Tungsten carbide wear strips offer exceptional hardness, abrasion resistance, and durability – ideal qualities for protecting critical tooling and industrial equipment surfaces against repetitive sliding or impact erosion damage.
This guide details tungsten carbide grades for wear strips, manufacturing methods, sizes available plus applications and leading suppliers. Comparison tables highlight relative strengths across wear strip materials, processes and key selection criteria.
Overview of Tungsten Carbide Wear Strips
As ultrahard protective surface treatments, key traits tungsten carbide strips for high wear areas provide:
- Extreme hardness over HV 1600+ to resist abrasive wear
- Tough carbide composition withstands impact without cracking
- Corrosion resistant nickel alloy binder system
- Smooth finish lowers sliding friction and pressure
- Thin strips simplify retrofitting existing assets
- Lower long term costs than replacing tools/parts
Combined with precision manufacturing techniques for dimensional accuracy, tungsten carbide strips combat erosion damage lengthening service lifetimes.
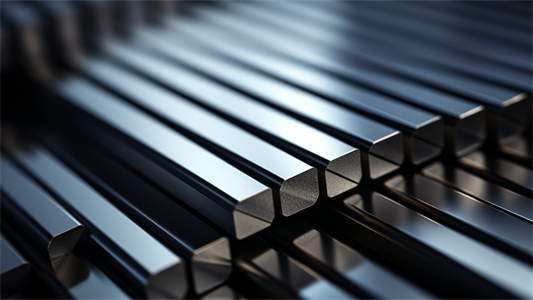
Types of Tungsten Carbide Grades for Wear Strips
Tungsten carbide wear strip choice depends primarily on the abrasion or impact mechanism severity.
Tungsten Carbide Grades Comparison
Grade | Hardness Range | Toughness | Key Applications |
---|---|---|---|
8-12% Cobalt | HV 1600 – 1900 | Higher, but lower max hardness | Moderate abrasion, repeated impact, 49-62 HRC tools |
6% Cobalt | HV 1900 – 2200 | Medium, increased brittleness | Severe sliding abrasion resistance |
3-6% Cobalt | HV 2500 – 3200 | Lower, very brittle | Extreme abrasion; Poor chipping/spalling areas |
Grain sizes range 1-16 micron depending on feature detail resolution needs. Cobalt concentrations dictate ultimate harness potential. Low row recommends multi-carbide blends using Ni, Cr supplements to boost toughness.
Tungsten Carbide Wear Strip Sizes
Standard tungsten carbide strip sizes vary in thickness, width and composition making them easy to retrofit onto most equipment.
Standard Wear Strip Size Specifications
Thickness | Width | Length |
---|---|---|
1mm | 6mm – 60mm | Up to 2 meters |
1.5mm | 10mm – 80mm | Up to 2 meters |
2mm | 15mm – 100mm | Up to 2 meters |
3mm | 20mm – 150mm | Up to 2 meters |
4mm | 20mm – 150mm | Up to 2 meters |
5mm | 20mm – 150mm | Up to 2 meters |
6mm | 20mm – 150mm | Up to 2 meters |
8mm | 20mm – 150mm | Up to 2 meters |
10mm | 20mm – 150mm | Up to 2 meters |
Oversize thicknesses, widths and custom lengths possible. Strips may be straight or curved shaped.
Hole patterns can be added for mechanical fastening if desired.
Manufacturing Processes for Tungsten Carbide Strips
Advanced sintering techniques transform tungsten carbide into wear-resistant blanks subsequently machined into finished strips.
Tungsten Carbide Wear Strip Production Methods
Powder Metallurgy Press+Sinter
Powdered tungsten carbide with nickel alloy binder pressed into shape; Solidified at high temp into a densified structure. Offers intricate, net shape capability. Most strips utilize this process.
Machining from Rolls
Sinter-HIP tungsten carbide roll stock precisely cut into wear strip blanks. Simplifies complex geometries compared to press/sinter process.
Brazing Attachment
Carbide strips furnace brazed using specialty nickel alloys onto metallic substrates. Provides the strongest attachment systems.
Mechanical Fastening
Screws, rivets or other fastener elements anchor tungsten carbide wear strips onto equipment surfaces. Convenience tradeoff versus brazing.
Applications of Tungsten Carbide Wear Strips
The exceptional hardness and wear properties tungsten carbide provides suits high erosion areas across industries:
Industries Using Tungsten Carbide Wear Strips
Mining – Crushing, materials handling, drilling equipment
Forestry – Sawmill and wood processing gear
Construction – Excavation buckets, concrete vibrators
Agriculture – Tillage tools and blades
Food Processing – Chopping and size reduction knives
Recycling – Metal shredders, car crushers
Any environment with excessive particulate abrasion or repetitive instrument surface wear can benefit from retrofit carbide strips prolonging steel tool and component lifetimes 5-10X.
Comparing Wear Strips By Material
While more costly, tungsten carbide significantly outperforms other wear protection materials across key metrics:
Wear Strips Material Selection Matrix
Material | Hardness | Abrasion Resistance | Cost | Cons |
---|---|---|---|---|
Tungsten Carbide | Best | Best | High | Brittle if overloaded |
Ceramics | Good | Good | Medium | Cracks under impact |
Hardened Steel | Average | Average | Lowest | Softens over time from friction heating effects |
Chrome Plate | Low | Low | Low | Poor abrasion resistance |
Carbide strips offer the ultimate sliding abrasion protection for the longest working lifespan.
Leading Tungsten Carbide Wear Strip Manufacturers
Top producers of tungsten carbide wear strips include:
Suppliers of Tungsten Carbide Strips
Company | Grades Offered | Pricing Estimate |
---|---|---|
Kennametal | 6-15% Cobalt | $25-$100 per strip |
Sandvik | 6-20% Cobalt | $20-$150 per strip |
Global Tungsten | 3-12% Cobalt | $15-$80 per strip |
Cornerstone Carbide | 6-15% Cobalt | $30-$125 per strip |
Allied Metals | 6-20% Cobalt | $25-$175 per strip |
Pricing varies based on size specifications, grade selected, order volumes and customization needs. Quotes readily available.
FAQ
What industries generate the most significant demand for tungsten carbide wear strips?
Mining, construction, forestry, and primary metals manufacturing spur the heaviest usage of tungsten carbide strips due to the extreme particle abrasion exposure wearing down heavy asset cutting faces, crushing surfaces and digging implements constantly stressed during use.
What backing or substrate metals work best for attaching carbide strips?
Medium carbon alloy steels offer suitable expansion coefficients and ruggedness to allow durable braze joints or mechanical anchoring. Hardness levels 25-35 HRC provide a sound foundation allowing integration of the hard tungsten carbide layer over areas needing protection.
How thick should tungsten carbide strips be for maximum durability?
For optimum shielding to resist both repetitive abrasive wear and periodic impact stresses, carbide strip thickness should fall between 4-8mm. Thinner strips under 2mm risk cracking. Over 8mm does not appreciably improve working lifespans.
Should tungsten carbide strips be custom fabricated or standardized for a particular application?
Retrofitting existing equipment with standardized strips allows rapid installation using conventional mechanical fasteners or furnace brazing methods. However, custom machined curved strips tailored to precisely match damaged areas speeds replacement and lowers any asset modification requirements.
How often should tungsten carbide wear strips be inspected and replaced?
Routine inspections each maintenance cycle should validate strips remain fully secured with no loosening or mechanical issues. Annual proactive replacements are recommended for extreme duty cycles regardless of actual wear to prevent any unexpected failures in service. Higher cobalt content grades sustain usefulness the longest between changeouts.