Tungsten carbide saw tips are an extremely hard and durable material used on the cutting edges of saw blades. This article provides an overview of tungsten carbide tips, their composition, properties, applications, specifications, suppliers, and comparisons to other saw tip materials.
Overview of tungsten carbide saw tip
Tungsten carbide, often referred to as carbide, is made by mixing tungsten powder and carbon at high temperatures. This produces an incredibly tough composite that is harder than most steels and maintains strength at high temperatures.
These properties make carbide an ideal material for cutting tools and saw tips. Carbide-tipped saw blades last much longer between sharpenings and can cut faster and smoother than steel blades.
Carbide tips are commonly brazed or welded onto the teeth of circular, chop, and other types of saws used to cut metal, masonry, concrete, wood, plastic, and more. They improve cutting performance and blade life significantly.
Composition
Tungsten carbide used for saw tips is a composite containing between 3-25% carbon compounds and the balance tungsten metal. It may also include small amounts of other carbides like tantalum, titanium, or niobium carbide.
The exact composition depends on the grade and application requirements:
- Higher carbon content increases hardness and wear resistance
- Higher tungsten content improves toughness
Common grades have 6-15% cobalt added as the metal binder that holds the composite together during sintering.
Properties
The key properties that make carbide superior for saw tips are:
- Extreme hardness – 89-93 on the Rockwell A scale, compared to 60-65 for tool steel
- Very high strength and toughness
- Excellent wear and abrasion resistance
- Resists deformation at high cutting temperatures
- Maintains a sharp cutting edge
These characteristics significantly improve cutting speed, reduce cutting forces, and increase blade life relative to other tip materials.
Carbide is also somewhat brittle however, so the blades may chip if subjected to sharp impacts. Proper use is important to maximize service life.
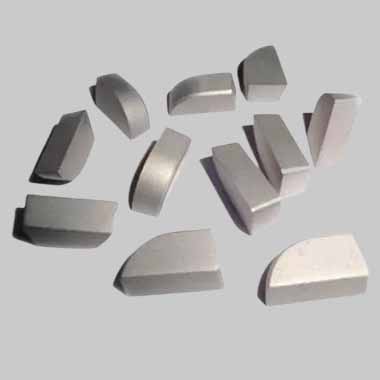
Applications and Uses
Tungsten carbide-tipped saw blades are used to cut virtually all types of materials including:
Material | Details |
---|---|
Metals | All types of steel, stainless steel, cast iron, aluminum, copper etc. Can cut much faster than high speed steel blades. |
Masonry | Concrete, cinder blocks, brick, tile, stone |
Asphalt | Fast cutting of asphalt paving |
Wood | Manmade wood products, chipboard, plywood. Carbide tips improve cutting rate and reduce gumming relative to steel. |
Plastics | Fiberglass, ABS, PVC piping and sheets, nylon, plexiglass |
Composites | Carbon fiber, fiberglass |
The extreme hardness of carbide allows fast, smooth cutting of very abrasive materials like concrete and cinder block which quickly wear down steel blades:
Common saw types utilizing carbide teeth include:
- Circular saws
- Masonry / tile saws
- Concrete cut-off saws
- Chop saws
- Cut-off machines
- Hole saws
- Band saws
- Reciprocating saws
Specifications of tungsten carbide saw tip
Tungsten carbide saw tips are produced in several grades and configurations to suit different applications:
Sizes
- Range from micrograin tips <0.5 mm to large teeth >25 mm
- Based on desired feed rate, cut quality, machine power
Grades
Grade | Hardness | Toughness | Description |
---|---|---|---|
C1/K01/H10 | Very high | Low | Maximum wear life for abrasive non-ferrous materials |
C2/K10/H15 | High | Medium | Ferrous materials, medium impacts |
C3/P10/H25 | Medium | High | Tougher grades ability to resist breakage |
C4/P20/H30 | Low | Very high | Used in mining and construction tools |
Brazing
- Carbide tips brazed with silver solder or nickel alloys
- Braze integrity critical for safety and performance
Connection Style
- Tips may be brazed flat or with + shaped ridges
- Raised inserts provide extra braze area
Tooth Geometry
- Alternate top bevel, double bevel, triple chip grinds
- Relief angles, rake angles, and tip shape designed for material type
Quality Standards
- ISO 513 – Classification and application of hard cutting materials
- ANSI B74.5 – Saw blades are classified by material, size, tooth geometry, and performance
Pricing
Unit | Price Range |
---|---|
Tungsten carbide saw blade | $50 – $500 |
10 inch carbide tipped masonry blade | $100 – $250 |
Carbide insert replacement kit | $10 – $200 |
100 pack of carbide laser cut inserts | $15 – $150 |
Replacement tips cost more than steel but can last 10-100x longer. Carbide blades have much higher up front cost but save significantly over lifespan.
Cost Factors:
- Carbide grade and source material quality
- Size of saw blade
- Tooth count
- Complexity of grind/braze
- Quality control and tolerances
Ways To Save:
- Have old blades re-tipped vs new
- Buy blades without branding
- Purchase segmented kits for self-assembly
- Import direct from manufacturers
Suppliers and Manufacturers
Carbide saws and replacement inserts are sold globally. Some top producers include:
Company | Location | Notes |
---|---|---|
Addison & Co. | USA | Broad range, custom blades |
Bosch | Germany | Power tools and accessories |
Diager | Spain | Specialists in circular saws |
Ehwa Diamond | Korea | Diamond and carbide composites |
Forrest Manufacturing | UK | Chop saws and metal cutting |
Freud | Italy | Circular saw sets for woodworking |
Irwin Industrial Tools | USA | Part of Newell Brands, retail channel |
KHD Humboldt Wedag | Germany | Cement and mining equipment |
LEUCO | Germany | Woodworking and specialty saws |
Morse Cutting Tools | USA | Carbide tipped band saws |
Neue Herkules | Germany | Metal industry supplier |
Roberts Carbide | USA | Aftermarket tips and tooling |
The Blade Manufacturing Company | UK | Custom masonry and asphalt saws |
Vollmer of America | USA | CNC grinders for carbide and diamond |
Online retailers like Amazon and woodworking outlets carry a selection of blades for end users. Building trade stores will stock common concrete, metal, and wood cutting blades.
Buying direct from manufacturers, joining regional distribution networks, or importing in quantity from Asia can provide significant cost savings but has higher risk.
Advantages of Tungsten Carbide Tips
Parameter | Benefit |
---|---|
Hardness | Cuts faster, reduces cutting forces |
Abrasion resistance | Lasts through many sharpenings |
Maintains edge | Less downtime changing dull blades |
Thermal resistance | Higher working temperatures |
Smooth cutting action | Fine finish cuts |
Impact strength | Carbide resists fracturing |
Tool life | Outlasts other cutting materials |
Productivity | Higher feed rates possible |
Carbide tipped blades also produce less friction and smoother cutting action. This causes less binding, reduces gumming when cutting wood materials, and creates an overall superior cut finish.
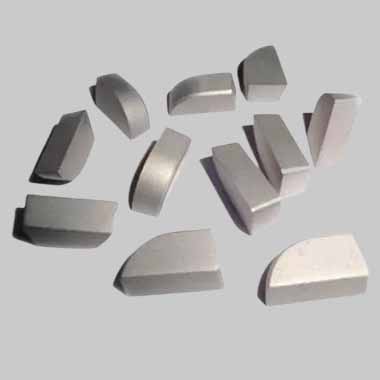
Disadvantages and Limitations
Drawback | Discussion |
---|---|
Cost | Carbide is significantly more expensive than steel |
Brittleness | Prone to chipping when dropped or overloaded |
Brazing concerns | Carbide tips must be expertly brazed to substrate |
Safety | Carbide blades may shatter if core steel fails |
The manufacturing process requires extremely high temperature furnaces, extensive grinding and machining equipment, and consistent technical expertise. These factors drive up pricing but produce a longer lasting, more effective cutting surface.
Risk Mitigations:
- Adhere to operating guidelines
- Inspect for cracks frequently
- De-tension blades after use
- Use blade wash to keep core steel from rusting
With responsible precautions and care, tungsten carbide tipped saws provide superior productivity and value comparedCopy
Carbide vs Other Saw Tip Materials
Tungsten carbide has distinct advantages over other materials used to tip saw blades:
Carbide vs Steel
Parameter | Carbide | Steel |
---|---|---|
Hardness | Triple that of alloy steel | Quickly gets dull |
Speed | Up to 2-3x faster cutting | Slow feed rates required |
Tool life | Hundreds of times longer | Goes dull after short run times |
Thermal resistance | Withstands much higher temperatures | Loses hardness when hot |
Brittleness | Prone to chipping | Flexes before breaking |
Cost | 4-10x higher | Very economical |
Carbide vs Ceramics
Parameter | Carbide | Ceramics |
---|---|---|
Toughness | Much less brittle due to metallic binder | Hard but no plasticity |
Thermal shock resistance | Superior to pure ceramics | Prone to cracking when heated |
Wear rates | Comparable | Slightly better in abrasive materials |
Cost | Moderate price range | Often the most expensive option |
Carbide vs Cubic Boron Nitride (CBN)
Parameter | Carbide | CBN |
---|---|---|
Hardness | Up to 4500 Vickers | Second only to diamond at 4700+ |
Temperature stability | Softens above roughly 1000°C | Better maintains hardness at high heat |
Chemical stability | Reacts with ferrous metals at high temps | Low affinity for iron makes it more stable |
Cost | Far less expensive | Up to 6 times the price per carat |
CBN is superior for ferrous metal cutting applications where high heat is generated. Carbide strikes a better balance between cost and performance for most general purpose saw blade applications.
Carbide vs Diamond
Parameter | Carbide | Diamond |
---|---|---|
Hardness | Highest grade carbide around 93 Rockwell A | Diamond is a perfect 10 on the Mohs scale |
Toughness | Ductile, relatively resistant to fracture | Extremely brittle without cobalt or nickel sintering |
Thermal stability | Deteriorates slowly above 1100°C | Starts oxidizing to carbon dioxide above 700°C |
Wear resistance | Very low wear rate | The longest lasting superficial material |
Cost | Expensive but affordable for most | Usually prohibitive for widespread use |
Industrial diamond tips are primarily used in niche applications like geological core sample drilling and precision glass cutting where maximizing tool life is paramount.
FAQ
Q: How often do carbide tipped blades require sharpening?
A: On average every 25-50 hours of cutting time. Proper blade maintenance helps prevent unnecessary sharpening.
Q: Can I sharpen carbide blades myself?
A: Only with proper carbide grinding equipment. Most send blades out for professional sharpening or replacement tips.
Q: What causes carbide teeth to chip or break?
A: Frequently hitting nails or other embedded objects in wood or masonry materials. Dropping blades on hard surfaces. Operating saws too aggressively.
Q: Is brazing my own carbide inserts difficult?
A: It requires high temperature torches, precision fitment, and experienced technique. Most opt to have shop-brazed blades made or buy factory replacements.
Q: How thick of material can carbide-tipped blades cut?
A: Up to 16 inches for specialized concrete saws. Chop saws typically cut up to 6 inches. Metal cutting band saws 12+ inches.
Q: Can I cut wood materials with a carbide blade?
A: Yes carbide works on all types of wood. It cuts faster and smoother but is more expensive. Great for manmade boards.