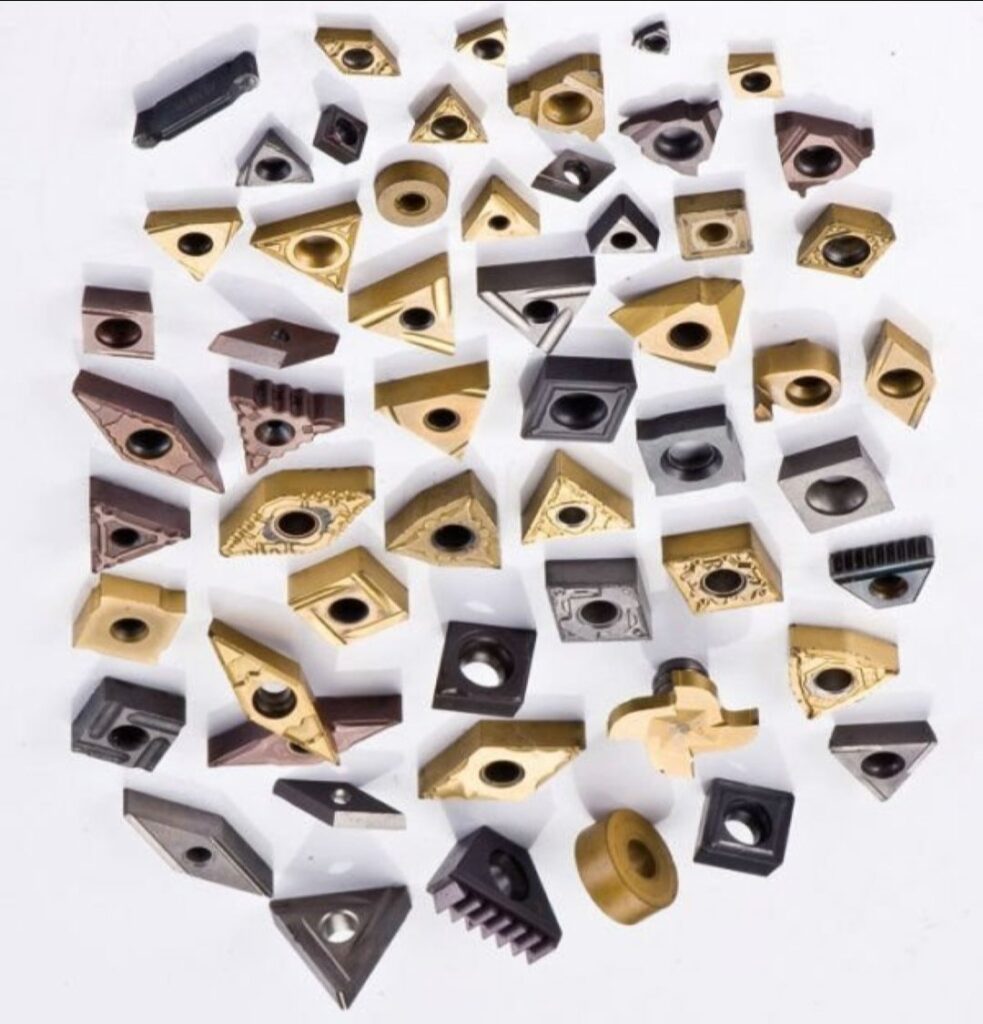
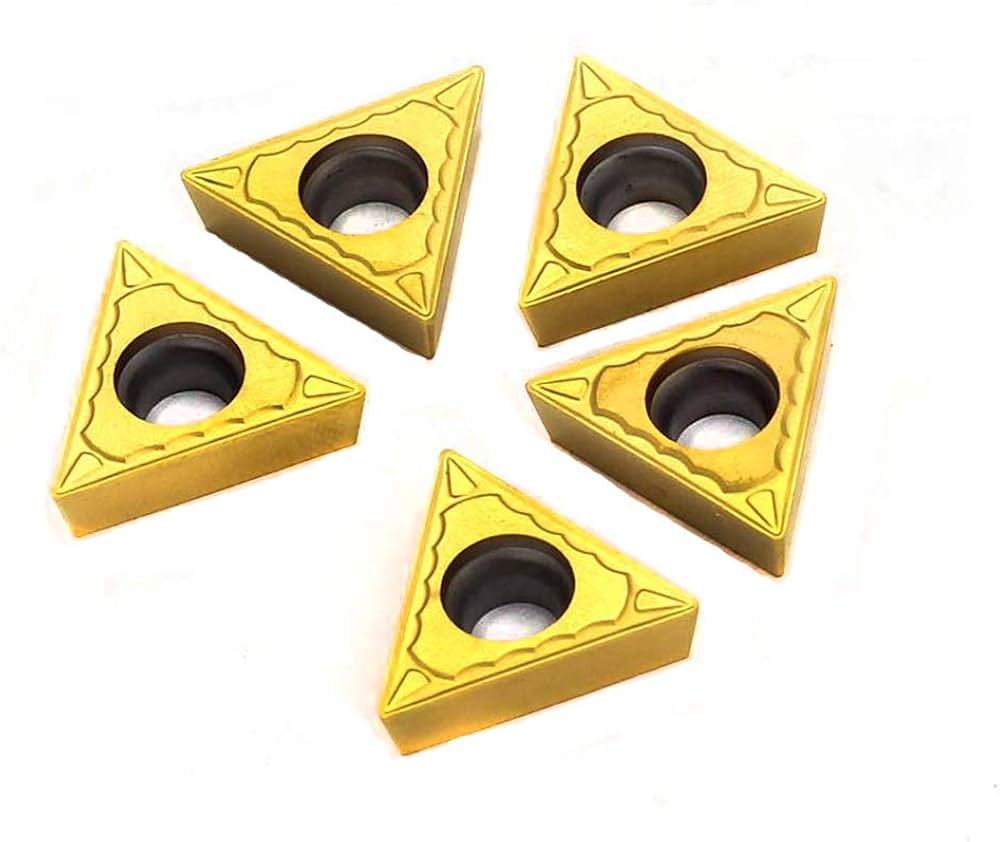
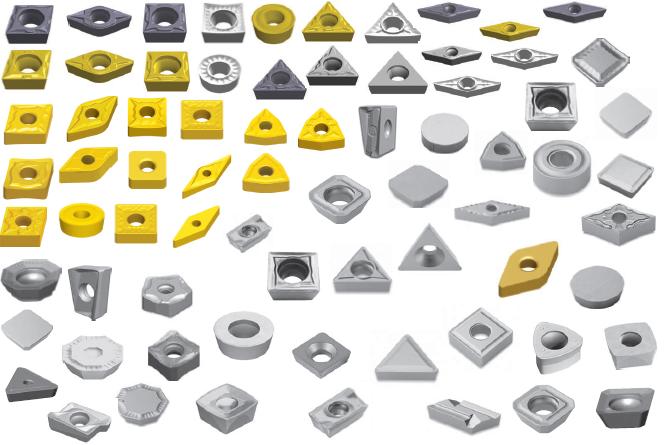
Composition and Characteristics of Carbide Tool Inserts
Carbide tool inserts are made from different grades of carbide, each offering unique characteristics. Here’s a table to present composition, properties, characteristics, etc.:
Grade | Composition | Characteristics |
---|---|---|
C1 | 97% WC, 3% Co | High wear resistance, used for non-ferrous materials |
C2 | 94% WC, 6% Co | Versatile, good for ferrous and non-ferrous materials |
C3 | 90% WC, 10% Co | Higher toughness, used for interrupted cuts |
C4 | 86% WC, 14% Co | Very tough, suitable for heavy-duty applications |
C5 | 81% WC, 19% Co | Highest toughness, used for very heavy-duty applications |
P10 | 92% WC, 8% Co, TiC/TaC additives | Good for high-speed finishing of steel |
P20 | 89% WC, 11% Co, TiC/TaC additives | General purpose turning and milling of steel |
P30 | 85% WC, 15% Co, TiC/TaC additives | Roughing and interrupted cuts in steel |
K10 | 94% WC, 6% Co, Cr3C2/TaC additives | Finishing and semi-finishing of cast iron |
K20 | 90% WC, 10% Co, Cr3C2/TaC additives | Roughing of cast iron and non-ferrous metals |
Hardness, Strength, and Wear Resistance
Here’s a table to show hardness, strength, and wear resistance of carbide tool inserts:
Grade | Hardness (HV) | Toughness (MPa) | Wear Resistance |
---|---|---|---|
C1 | 1800 | 1200 | Very High |
C2 | 1600 | 1500 | High |
C3 | 1500 | 1800 | Medium |
C4 | 1400 | 2200 | Medium |
C5 | 1300 | 2500 | Low |
P10 | 1700 | 1400 | High |
P20 | 1600 | 1600 | Medium |
P30 | 1500 | 2000 | Low |
K10 | 1650 | 1300 | High |
K20 | 1500 | 1800 | Medium |
Specifications, Sizes, Shape, Standards
Carbide tool inserts are available in various specifications, sizes, and shapes. Here’s a table to show specifications, sizes, shape, standards:
Shape | Size (mm) | Thickness (mm) | ISO Standard | ANSI Standard |
---|---|---|---|---|
Triangle | 12, 16, 20 | 3.97, 4.76, 6.35 | ISO 1832 | ANSI B212.4 |
Diamond | 11, 13, 16 | 2.38, 3.18, 4.76 | ISO 1832 | ANSI B212.4 |
Square | 12, 16, 20 | 3.97, 4.76, 6.35 | ISO 1832 | ANSI B212.4 |
Round | 16, 20, 25 | 4.76, 6.35, 9.53 | ISO 1832 | ANSI B212.4 |
Rectangular | 10, 15, 20 | 2.38, 3.97, 4.76 | ISO 1832 | ANSI B212.4 |
Suppliers and Pricing Details
Selecting the right supplier is crucial for ensuring the quality and performance of carbide tool inserts. Here’s a table with suppliers and pricing details:
Supplier | Location | Price Range (USD) | Contact |
---|---|---|---|
Kennametal | USA | 10-50 per insert | www.kennametal.com |
Sandvik Coromant | Sweden | 15-60 per insert | www.sandvik.coromant.com |
Iscar | Israel | 12-55 per insert | www.iscar.com |
Seco Tools | Sweden | 13-58 per insert | www.secotools.com |
Mitsubishi | Japan | 14-60 per insert | www.mitsubishicarbide.com |
Kyocera | Japan | 10-45 per insert | www.kyocera.com |
Sumitomo | Japan | 11-50 per insert | www.sumitomotool.com |
Walter Tools | Germany | 13-55 per insert | www.walter-tools.com |
Tungaloy | Japan | 12-54 per insert | www.tungaloy.com |
Ceratizit | Luxembourg | 15-60 per insert | www.ceratizit.com |
How to Select the Right Carbide Tool Inserts
Choosing the right carbide tool insert involves considering several factors, including the material being machined, the type of machining operation, and the specific requirements of the job. Here’s a table to show how to select the right carbide tool inserts:
Factor | Considerations |
---|---|
Material to be Machined | Hardness, toughness, and abrasiveness of the material |
Type of Operation | Turning, milling, drilling, finishing, roughing |
Cutting Speed | Higher speeds require inserts with better heat resistance |
Feed Rate | Higher feed rates may require tougher inserts |
Depth of Cut | Deeper cuts may require inserts with higher toughness |
Machine Tool Capability | Power, rigidity, and speed of the machine tool |
Surface Finish Required | Finishing operations may require inserts with finer grain structure |
Tool Life Expectations | Longer tool life may justify higher initial cost |
Comparing Advantages and Limitations of Carbide Tool Inserts
Here’s a table comparing advantages and limitations of carbide tool inserts:
Advantages | Limitations |
---|---|
High Hardness | Can be brittle, susceptible to chipping |
Excellent Wear Resistance | Higher cost compared to high-speed steel (HSS) |
Ability to Maintain Cutting Edge | Limited toughness compared to ceramics |
High Cutting Speeds | Requires precise handling and setup |
Versatility in Applications | Specialized inserts needed for specific tasks |
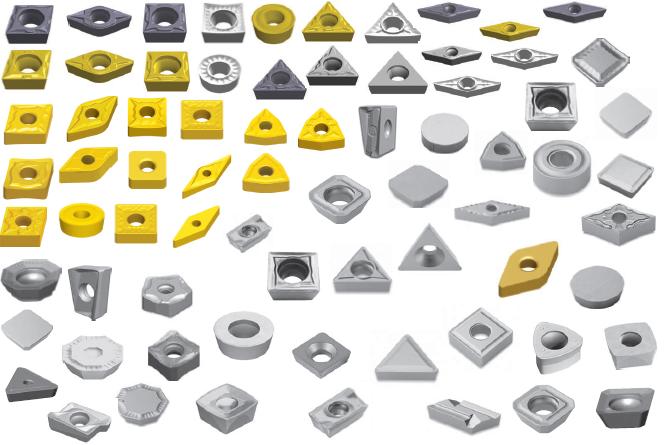
FAQ
What are carbide tool inserts used for?
Carbide tool inserts are used for cutting, shaping, and finishing various materials in machining operations such as turning, milling, and drilling.
Why are carbide inserts preferred over HSS tools?
Carbide inserts are preferred because they offer superior hardness, wear resistance, and the ability to maintain cutting performance at higher speeds and temperatures compared to high-speed steel (HSS) tools.
How do I choose the right carbide insert for my application?
Selecting the right carbide insert involves considering the material being machined, the type of machining operation, cutting speed, feed rate, and the required surface finish. Refer to the selection table provided above for detailed guidance.
What are the different grades of carbide inserts?
Carbide inserts come in various grades, each tailored for specific applications. For example, C1 is highly wear-resistant for non-ferrous materials, while P20 is a general-purpose grade for turning and milling steel.
Can carbide inserts be resharpened?
In most cases, carbide inserts are not resharpened. Instead, they are replaced once worn out or damaged, as resharpening can compromise their precision and performance.
How long do carbide inserts last?
The lifespan of carbide inserts depends on factors such as the material being machined, cutting conditions, and the type of operation. Proper selection and usage can maximize their longevity.
What are the advantages of using coated carbide inserts?
Coated carbide inserts offer additional benefits, including increased wear resistance, reduced friction, and extended tool life, particularly in high-speed and high-temperature applications.
Where can I buy carbide tool inserts?
Carbide tool inserts can be purchased from various suppliers such as Kennametal, Sandvik Coromant, Iscar, Seco Tools, and many others. Refer to the supplier table for more details.
Are there different shapes of carbide inserts?
Yes, carbide inserts come in different shapes like triangle, diamond, square, round, and rectangular, each suited for specific cutting tasks and applications.
What is the cost range for carbide inserts?
The cost of carbide inserts varies based on the supplier, grade, and specific type. Prices generally range from $10 to $60 per insert. Refer to the supplier pricing table for detailed information.
In conclusion, carbide tool inserts are essential for efficient and precise machining operations. By understanding their types, applications, properties, and how to select the right insert, you can optimize your machining processes and achieve superior results.