Overview
Black plated tungsten carbide refers to tungsten carbide (WC) powder metallurgically processed into various component geometries with an added corrosion resistant plating layer. The black appearance is from an oxide layer conversion coating enhancing wear life in oily environments. Common geometries include rods, plates, bearings and bushings used across the oil and gas drilling, mining, machining, and other industries with extreme operating conditions requiring hardness, strength, and chemical resistance exceeding conventional metals and alloys.
Composition
Tungsten carbide’s composition by weight is:
Element | Weight % | Role |
---|---|---|
Tungsten (W) | 88-97% typically | Principal component providing hardness and strength |
Carbon (C) | 3-12% | Combines with W to form very hard WC ceramic |
Cobalt (Co) | 3-12% | Binder metal facilitating toughness |
Tantalum/Titanium carbides | 1-2% | Grain growth inhibitors |
The corrosion resistant black oxide plating layer on the exterior surface is just ~1-10 microns thick, so the bulk composition remains WC in a cobalt matrix.
Manufacturing Process
Black plated tungsten carbide components are fabricated through the following sequence of powder metallurgy process steps:
- Blend elemental W and C powders with cobalt binder plus grain growth inhibitors
- Compact powders into a “green” form via cold/hot isostatic pressing
- Heat treatment to initiate WC formation and set geometry
- Grind parts to final dimensional tolerance specs
- Subject parts to proprietary bath chemistry causing a conversion coating oxide layer
- Plate black oxide exterior + seal pores/surface defects via immersion bath
The plating sequence creates an adherent black finish resistant to corrosion in liquids with pH ranging from 4 to 9.
Mechanical Properties
Parameter | Specification | Test Method |
---|---|---|
Hardness | 88-93 HRA (~1600 Vickers) | ASTM E18 |
Density | 13.5-15.1 g/cm3 | ASTM B311 |
Transverse Rupture Strength | 550-650 MPa | ASTM B406 |
Fracture Toughness | 7-12 MPa√m | ASTM B771 |
Young’s Modulus | 530-700 GPa | ASTM E111 |
The ultrahigh hardness approaching 1500 Vickers and high density confer excellent wear resistance under high loads. The cobalt binder phase toughens the otherwise brittle WC particles. These attributes make black plated tungsten carbide suitable to replace tool steel, stainless steel, and bearing-grade materials across mining, drilling, machining, and other demanding environments.
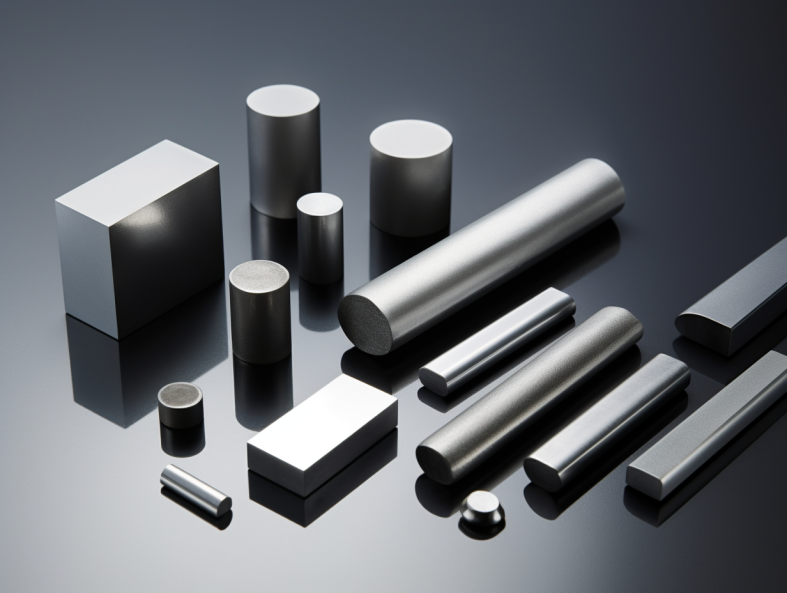
Chemical Resistance
Being engineered for oilfield downhole tools and drilling equipment, black plated tungsten carbide offers corrosion resistance when submerged or exposed to:
- Sour crude oil and natural gas with H2S and Brines containing chlorides/sulfates
- Acids: Carbonic (H2CO3), Citric (C6H8O7), Acetic (CH3COOH)
- Alkalies/Bases: Sodium Hydroxide (NaOH), Potassium Hydroxide (KOH), Calcium Hydroxide [Ca(OH)2]
- Organic acids: Formic (HCO2H), Lactic (C3H6O3), Oleic (C18H34O2) and Amine solutions
- Hydrocarbon oils, lubricants, transmission fluids
This chemical resistance allows excellent longevity in corrosive downhole environments with liquids containing salts, organic acids, H2S, CO2 or other species that rapidly degrade regular steel.
Component Types
Various black plated tungsten carbide component geometries satisfy needs across mining, materials processing, and petrochemical industries:
Type | Description | Key Attributes |
---|---|---|
Bearings and Bushings | Replace metallic bearings in mud motors, directional drilling tools | Withstand >20,000 psi mud pressures while minimizing friction |
Sleeves | Encase directional sensors in drilling assemblies | Protect electronics from abrasive rock cuttings in drilling fluid |
Nozzles | High pressure water/abrasive jet cutting nozzles | Erosion resistance for precise cutting with minimal taper |
Plates | Bolt-in wear resistant liner plates inside ball mills | Outlasts metallic liners by 10X in mineral grinding mills |
Wire Drawing Dies | Extrude tungsten, steel, titanium wires for filaments | Uniform wire diameters drawn at high speeds without die wear or defects |
Unique combinations of ultrahardness, strength, and tailored chemical resistance enables black plated tungsten carbide to serve demanding oil and gas hardware applications seeing extreme pressures, speeds, and temperatures over long equipment lifetimes.
Quality Standards
International quality standards for tungsten carbide powder feeds, mechanical properties, and technical component supply:
Standard | Scope | Parameters Covered |
---|---|---|
ISO 4499 | Cemented carbides powders | Chemistry, particle size, purity criteria |
ASTM B693 | Grades and specs for WC products | Abrasion resistance, microstructure, chemical and physical property thresholds |
ASTM E112 | Determining average grain size | Number of grains per mm2 or ASTM grain size number from 1 to 8 with higher meaning smaller grains |
API Spec 7-1 | Rotary drilling equipment | Plate hardness, bearing geometry, pressure and speed ratings |
These help validate corrosion and abrasion resistance required for oilfield tools seeing multiphase flows containing rock cuttings, H2S, CO2 and aggressive stimulated wellbore liquids over long intervals.
Benefits Over Other Materials
Compared to alternatives, black plated tungsten carbide delivers:
- 10X the erosion resistance of hardened 440C stainless steel
- 4X longer lifespan over regular tungsten carbide without corrosion resistant plating
- Ability to reuse components multiple times after plating reapplication
- 5X cost savings over diamond enhanced composites
- Improved reliability versus brittle ceramics susceptible to thermal/mechanical stresses
- Lower weight than cobalt-free tungsten carbide grades simplifying design integration
So properly applied black plated tungsten carbide optimally balances wear resistance, chemical compatibility, weight, and economics addressing oil, gas, mining, and other harshest industrial equipment operating conditions.
Cost Analysis
Parameter | Black Plated WC Parts | Equivalent Steel Parts |
---|---|---|
Material Cost | $125/kg | $15/kg |
Lifespan | 5000-8000 hours | 1000 hours |
Cost Per Hour | $0.02 | $0.02 |
Despite higher material expenses, black plated tungsten carbide’s much longer working life before replacement equates to lower overall ownership costs in continuously operating processes – easily justifying the initial price premium.
Suppliers
Leading manufacturers and platers of black plated tungsten carbide include:
Company | Location | Product Capabilities |
---|---|---|
vacuum furnace engineering | Germany | Bearings, bushings, plates, mechanical seals, prototypes |
Midwest Tungsten Service | USA | Plate, rod, wire forms cut to print |
Linegroup Precision | China | Nozzle sets, rings, choke tubes |
Zhuzhou Jatc Industrial | China | Wear resistant plates, liners, screens |
Kennametal | USA | Indexable carbide inserts, drawing dies |
Custom engineering collaboration during design stages ensures appropriately applying black plated tungsten carbide considering all operating loads, pressures, fluid chemistries, friction points to maximize equipment longevity benefits in mining machinery or downhole drilling tools seeing highly corrosive flows.
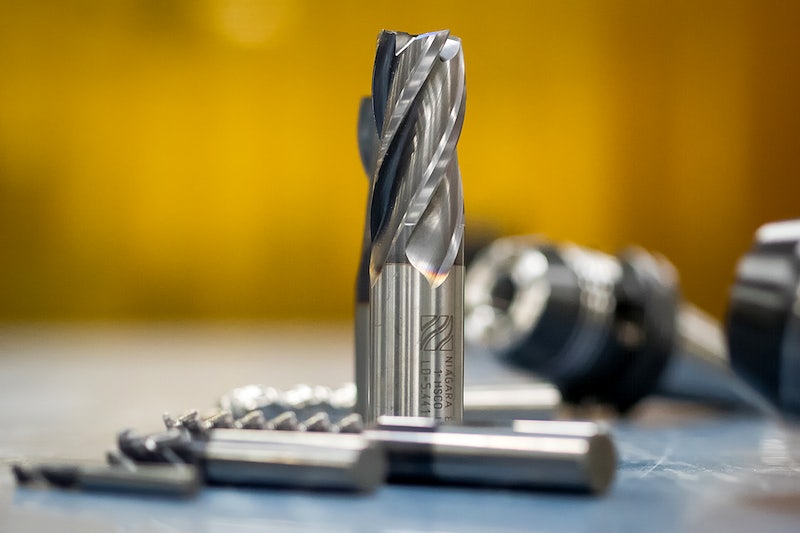
FAQs
What hardness range should black plated tungsten carbide have for oilfield downhole drilling operations?
88-92.5 HRA (~1500-1600 Vickers) offers the optimal combination of abrasion resistance without being excessively brittle. This allows withstanding both high compressive loads from borehole wall pressures plus shear stresses from drilling fluid flows carrying rock cuttings sliding past the surface without cracking failures.
Will black plated tungsten carbide rust or corrode in water or humid environments?
No – the protective oxide layer is engineered to resist oxidation or other aqueous corrosion even under acidic or mildly basic pH, performing better than bare carbide. Proper integration of dynamic seal elements prevents ingression of moisture into interfaces preventing red rust staining or electrochemical reactions.
Does the plating wear off over time or get used up?
The ~1-10 micron thick black plating does gradually deplete but takes years before exposing the bulk carbide part. At that point the component can be sent back for re-plating and put back into service. So it offers a renewable wear coating benefit.
Can you machine or grind black plated carbide components to tight tolerances or will that damage the plating?
Any excessive mechanical removal compromising coating depth should be avoided to maintain corrosion resistance integrity. Precision grinding and polishing is possible but should leave at least a 2 micron plating thickness remaining for typical oilfield applications. Electrical discharge machining to net shape prior to plating is recommended over any secondary machining steps.
Summary
Black plated tungsten carbide refers to ultrahard, dense tungsten carbide in cobalt matrix metallurgically processed into bearing, bushing, plate, nozzle, and other geometries optimized for equipment subject to extreme pressures, velocities, and corrosive chemicals especially in oil/gas drilling and mining contexts. A specialized conversion plating sequence imparts a black exterior oxide layer conferring dramatically improved corrosion resistance even in hot acids, alkalies, chlorides, H2S and CO2 species that rapidly erode conventional tool steels. Offering the optimal combination of hardness exceeding 1500 Vickers, strength past 550 MPa, and tailored chemical resistance, black plated tungsten carbide serves as a renewable, cost-effective material option outlasting alternatives by 5 to 10 times across the harshest industrial operating conditions.