From the depths of oil wells to the sterile environments of operating rooms, carbide rods are quietly revolutionizing industries worldwide. These unassuming cylindrical rods, crafted from one of the hardest materials known to man, possess a unique blend of properties that make them indispensable across a vast spectrum of applications.
This deep dive explores the diverse world of carbide rod applications, showcasing how their exceptional hardness, wear resistance, and ability to withstand extreme conditions are transforming industries and driving innovation.
Beyond the Surface: Understanding the Power of Carbide
Before delving into the applications, it’s crucial to grasp what makes carbide rods so special. Unlike steel, which softens at high temperatures, tungsten carbide, the primary component of these rods, retains its strength and hardness even in extreme heat. This, coupled with its exceptional wear and corrosion resistance, makes it the ideal material for demanding applications where other materials falter.
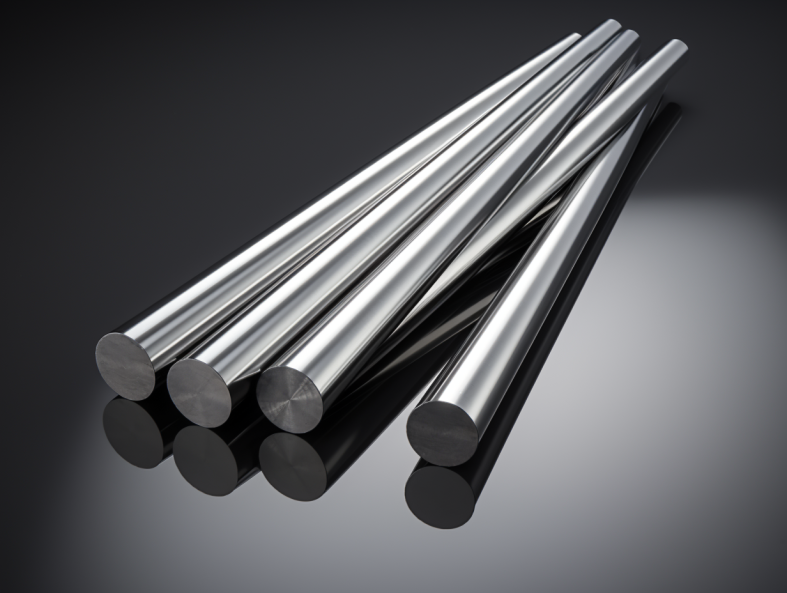
1. Metalworking: Where Precision Meets Performance
Carbide rods are the unsung heroes of the metalworking industry, forming the foundation for a wide array of cutting tools that shape and mold metal components with unparalleled precision:
- End Mills: These workhorses of the machining world rely on carbide rods for their cutting edges. The extreme hardness of carbide allows end mills to cut through tough metals like steel and titanium with ease, while its wear resistance ensures long tool life and consistent performance.
- Drills: From creating small holes in circuit boards to boring large openings in heavy machinery, carbide drill bits are essential for their ability to penetrate even the toughest materials. Their resistance to heat build-up further enhances their performance and longevity.
- Reamers: When precision hole finishing is critical, carbide reamers take center stage. These tools, crafted from carbide rods, enlarge and refine pre-drilled holes to exact dimensions, ensuring smooth, accurate surfaces for bearings, bushings, and other critical components.
2. Oil & Gas: Conquering Extreme Environments
The unforgiving conditions of oil and gas exploration and extraction demand materials that can withstand immense pressure, abrasive materials, and corrosive environments. Carbide rods rise to the challenge:
- Nozzles: In drilling operations, high-pressure jets of fluid containing abrasive materials are used to break down rock formations. Carbide nozzles, with their exceptional wear resistance, ensure these jets maintain their shape and effectiveness, maximizing drilling efficiency and extending equipment lifespan.
- Drill Bits: Drilling through layers of rock demands incredible strength and durability. Carbide inserts are incorporated into drill bits to provide the necessary hardness and wear resistance to penetrate even the toughest formations, reducing downtime and lowering overall drilling costs.
3. Aerospace: Reaching for the Skies with Strength and Lightweight
The aerospace industry demands materials that are both incredibly strong and lightweight to maximize fuel efficiency and performance. Carbide rods, with their unique combination of properties, play a vital role:
- Engine Components: The extreme temperatures and high stresses within aircraft engines require materials that can withstand these demanding conditions. Carbide components, such as turbine blades and seals, provide the necessary strength, heat resistance, and wear resistance to ensure reliable engine performance.
- Structural Parts: In specific applications where high strength-to-weight ratios are critical, carbide components are used in structural parts of aircraft, contributing to overall weight reduction without compromising on structural integrity.
4. Medical: Precision Engineering for Life-Saving Applications
When it comes to medical devices and instruments, precision, biocompatibility, and reliability are paramount. Carbide rods answer the call:
- Surgical Instruments: Carbide’s hardness and ability to maintain a sharp cutting edge make it ideal for surgical instruments. Scalpels, drills, and other cutting tools made from carbide enable surgeons to perform delicate procedures with precision and accuracy.
- Implants: In certain applications, such as dental implants and joint replacements, carbide’s biocompatibility and wear resistance make it suitable for creating durable and long-lasting implants that can withstand the stresses of everyday use within the human body.
5. Automotive: Driving Innovation with Durability and Performance
The automotive industry constantly seeks materials that can enhance vehicle performance, efficiency, and longevity. Carbide rods contribute to these goals in various ways:
- Bearings: In high-stress areas like wheel bearings, carbide’s hardness and wear resistance translate to longer bearing life, improved fuel efficiency, and reduced maintenance requirements.
- Valve Components: Within engine valves, carbide components are used for their ability to withstand high temperatures and resist wear, contributing to optimal engine performance and reduced emissions.
6. Woodworking: Achieving Smooth, Precise Cuts
While often associated with metalworking, carbide rods also play a crucial role in the woodworking industry, particularly in demanding applications:
- Saw Tips: Carbide-tipped saw blades are renowned for their sharpness, durability, and ability to produce smooth, precise cuts in various wood types, including hardwoods and composites. These blades maintain their sharpness longer than traditional steel blades, reducing downtime for sharpening and improving overall cutting efficiency.
7. Moldmaking: Shaping the Future with Intricate Detail
The creation of molds for manufacturing a wide range of products, from plastic components to metal parts, requires materials that can hold intricate details and withstand repeated use. Carbide rods are up to the task:
- Mold Inserts: Carbide inserts are incorporated into molds to form complex shapes and features that would be difficult or impossible to achieve with other materials. Their hardness and wear resistance ensure the mold maintains its dimensional accuracy over extended production runs, resulting in high-quality, consistent parts.
Table 1: A Glimpse into the Diverse Applications of Carbide Rods
Industry | Application | Key Properties of Carbide |
---|---|---|
Metalworking | Cutting tools (end mills, drills, reamers) | Hardness, wear resistance, high-temperature stability |
Oil & Gas | Nozzles, drill bits | Wear resistance, corrosion resistance |
Aerospace | Engine components, structural parts | High-temperature strength, lightweight |
Medical | Surgical instruments, implants | Biocompatibility, wear resistance |
Automotive | Bearings, valve components | Wear resistance, high-temperature stability |
Woodworking | Saw tips | Hardness, wear resistance, sharpness |
Moldmaking | Mold inserts | Hardness, wear resistance, dimensional stability |
FAQs: Your Carbide Rod Application Questions Answered
1. What factors should I consider when choosing carbide rods for a specific application?
Key factors include the material being worked with, required tolerances, operating temperatures, expected wear and tear, and budget constraints. Consulting with a carbide supplier or expert is recommended to determine the optimal grade and properties for your specific needs.
2. Are there any limitations to using carbide rods in certain applications?
While carbide offers exceptional properties, it’s essential to consider its limitations. Carbide can be brittle and prone to chipping under impact or high-vibration conditions. Additionally, machining carbide requires specialized equipment and expertise due to its extreme hardness.
3. Can carbide rods be coated to enhance their performance?
Yes, carbide rods can be coated with various materials, such as titanium nitride (TiN) or titanium aluminum nitride (TiAlN), to further enhance their wear resistance, lubricity, and oxidation resistance. Coatings are often application-specific and can significantly extend tool life in demanding environments.
4. How do I dispose of carbide rods properly?
Carbide is considered hazardous waste due to the presence of tungsten and cobalt, which can be harmful to human health and the environment. It’s crucial to dispose of carbide rods through a certified waste management company specializing in handling hazardous materials.
5. What are the future trends in carbide rod applications?
The demand for carbide rods is expected to grow as industries continue to seek materials that can withstand increasingly demanding conditions. Advancements in carbide grades, coatings, and manufacturing technologies will further expand the applications of these versatile materials, driving innovation across various sectors.
Want to buy cheap tungsten carbide rods at good prices? please click here.