Carbide blanks in metric dimensions provide the starting material for making cutting tools, dies, and wear parts through grinding and machining. This guide covers metric tungsten carbide blanks for metalworking applications.
Overview of Metric Carbide Blanks
- Made from tungsten carbide-cobalt (WC-Co)
- High hardness, wear resistance and compressive strength
- Available in metric sizes as rods, discs, cylinders, blocks
- Ground to final dimensions and geometry for tools
- Ideal for high-speed machining applications
Typical sizes:
- Diameters: 1 to 75 mm
- Lengths: 5 to 300 mm
- Discs up to 300 mm diameter
Common grades:
- Straight tungsten carbide (WC)
- 6% cobalt, 10% cobalt and 15% cobalt
Carbide blanks provide the optimal starting material for metalworking, cutting and forming tools.
Applications of Metric Carbide Blanks
Metric carbide blanks are used to manufacture:
- Cutting tools – drills, endmills, chamfer tools
- Forming and stamping dies
- Drawing and extrusion dies
- Pelletizing and pulverizing tools
- Wear parts and nozzles
- Punching and pressing tools
- Mining and construction tools
- Slurry and pumping seals
- Metal deburring and finishing tools
Carbide blanks enable optimal tooling geometries and complex contours for maximum productivity.
Advantages of Carbide Blanks
- High wear resistance and hardness
- Maintains sharp cutting edge
- Withstands high machining speeds and feeds
- High temperature and chemical resistance
- Consistent quality from standard blanks
- Available in a wide range of sizes
- Cost-effective compared to custom preforms
- Shorter lead times
Carbide blanks provide an excellent starting raw material for tooling requirements.
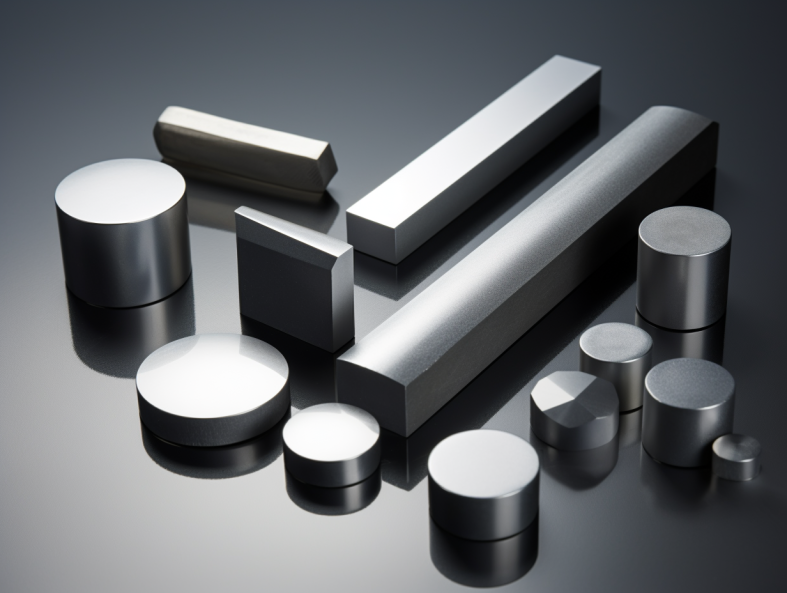
Types of Metric Carbide Blanks
1. Cobalt Content
- Straight tungsten carbide (WC)
- 6% cobalt (WC-Co 6%)
- 10% cobalt (WC-Co 10%)
- 15% cobalt (WC-Co 15%)
2. Quality Grades
- Standard/Commercial quality
- Premium/Air-craft quality
- Superior/Nuclear quality
3. Physical Format
- Rod blanks
- Cylindrical blanks
- Disc blanks
- Custom preform blanks
- Rectangular/square blanks
- Complex profile blanks
Popular standard sizes are readily available off the shelf from stock. Custom preforms can also be manufactured.
Material Properties
Properties of tungsten carbide-cobalt grades:
Grade | Hardness HRA | Transverse Rupture Strength MPa | Density g/cc |
---|---|---|---|
Straight WC | 89.0 – 93.0 | 1450 | 14.95 |
WC-6Co | 89.0 – 91.5 | 1650 | 14.70 |
WC-10Co | 86.5 – 89.0 | 1850 | 14.30 |
WC-15Co | 84.0 – 88.0 | 1850 | 13.60 |
Higher cobalt content improves fracture strength but decreases hardness.
International Size Standards
Metric carbide blanks are available in standard sizes as per:
- ISO 1832 – Indexable inserts for cutting tools
- DIN 6580 – Solid carbide endmills and drills
- ANSI B212.4 – Tool holder boring bar shank dimensions
- DIN 8030 – Drawing die blanks
- Custom sizes also manufactured
Standard sizes optimize material usage and lower machining costs.
Size Range Examples
Round Rod Blanks
Diameters: 1mm to 75 mm Lengths: 5 mm to 300 mm
Square Block Blanks
Sizes: 4 mm to 60 mm Lengths: 8 mm to 150 mm
Rectangular Blocks
Widths: 6 mm to 75 mm Lengths: 20 mm to 180 mm
Disc Blanks
Diameters: 25 mm to 300 mm Thicknesses: 3 mm to 25 mm
Metric blanks cover a wide range of tooling sizes. Custom preforms also available.
Technical Specifications
Parameter | Details |
---|---|
Carbide grade | Straight WC, WC-Co 6%, 10%, 15% |
Hardness range | 84 to 93 HRA |
Density | 13.6 to 15 g/cc |
Transverse rupture strength | 1450 to 1850 MPa |
Coarseness | 0.2 to 15 μm |
Total porosity | A06, B00, C00 |
Surface finish | Up to 0.4 μm Ra |
Dimensional tolerances | ±0.1 to 0.3 mm |
Chamfer and edge prep | Optional |
Certifications | ISO 9001, ISO 14001 |
Grades, finishes, chamfers and tolerances can be customized as per application requirements.
Manufacturing Process
1. Milling: Rough mills carbide blocks to oversize blanks
2. Grinding: Grinds blanks to precise dimensions and finishes
3. Chamfering and Edge Prep: Done if specified
4. Testing and Inspection: Confirms dimensions, finish, grade etc.
5. Packaging: Careful packing to avoid damage in transit
Automated, high-precision manufacturing ensures consistent quality metric carbide blanks.
Global Suppliers and Price Ranges
Supplier | Location | Price Range |
---|---|---|
Cera Materials | USA | $2 – $30 per piece |
Ceratizit | Luxembourg | $5 – $50 per piece |
Kennametal | USA | $3 – $35 per piece |
Yi Bang Industrial | China | $2 – $25 per piece |
Miranda Tools | India | $1 – $15 per piece |
- Prices depend on size, grade, quality, tolerance and order volume
- Larger blanks and premium grades cost more
- Custom preforms are higher cost
- Price decreases with quantity due to scaling
Packing for Safe Transport
Carbide blanks require careful packing to prevent damage:
- Individual pieces wrapped in abrasive-resistant paper
- Grouped in cardboard boxes with compartment slots
- Cushioned with foam or soft wrapping
- Secured in crate or pallet for load stability
- Desiccant bags to absorb moisture
- Labelling with details like grade, size, PO number
- Fragile labels on box to prevent mishandling
Proper packing ensures blanks reach the customer unblemished and ready to use.
Design Considerations for Blanks
- Select grade based on hardness and strength needs
- Consider section size, availability, and utilization
- Minimize machining requirements if possible
- Design contour andrelief angles appropriately
- Accommodate mounting interfaces and hardware
- Plan for smoothing beads and corner radii
- Leave sufficient material for coating if needed
- Avoid thin or unstable projecting features
Collaborating with carbide blank suppliers during the design stage is recommended to optimize the blanks.
How to Select the Right Blank Supplier
Factors for choosing a metric carbide blank supplier:
Technical capabilities:
- Can they supply the grades and tolerances required?
- Do they have size range to meet needs?
- Will they manufacture custom preforms?
Quality:
- Consistency in dimensions and material properties
- Stringent manufacturing process controls
- Robust quality management system
Services:
- Technical consultation for design and material selection
- Flexibility in order quantities and lead times
- Willingness for new product development
Commercial:
- Competitive transparent pricing
- Responsiveness to RFQs and quotes
- Ease of order placement and follow-up
Logistics:
- Packaging expertise to prevent transit damage
- On-time delivery capabilities
- Inventory and stocking abilities
Evaluating carbide blank suppliers on these parameters ensures getting a partner that delivers ideal blanks cost-effectively.
Pros and Cons of Carbide Blanks
Advantages
- Enables optimized tool geometry
- Higher performance than assembled inserts
- Sintered structure with minimal defects
- Protects IP versus purchasing inserts
- Cost-effectiveness for medium volumes
- Shorter lead times than custom preforms
Disadvantages
- Additional grinding/machining needed
- Higher unit costs than mass produced inserts
- Technical expertise needed for design
- Minimum order quantities may apply
Troubleshooting Carbide Tool Failures
Failure Mode | Possible Causes | Corrective Actions |
---|---|---|
Fracture | Poor grade or substandard material | Switch suppliers, get certification |
Inadequate machining/surface defects | Improve machining methods | |
Overload beyond design | Redesign tool geometry and usage | |
Wear | Wrong grade for application | Select grade with higher wear resistance |
Insufficient surface finish | Ensure fine finishing of 0.1-0.4 μm Ra | |
Operation outside limits | Modify operating parameters within limits | |
Chipping | Unfavorable geometry | Redesign edge angles, avoid sharp corners |
Interrupted cuts | Optimize approach, speed, feed rates | |
Built-up edge | Use proper coatings, clearance angles |
Consulting with the blank supplier helps correct carbide tool failures.
FAQs
Q: What size metric carbide blanks are commonly stocked?
A: Most suppliers stock a range of 1mm-20mm rods, 20mm-75mm discs, and squares from 4mm-25mm.
Q: What is the lead time for procuring custom preforms?
A: Custom blank preforms may need 4-6 week lead time depending on the supplier.
Q: What certification is provided with blanks?
A: Reputable suppliers provide material certification per ISO standards and lot-specific test reports.
Q: Does using higher cobalt blanks increase toughness?
A: Yes, 10-15% cobalt grades provide the best combination of wear resistance and toughness.
Q: What post-processing method strengthens carbide?
A: CVD or PVD coatings deposited on the carbide surface increase hardness and wear life significantly.
Q: How should damaged carbide blanks be handled?
A: Never use damaged, cracked or corroded blanks which can fail unexpectedly. Reject them and return to the vendor.
Conclusion
Metric tungsten carbide blanks offer an economical starting format for manufacturing custom cutting, stamping and forming tools to meet specific productivity targets. With high wear resistance and compressive strength, carbide blanks can be ground into inserts and dies with complex shapes, profiles and surface coatings not possible with assembled inserts. Partnering with a qualified carbide blank supplier and leveraging their technical expertise in material selection and design ensures a cost-effective tooling solution optimized for the application. With stringent quality control and international material certification, metric carbide blanks provide a building block approach to maximize productivity in machining and metalworking.